Чья сборка лучше?: как производят автомобили Škoda в России и Чехии — Тест-Драйвы — Афиша Калининграда
Денис Туголуков съездил в Калугу и Млада-Болеслав для того, чтобы выяснить, есть ли разница между отечественной и европейской сборкой автомобилей марки Škoda.
В чем, собственно, вопрос?
В социальных сетях и на специализированных форумах между автолюбителями довольно часто возникают дискуссии о том, есть ли разница между отечественной и зарубежной сборкой автомобилей одной и той же марки. Чтобы развеять сомнения и возможные домыслы, российское представительство Škoda Auto пригласило журналистов ведущих региональных СМИ посетить производственные мощности Volkswagen Group в России и Чехии.
Почему марку Škoda сегодня часто отождествляют с Volkswagen?
Потому что компания Škoda входит в состав Volkswagen Group — огромного концерна, объединяющего также бренды Seat, Audi, Porsche и даже Lamborghini. Всего — более дюжины всемирно известных автомобильных марок. Škoda стала частью концерна в 1991 году, а сама чешская компания, как считается, была основана в 1895 году в городе Млада-Болеслав двумя Вацлавами — Лаурином и Клементом. Сегодня в честь отцов-основателей — Laurin & Klement — компания называет лимитированные «люксовые» комплектации своих автомобилей.
Стоп, а откуда тогда вообще взялось название Škoda?
Шкода — это фамилия чешского инженера Эмиля Шкоды, купившего в 1869 году машиностроительную фабрику в Пльзени. Изначально предприятие производило узлы и детали для гидроэлектростанций, шлюзовое оборудование и даже — в преддверии Первой мировой войны — оружие и боеприпасы. Объединение с Laurin & Klement случилось лишь спустя восемь лет после Первой мировой, а в 1926 году родился узнаваемый сегодня логотип Škoda, изначально выполненный в сине-белой гамме. Оригинальный зеленый цвет, ставший затем фирменным цветом марки, логотип приобрел лишь в 1999 году.
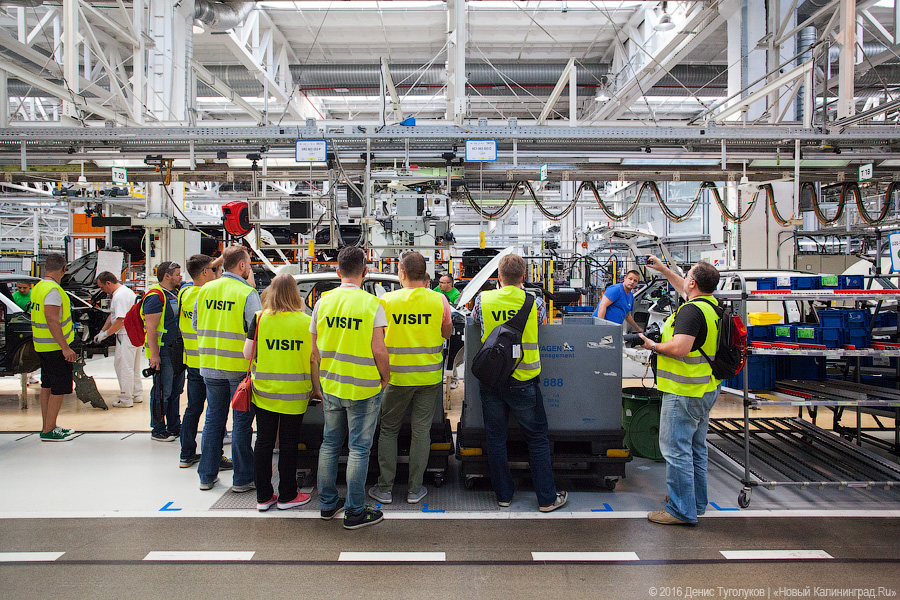
И где же производят автомобили Škoda сейчас?
Много где: в России, Китае, Словакии, Индии — локальные партнеры есть даже на территории Украины и Казахстана. Основными предприятиями Škoda в Чехии, на которых производится непосредственно сборка автомобилей, на сегодняшний день являются заводы в Млада-Болеславе и Квасинах. Ежедневно на них выпускается порядка 3000 автомобилей. При этом завод в Млада-Болеславе — один из самых крупных в Восточной Европе. По площади он даже больше, чем самое маленькое государство Старого Света — княжество Монако. Здесь представлен полный цикл производства: литье блоков цилиндров и сборка двигателей, штамповка отдельных элементов, сварка кузова, его грунтовка и покраска, сборка салона и «свадьба» — процесс соединения кузова с ходовой частью, двигателем и трансмиссией. В среднем на сборку одного автомобиля с нуля до его выезда за ворота сборочного цеха уходят сутки.
Так что, Škoda «берет» за счет объемов производства?
Не совсем. Сотрудники Škoda очень гордятся и постоянно подчеркивают тот факт, что все выпускаемые компанией автомобили уже имеют своих покупателей — впрок здесь машины не делают. На этапе сборки над каждым автомобилем закрепляется специальный большой лист документации, на котором отображены все особенности комплектации. Эта же информация дублируется и в электронном виде, а рабочие при необходимости сверяются с данной «родословной». Такая система помогает учитывать все возможные пожелания клиентов, вплоть до цветовой гаммы. Кстати, в этом сезоне особой популярностью пользуются оттенки коричневого.
Про заводы в Чехии все ясно. Как давно автомобили Škoda собирают в России?
С ноября 2007 года. Сначала это была крупноузловая сборка, но в 2009 году на заводе Volkswagen Group Rus под Калугой было запущено производство полного цикла. Так же, как на головном предприятии в Млада-Болеславе, здесь осуществляют сварку и покраску кузова, сборку салона, «женят» кузов с шасси, двигателем и трансмиссией. Еще одна сборочная площадка автомобилей Škoda находится в Нижнем Новгороде, где также налажено производство полного цикла. Правда, сегодня на обоих российских заводах выпускаются только три наиболее популярные модели марки: Octavia, Yeti и Rapid, — но зато из российского металла. Патриотично, как ни крути.
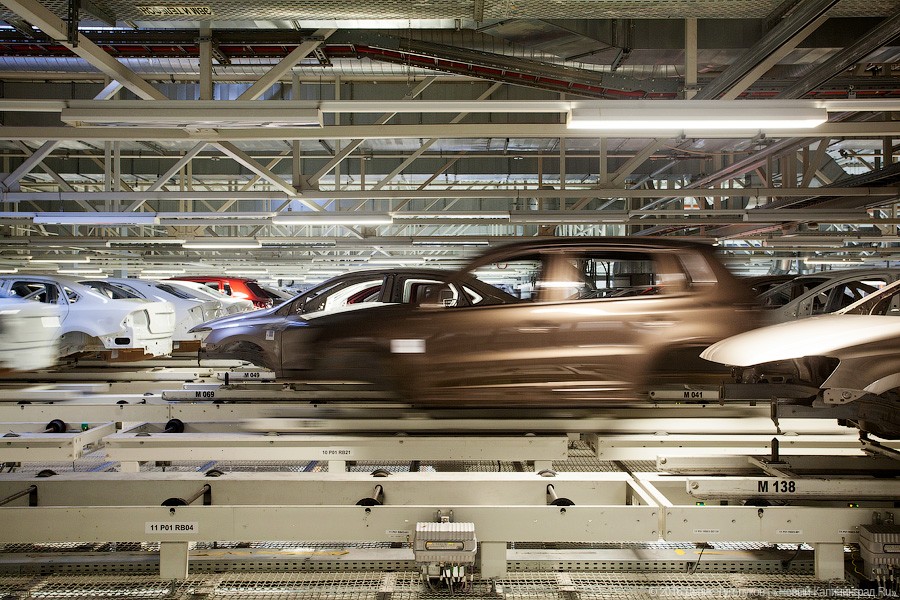
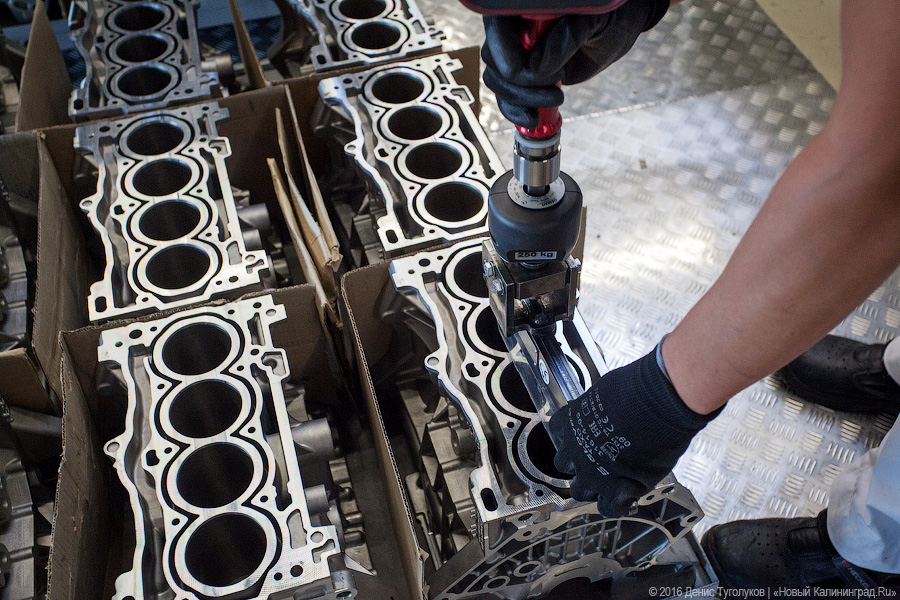
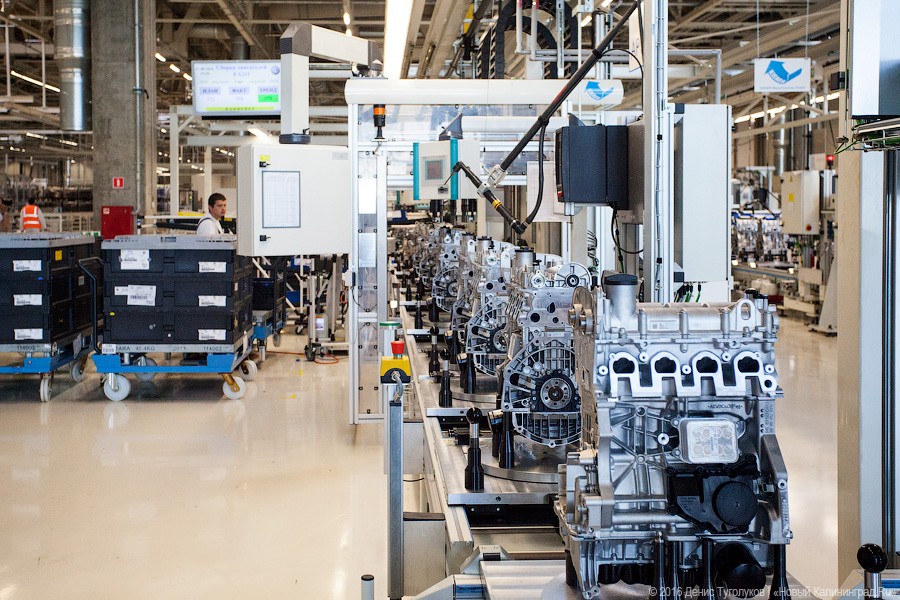
Понятно. А как обстоят дела с системой контроля качества?
Здесь все очень строго. Даже материалы, получаемые от локальных партнеров, проходят лабораторную экспертизу, не говоря уже о контроле качества производимых работ. Процесс сборки строго стандартизирован, часть произвольно выбранных кузовов обязательно исследуется на предмет соответствия заданным стандартам. А прежде чем покинуть стены завода, собранные автомобили проходят серию тестов, в ходе которых проверяется качество лакокрасочного покрытия, герметичность кузова, работа двигателя, электронных систем и тормозной системы.
А двигатели тоже в России производят?
Представьте себе! Завод по производству двигателей под Калугой был запущен совсем недавно, в 2015 году, и считается самым современным в концерне. Сейчас там выпускают атмосферные бензиновые двигатели 1.6 MPI для пяти различных моделей Škoda и Volkswagen — автомобили, укомплектованные такими силовыми агрегатами, традиционно пользуются большим спросом среди российских покупателей. Все собранные на предприятии двигатели обязательно проходят так называемый «холодный тест» — «раскручиваются» без запуска до рабочих оборотов на специальном стенде, — а каждый четвертый подвергается «горячему» тестированию. По одному двигателю из каждой готовой партии разбирают до винтика и исследуют в лаборатории с целью контроля качества.
Получается, производственные площадки в Чехии и России примерно одинаковые?
И да, и нет. Производственные линии на заводах в обеих странах соответствуют очень жестким корпоративным стандартам, соблюдение которых блюдется неукоснительно, и это делает их похожими друг на друга. В то же время различий между ними не меньше, чем сходств. Начнем с того, что предприятие в Млада-Болеславе элементарно крупнее завода в Калуге. Большие объемы производства предполагают гораздо более высокий уровень автоматизации, который на некоторых линиях здесь достигает 83% (для российского предприятия этот показатель скромнее — около 30%). Есть различия и во внутрикорпоративной этике: если у чешского рабочего неподалеку от рабочего места может стоять коробка с пиццей или бутылка воды, то у российского ничего, кроме необходимых инструментов и оборудования не встретишь (зато наших сотрудников кормят и развозят с работы и на работу бесплатно). Наконец, попасть на завод в Млада-Болеславе и увидеть своими глазами процесс сборки автомобилей Škoda может любой желающий — для этого достаточно купить билет в музей чешской марки с соответствующим экскурсионным обслуживанием (стоимость — 200 крон для взрослых и 100 для детей). В Калуге же даже нам, журналистам, было непросто — за каждым шагом зорко следили сотрудники службы безопасности, пресекавшие любые попытки отклонения от регламента посещения завода. В целом, уровень трудовой дисциплины на предприятии в России показался нам даже более высоким, чем в Чехии.
www.newkaliningrad.ru
Справка о производственных мощностях ŠKODA AUTO
Завод в Калуге
Завод «ФОЛЬКСВАГЕН Груп Рус» в Калуге — главная производственная площадка ŠKODA в России, открывшаяся в ноябре 2007 года. Предприятие стало пятым заводом марки за пределами Чешской Республики. Данная площадка является одной из самых современных в рамках концерна Volkswagen AG.
С февраля 2014 года здесь производится компактный лифтбэк ŠKODA Rapid — бестселлер марки на российском рынке. В рамках подготовки к выпуску этой модели завод был значительно расширен и модернизирован. В частности, был открыт новый кузовной цех с инновационным оборудованием, отвечающим последнему стандарту концерна VASS, предполагающему быструю, точную, надежную и энергосберегающую работу. Это позволило сделать выпускаемую продукцию более доступной для потребителей. Общие инвестиции в развитие площадки составили 150 млн. евро.
Для обеспечения высоких стандартов качества производства на заводе действует лаборатория качества — неотъемлемая часть любого предприятия концерна Volkswagen. Лаборатория следит за стандартами в самых различных областях, от безопасности и надежности до эстетических характеристик автомобиля. На калужском заводе лаборатория качества впервые появилась в 2009 году, к моменту запуска производства полного цикла. Объем инвестиций в оборудование составил порядка 3 млн евро. В лаборатории качества в Калуге можно произвести до 200 различных тестов. Система контроля качества концерна Volkswagen — многоэтапная и сложная процедура. Многочисленные проверки включают оценку используемых материалов, лакокрасочного покрытия, коррозионную стойкость, автоматизированный контроль качества сборки.
На заводе действует измерительная лаборатория, где работают с перспективными кузовами и контролируют качество изготовления кузовов серийных автомобилей. Оборудование лаборатории позволяет измерить объект с точностью от одной десятой до трех тысячных миллиметра. Система построена так, чтобы была возможность отследить ошибку на самом раннем этапе. Одна из задач лаборатории — выявлять отклонения при сварке кузовка и давать соответствующие указания. Измерения кузовных деталей проводятся специалистами на регулярной основе: минимум один раз в сутки произвольно взятый кузов каждой из трех собираемых в Калуге моделей тщательно осматривается и замеряется по сотням точек. Вдобавок, абсолютно все кузова модели Rapid проходят измерительную проверку с помощью лазера Zeiss в автоматическом режиме прямо в сварочном цехе.
Лаборатория тесно работает и с поставщиками: здесь под силу решить любые разногласия относительно размеров и параметров автомобильных деталей. Для этих целей на заводе существует «кубинг» — алюминиевая модель кузова из цельного куска алюминия, на которую можно установить практически любую навесную деталь: фары, фонари, стекла, сиденья, элементы внутренней обшивки и т.д. Детали изготавливаются с точностью до 0,1 мм. Стоимость алюминиевого макета составляет больше полумиллиона евро. С помощью уникального инструмента специалисты могут быстро выяснить, насколько любая из комплектующих деталей соответствует идеально выверенной геометрии.
Производство полного цикла означает, что в Калугу поступают детали и компоненты будущей модели, которые уже на месте проходят процессы сварки, двойной грунтовки, покраски, антикоррозийной обработки горячим воском и фирменным составом концерна Volkswagen. На заводе устанавливается двигатель, коробка передач, вклеиваются стекла, монтируются сиденья, закрепляются логотипы. Далее автомобиль заправляют и тщательно тестируют.
Собранный автомобиль должны как минимум дважды проинспектировать в световом тоннеле. Модель проходит водный тест в дождевальной камере, который позволяет убедиться в отсутствии протечек кузова. Далее автомобиль ставится на роликовый стенд, имитирующий различные ситуации, возможные при движении или торможении транспорта. После автомобиль тестируют на дорогах общего пользования, при этом обязательно проезжают участок с разбитым покрытием. В распоряжении специалистов около 50 тестовых маршрутов: от автомагистралей до разбитых грунтовых дорог. Таким образом, компания проверяет, что каждый автомобиль ŠKODA отвечает требованиям российских дорог и демонстрирует хорошую управляемость даже на дорогах низкого качества. Лишь после многочисленных проверок и измерений автомобиль отправляется в дилерский центр.
Работая в две смены, завод производит около 90 автомобилей ŠKODA Rapid в сутки. Автомобили локального производства оснащаются пакетом для плохих дорог, отличаются более высоким дорожным просветом и мощным аккумулятором, лучше приспособленным для суровых российских зим. При производстве ŠKODA Rapid используется продукция из более чем 45 стран мира. Тем не менее, практически весь кузовной металл выпускается в России. Прокат, оцинкованный стальной лист, кресла в сборе, внутреннюю пластиковую обшивку дверей, переднюю панель, элементы системы выпуска, топливные баки и т.д. также изготовляют локально.
Volkswagen Group Rus стала одной из первых иностранных компаний, построивших и запустивших в 2015 году собственный завод по производству двигателей в России. Проект по строительству нового современного завода был реализован всего за три года — в 2012 году соглашение о строительстве завода подписали председатель правления Volkswagen AG проф. д-р Мартин Винтеркорн и губернатор Калужской области Анатолий Артамонов. В декабре того же года был заложен первый камень моторного завода. В строительство предприятия, производственная мощность которого составляет 150 тыс. двигателей в год, концерн Volkswagen инвестировал около 250 млн. евро. Новый завод площадью 32 тыс. м2 расположен в Калуге, в непосредственной близости от автомобильного предприятия Volkswagen. Моторный завод создал около 400 новых рабочих мест в регионе.
Предприятие также занимается выпуском двигателей для брендов концерна. Агрегаты собираются в строгом соответствии с международными стандартами качества концерна Volkswagen AG. На калужском заводе осуществляется полный контроль качества выпускаемой продукции, проводятся многочисленные испытания и тесты. На моторном заводе установлено 13 роботов производства всемирно известных немецких, словенских и итальянских высокотехнологичных компаний. Оборудование, установленное на производстве, гарантирует точность обработки деталей до 1 микрона (0,001 мм), а точность обработки цилиндров составляет 6 микронов (0,006 мм). Контроль деталей по самым критичным параметрам производится непосредственно в процессе производства с помощью встроенных в обрабатывающее оборудование датчиков. Для постоянного контроля качества выпускаемой продукции на заводе организованы лаборатория чистоты и измерительная лаборатория.
Общий объем инвестиций концерна Volkswagen в оборудование по контролю качества продукции составил 8,6 млн. евро. В лаборатории чистоты осуществляется тестирование готовой продукции для контроля качества выполнения операций механической обработки на производстве. Здесь проверки проходят коленчатый вал, головка блока цилиндров и блок цилиндров двигателя, а также заготовки, которые приходят от поставщиков. Следующим этапом проверки качества деталей является оценка в измерительной лаборатории. Здесь с помощью 7 основных высокоточных приборов производят измерения формы и свойств поверхностей деталей.
В сентябре 2015 года здесь было запущено производство бензиновых двигателей 1.6 MPI серии EA 211, которые устанавливаются на все модели ŠKODA российской сборки. Эта мера позволяет снизить стоимость автомобилей для российских клиентов. Производственные операции, осуществляемые при выпуске двигателей внутреннего сгорания, включают механическую обработку блока цилиндров, обработку головки блока цилиндров (включая монтаж), обработку коленчатого вала и сборку всего двигателя. Завершается сборка двигателя «горячим тестом», направленным на проверку всех его функций: запуск, холостой ход, работа при всех степенях нагрузки, проверка электрической, топливной, масляной и охлаждающей систем, газораспределительного механизма, мощности, крутящего момента. Компания Volkswagen Group Rus активно привлекает к сотрудничеству крупных поставщиков: заготовки блока цилиндров и головки блока цилиндров поступают в Калугу с ульяновского завода компании Nemak, которая производит детали двигателя из российского алюминия, а в производственном процессе использует песок с местного месторождения. Компания Fujikura поставляет на производство проводку для моторов. Компания Volkswagen постоянно работает над расширением базы локальных поставщиков.
Залогом успешного производства также является подготовка и обучение сотрудников. Для этого на моторном заводе работает специализированный тренинговый центр, в котором сотрудники проходят обучение основным навыкам и базовым знаниям по системе компании Volkswagen. Внимание учащихся концентрируется на освоении процесса контроля качества и понимании необходимости стандартизированного хода рабочего процесса. Сотрудники калужского завода проходят обучение на предприятиях концерна Volkswagen в Млада-Болеславе (Чехия), Хемнице (Германия), Зальцгиттере (Германия), Польковице (Польша).
Основные даты:
2006, 28 октября Закладка первого камня в строительство завода
2007, 28 ноября Открытие завода и запуск крупноузлового производства
2009, 20 октября Запуск производства полного цикла, включающего сварку и окраску (бренд ŠKODA был представлен моделью Octavia)
2010, 8 декабря Производство 200-тысячного автомобиля с момента открытия завода
2011, 14 октября Производство 300-тысячного автомобиля с момента открытия завода
2012, 28 августа Подписание соглашения о строительстве завода по производству двигателей
2012, 21 ноября Производство 500-тысячного автомобиля с момента открытия завода
2012, 11 декабря Закладка первого камня в фундамент нового завода двигателей
2013, 6 июняПроизводство 600-тысячного автомобиля с момента открытия завода и 400-тысячного автомобиля по технологии полного цикла
2013, 26 ноября Производство 700-тысячного автомобиля с момента открытия завода
2014, февраль Начало производства полного цикла ŠKODA Rapid
2014, 3 марта Строительство нового кузовного цеха
2015, 4 сентября Запуск производства двигателей 1.6 MPI серии EA211
2016, 26 февраля Производство 1 000 000-го автомобиля с момента открытия завода
www.skoda-avto.ru
Где собирают ŠKODA для российского рынка?
Где собирают SKODA?
Volkswagen AG отличается соблюдением высоких стандартов. Будучи одним из ведущих участников этого крупного конгломерата, «ШКОДА» также гарантирует безупречное качество всей своей продукции, независимо от географического расположения завода-изготовителя. Производства, где собирают 95% новых SKODA, поступающих на российский рынок, расположены в двух городах — это Калуга и Нижний Новгород.
Локализация процессов изготовления позволяет сделать конечную стоимость продукции ниже, а значит, доступнее для большего круга потенциальных владельцев. При этом безукоризненное качество, которым известен чешский бренд, остается неизменным. Например, решив купить «ШКОДА ОКТАВИЯ А7» отечественной сборки, вы получите тот же автомобиль, но по более выгодной цене.
На обоих заводах, где производят «ШКОДУ», налажено производство полного цикла по контрактной схеме. Это значит, что в цеха поставляются оригинальные детали будущей модели, где они проходят такие этапы, как сварка, двойное грунтование, покраска и антикоррозийная обработка специальными составами Volkswagen.
Помимо этого, на российских предприятиях устанавливаются силовые агрегаты, коробки передач, производится монтаж сидений, стекол и другого оборудования. На всех стадиях существует неусыпный контроль, будь то проверка соответствия оттенков кузовной эмали или точность подгонки механизмов и компонентов.
В активе заводов имеется самое современное оборудование и, конечно же, штат настоящих профессионалов, имеющих такую же квалификацию, как у их коллег из Чехии и Германии. Все потому, что такой крупный мировой производитель, как SKODA, дорожит своей репутацией и просто не может себе позволить пренебречь качеством выпускаемых автомобилей.
Где собирают двигатели ŠKODA
В сентябре 2015 года в Калуге был открыт моторный завод, где и сегодня собирают двигатели ŠKODA MPI 1.6. Производственные этапы включают в себя механическое обрабатывание блока цилиндров, коленчатого вала и непосредственно сборку всего ДВС, а по завершении изготовления производится тестирование всех функций.
Почему был выбран именно этот силовой агрегат? Все просто — данный атмосферный мотор устанавливается во многие модели, например в «РАПИД» и «ОКТАВИЮ», и является наиболее популярным у российских автомобилистов.
Отметим, что калужские двигатели принадлежат к прогрессивному семейству EA 211. Особенности конструкции этих ДВС позволяют им быстро настраиваться на рабочую температуру, меньше расходовать топливо и способствовать лучшему прогреву салона зимой.
ŠKODA активно сотрудничает с производителями компонентов для двигателей из России. Так, например, заготовки блока цилиндров и головки блока цилиндров поставляет компании Nemak из Ульяновска. Поставщик прекрасно зарекомендовал себя, работая со многими известными брендами, такими как Mercedes-Benz, BMW и Ferrari.
Где производят «ШКОДУ РАПИД»
RAPID относится к бюджетному сегменту автомобилей, и, соответственно, его стоимость должна быть максимально конкурентоспособной. Поэтому была организована сборка данной модели на заводе в Калуге, где производят «ШКОДУ РАПИД» уже на протяжении пяти лет.
Где собирают «ШКОДУ КОДИАК»
Изначально комфортабельный и солидный кроссовер KODIAQ поставлялся в нашу страну из Чешской Республики. Но из-за таможенных нюансов и организации транспортировки его стоимость была не вполне приемлема, а между тем интерес к модели в России был велик. Естественно, что концерном было принято решение о локализации.
В рекордно короткие сроки было организовано производство в Нижнем Новгороде, где и собирают «ШКОДУ КОДИАК» для российского рынка.
Где собирают «ШКОДУ ОКТАВИЮ»
Одним из основных двигателей продаж чешского концерна в России традиционно остается OCTAVIA. Модель завоевала доверие и безграничную симпатию россиян своей надежностью, комфортабельностью и гармоничным сочетанием цены и качества.
Появление новой модификации данного автомобиля подтолкнуло концерн укрепить позиции в России. В марте прошлого года было организовано локализованное производство в Нижнем Новгороде, где собирают «ШКОДУ ОКТАВИЮ» по методу CKD (полный цикл).
Google+
skoda.medved-abakan.ru
По мировым стандартам — ŠKODA
Пётр Линхарт и Оливер Грюнберг вдвоём руководят проектом концерна Volkswagen в Нижнем Новгороде. С прошлого года они проводят на ГАЗе по двенадцать часов в день. Сроки, отведённые на развёртывание производства, по-военному сжаты. Битва за рынок не терпит промедления.
Почему концерн Volkswagen пришел на ГАЗ, в то время как у него была зарезервирована площадка для строительства второй очереди завода в Калуге?
Да, планы по строительству второго завода, аналогичного первому, были, все возможности для этого есть и сейчас, но карты спутал кризис 2008 года. Автомобильный рынок в России очень сильно просел — а вкладываться в строительство нового предприятия, когда не совсем понятно, как будет загружено имеющееся, по меньшей мере странно, — и неожиданно быстро восстановился. Стало очевидным, что требуется придумать какой-то новый вариант. В 2010 году мы начали подготовку к заключению договора с ГАЗом, в июне 2011-го он был подписан.
Завод в Калуге выпустил продукцию по полному циклу через 37 месяцев после закладки первого камня. В партнерстве с ГАЗом мы уложились в рекордные 18 месяцев, потому что пришли на действующее предприятие. При этом на изготовление оборудования — оно на проекты такого масштаба делается под заказ — ушло восемь месяцев.
А крупноузловая сборка Yeti началась почти сразу.
Да, она началась прошлой осенью и продолжалась около года. Мы выпустили несколько тысяч автомобилей. Главной целью организации крупноузловой сборки было ознакомление персонала ГАЗа с автомобилем, с технологиями, с нашей культурой производства. Очень логичный подготовительный этап перед производством полного цикла.
По какой причине производство в Нижнем стартовало именно с модели Yeti?
Потому что Yeti — популярная в Европе и в России машина. Ее производство на 100 процентов отлажено на заводе в чешском городе Квасины. Нам было очень удобно зеркально копировать процесс. Volkswagen Jetta, который встанет на конвейер после Yeti, делают в Мексике — это несколько дальше, хотя и мексиканский завод мы посещали не раз, а к производству ŠKODA Octavia нового поколения только приступают в Чехии. Тем не менее выпуск Jetta и Octavia должен быть налажен на ГАЗе в 2013 году. Планируется, что основная доля выпуска придется как раз на Octavia, самую популярную модель ŠKODA во всем мире.
В чем вы видите преимущества ГАЗа как нового партнера концерна?
Их множество. Удобное расположение — недалеко и от Калуги, и от Москвы. Наличие собственного таможенного терминала. И конечно, главное — это люди. В Нижнем нам очень повезло с людьми. Они знают, что такое автомобильное производство, что такое дисциплина. На руку нам сыграл и тот факт, что до нашего появления ГАЗ получил опыт с проектом «Волга Сайбер» — все-таки в основе этой машины достаточно современная американская конструкция. Кстати, наши автомобили будут собирать на том же конвейере, на котором делали «Сайбер» — модернизация линии монтажа потребовалась, но не очень значительная.
На какой срок рассчитано сотрудничество с ГАЗом?
Контракт действует до 2019 года — к этому времени проект должен оправдать вложения. Будет ли продолжение, посмотрим. Скажу одно: концерн Volkswagen обычно приходит всерьез и надолго
На площадях ГАЗа есть куда развиваться?
У ГАЗа территория существенно больше, чем у завода Volkswagen в Вольфсбурге, самого большого по объему выпуска автомобильного предприятия в Европе. Так что возможности есть, но об этом говорить рано.
Какой объем выпуска запланирован в рамках проекта?
В перспективе — более 130 000 автомобилей в год. На эту цифру мы собираемся выходить поэтапно.
Три модели на конвейере — это предел?
В рамках данного проекта да. Но это не значит, что один раз наладив процесс, мы можем до 2019 года ничего не трогать. Не забывайте про то, что модели время от времени обновляются, что требует серьезной переналадки оборудования.
Сколько человек будет задействовано в проекте?
С обеих сторон, то есть ГАЗа и концерна Volkswagen, более 3000 сотрудников.
Чем займутся сотрудники Volkswagen?
Прежде всего их задача состоит в том, чтобы помочь отладить процессы.
Каков средний возраст персонала?
30–35 лет. Работники концерна еще моложе.
Какие средства инвестируются в проект?
Общая сумма инвестиций до 2018 года составляет более 300 миллионов евро. 85 миллионов вкладывает «Группа ГАЗ», остальное — концерн Volkswagen через свою дочернюю структуру «Фолькваген Груп Рус».
Как стороны решают, кто и во что вкладывает деньги?
ГАЗ инвестирует в общую инфраструктуру, в то оборудование, которое может быть использовано при производстве разных машин, не только наших. Мы — в специфический инструмент, часто сделанный по уникальным, запатентованным технологиям. Приведем понятный пример. Робот, задействованный на сварке, покупает ГАЗ, поскольку это универсальное оборудование, а сварочные клещи, которыми действует робот, покупаем мы — они сделаны по нашей спецификации для изготовления именно наших автомобилей. Помимо того, мы будем инвестировать средства в производство комплектующих на территории России. Эти деньги тоже учтены в смете.
Куда будут направлены первые Yeti, сделанные по полному циклу в Нижнем Новгороде?
Пробные 15 автомобилей давно уже находятся на испытаниях. Их произвели до торжественного запуска конвейера. Ресурсные тесты, когда машина в течение нескольких недель каждый день проезжает от 800 до 1000 километров, проходят в Калужской области. Часть машин отправили в Чехию. Их тщательно изучат, а несколько штук разобьют. Краш-тесты должны подтвердить, что автомобиль как был, так и остается отличником в плане безопасности, вне зависимости от места производства.
На заводе в Нижнем Новгороде вы установили какие-то дополнительные меры по контролю качества выпускаемой продукции?
Зачем? Концерн Volkswagen делает автомобили на 99 предприятиях, расположенных в 27 странах мира: от Германии до Аргентины. Тем мы и сильны, что везде внедряем одинаковые стандарты и одинаково жестко следим за их выполнением. Неужели вы думаете, что русские рабочие чем-то хуже других? Поверьте: у вас замечательные люди. И наш опыт в Калуге говорит о том же: ее продукция по качеству не уступает чешской — таковы данные исследований.
Имплантировать новое производство в действующий завод — сложнейшая задача. Кто разработал проект? Отдел планирования ŠKODA в Млада-Болеславе при поддержке специалистов концерна.
Какой язык считается рабочим на производстве?
Тот, на котором мы сейчас с вами разговариваем, — русский. Volkswagen и ŠKODA пришли в Россию надолго.
www.skoda-avto.ru
Где собирают Шкоду Октавия — официальные сайты производителей шкоды |
Кратко четко без воды о том, где собирают автомобиль Шкода Октавия.
Какие модификации и в каких странах.
В статье: список, в каких городах можно купить эту машину, три видео ролика как собирают шкоду в Чехии, Калуге и Нижнем Новгороде и видео — сравнение сборки чешская для Германии и русская.
Так же, размещаю официальные сайты Шкоды тех стран, где они производятся.
Часто спрашивают официальные сайты заводов Шкоды в Калуге и Н.Н.
Таких сайтов нет./на момент написания статьи/
Максимум, что есть в инете — сайт ФОЛЬКСВАГЕН Груп Рус — volkswagengrouprus.ru на котором размещена инфа об этих заводах и их адреса.
Что ж, до изучения этой темы, я думал, что Шкоду Октавию собирают только в Чехии и Калуге.
Но посерфил инет, и нашел: (если что упустил, поправьте)
На данный момент у Skoda есть 10 заводов производящих автомобили
Чехия: официальный сайт http://new.skoda-auto.com/en
Более полные контакты завода в Чехии, e-mail написал здесь >>
Млада-Болеслав основной завод- Skoda Octavia
Врхлаби сборочный — Skoda Octavia Tour и Skoda Octavia.
Квасины сборочный — Roomster, Yeti и Superb.
Россия: официальный сайт Шкоды Авто в России skoda-avto.ru
Контакты представительства Шкоды в Москве смотрим здесь >>
Калуга — Octavia, Fabia.
Нижний Новгород — Yeti Octavia
Украина: skoda.com.ua официальный сайт Шкоды Авто в Украине
Соломоново – Octavia Fabia Суперб, Йети и Румстер
Казахстан: официальный сайт Шкоды Авто в Казахстане» skoda-auto.kz
Усть-Каменогорск — Superb, Yeti, Fabia Octavia Рапид
Китай
Шанхай — Yeti, Superb, Octavia, Rapid и Fabia
Индия
Пуна, Аурангабад – Fabia Octavia Рапид Superb, Yeti skoda-auto.co.in
Сараево Босния и Герцеговина – выпускалась Фабия. С 2008 года производство прекращено.
Словакия – с 2010 Skoda – Octavia не выпускается.
Сравнение сборки чешская для Германии и русская — различия — 1-я часть >>
Сравнение сборки чешская для Германии и русская — различия — 2-я часть >>
Список, в каких городах можно купить Шкоду
Москва, Санкт-Петербург, Архангельск, Астрахань, Барнаул, Белгород,
Великий Новгород, Верхняя Пышма, Владимир, Волгоград, Вологда, Воронеж,
Екатеринбург, Иваново, Ижевск, Иркутск, Казань, Калининград, Калуга, Каменск-Уральский,
Кемерово, Киров, Кострома, Краснодар, Красноярск, Курск, Липецк, Магнитогорск,
Минусинск, Мурманск, Набережные Челны, Нижний Новгород, Нижний Тагил,
Новокузнецк, Новомосковск, Новороссийск, Новосибирск, Октябрьский, Омск, Орел,
Оренбург, Пенза, Пермь, Петрозаводск, Пятигорск, Ростов-на-Дону, Рязань, Самара,
Саратов, Северодвинск, Сочи, Ставрополь, Стерлитамак, Сургут, Сыктывкар, Тверь,
Тольятти, Томск, Тула, Тюмень, Улан-Удэ, Ульяновск, Уфа, Хабаровск, Челябинск,
Череповец, Ярославль
Как собирают Skoda в Чехии
Производство Skoda в Нижнем Новгороде
www.avtopol-msk.ru
Люди и роботы: как делают Skoda Rapid в Калуге
Человек всегда мечтал о появлении устройств, способных выполнять за него сложную работу. И вместе с этими мечтами появились и размышления о том, как же будут строиться отношения машин и человека, когда эти мечты станут реальностью? В общем, никаких роботов еще не было и в помине, а Карел Чапек уже писал свою знаменитую пьесу «R.U.R, или Россумские универсальные роботы». А уж когда в 1961 году компания Unimation начала продажу настоящих, а не вымышленных промышленных роботов (правда, совершенно не похожих на человека), проблема вышла из общефилософской в абсолютно практическую плоскость.
Сегодня роботы стали символами современной автомобильной промышленности (кстати, автопром всегда был на переднем крае роботизации — самые первые промышленные роботы были применены на заводах GM). И когда компания Skoda пригласила меня познакомиться с тем, как производят автомобили чешской марки на заводе в технопарке Грабцево около Калуги, то я уже знал, что именно вопрос организации совместной работы людей и роботов будет интересовать меня в первую очередь.
Представители Volkswagen Group неоднократно заявляли, что этот завод является самым технологичным, самым автоматизированным и роботизированным производством из всех автозаводов иностранных производителей, построенных на территории РФ.
Собственно, у проектировавших завод инженеров концерна и не было никакого другого выхода, кроме как максимально насытить предприятие электронными системами контроля и управления, ведь изначально планировалось, что с одной конвейерной линии будут, чередуясь, сходить несколько моделей, относящихся к разным брендам. Естественно, это создает определенные сложности.
Вот, скажем, работает отдельный пост на конвейере. Одно дело, когда раз за разом на этом посту нужно проделывать одни и те же операции, и совсем другое, когда на пост поступает то один кузов, то совсем другой, и операции с ним требуют сменить инструмент и выбрать разные комплектующие.
Может быть, зря они все это затеяли, может быть, проще было бы организовать отдельные линии? Ведь на некоторых заводах пошли именно по пути разделения производственных потоков. Но в VW Group уверены, что все сложности вполне преодолимы на современном уровне развития технологий, а выигрыш в гибкости производства вместе с экономией места и более эффективным использованием трудовых ресурсов окупает все затраты.
Логистика
Когда я ехал на завод (кстати, на Skoda Rapid локальной сборки, и о своих впечатлениях от этого автомобиля я обязательно расскажу отдельно), то слегка промахнулся с поворотом с трассы. В итоге мне пришлось объехать предприятие по периметру. Но нет худа без добра: да, пришлось проехать пару лишних километров, зато я смог в полной мере ощутить масштабы впадающей в предприятие логистической реки.
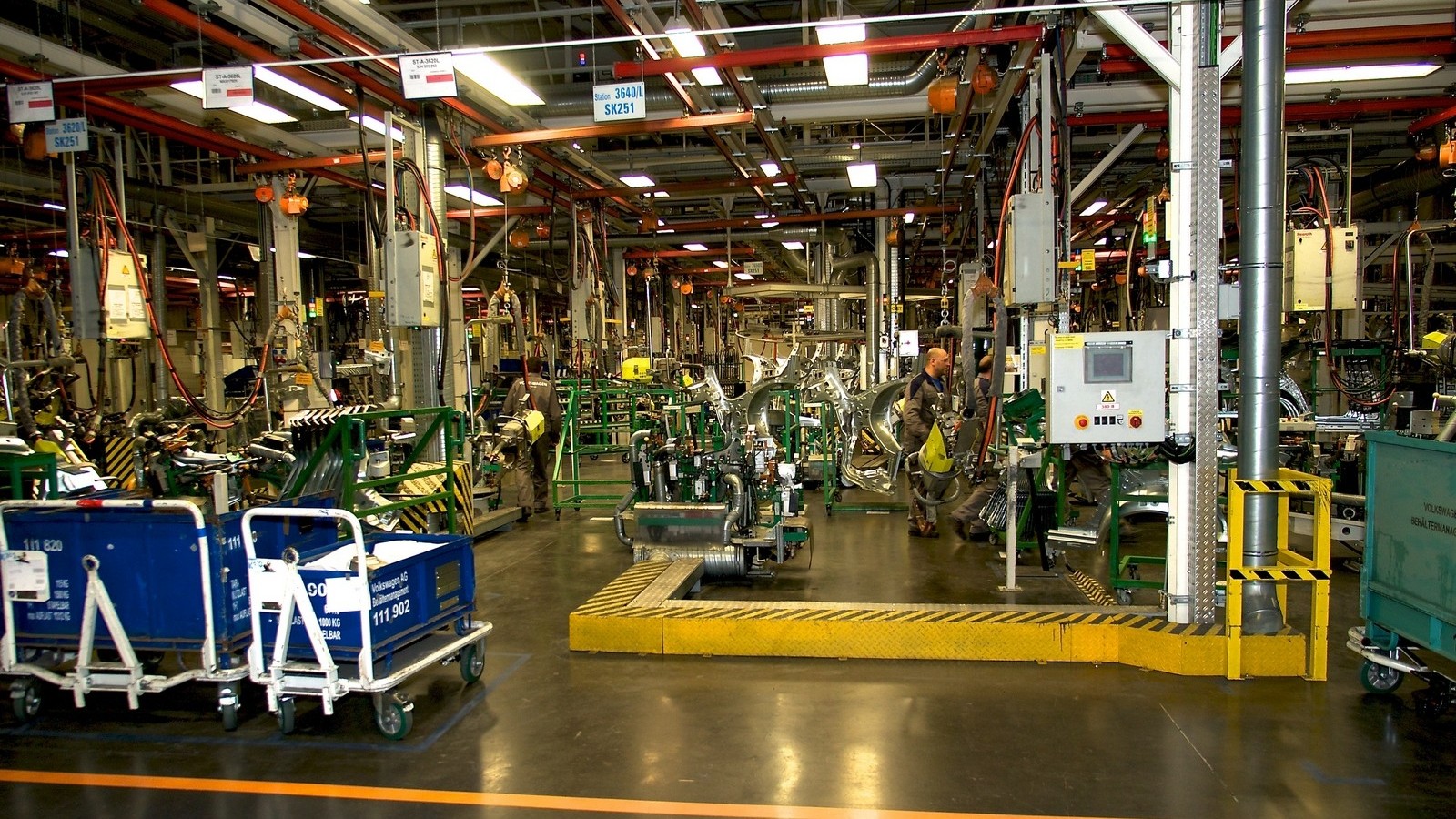
Бесконечная череда разноцветных железнодорожных контейнеров, специальные погрузчики-ричстакеры на огромных, в рост человека, колесах, собственная таможня… Ведь все необходимое для сборки Skoda Rapid поставляется со множества предприятий, расположенных как у нас в стране, так и за рубежом. И всю эту полноводную реку нужно рассортировать и разделить на множество отдельных ручейков, каждый из которых нужно отправить точно в заданную точку технологической цепочки.
Производство
Ну а теперь давайте прогуляемся вдоль другой реки, производственной. Здесь будет происходить обратный процесс: ручейки отдельных заготовок и комплектующих шаг за шагом будут сливаться воедино, чтобы в конце пути превратиться в сияющие лаком новые машинки на площадке готовой продукции.
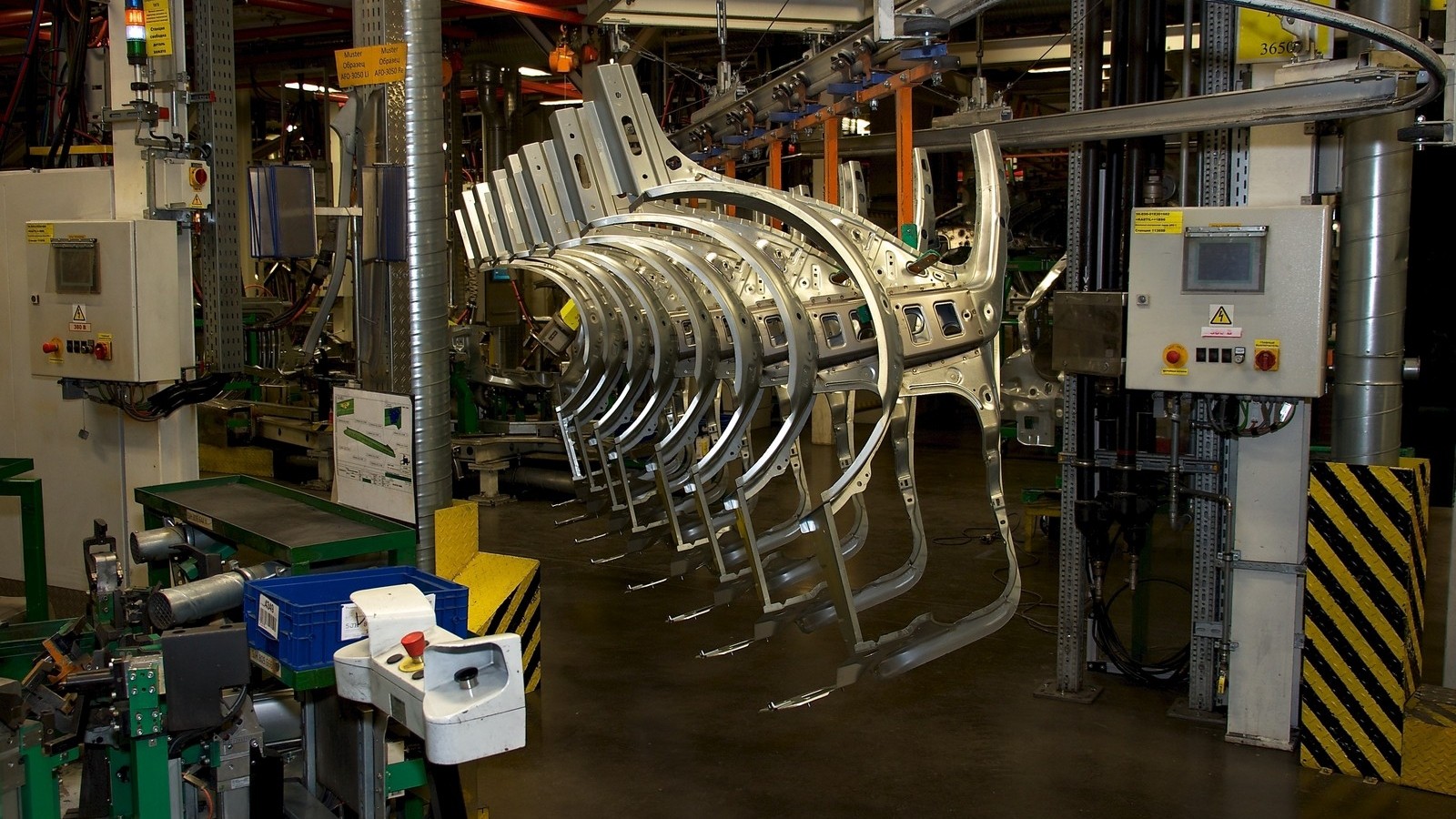
Естественно, все начинается со сварки кузова… «В начале времен» кузов представляет собой набор неких железок, причем некоторые из них выглядят весьма декоративно, а некоторые — откровенно загадочно, и даже человеку, в принципе знакомому с устройством современного автомобиля, совсем не просто определить, для чего нужна та или иная штампованная деталь.
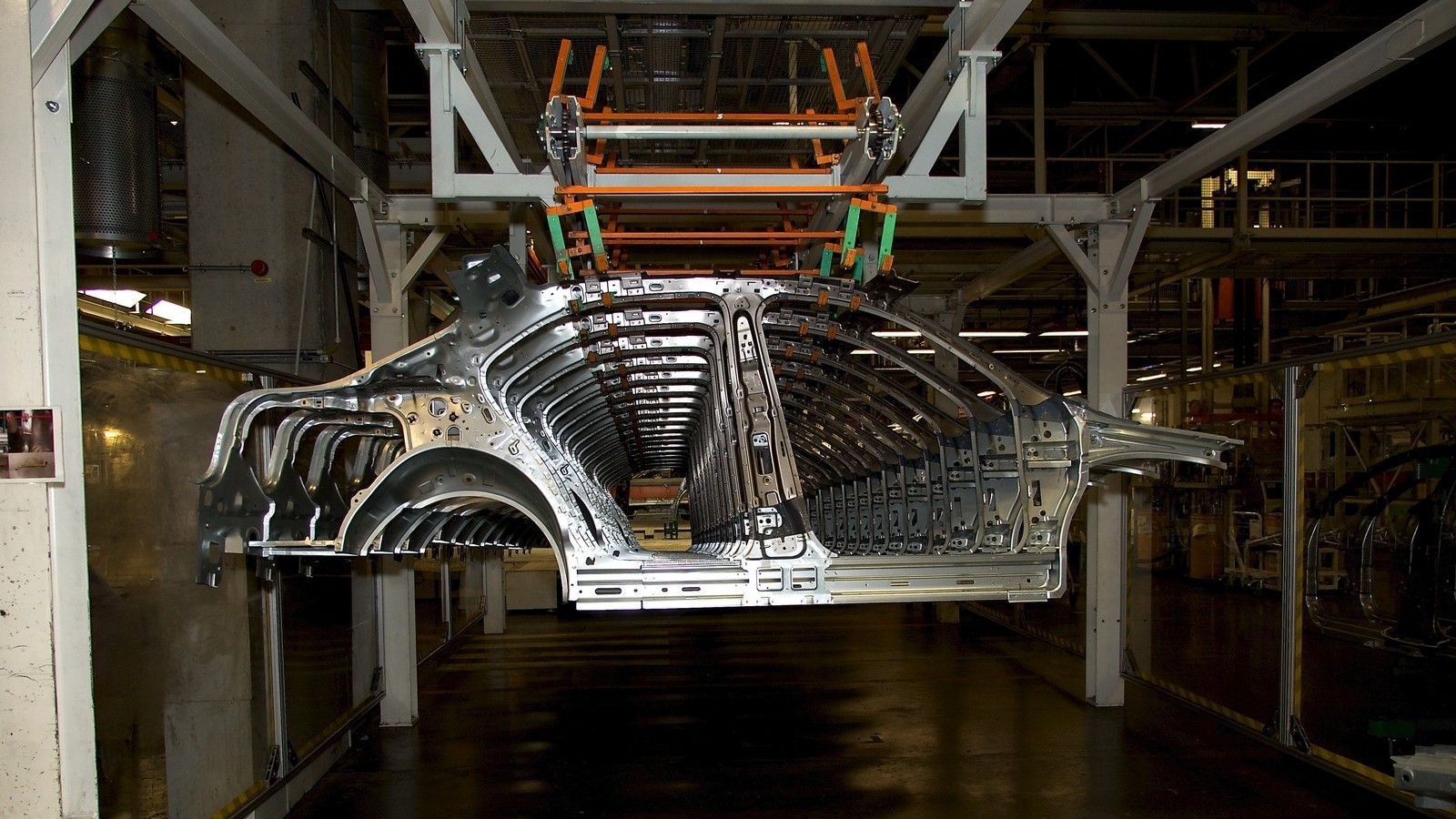
На первом этапе из этих железяк собираются более крупные блоки. Эта работа в основном производится на кондукторах, при помощи сварочных клещей, которыми управляют люди. Впрочем, и на этой стадии есть операции, отданные на откуп роботам.
Например, на пост поступает боковина кузова. Рабочие устанавливают боковину в специальный держатель, берут два кронштейна, к которым впоследствии будут крепиться фары, и просто-напросто приклеивают их на предназначенные для этого места: на стеллажах лежат детали с уже нанесенными на них порциями клея. После этого робот проверяет точность установки, держатель поворачивается и отправляет узел в камеру, где за дело принимается автомат лазерной сварки. Людям ход в камеру закрыт, а проконтролировать процесс можно только наблюдая за картинкой на специальном мониторе.
Мне вообще бросилось в глаза широкое использование клеевых соединений. Чаще всего они работают вместе с лазерной сваркой и пайкой, одновременно и в роли флюса, и в роли герметизатора получающегося стыка. На заводе вообще очень гордятся использованием такого технологически продвинутого приема как лазерная пайка.
Организовано это так: сначала две работницы при помощи специальных пистолетов наносят вдоль всей линии соединения крыши с боковинами аккуратные «колбаски» клея, затем, оперируя манипулятором, устанавливают крышу, и кузов отправляется в камеру, где работает робот. В итоге крышу соединяют с боковинами аккуратные полоски припоя. Такое соединение, по мнению инженеров завода, не только обеспечивает полную герметичность, но и серьезно повышает общую жесткость кузова, а жесткость, как вы знаете, является ключевым элементом улучшения управляемости. Шлифовку получившегося стыка также выполняет робот.
Впрочем, простите, тут я несколько забежал «вниз по течению». Ведь на вклейку крыши поступил уже сформированный кузов, а этот процесс полностью отдан роботам. Сначала подготовленные крупные блоки поступают в массивный станок-фреймер, который соединяет и сжимает их вместе, обеспечивая идеальную точность геометрии всей сборки. Этот станок тоже по своей сути является настоящим роботом, поскольку он точно знает, кузов какой модели ему предстоит собрать, и в процессе сборки и закрепления сваркой собранных блоков постоянно контролирует процесс, производя множество измерений (для этого, естественно, также используются лазеры).
Ну а потом кузов перемещается на пост, где на него накидывается целая стая сварочных роботов, удивительно похожая на группу терзающих жертву хищных динозавров. Но финальные операции производят все-таки люди, причем в них используется не только точечная электросварка, но и сварка в струе смеси аргона с углекислотой. Удивительное, завораживающее зрелище: ярко-голубое пламя, совершенно не похожее на оранжевые сполохи точечной сварки, и операторы, одетые в защитные костюмы, похожие на скафандры космонавтов из фантастического триллера.
Наконец, готовый кузов отправляется на окраску. Там с ним тоже будут работать преимущественно роботы: человеку в этот процесс вмешиваться, по сути, незачем. В процессе производства кузова роли человека и «искусственного интеллекта» постоянно меняются, на каких-то этапах основную работу выполняют роботы, а люди действуют «на подхвате», на каких-то — наоборот, главные операции осуществляют люди, а роботам отданы функции помощников и контролеров.
Испытания
Ну а мы отправимся на очень важный участок, где работают исключительно специалисты самой высокой квалификации, и без которого автомобили Skoda не смогли бы стать эталоном качества и надежности. Вы, наверное, поняли, что речь идет о заводской испытательной лаборатории.
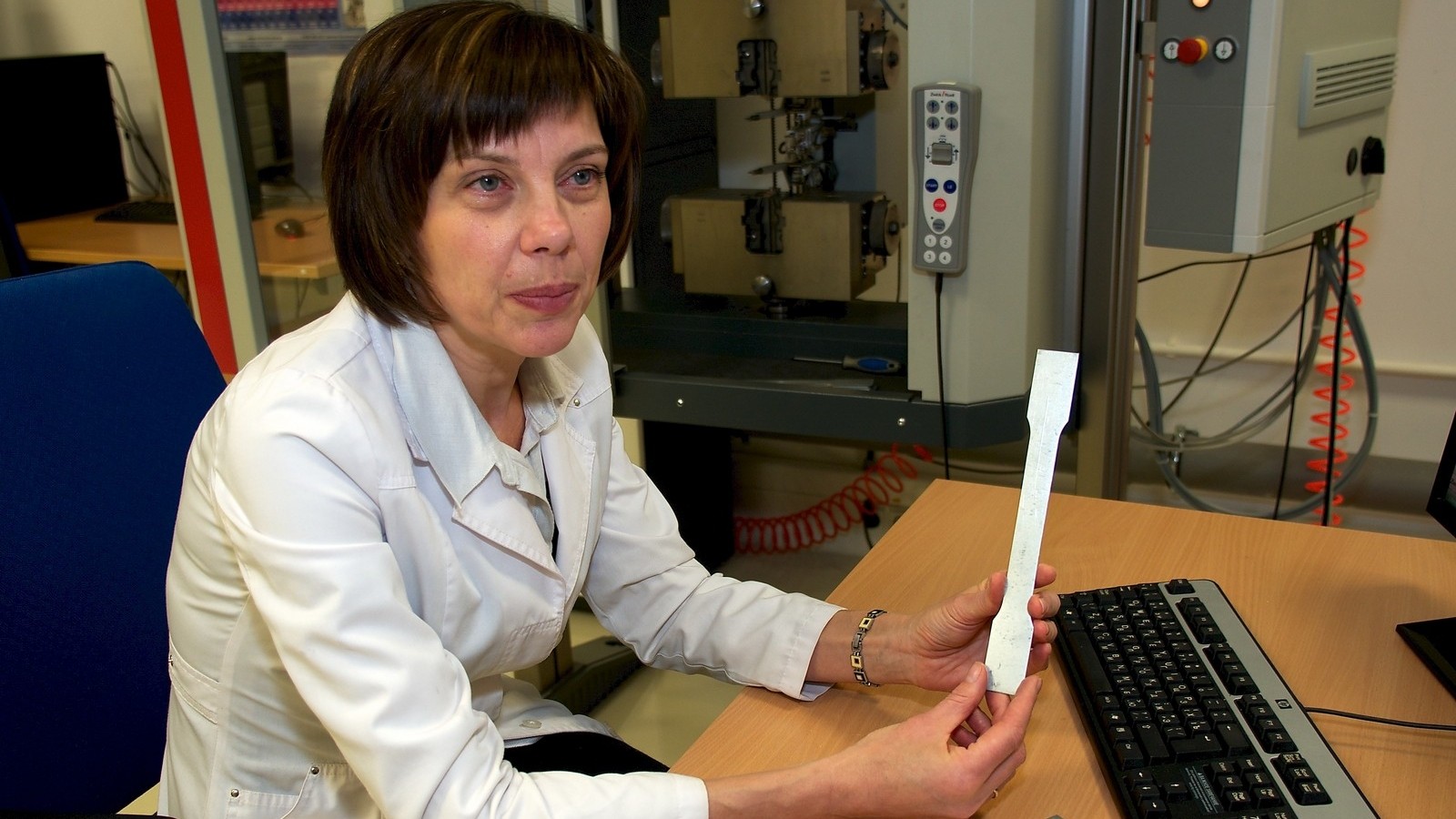
Здесь проверяется все: и материалы, и готовые изделия, поступающие от смежников на сборочный конвейер. И, естественно, через строгие лабораторные проверки проходит любое изделие отечественных производителей, претендующее на замену импортной продукции в рамках программы локализации. А уж разнообразие исследований, которые проводятся в лаборатории, меня просто потрясло.
Например, колористика: любая деталь внешнего оформления автомобиля или его салона должна сочетаться по цвету с соседними. Естественно, используются и точные измерения, но самым главным прибором тут является глаз человека. Но и этот инструмент нуждается в проверке, и для этого служит специальный тестовый набор, состоящий из отдельных «фишек» разного цвета. Фишки перемешиваются, и испытуемому предлагается расставить их по градиенту. Результаты теста обсчитывает специальная программа, и компьютер выдает заключение: можно или нет доверить человеку сравнение цвета той или иной детали с эталоном. Естественно, сравнение производится при стандартном освещении лампой с заданной цветовой температурой.
Или, например, такой тест: в лаборатории есть специальные составы, позволяющие имитировать воздействие на пластиковые детали разнообразной парфюмерии, прежде всего — кремов для рук и солнцезащитных мазей. Но это не самое жестокое испытание, которому подвергаются детали автомобиля.
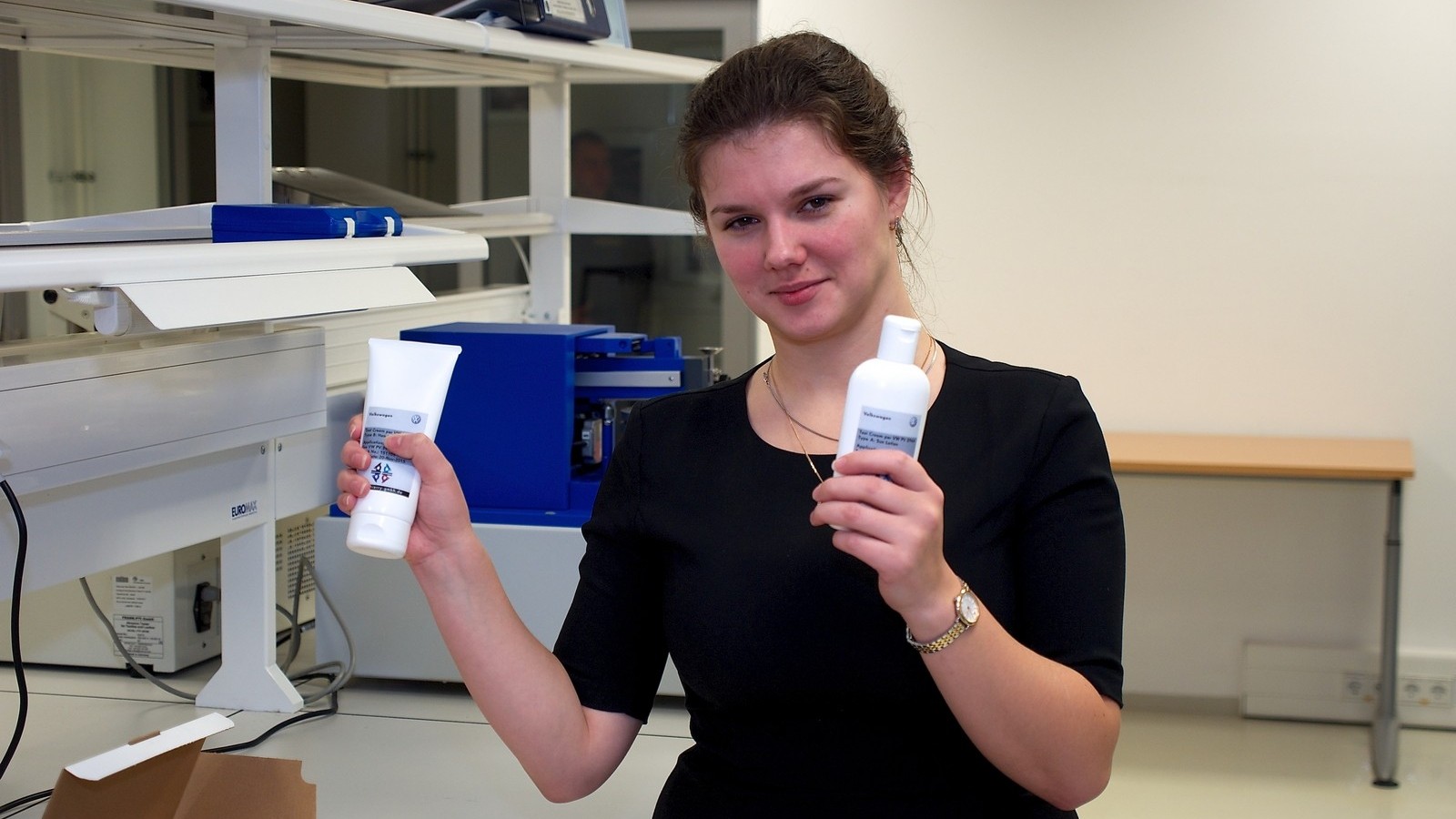
Перед тем, как получить допуск на конвейер, им предстоит мерзнуть и жариться в термокамерах, выдержать пытку водой и в специальной камере с соляным туманом, доказать свою устойчивость к ультрафиолетовому излучению и открытому огню. Способность внешних деталей противостоять «пулеметному обстрелу» гравием, летящим из-под колес автомобилей, проверяется на специальном испытательном стенде, получившем у сотрудников название «Синий слон».
Важным испытательным инструментом становится и обычная ручная мойка высокого давления. На окрашенную деталь, подвергавшуюся в течение определенного времени воздействию жары, холода и солнечного света, наносятся крестообразные царапины, на которые и направляется струя воды под давлением. Лакокрасочное покрытие не должно отслаиваться…
Детали из листового металла подвергаются испытаниям на разрыв, а крепежные элементы и сварные соединения разрезаются, заливаются в специальный пластик, шлифуются и исследуются под микроскопом.
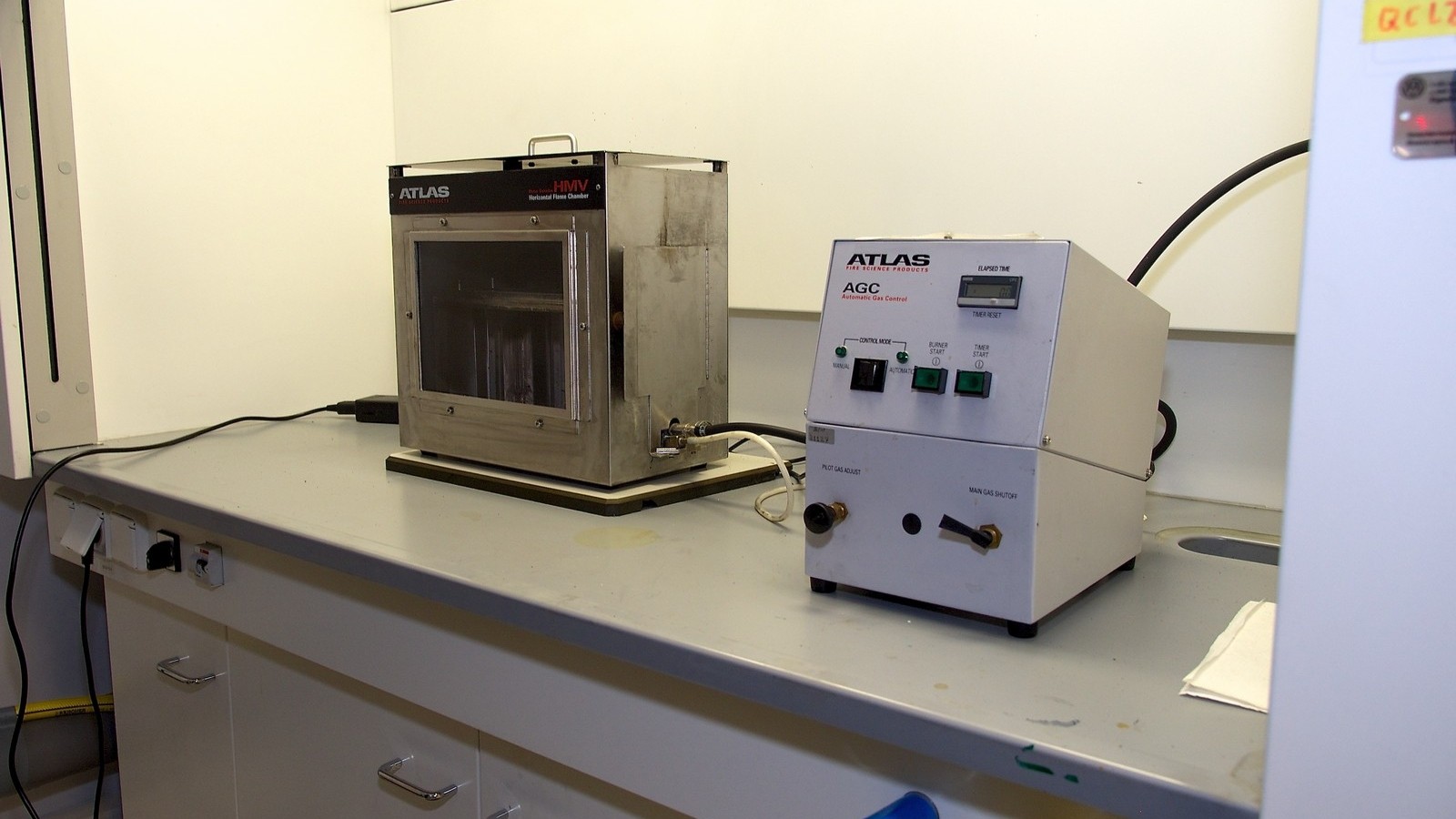
Выпуск моторов
Есть, кстати, собственная лаборатория и на моторном производстве. Там свои задачи. Например, проверить все технические жидкости, которые будут залиты в собранные моторы. Или на специальном стенде с переменными нагрузками изучить предельные возможности коленчатого вала.
Вообще, моторное производство — самое молодое на Калужском заводе VW Group. Его запустили только год с небольшим назад, в сентябре 2015-го. Тем не менее, значение его огромно: во-первых, это позволило резко увеличить процент локализации, а во-вторых, получая сделанное в России сердце, автомобиль начинает восприниматься как по-настоящему отечественный. В Грабцево производят 1,6-литровый атмосферник новейшего модульного семейства ЕА211, в двух вариантах по мощности, 90 и 110 л. с. Именно на версии с этими моторами приходится львиная доля продаж Skoda Rapid в России.
Само расположенное в отдельном корпусе производство поражает своим малочисленным персоналом. Человек в этом царстве автоматики — лишь помощник, обеспечивающий бесперебойную работу линии. Например, сотрудник совершает предмонтаж шатунов на специальном поворотном столе, который служит для установки поршней с шатунами в хонингованный блок и подачи подготовленных деталей роботу. Или человек вкладывает датчик положения коленвала в предназначенное для него гнездо, а запрессовку производит автомат. И так — по всей сборочной линии… Ведь любой человек может ошибиться, а автоматика ошибаться не умеет в принципе.
Более того, каждый переход собираемого двигателя с одного поста на другой возможен лишь после того, как электроника проверит качество произведенной операции и даст добро. Впрочем, последний контроль, после которого на двигатель приклеивается табличка с уникальным штрих-кодом, производит все-таки человек.
Сборка
А теперь вернемся к обещанному в заголовке — к производству Skoda Rapid. Итак, сваренные и окрашенные кузова после обязательных проверок поступают на линию сборки. И тут снова человек выходит на первые роли. Наверное, можно было бы научить роботов укладывать электропроводку, монтировать приборные панели и пластиковые детали интерьера. Только вот сколько будут стоить такие роботы? Ведь одно дело — жесткие кузовные детали, которые можно четко позиционировать в пространстве, другое — жгуты проводки. Так что здесь оказывается выгоднее доверить большую часть операций хорошо обученным сборщикам, максимально облегчив их работу средствами малой механизации.
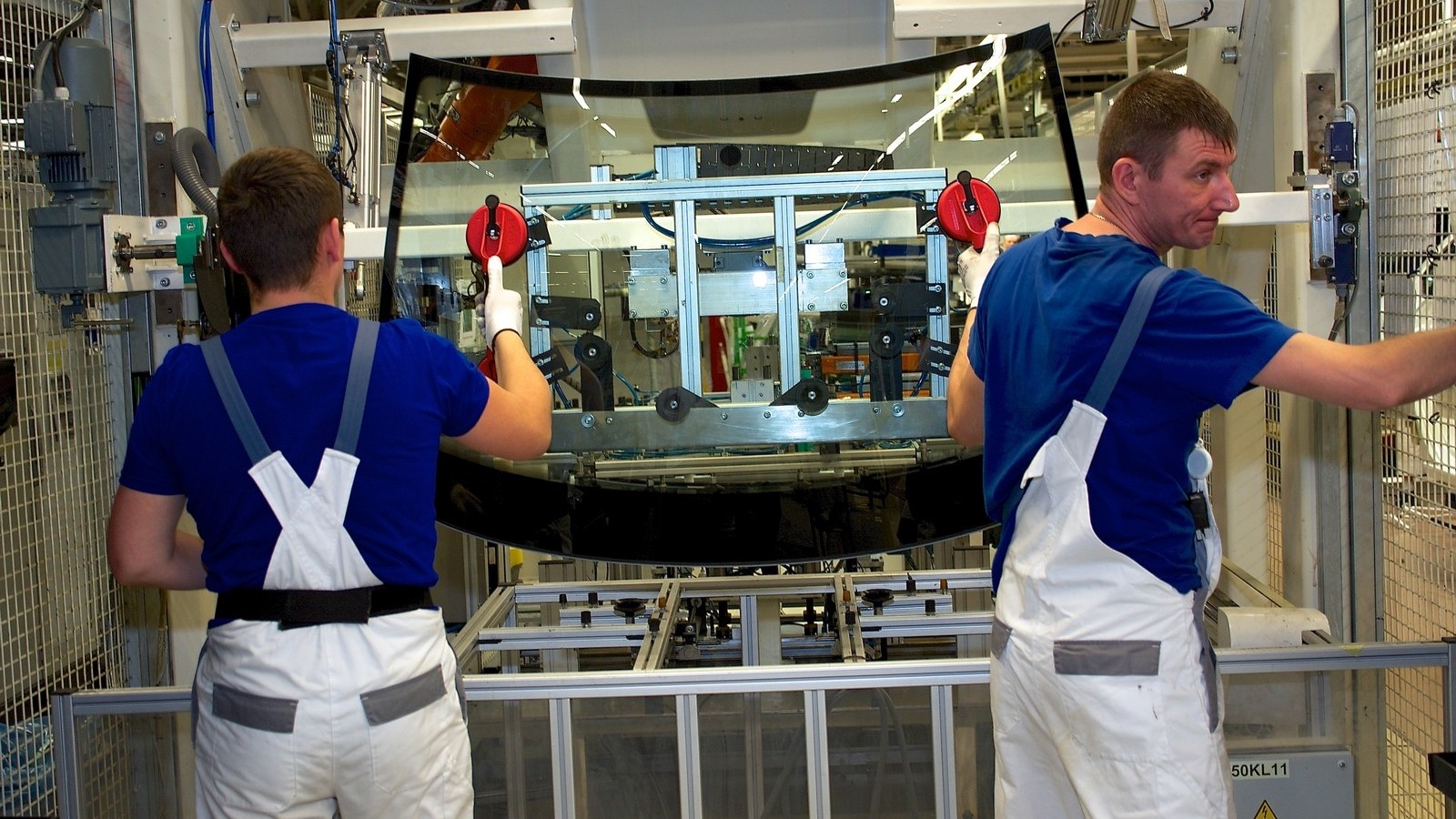
Мне, например, очень понравилось подвижное кресло, подвешенное на консольную балку. Рабочий садится в кресло и въезжает в салон, как Иванушка в печь на лопате Бабы-Яги. Впрочем, роботы на сборочной линии тоже есть: например, клей на лобовое и заднее стекла наносит робот, затем два монтажника «хватают» стекло при помощи вакуумных присосок и уже вручную ставят его на место.

Конечно же, автоматизирован и самый главный этап сборки, так называемая «свадьба». По нижней ветви конвейера подается собранная ходовая часть с двигателем и трансмиссией, по верхней — практически готовый кузов. Их взаимное положение выверяется с микронной точностью. Несколько секунд — и вот на посты окончательного монтажа движется уже не «кузов», а автомобиль. Остается навесить двери, установить фары, колеса, пластиковый обвес — и новенький Rapid готов отправиться на тестовый трек, а затем — на площадку готовой продукции.
За годы журналистской работы мне пришлось побывать на очень многих автосборочных производствах. Я видел и вообще практически безлюдные сборочные линии, где даже комплектующие на конвейер доставляли беспилотные тележки-дроны, и относительно недавно запущенные заводы, где все сварочные операции производят люди со сварочными клещами.
На самом деле, то, какой именно вариант распределения ролей между людьми и роботами будет выбран на конкретном заводе, определяется не «отсталостью» или «продвинутостью», а такими приземленными вещами, как экономика производства и стоимость рабочей силы.
В Калуге, на мой взгляд, нашли весьма точный баланс, отлично подходящий к нашей экономической реальности. Ведь покупателю Skoda Rapid абсолютно все равно, выполнена та или иная операция рукой живого человека или железным манипулятором робота. Ему важно, чтобы операция эта была выполнена безукоризненно, чтобы в итоге он получил качественный и надежный автомобиль, за который он будет готов проголосовать своим трудовым рублем.
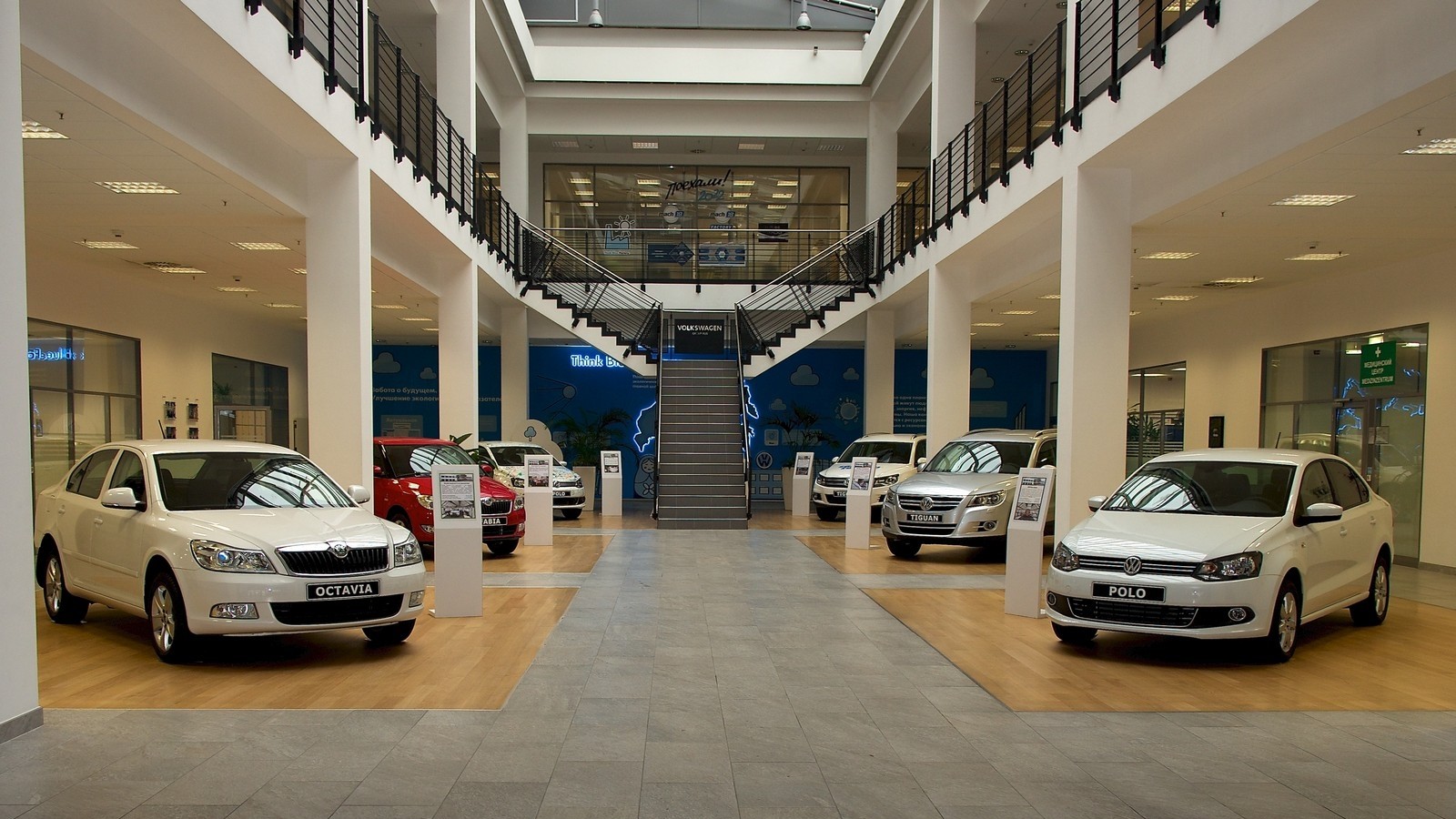
www.kolesa.ru
Начало производства Кодиак в России
На днях, на мощностях завода «Группы ГАЗ» в Нижнем Новгороде стартовало производство чешских кроссоверов Шкода Кодиак, анонс которых был еще в прошлом году.
Сразу после того, как новинку анонсировали, к ней начал проявляться немалый интерес со стороны автолюбителей.
Это объясняется эффектным экстерьером автомобиля и обширной функциональностью, которая способна удовлетворить даже самых требовательных пользователей.
Skoda Kodiaq российской сборки получит полный набор комплектаций, в которых имеется два вида силового агрегата с объемами 1.4 и 2.0 литра.
Мощность моторов составляет 125 и 180 лошадинных сил соответственно. Стоит отметить, что впервые для отечественной аудитории, Volkswagen Group Rus представил двигатель 1.4 TSI, как с передним приводом, так и с задним.
Все доступные на данный момент трансмиссии этого автомобиля, также будут доступны российскому покупателю.
Особенности производства Шкоды Кодиак в России
Для нового автомобиля в России Фольксваген Груп Рус выделила 87 миллионов евро. Значительную часть инвестиций вложили в проверку качества.
Срок подготовки составил целых восемнадцать месяцев. Рабочий персонал завода ГАЗ, также подготовился. Сотрудники прошли полный курс обучения и специальную подготовку в городах Чехии, где уже вовсю идет сборка и выпуск Кодиака.
Производство чешского кроссовера будет осуществляться по полному циклу. Это означает, что на производственную площадку буду поставляться уже готовые детали и устанавливаться непосредственно в Нижнем Новгороде.

Компоненты будут подвергаться сварочным работам, антикоррозийной обработке (фирменной от Volkswagen), грунтовке и покраске.
Окончательная сборка модели подразумевает монтаж силовой установки, коробки переключения переда, стекол, сидений и ряд других рабочих операций.
Производитель делает ставку на учинение позиций на российском рынке. Кроме этого, российское производство, позволит своевременно реагировать на изменение автомобильных тенденций в России.
Стоимость машины, произведенной в Нижнем Новгороде будет явно ниже, что является несомненным плюсом.
Важный шаг для Skoda
Член совета директоров Skoda Михаэль Оэльклаус отметил, что начало производства кроссовера Kodiaq в России — это серьезный и важный шаг в стратегии развития марки Skoda. Также, он добавил, что основной объем продаж в РФ приходится на те машины, которые здесь и собрали.

Это не только выходит дешевле для клиента, но и удобно для производителя, ведь не нужно тратить время и средства на поставки.
Мощности завода ГАЗ были выбраны в качестве конвейера для чешского кроссовера неспроста. Дело в том, что Volkswagen Group Rus уже выпустил несколько полноцикловых автомобилей совместно с ГАЗ. К ним относятся, Skoda Octavia и Yeti, а также Volkswagen Jetta.
Цены и плюсы Skoda Kodiaq
Прайс на кроссовер еще появлялся, но ожидается со дня на день. На данный момент точных данных о компиляциях и о том, во сколько они обойдутся нет.
Известно только о моторной гамме Skoda Kodiaq. Если верить главе российского подразделения чешской компании Яну Прохазке, то Skoda планирует выпускать в России до 30 тысяч кроссоверов в год.
Перовое ознакомление с автомобилем вызывает только положительные эмоции. Кодиак имеет:
- отличную эргономику;
- большой салон;
- высокий клиренс;
- оригинальный, привлекательный дизайн;
- вместительный багажник.
Преимуществ перед конкурентами у новинки более чем достаточно. Так что она должна очень быстро завоевать доверие отечественных автомобилистов. Допускается вероятность того, что российские кроссоверы Kodiaq будут поставляться за рубеж.
skoda-auto2.ru