ΠΠ°ΡΠ±ΠΎΠ½ΠΎΠ²ΡΠ΅ ΠΊΠΎΠ»Π΅ΡΠ½ΡΠ΅ Π΄ΠΈΡΠΊΠΈ Π΄Π»Ρ Π°Π²ΡΠΎΠΌΠΎΠ±ΠΈΠ»Ρ
Π₯ΠΎΡΠ΅ΡΡ Π΅Π·Π΄ΠΈΡΡ Π±ΡΡΡΡΠΎ β ΡΠ±ΠΈΡΠ°ΠΉ Π²Π΅Ρ Π²Π΅Π·Π΄Π΅, Π³Π΄Π΅ ΠΌΠΎΠΆΠ½ΠΎ. ΠΡΠΈΠΌΠ΅ΡΠ½ΠΎ ΡΠ°ΠΊΠΈΠΌ Π΄Π΅Π²ΠΈΠ·ΠΎΠΌ ΡΡΠΊΠΎΠ²ΠΎΠ΄ΡΡΠ²ΡΡΡΡΡ ΡΠ°Π·ΡΠ°Π±ΠΎΡΡΠΈΠΊΠΈ ΡΡΠ°Π½ΡΠΏΠΎΡΡΠ½ΡΡ ΡΡΠ΅Π΄ΡΡΠ², ΠΏΠΎΡΡΠΎΡΠ½Π½ΠΎ Π½Π°Ρ ΠΎΠ΄Ρ Π½ΠΎΠ²ΡΠ΅ ΡΠ΅ΡΠ΅Π½ΠΈΡ, ΠΈβ¦ Π½ΠΎΠ²ΡΠ΅ ΠΌΠ°ΡΠ΅ΡΠΈΠ°Π»Ρ Π΄Π»Ρ ΡΠ°Π·Π»ΠΈΡΠ½ΡΡ ΡΠ·Π»ΠΎΠ² ΠΈ Π΄Π΅ΡΠ°Π»Π΅ΠΉ. Π ΡΠ»ΡΡΠ°Π΅ Ρ ΠΊΠΎΠ»Π΅ΡΠ½ΡΠΌΠΈ Π΄ΠΈΡΠΊΠ°ΠΌΠΈ Π²ΡΠ±ΠΎΡ Π½Π΅ ΡΠ°ΠΊ ΡΠΆ Π²Π΅Π»ΠΈΠΊ, Π²Π΅Π΄Ρ ΠΊΡΠΎΠΌΠ΅ ΠΌΠ°Π»ΠΎΠ³ΠΎ Π²Π΅ΡΠ° ΠΎΠ½ΠΈ Π΄ΠΎΠ»ΠΆΠ½Ρ ΠΈΠΌΠ΅ΡΡ Π²ΡΡΠΎΠΊΠΈΠΉ Π·Π°ΠΏΠ°Ρ ΠΏΡΠΎΡΠ½ΠΎΡΡΠΈ.
ΠΠ΄Π½ΠΈΠΌ ΠΈΠ· Β«ΠΏΠΎΠ΄Ρ ΠΎΠ΄ΡΡΠΈΡ Β» Π²Π°ΡΠΈΠ°Π½ΡΠΎΠ² ΠΌΠΎΠΆΠ½ΠΎ Π½Π°Π·Π²Π°ΡΡ ΠΊΠ°ΡΠ±ΠΎΠ½ β ΠΊΠΎΠΌΠΏΠΎΠ·ΠΈΡΠ½ΡΠΉ ΠΌΠ°ΡΠ΅ΡΠΈΠ°Π» ΠΈΠ· ΡΠ³Π»Π΅ΡΠΎΠ΄Π½ΡΡ Π²ΠΎΠ»ΠΎΠΊΠΎΠ½, ΡΠΏΠ»Π΅ΡΠ΅Π½Π½ΡΡ Ρ ΡΠ΅Π·ΠΈΠ½ΠΎΠΉ ΠΈΠ»ΠΈ ΠΊΠ΅Π²Π»Π°ΡΠΎΠΌ. ΠΡΠ»ΠΈ Ρ Π²Π΅Π»ΠΎΡΠΈΠΏΠ΅Π΄Π°ΠΌΠΈ Π²ΡΠ΅ ΠΏΡΠΎΡΡΠΎ β Ρ ΠΎΡΡ Π²Π΅ΡΡ ΠΈΠ· Π½Π΅Π³ΠΎ Π΄Π΅Π»Π°ΠΉ, ΡΠΎ ΠΌΠΎΡΠΎΡΠΈΠΊΠ»Ρ, Π° ΡΠ΅ΠΌ Π±ΠΎΠ»Π΅Π΅ Π°Π²ΡΠΎΠΌΠΎΠ±ΠΈΠ»ΠΈ ΡΡΠ΅Π±ΡΡΡ ΠΊ ΡΠ΅Π±Π΅ Π±ΠΎΠ»ΡΡΠ΅Π³ΠΎ Π²Π½ΠΈΠΌΠ°Π½ΠΈΡ ΠΈ ΡΠ²Π°ΠΆΠ΅Π½ΠΈΡ.
ΠΠ΅ΠΌΠ½ΠΎΠ³ΠΎ ΠΈΡΡΠΎΡΠΈΠΈ.
ΠΠ΅ΡΠ²ΡΠ΅ Π°Π²ΡΠΎΠΌΠΎΠ±ΠΈΠ»ΡΠ½ΡΠ΅ Π΄ΠΈΡΠΊΠΈ ΠΈΠ· ΠΊΠ°ΡΠ±ΠΎΠ½Π° ΠΏΠΎΡΠ²ΠΈΠ»ΠΈΡΡ Π΅ΡΠ΅ Π² 2008 Π³ΠΎΠ΄Ρ, ΠΈΡ Π²ΡΠΏΡΡΡΠΈΠ»Π° Π½Π΅ΠΌΠ΅ΡΠΊΠ°Ρ ΠΊΠΎΠΌΠΏΠ°Π½ΠΈΡ, ΡΠΏΠ΅ΡΠΈΠ°Π»ΠΈΠ·ΠΈΡΡΡΡΠ°ΡΡΡ Π½Π° ΠΊΠΎΠΌΠΏΠ»Π΅ΠΊΡΠ°ΡΠΈΠΈ Π³ΠΎΠ½ΠΎΡΠ½ΡΡ Π°Π²ΡΠΎ. ΠΠΎΠΌΠΏΠ»Π΅ΠΊΡ ΡΠ°ΠΊΠΈΡ Π΄ΠΈΡΠΊΠΎΠ² Π΄Π΅Π»Π°Π»ΡΡ ΠΏΠΎΠ΄ Π·Π°ΠΊΠ°Π· ΠΈ ΡΡΠΎΠΈΠ» ΠΏΠΎΡΡΠ΄ΠΊΠ° 15 ΡΡΡΡΡ Π·Π΅Π»Π΅Π½Π΅Π½ΡΠΊΠΈΡ ΠΏΡΠ΅Π·ΠΈΠ΄Π΅Π½ΡΠΎΠ². ΠΠ·-Π·Π° ΡΠ΅Π½Ρ, Π° Π΅ΡΠ΅ ΠΈΠ·-Π·Π° ΡΡΡΠ΄ΠΎΠ΅ΠΌΠΊΠΎΡΡΠΈ ΠΏΡΠΎΡΠ΅ΡΡΠ° ΠΈ Π½Π΅ Π²ΡΠ΅Π³Π΄Π° Π³Π°ΡΠ°Π½ΡΠΈΡΠΎΠ²Π°Π½Π½ΠΎΠ³ΠΎ ΠΊΠ°ΡΠ΅ΡΡΠ²Π΅Π½Π½ΠΎΠ³ΠΎ ΡΠ΅Π·ΡΠ»ΡΡΠ°ΡΠ°, ΡΡΠΈ ΠΊΠΎΠ»Π΅ΡΠ° Π² ΡΠ΅ΡΠΈΡ ΡΠ°ΠΊ ΠΈ Π½Π΅ ΠΏΠΎΡΠ»ΠΈ.
Π ΡΠΎΠΌΡ ΠΆΠ΅, ΠΊΠ°ΡΠ±ΠΎΠ½ΠΎΠ²ΡΠΌΠΈ Π² ΠΏΠΎΠ»Π½ΠΎΠΌ ΡΠΌΡΡΠ»Π΅ ΠΎΠ½ΠΈ Π½Π΅ ΡΠ²Π»ΡΠ»ΠΈΡΡ, ΡΡΠΎ Π±ΡΠ»ΠΎ ΡΠ±ΠΎΡΠ½ΠΎΠ΅ ΠΈΠ·Π΄Π΅Π»ΠΈΠ΅ ΠΈΠ· ΡΡΠ°Π»ΠΈ ΠΈ ΡΠ³Π»Π΅ΡΠΎΠ΄Π½ΠΎΠ³ΠΎ Π²Π»ΠΎΠΊΠ½Π°, ΡΠΎ Π΅ΡΡΡ, ΠΈΡΠΎΠ³ΠΎΠ²Π°Ρ ΡΠ°Π·Π½ΠΈΡΠ° Π² Π²Π΅ΡΠ΅ Π±ΡΠ»Π° Π½Π΅ ΡΡΠΎΠ»Ρ Π±ΠΎΠ»ΡΡΠΎΠΉ, ΡΡΠΎΠ±Ρ ΠΏΠ»Π°ΡΠΈΡΡ Π·Π° Π½Π΅Π΅ ΡΠ°ΠΊΠΈΠ΅ Π΄Π΅Π½ΡΠ³ΠΈ.
ΠΠ° ΡΠΎΡΠΎ ΡΠ»Π΅Π²Π° ΠΈΠ·ΠΎΠ±ΡΠ°ΠΆΠ΅Π½ Π΄ΠΈΡΠΊ Ρ ΠΊΠ°ΡΠ±ΠΎΠ½ΠΎΠ²ΡΠΌ ΠΎΠ±ΠΎΠ΄ΠΎΠΌ ΠΈ ΠΎΡΠ½ΠΎΠ²Π°Π½ΠΈΠ΅ΠΌ (ΡΡΡΠΏΠΈΡΠ½ΠΎΠΉ ΡΠ°ΡΡΡΡ), ΠΈΠ·Π³ΠΎΡΠΎΠ²Π»Π΅Π½Π½ΡΠΌ ΠΈΠ· ΠΊΠΎΠ²Π°Π½Π½ΠΎΠ³ΠΎ Π°Π»ΡΠΌΠΈΠ½ΠΈΠ΅Π²ΠΎΠ³ΠΎ ΡΠΏΠ»Π°Π²Π°.
ΠΡΠ΅ΠΌΡ ΡΠ»ΠΎ, ΠΊΠ°ΡΠ±ΠΎΠ½ Β«ΠΏΡΠΎΠ½ΠΈΠΊΠ°Π»Β» Π΅Π΄Π²Π° Π»ΠΈ Π½Π΅ Π²ΠΎ Π²ΡΠ΅ ΡΠ·Π»Ρ Π°Π²ΡΠΎΠΌΠΎΠ±ΠΈΠ»Π΅ΠΉ, Π΄Π°ΠΆΠ΅ Π½Π°ΡΠ°Π»ΠΈ ΡΡΡΠΈΡΡ, ΡΡΠΎ ΠΏΠΎΡΠ° ΠΎΠΆΠΈΠ΄Π°ΡΡ ΠΏΠΎΡΠ²Π»Π΅Π½ΠΈΡ ΠΊΠ°ΡΠ±ΠΎΠ½ΠΎΠ²ΠΎΠ³ΠΎ Π΄Π²ΠΈΠ³Π°ΡΠ΅Π»Ρ, ΠΎΡΠΎΠ±Π΅Π½Π½ΠΎ ΠΏΠΎΡΠ»Π΅ ΡΠΎΠ³ΠΎ, ΠΊΠ°ΠΊ Π½Π° Π΄Π²ΠΈΠΆΠΊΠΈ ΡΡΠ°Π»ΠΈ ΡΡΠ°Π²ΠΈΡΡ ΠΊΡΡΡΠΊΠΈ ΠΈΠ·Π³ΠΎΡΠΎΠ²Π»Π΅Π½Π½ΡΠ΅ ΠΈΠ· Π½Π΅Π³ΠΎ, Π½ΠΎ Π΄ΠΈΡΠΊΠΈ ΠΈΠ· ΡΡΠΎΠ³ΠΎ ΠΌΠ°ΡΠ΅ΡΠΈΠ°Π»Π° Π²ΡΠ΅ Π΅ΡΠ΅ ΠΎΡΡΠ°Π²Π°Π»ΠΈΡΡ ΠΌΠ΅ΡΡΠΎΠΉ.
Π Π²ΠΎΡ Π² 2012 Π³ΠΎΠ΄Ρ, Π°Π²ΡΡΡΠ°Π»ΠΈΠΉΡΡ Β«Carbon RevolutionΒ» ΠΏΡΠ΅Π΄ΡΡΠ°Π²ΠΈΠ»ΠΈ ΠΏΠ΅ΡΠ²ΡΠ΅ ΠΌΠΎΠ½ΠΎΠ»ΠΈΡΠ½ΡΠ΅ Π΄ΠΈΡΠΊΠΈ, ΠΏΠΎΠ»ΡΡΠΈΠ²ΡΠΈΠ΅ Π½Π°Π·Π²Π°Π½ΠΈΠ΅ CR9. ΠΠ° ΠΏΡΠ΅Π·Π΅Π½ΡΠ°ΡΠΈΠΈ Π±ΡΠ»ΠΎ ΠΎΠ±Π΅ΡΠ°Π½ΠΎ, ΡΡΠΎ ΡΡΠΎ Π±ΡΠ΄ΡΡ Π½Π΅ ΠΏΡΠΎΡΡΠΎ ΠΏΠ΅ΡΠ²ΡΠ΅, ΠΏΠΎΠ»Π½ΠΎΡΡΡΡ ΠΊΠ°ΡΠ±ΠΎΠ½ΠΎΠ²ΡΠ΅ Π΄ΠΈΡΠΊΠΈ, Π½ΠΎ ΠΈ ΠΏΠ΅ΡΠ²Π°Ρ ΡΠ΅ΡΠΈΠΉΠ½Π°Ρ ΠΌΠΎΠ΄Π΅Π»Ρ. Π‘ΠΊΠ°Π·Π°Π½ΠΎ β ΡΠ΄Π΅Π»Π°Π½ΠΎ, ΠΏΡΠ°Π²Π΄Π°, ΠΏΠΎΠΊΠ° Π½Π΅ Π΄ΠΎ ΠΊΠΎΠ½ΡΠ°. Π 2013-ΠΎΠΌ ΠΎΠ½ΠΈ Π½Π°ΡΠ°Π»ΠΈ Π²ΡΠΏΡΡΠΊΠ°ΡΡΡΡ ΡΠΎΠ»ΡΠΊΠΎ Π² Π΄Π²ΡΡ Π²Π°ΡΠΈΠ°ΡΠΈΡΡ β 19Ρ 8.5 ΠΈ 19Ρ 12, Π²Π΅Ρ ΡΠΎΠΎΡΠ²Π΅ΡΡΡΠ²Π΅Π½Π½ΠΎ 7 ΠΈ 7.9 ΠΊΠ³. ΠΠΎ Π²Π½Π΅ΡΠ½Π΅ΠΌΡ ΠΆΠ΅ ΠΌΠΎΠ΄Π΅Π»ΡΠ½ΠΎΠΌΡ ΡΡΠ΄Ρ ΠΌΠΈΡΡ Π±ΡΠ»ΠΈ ΠΏΡΠ΅Π΄ΡΡΠ°Π²Π»Π΅Π½Ρ ΡΠΎΠ»ΡΠΊΠΎ Π΄Π΅Π²ΡΡΠΈΠ»ΡΡΠ΅Π²ΡΠ΅ ΠΊΠ»Π°ΡΡΠΈΡΠ΅ΡΠΊΠΈΠ΅ ΠΊΠΎΠ»Π΅ΡΠ°, ΡΠΎ ΡΡΡΠΎΠ³ΠΈΠΌ Π²Π½Π΅ΡΠ½ΠΈΠΌ Π²ΠΈΠ΄ΠΎΠΌ ΠΈ ΠΎΠ±ΡΠ·Π°ΡΠ΅Π»ΡΠ½ΡΠΌ Π»ΠΎΠ³ΠΎΡΠΈΠΏΠΎΠΌ ΠΊΠΎΠΌΠΏΠ°Π½ΠΈΠΈ-ΠΏΡΠΎΠΈΠ·Π²ΠΎΠ΄ΠΈΡΠ΅Π»Ρ Π½Π° ΡΡΡΠΏΠΈΡΠ΅.
ΠΠ° Π΄Π°Π½Π½ΡΠΉ ΠΌΠΎΠΌΠ΅Π½Ρ ΠΈΡ Π²ΡΠ±ΠΎΡ ΡΡΠ°Π» ΡΠΈΡΠ΅, Π½Π°ΠΏΡΠΈΠΌΠ΅Ρ ΠΈΠ·ΠΎΠ±ΡΠ°ΠΆΠ΅Π½Π½ΡΠΉ Π½Π° ΡΠΎΡΠΎ ΡΠ»Π΅Π²Π° ΠΌΠΎΠ½ΠΎΠ»ΠΈΡ ΡΠΈΡΠΌΡ Carbon Revolution.
ΠΠΎΡΡΠΎΠΈΠ½ΡΡΠ²Π°.
ΠΠ°ΠΊ Π²ΠΈΠ΄ΠΈΠΌ, Π½Π°Π»ΠΈΡΠΎ Π³Π»Π°Π²Π½ΠΎΠ΅ Π΄ΠΎΡΡΠΎΠΈΠ½ΡΡΠ²ΠΎ ΠΊΠ°ΡΠ±ΠΎΠ½ΠΎΠ²ΡΡ ΠΊΠΎΠ»Π΅Ρ β Π΅ΡΠ»ΠΈ ΡΡΠ°Π²Π½ΠΈΠ²Π°ΡΡ ΠΈΡ Ρ Π»ΠΈΡΡΠΌ, ΠΈ Π΄Π°ΠΆΠ΅ ΠΊΠΎΠ²Π°Π½ΡΠΌ Π°Π»ΡΠΌΠΈΠ½ΠΈΠ΅ΠΌ, ΡΠΎ ΠΏΠΎΠ»ΡΡΠ°Π΅ΡΡΡ, ΡΡΠΎ ΡΠ³Π»Π΅ΠΏΠ»Π°ΡΡΠΈΠΊΠΎΠ²ΡΠ΅ ΠΈΠ·Π΄Π΅Π»ΠΈΡ Π»Π΅Π³ΡΠ΅ Π½Π° 40-50 %. Π’ΠΎ Π΅ΡΡΡ, Π²ΠΏΠΎΠ»Π½Π΅ ΠΎΡΠ΅Π²ΠΈΠ΄Π½ΠΎ, ΡΡΠΎ ΠΎΠ½ΠΈ ΡΠ²Π»ΡΡΡΡΡ ΡΠ°ΠΌΡΠΌΠΈ Π»Π΅Π³ΠΊΠΈΠΌΠΈ ΠΈΠ· ΡΡΡΠ΅ΡΡΠ²ΡΡΡΠΈΡ .
ΠΡΠ»ΠΈ ΡΠ°ΡΡΠΌΠ°ΡΡΠΈΠ²Π°ΡΡ ΡΡΠ΅Π· ΠΊΠ°ΡΠ±ΠΎΠ½Π° ΠΏΠΎΠ΄ ΡΠΈΠ»ΡΠ½ΡΠΌ ΡΠ²Π΅Π»ΠΈΡΠ΅Π½ΠΈΠ΅ΠΌ, ΡΠΎ ΠΌΠΎΠΆΠ½ΠΎ ΡΠ°ΡΡΠΌΠΎΡΡΠ΅ΡΡ ΠΌΠ½ΠΎΠΆΠ΅ΡΡΠ²ΠΎ ΠΏΠ΅ΡΠ΅ΠΏΠ»Π΅ΡΠ΅Π½Π½ΡΡ Π²ΠΎΠ»ΠΎΠΊΠΎΠ½, ΡΡΠ° ΠΎΡΠΎΠ±Π΅Π½Π½ΠΎΡΡΡ ΡΠ²Π΅Π»ΠΈΡΠΈΠ²Π°Π΅Ρ ΡΠΈΠ·ΠΈΡΠ΅ΡΠΊΡΡ ΠΏΡΠΎΡΠ½ΠΎΡΡΡ Π½Π° ΡΠΆΠ°ΡΠΈΠ΅ ΠΈ ΡΠ°ΡΡΡΠΆΠ΅Π½ΠΈΠ΅. Π ΠΈΡΠΎΠ³Π΅, ΠΏΠΎ ΠΊΠΎΠ½ΡΡΡΡΠΊΡΠΈΠ²Π½ΠΎΠΉ ΠΏΡΠΎΡΠ½ΠΎΡΡΠΈ Π΄Π°Π½Π½ΡΠΉ ΠΌΠ°ΡΠ΅ΡΠΈΠ°Π» Π½Π΅ ΡΡΡΡΠΏΠΈΡ Π½ΠΈ ΠΎΠ΄Π½ΠΎΠΌΡ ΠΈΠ· ΠΈΡΠΏΠΎΠ»ΡΠ·ΡΠ΅ΠΌΡΡ Π΄Π»Ρ Π°Π²ΡΠΎΠΌΠΎΠ±ΠΈΠ»ΡΠ½ΡΡ ΠΊΠΎΠ»Π΅Ρ ΠΌΠ°ΡΠ΅ΡΠΈΠ°Π»ΠΎΠ².
Π£ΡΠΈΡΡΠ²Π°Ρ, ΡΡΠΎ Π³Π»Π°Π²Π½ΠΎΠ΅ ΠΏΡΠ΅Π΄Π½Π°Π·Π½Π°ΡΠ΅Π½ΠΈΠ΅ ΠΊΠ°ΡΠ±ΠΎΠ½ΠΎΠ²ΡΡ Π΄ΠΈΡΠΊΠΎΠ², ΡΡΠΎ ΠΈΡΠΏΠΎΠ»ΡΠ·ΠΎΠ²Π°Π½ΠΈΠ΅ ΠΈΡ Π² ΠΊΠ°ΡΠ΅ΡΡΠ²Π΅ Π΄Π΅ΡΠ°Π»ΠΈ Π΄Π»Ρ ΡΠΊΠΎΡΠΎΡΡΠ½ΡΡ Π°Π²ΡΠΎ, ΡΠΎ ΡΠΎΠ²ΡΠ΅ΠΌ Π½Π΅ Π»ΠΈΡΠ½ΠΈΠΌ Π±ΡΠ΄Π΅Ρ ΡΠ°ΠΊΠΎΠΉ ΠΏΠΎΠΊΠ°Π·Π°ΡΠ΅Π»Ρ, ΠΊΠ°ΠΊ Π²ΡΡΠΎΠΊΠ°Ρ ΡΠ΅ΠΌΠΏΠ΅ΡΠ°ΡΡΡΠ½Π°Ρ ΡΡΠΎΠΉΠΊΠΎΡΡΡ. Π£ Π΄Π°Π½Π½ΡΡ ΠΈΠ·Π΄Π΅Π»ΠΈΠΉ ΠΎΠ½Π° Π΄ΠΎΡΡΠΈΠ³Π°Π΅Ρ 1600 Β°C, ΡΡΠΎ Π² ΡΠΎΡΠ΅ΡΠ°Π½ΠΈΠΈ Ρ Π²ΡΡΠΎΠΊΠΎΠΉ ΡΠ½Π΅ΡΠ³ΠΎΠΏΠΎΠ³Π»ΠΎΡΠ°Π΅ΠΌΠΎΡΡΡΡ ΠΎΠ±Π΅ΡΠΏΠ΅ΡΠΈΠ²Π°Π΅Ρ Π΄ΠΎΠ»Π³ΠΈΠΉ ΡΡΠΎΠΊ ΡΠ»ΡΠΆΠ±Ρ ΡΠ°ΠΌΠΈΡ Π΄ΠΈΡΠΊΠΎΠ² ΠΈ ΡΠ»Π΅ΠΌΠ΅Π½ΡΠΎΠ² ΡΠΎΡΠΌΠΎΠ·Π½ΠΎΠΉ ΡΠΈΡΡΠ΅ΠΌΡ.
Π ΠΊΠΎΠ½ΡΠ΅ ΠΊΠΎΠ½ΡΠΎΠ², Π²Π½Π΅ΡΠ½Π΅ ΠΎΠ½ΠΈ ΡΠΌΠΎΡΡΡΡΡΡ ΠΏΡΠΎΡΡΠΎ ΠΎΡΠ»ΠΈΡΠ½ΠΎ, ΠΈ ΡΡΠΎ Π΄Π΅Π»Π°Π΅Ρ ΠΈΡ ΡΠ΄Π°ΡΠ½ΠΎΠΉ Π½Π°Ρ ΠΎΠ΄ΠΊΠΎΠΉ Π½Π΅ ΡΠΎΠ»ΡΠΊΠΎ ΡΠΎ ΡΡΠΎΡΠΎΠ½Ρ ΡΡΠ½ΠΈΠ½Π³Π° ΡΠ΅Ρ Π½ΠΈΡΠ΅ΡΠΊΠΎΠ³ΠΎ, Π½ΠΎ ΠΈ Π²Π½Π΅ΡΠ½Π΅Π³ΠΎ. Π§ΡΠΎ ΠΊΠ°ΡΠ°Π΅ΡΡΡ ΠΊΠΎΡΡΠΎΠ·ΠΈΠΉΠ½ΠΎΠΉ ΡΡΠΎΠΉΠΊΠΎΡΡΠΈ, ΡΠΎ Π΄ΠΎΡΡΠ°ΡΠΎΡΠ½ΠΎ Π²ΡΠΏΠΎΠΌΠ½ΠΈΡΡ, ΡΡΠΎ Π² ΠΏΠΎΡΠ»Π΅Π΄Π½Π΅Π΅ Π²ΡΠ΅ΠΌΡ ΠΏΠ»Π΅Π½ΠΊΠΈ ΠΈΠΌΠ΅Π½Π½ΠΎ ΠΈΠ· ΡΠ³Π»Π΅ΠΏΠ»Π°ΡΡΠΈΠΊΠΎΠ²ΡΡ ΠΌΠ°ΡΠ΅ΡΠΈΠ°Π»ΠΎΠ² ΠΈΡΠΏΠΎΠ»ΡΠ·ΡΡΡΡΡ Π² ΠΊΠ°ΡΠ΅ΡΡΠ²Π΅ Π·Π°ΡΠΈΡΡ Π»Π°ΠΊΠΎΠΊΡΠ°ΡΠΎΡΠ½ΠΎΠ³ΠΎ ΠΏΠΎΠΊΡΡΡΠΈΡ ΠΊΡΠ·ΠΎΠ²Π° Π°Π²ΡΠΎ ΠΈ ΡΠ΅ΠΌΡ ΠΌΠΎΠΆΠ½ΠΎ Π·Π°ΠΊΡΡΠ²Π°ΡΡ.
ΠΠ΅Π΄ΠΎΡΡΠ°ΡΠΊΠΈ.
Π ΡΠ΅ΠΏΠ΅ΡΡ ΡΡΠ°Π²Π½ΠΈΠΌ ΡΡΡ Π±ΠΎΡΠΈΡΡ ΠΌΠ΅Π΄Π° Ρ Π½Π΅ΠΌΠ°Π»Π΅Π½ΡΠΊΠΎΠΉ Π΅ΠΌΠΊΠΎΡΡΡΡ Π΄Π΅Π³ΡΡ. Π’ΠΎ Π΅ΡΡΡ, Π²ΡΠΏΠΎΠΌΠ½ΠΈΠΌ, ΡΠ΅ΠΌ ΠΊΠ°ΡΠ±ΠΎΠ½ΠΎΠ²ΡΠ΅ Π΄ΠΈΡΠΊΠΈ ΠΌΠΎΠ³ΡΡ ΡΠ°ΡΡΡΡΠΎΠΈΡΡ ΡΠ²ΠΎΠ΅Π³ΠΎ Π²Π»Π°Π΄Π΅Π»ΡΡΠ°, ΠΈΡ ΡΡΡΠ΅ΡΡΠ²Π΅Π½Π½ΡΠ΅ Π½Π΅Π΄ΠΎΡΡΠ°ΡΠΊΠΈ.
ΠΡΠΈ Π²ΡΡΠΎΠΊΠΎΠΉ ΠΎΠ±ΡΠ΅ΠΉ ΠΏΡΠΎΡΠ½ΠΎΡΡΠΈ ΠΊΠ°ΡΠ±ΠΎΠ½ Β«Π½Π΅ Π»ΡΠ±ΠΈΡΒ» ΡΠΎΡΠ΅ΡΠ½ΡΡ ΡΠ΄Π°ΡΠΎΠ², ΠΈ ΠΏΡΠΈ ΠΎΡΠ΅Π½Ρ ΡΠΈΠ»ΡΠ½ΠΎΠΌ ΡΠ΄Π°ΡΠ΅ ΠΌΠΎΠΆΠ΅Ρ ΡΠ°ΡΠΊΠΎΠ»ΠΎΡΡΡΡ Π½Π° ΠΌΠ½ΠΎΠΆΠ΅ΡΡΠ²ΠΎ ΠΎΡΠΊΠΎΠ»ΠΊΠΎΠ², ΡΡΠΎ Π΄Π΅Π»Π°Π΅Ρ Π½Π΅Π²ΠΎΠ·ΠΌΠΎΠΆΠ½ΡΠΌ Π΅Π³ΠΎ Π²ΠΎΡΡΡΠ°Π½ΠΎΠ²Π»Π΅Π½ΠΈΠ΅. ΠΡΠΈ ΡΡΠΎΠΌ ΠΈΠ·Π³ΠΎΡΠΎΠ²Π»Π΅Π½ΠΈΠ΅ Π΄ΠΈΡΠΊΠ° Π½Π° Π·Π°ΠΊΠ°Π· β ΡΡΠΎ ΠΏΡΠΎΡΠ΅ΡΡ Π΄ΠΎΡΡΠ°ΡΠΎΡΠ½ΠΎ Π΄Π»ΠΈΡΠ΅Π»ΡΠ½ΡΠΉ.
Π₯ΠΎΡΡ ΠΊΠΎΡΡΠΎΠ·ΠΈΠΉΠ½Π°Ρ ΡΡΠΎΠΉΠΊΠΎΡΡΡ ΡΠ°ΠΌΠΎΠ³ΠΎ ΠΌΠ°ΡΠ΅ΡΠΈΠ°Π»Π° Π½Π° ΠΎΡΠ΅Π½Ρ Π²ΡΡΠΎΠΊΠΎΠΌ ΡΡΠΎΠ²Π½Π΅, Π½ΠΎ Π΅Π³ΠΎ ΠΏΡΡΠΌΠΎΠΉ ΠΊΠΎΠ½ΡΠ°ΠΊΡ Ρ ΠΌΠ΅ΡΠ°Π»Π»ΠΈΡΠ΅ΡΠΊΠΈΠΌΠΈ ΡΠ»Π΅ΠΌΠ΅Π½ΡΠ°ΠΌΠΈ Ρ ΠΎΠ΄ΠΎΠ²ΠΎΠΉ Π² ΡΠΎΡΠ΅ΡΠ°Π½ΠΈΠΈ Ρ ΡΠΎΠ»Π΅Π½ΠΎΠΉ ΡΡΠ΅Π΄ΠΎΠΉ ΠΏΡΠΈΠ²ΠΎΠ΄ΠΈΡ ΠΊ Π±ΡΡΡΡΠΎΠΌΡ ΡΠ°Π·ΡΡΡΠ΅Π½ΠΈΡ ΠΌΠ΅ΡΠ°Π»Π»Π°. Π§ΡΠΎΠ±Ρ ΠΈΡΠΊΠ»ΡΡΠΈΡΡ ΠΏΠΎΠ΄ΠΎΠ±Π½ΡΡ ΠΏΡΠΎΠ±Π»Π΅ΠΌΡ ΠΏΠΎΡΡΠ΅Π±ΡΡΡΡΡ Π΄ΠΎΠΏΠΎΠ»Π½ΠΈΡΠ΅Π»ΡΠ½ΡΠ΅ Π²ΡΡΠ°Π²ΠΊΠΈ ΠΈΠ· ΡΡΠ΅ΠΊΠ»ΠΎΠΏΠ»Π°ΡΡΠΈΠΊΠ°, ΠΌΠ΅ΠΆΠ΄Ρ ΠΊΠ°ΡΠ±ΠΎΠ½ΠΎΠΌ ΠΈ ΠΌΠ΅ΡΠ°Π»Π»ΠΎΠΌ.
Π’Π°ΠΊΠΆΠ΅ Π² ΠΎΠ±ΡΠ·Π°ΡΠ΅Π»ΡΠ½ΠΎΠΌ ΠΏΠΎΡΡΠ΄ΠΊΠ΅ ΡΡΠ΅Π±ΡΠ΅ΡΡΡ Π΄ΠΎΠΏΠΎΠ»Π½ΠΈΡΠ΅Π»ΡΠ½Π°Ρ Π·Π°ΡΠΈΡΠ° ΠΎΡ ΡΠ»ΡΡΡΠ°ΡΠΈΠΎΠ»Π΅ΡΠΎΠ²ΡΡ Π»ΡΡΠ΅ΠΉ β ΠΊΠ°ΡΠ±ΠΎΠ½ Π±ΡΡΡΡΠΎ Π²ΡΠ³ΠΎΡΠ°Π΅Ρ Π½Π° ΡΠΎΠ»Π½ΡΠ΅, ΡΠ΅ΡΡΡ Π²ΡΡΠΊΡΡ ΠΏΡΠΈΠ²Π»Π΅ΠΊΠ°ΡΠ΅Π»ΡΠ½ΠΎΡΡΡ, Π° Π²Π΅Π΄Ρ ΠΎΠ½ Π½Π°ΠΈΠ±ΠΎΠ»Π΅Π΅ Π²Π½Π΅ΡΠ½Π΅ ΠΏΡΠΈΠ²Π»Π΅ΠΊΠ°ΡΠ΅Π»Π΅Π½ ΠΈΠΌΠ΅Π½Π½ΠΎ Π½Π΅ΠΎΠΊΡΠ°ΡΠ΅Π½Π½ΠΎΠΌ Π²ΠΈΠ΄Π΅.
ΠΡ ΠΈ, Π½Π°ΠΊΠΎΠ½Π΅Ρ, ΡΠ°ΠΌΠ°Ρ Π±ΠΎΠ»ΡΡΠ°Ρ ΠΏΡΠΎΠ±Π»Π΅ΠΌΠ° β ΡΡΠΎΠ±Ρ Π³ΠΎΡΠΎΠ²ΡΠΉ ΠΊΠ°ΡΠ±ΠΎΠ½ΠΎΠ²ΡΠΉ Π΄ΠΈΡΠΊ ΠΈΠΌΠ΅Π» Π²ΡΠ΅ ΡΠ΅ Π²ΡΡΠΎΠΊΠΈΠ΅ ΠΊΠ°ΡΠ΅ΡΡΠ²Π΅Π½Π½ΡΠ΅ ΠΏΠΎΠΊΠ°Π·Π°ΡΠ΅Π»ΠΈ, Π΅Π³ΠΎ ΠΈΠ·Π³ΠΎΡΠΎΠ²Π»Π΅Π½ΠΈΠ΅ Π΄ΠΎΠ»ΠΆΠ½ΠΎ Π²Π΅ΡΡΠΈΡΡ Π² ΡΡΡΠΎΠ³ΠΎΠΌ ΡΠΎΠΎΡΠ²Π΅ΡΡΡΠ²ΠΈΠΈ Ρ ΠΏΡΠ΅Π΄ΡΡΠΌΠΎΡΡΠ΅Π½Π½ΡΠΌΠΈ ΡΠ΅Ρ Π½ΠΎΠ»ΠΎΠ³ΠΈΡΠΌΠΈ. Π ΡΡΠΎ ΠΎΠ·Π½Π°ΡΠ°Π΅Ρ Π²ΡΡΠΎΠΊΡΡ ΡΠ΅Π½Ρ, Π½Π°ΡΡΠΎΠ»ΡΠΊΠΎ Π²ΡΡΠΎΠΊΡΡ, ΡΡΠΎ ΡΠΈΡΠ°Π½ΠΎΠ²ΡΠ΅ ΠΊΠΎΠ»Π΅ΡΠ° Β«Π½Π΅ΡΠ²Π½ΠΎ ΠΊΡΡΡΡ Π² ΡΡΠΎΡΠΎΠ½Π΅Β». ΠΠΎΠΌΠΏΠ»Π΅ΠΊΡ ΠΊΠ°ΡΠ΅ΡΡΠ²Π΅Π½Π½ΡΡ ΠΊΠ°ΡΠ±ΠΎΠ½ΠΎΠ²ΡΡ ΠΊΠΎΠ»Π΅Ρ Β«ΠΏΠΎΡΡΠ½Π΅ΡΒ» Π½Π° ΡΠ΅Π»ΡΠΉ Π°Π²ΡΠΎΠΌΠΎΠ±ΠΈΠ»Ρ, Π½Π΅ Β«Π»Π°ΠΌΠ±ΠΎΡΠ³ΠΈΠ½ΠΈΒ», ΠΊΠΎΠ½Π΅ΡΠ½ΠΎ, Π½ΠΎ Π½Π° ΠΎΡΠ΅ΡΠ΅ΡΡΠ²Π΅Π½Π½ΡΠΉ Π²ΠΏΠΎΠ»Π½Π΅ Ρ Π²Π°ΡΠΈΡ, Π±ΡΡΡ ΠΌΠΎΠΆΠ΅Ρ, Π΄Π°ΠΆΠ΅ Π½Π΅ ΠΎΠ΄ΠΈΠ½β¦
autoforeach.ru
ΠΠ°ΡΠ±ΠΎΠ½ΠΎΠ²ΡΠ΅ Π΄ΠΈΡΠΊΠΈ Π½Π° Π°Π²ΡΠΎ: ΠΏΡΠ΅ΠΈΠΌΡΡΠ΅ΡΡΠ²Π° ΠΈ Π½Π΅Π΄ΠΎΡΡΠ°ΡΠΊΠΈ
Π Π±ΠΎΠ»ΡΡΠΈΠ½ΡΡΠ²Π΅ ΡΠ»ΡΡΠ°Π΅Π² ΡΠΎΡΡΠ°Π²Π½ΡΠ΅ ΡΠ°ΡΡΠΈ Π°Π²ΡΠΎΠΌΠΎΠ±ΠΈΠ»Ρ ΠΈΠ·Π³ΠΎΡΠ°Π²Π»ΠΈΠ²Π°ΡΡΡΡ ΠΈΠ· ΡΡΠ°Π»ΠΈ ΠΈΠ»ΠΈ Π΄ΡΡΠ³ΠΈΡ ΠΌΠ΅ΡΠ°Π»Π»ΠΎΠ². Π ΡΡΠΎ Π»Π΅Π³ΠΊΠΎ ΠΎΠ±ΡΡΡΠ½ΠΈΠΌΠΎ: ΡΡΠΈ ΠΌΠ°ΡΠ΅ΡΠΈΠ°Π»Ρ Π²ΡΡΠΎΠΊΠΎΠΏΡΠΎΡΠ½ΡΠ΅, Π½Π΅ ΡΡΠ΅Π±ΡΡΡ ΡΠ»ΠΎΠΆΠ½ΠΎΠΉ ΠΎΠ±ΡΠ°Π±ΠΎΡΠΊΠΈ, Π° Π³Π»Π°Π²Π½ΠΎΠ΅ Π±Π΅Π· ΠΏΡΠΎΠ±Π»Π΅ΠΌ ΠΏΠΎΠ΄Π΄Π°ΡΡΡΡ ΡΠ΅ΠΌΠΎΠ½ΡΡ.
ΠΠΎ Π½Π΅ΡΠΌΠΎΡΡΡ Π½Π° ΡΡΠΈ Π΄ΠΎΡΡΠΎΠΈΠ½ΡΡΠ²Π°, Ρ ΠΌΠ΅ΡΠ°Π»Π»ΠΈΡΠ΅ΡΠΊΠΈΡ ΠΈ ΠΊΠΎΠ²Π°Π½ΡΡ Π΄ΠΈΡΠΊΠΎΠ² Π½Π° Π°Π²ΡΠΎ Π΅ΡΡΡ ΠΈ ΡΠ²ΠΎΠΈ ΠΌΠΈΠ½ΡΡΡ. Π ΠΏΡΠΈΠΌΠ΅ΡΡ, ΠΏΠΎΠΊΠ»ΠΎΠ½Π½ΠΈΠΊΠΈ ΡΠΏΠΎΡΡΠΊΠ°ΡΠΎΠ², ΠΊΠΎΡΠΎΡΡΠ΅ ΡΡΡΠ΅ΠΌΡΡΡΡ ΡΠ»ΡΡΡΠΈΡΡ ΠΏΠΎΠΊΠ°Π·Π°ΡΠ΅Π»ΠΈ ΡΠΊΠΎΡΠΎΡΡΠΈ ΠΈ ΡΠΏΡΠ°Π²Π»ΡΠ΅ΠΌΠΎΡΡΠΈ ΡΠ²ΠΎΠΈΡ Π°Π²ΡΠΎΠΌΠΎΠ±ΠΈΠ»Π΅ΠΉ, ΡΡΡΠ°Π΄Π°ΡΡ ΠΈΠ·-Π·Π° Π±ΠΎΠ»ΡΡΠΎΠ³ΠΎ Π²Π΅ΡΠ° ΠΌΠ΅ΡΠ°Π»Π»ΠΈΡΠ΅ΡΠΊΠΈΡ Π΄Π΅ΡΠ°Π»Π΅ΠΉ. ΠΠΎΠ½Π΅ΡΠ½ΠΎ, ΠΌΠΎΠΆΠ½ΠΎ ΠΈΠ·Π³ΠΎΡΠ°Π²Π»ΠΈΠ²Π°ΡΡ ΠΈΡ ΠΈΠ· ΡΠΎΠ²ΡΠ΅ΠΌΠ΅Π½Π½ΡΡ Π»Π΅Π³ΠΊΠΈΡ ΠΌΠ°ΡΠ΅ΡΠΈΠ°Π»ΠΎΠ², Π½ΠΎ, ΠΊ ΡΠΎΠΆΠ°Π»Π΅Π½ΠΈΡ, ΠΎΠ½ΠΈ ΠΏΠΎΠ»ΡΡΠ°ΡΡΡ Π½Π΅ ΡΠ°ΠΊΠΈΠΌΠΈ ΠΏΡΠΎΡΠ½ΡΠΌΠΈ, ΠΊΠ°ΠΊ Π½Π΅ΠΎΠ±Ρ ΠΎΠ΄ΠΈΠΌΠΎ. Π Π΅ΡΠ΅Π½ΠΈΠ΅ Π΄Π°Π½Π½ΠΎΠΉ ΠΏΡΠΎΠ±Π»Π΅ΠΌΡ Π΅ΡΡΡ β ΠΈΠ·Π³ΠΎΡΠΎΠ²Π»Π΅Π½ΠΈΠ΅ Π°Π²ΡΠΎΠΌΠΎΠ±ΠΈΠ»ΡΠ½ΡΡ Π΄ΠΈΡΠΊΠΎΠ² ΠΈΠ· ΠΊΠ°ΡΠ±ΠΎΠ½Π° (ΡΠ³Π»Π΅ΠΏΠ»Π°ΡΡΠΈΠΊΠ°). ΠΡΠΎΡ ΠΌΠ°ΡΠ΅ΡΠΈΠ°Π» Π½Π΅ ΠΈΠ΄Π΅Π°Π»Π΅Π½, Π½ΠΎ Π΅Π³ΠΎ Π»Π΅Π³ΠΊΠΎΡΡΡ ΠΈ ΠΏΡΠΎΡΠ½ΠΎΡΡΡ ΠΊΠΎΠΌΠΏΠ΅Π½ΡΠΈΡΡΠ΅Ρ Π²ΡΠ΅ Π½Π΅Π΄ΠΎΡΡΠ°ΡΠΊΠΈ.
ΠΡΡΠΎΡΠΈΡ ΠΏΠΎΡΠ²Π»Π΅Π½ΠΈΡ ΠΊΠ°ΡΠ±ΠΎΠ½ΠΎΠ²ΡΡ Π΄ΠΈΡΠΊΠΎΠ²
Π‘Π°ΠΌΡΠ΅ ΠΏΠ΅ΡΠ²ΡΠ΅ ΠΊΠ°ΡΠ±ΠΎΠ½ΠΎΠ²ΡΠ΅ Π΄ΠΈΡΠΊΠΈ Π½Π° Π°Π²ΡΠΎ ΠΏΠΎΡΠ²ΠΈΠ»ΠΈΡΡ Π½Π° ΡΠ²Π΅Ρ ΡΠΎΠ²ΡΠ΅ΠΌ Π½Π΅Π΄Π°Π²Π½ΠΎ: Π² 2008 Π³ΠΎΠ΄Ρ. ΠΠ½ΠΈ Π±ΡΠ»ΠΈ ΠΈΠ·Π³ΠΎΡΠΎΠ²Π»Π΅Π½Ρ Π½Π΅ΠΌΠ΅ΡΠΊΠΎΠΉ ΠΊΠΎΠΌΠΏΠ°Π½ΠΈΠ΅ΠΉ, ΠΊΠΎΡΠΎΡΠ°Ρ ΡΠΏΠ΅ΡΠΈΠ°Π»ΠΈΠ·ΠΈΡΠΎΠ²Π°Π»Π°ΡΡ Π½Π° ΠΏΡΠΎΠΈΠ·Π²ΠΎΠ΄ΡΡΠ²Π΅ Π΄Π΅ΡΠ°Π»Π΅ΠΉ Π΄Π»Ρ Π³ΠΎΠ½ΠΎΡΠ½ΡΡ Π°Π²ΡΠΎΠΌΠΎΠ±ΠΈΠ»Π΅ΠΉ. Π‘ΡΠΎΠΈΠΌΠΎΡΡΡ ΡΠ°ΠΊΠΎΠ³ΠΎ ΠΊΠΎΠΌΠΏΠ»Π΅ΠΊΡΠ° ΡΠΎΡΡΠ°Π²Π»ΡΠ»Π° ΠΏΡΠΈΠΌΠ΅ΡΠ½ΠΎ 15 ΡΡΡΡΡ Π΄ΠΎΠ»Π»Π°ΡΠΎΠ². ΠΠΎ ΠΏΡΠΈΡΠΈΠ½Π΅ Π΄ΠΎΡΠΎΠ³ΠΎΠ²ΠΈΠ·Π½Ρ, ΡΠ»ΠΎΠΆΠ½ΠΎΡΡΠΈ ΠΏΡΠΎΡΠ΅ΡΡΠ° ΠΏΡΠΎΠΈΠ·Π²ΠΎΠ΄ΡΡΠ²Π°, Π° ΡΠ°ΠΊΠΆΠ΅ Π·Π°ΡΠ°ΡΡΡΡ ΠΏΠ»ΠΎΡ ΠΎΠ³ΠΎ ΠΊΠ°ΡΠ΅ΡΡΠ²Π° ΠΈΡΠΎΠ³ΠΎΠ²ΠΎΠΉ ΠΏΡΠΎΠ΄ΡΠΊΡΠΈΠΈ, ΡΡΠ° ΡΠ΅ΡΠΈΡ Π½Π΅ ΠΏΠΎΠ»ΡΡΠΈΠ»Π° Π΄ΠΎΠ»ΠΆΠ½ΠΎΠΉ ΠΏΠΎΠΏΡΠ»ΡΡΠ½ΠΎΡΡΠΈ.
ΠΠ΄Π½Π°ΠΊΠΎ ΡΠΎΠ·Π΄Π°Π½Π½ΡΠ΅ ΡΡΠΎΠΉ ΠΊΠΎΠΌΠΏΠ°Π½ΠΈΠ΅ΠΉ Π΄ΠΈΡΠΊΠΈ Π½Π΅Π»ΡΠ·Ρ Π±ΡΠ»ΠΎ Π½Π°Π·Π²Π°ΡΡ ΠΏΠΎΠ»Π½ΠΎΡΠ΅Π½Π½ΠΎ ΠΊΠ°ΡΠ±ΠΎΠ½ΠΎΠ²ΡΠΌΠΈ, ΠΏΠΎΡΠΎΠΌΡ ΡΡΠΎ ΠΎΠ½ΠΈ ΠΏΡΠ΅Π΄ΡΡΠ°Π²Π»ΡΠ»ΠΈ ΡΠΎΠ±ΠΎΠΉ ΡΠ±ΠΎΡΠ½ΠΎΠ΅ ΠΈΠ·Π΄Π΅Π»ΠΈΠ΅ ΠΈΠ· ΡΠ³Π»Π΅ΡΠΎΠ΄Π½ΠΎΠ³ΠΎ Π²ΠΎΠ»ΠΎΠΊΠ½Π° ΠΈ ΡΡΠ°Π»ΠΈ. Π Π² ΠΈΡΠΎΠ³Π΅, ΠΎΠ½ΠΈ Π½Π΅ ΡΠΈΠ»ΡΠ½ΠΎ ΠΎΡΠ»ΠΈΡΠ°Π»ΠΈΡΡ ΠΏΠΎ Π²Π΅ΡΡ ΠΎΡ ΡΡΠ°Π»ΡΠ½ΡΡ Π°Π½Π°Π»ΠΎΠ³ΠΎΠ².
Π§Π΅ΡΠ΅Π· ΡΠ΅ΡΡΡΠ΅ Π³ΠΎΠ΄Π° Π°Π²ΡΡΡΠ°Π»ΠΈΠΉΡΠΊΠ°Ρ ΠΊΠΎΠΌΠΏΠ°Π½ΠΈΡ Β«Carbon RevolutionΒ» ΠΏΡΠ΅Π΄ΡΡΠ°Π²ΠΈΠ»Π° ΠΏΠ΅ΡΠ²ΡΠ΅ Π½Π°ΡΡΠΎΡΡΠΈΠ΅ ΡΠ³Π»Π΅ΠΏΠ»Π°ΡΡΠΈΠΊΠΎΠ²ΡΠ΅ Π΄ΠΈΡΠΊΠΈ CR9. ΠΠΎ ΡΡΠ°Π²Π½Π΅Π½ΠΈΡ Ρ ΠΈΠ·Π΄Π΅Π»ΠΈΡΠΌΠΈ ΠΈΠ· ΠΊΠΎΠ²Π°Π½ΠΎΠ³ΠΎ ΠΈΠ»ΠΈ Π»ΠΈΡΠΎΠ³ΠΎ Π°Π»ΡΠΌΠΈΠ½ΠΈΡ ΠΎΠ½ΠΈ ΠΈΠΌΠ΅ΡΡ ΠΌΠ°ΡΡΡ Π½Π° 50 ΠΏΡΠΎΡΠ΅Π½ΡΠΎΠ² ΠΌΠ΅Π½ΡΡΠ΅. ΠΠ½ΡΠΌΠΈ ΡΠ»ΠΎΠ²Π°ΠΌΠΈ, ΠΈΠ· Π²ΡΠ΅Ρ ΡΡΡΠ΅ΡΡΠ²ΡΡΡΠΈΡ Π°Π²ΡΠΎΠΌΠΎΠ±ΠΈΠ»ΡΠ½ΡΡ Π΄ΠΈΡΠΊΠΎΠ² ΠΊΠ°ΡΠ±ΠΎΠ½ΠΎΠ²ΡΠ΅ ΠΌΠΎΠ΄Π΅Π»ΠΈ ΡΠ°ΠΌΡΠ΅ Π»Π΅Π³ΠΊΠΈΠ΅.
ΠΠ°ΠΊ ΠΏΡΠΎΠΈΠ·Π²ΠΎΠ΄ΡΡ ΠΊΠ°ΡΠ±ΠΎΠ½
ΠΠ°ΡΠ±ΠΎΠ½ β ΡΡΠΎ ΠΊΠΎΠΌΠΏΠΎΠ·ΠΈΡΠ½ΡΠΉ ΠΌΠ°ΡΠ΅ΡΠΈΠ°Π», ΠΊΠΎΡΠΎΡΡΠΉ ΡΠΎΡΡΠΎΠΈΡ ΠΈΠ· ΡΠ°ΠΊΠΈΡ Π²Π΅ΡΠ΅ΡΡΠ², ΠΊΠ°ΠΊ ΠΏΠΎΠ»ΠΈΠΌΠ΅ΡΠ½Π°Ρ ΡΠΌΠΎΠ»Π° ΠΈ ΡΠ³Π»Π΅ΡΠΎΠ΄Π½ΠΎΠ΅ Π²ΠΎΠ»ΠΎΠΊΠ½ΠΎ. ΠΠΈΠ°ΠΌΠ΅ΡΡ Π²ΠΎΠ»ΠΎΠΊΠ½Π° Π½Π΅ ΠΏΡΠ΅Π²ΡΡΠ°Π΅Ρ ΡΠΎΡΠΎΠΉ ΡΠ°ΡΡΠΈ ΠΌΠΈΠ»Π»ΠΈΠΌΠ΅ΡΡΠ°! ΠΡΠ½ΠΎΠ²ΠΎΠΉ ΠΌΠ°ΡΠ΅ΡΠΈΠ°Π»Π° ΡΠ²Π»ΡΡΡΡΡ Π°ΡΠΎΠΌΡ ΡΠ³Π»Π΅ΡΠΎΠ΄Π°, ΠΎΠ±ΡΠ΅Π΄ΠΈΠ½Π΅Π½Π½ΡΠ΅ Π² ΡΠΎΡΠΌΠ΅ ΠΌΠΈΠΊΡΠΎΡΠΊΠΎΠΏΠΈΡΠ΅ΡΠΊΠΈΡ ΠΊΡΠΈΡΡΠ°Π»Π»ΠΎΠ². Π ΡΠ΅Π·ΡΠ»ΡΡΠ°ΡΠ΅ ΠΏΠΎΠΌΠΈΠΌΠΎ ΠΏΡΠ΅ΠΊΡΠ°ΡΠ½ΠΎΠ³ΠΎ Π²Π½Π΅ΡΠ½Π΅Π³ΠΎ Π²ΠΈΠ΄Π° ΠΌΡ ΠΈΠΌΠ΅Π΅ΠΌ Π²ΡΡΠΎΠΊΡΡ ΠΏΡΠΎΡΠ½ΠΎΡΡΡ ΠΈ Π½Π°Π΄Π΅ΠΆΠ½ΠΎΡΡΡ.
ΠΡΠΎΡΠ΅ΡΡ ΡΠ°Π±ΠΎΡΡ Ρ ΡΠ³Π»Π΅ΠΏΠ»Π°ΡΡΠΈΠΊΠΎΠ²ΡΠΌ ΠΌΠ°ΡΠ΅ΡΠΈΠ°Π»ΠΎΠΌ Π³ΠΎΡΠ°Π·Π΄ΠΎ ΡΠ»ΠΎΠΆΠ½Π΅Π΅, ΡΠ΅ΠΌ Π² ΡΠ»ΡΡΠ°Π΅ ΡΠΎ ΡΡΠ°Π»ΡΡ ΠΈΠ»ΠΈ Π°Π»ΡΠΌΠΈΠ½ΠΈΠ΅ΠΌ, Π½ΠΎ, Π½Π΅ΡΠΌΠΎΡΡΡ Π½Π° ΡΡΠΎ, ΡΠΎΠ²ΡΠ΅ΠΌΠ΅Π½Π½ΠΎΠ΅ ΡΠ΅Ρ Π½ΠΈΡΠ΅ΡΠΊΠΎΠ΅ ΠΎΠ±Π΅ΡΠΏΠ΅ΡΠ΅Π½ΠΈΠ΅ ΡΠΏΠΎΡΠΎΠ±Π½ΠΎ ΡΠΏΡΠ°Π²ΠΈΡΡΡΡ Ρ ΡΡΠΎΠΉ Π½Π΅ΠΏΡΠΎΡΡΠΎΠΉ Π·Π°Π΄Π°ΡΠ΅ΠΉ. ΠΠ· ΡΠ³Π»Π΅ΡΠΎΠ΄Π½ΠΎΠ³ΠΎ Π²ΠΎΠ»ΠΎΠΊΠ½Π° ΠΈΠ·Π³ΠΎΡΠ°Π²Π»ΠΈΠ²Π°Π΅ΡΡΡ ΡΠΊΠ°Π½Ρ, ΠΊΠΎΡΠΎΡΡΡ ΡΠΊΠ»Π°Π΄ΡΠ²Π°ΡΡ Π² ΡΡΠ΅Π±ΡΠ΅ΠΌΡΡ ΡΠΎΡΠΌΡ. ΠΠ°Π»Π΅Π΅, ΠΏΠΎΡΠ»Π΅ ΡΠ°Π·ΠΌΠ΅ΡΠ΅Π½ΠΈΡ Π² ΠΏΠΎΠ»ΠΈΠΌΠ΅ΡΠ΅, ΠΎΠ½Π° ΠΏΠΎΠ΄Π²Π΅ΡΠ³Π°Π΅ΡΡΡ Π΄Π°Π²Π»Π΅Π½ΠΈΡ ΠΏΠΎΠ΄ Π²ΡΡΠΎΠΊΠΎΠΉ ΡΠ΅ΠΌΠΏΠ΅ΡΠ°ΡΡΡΠΎΠΉ. ΠΠ° Π²ΡΡ ΠΎΠ΄Π΅ ΠΌΡ ΠΏΠΎΠ»ΡΡΠ°Π΅ΠΌ ΡΠΎΠ²ΡΠ΅ΠΌΠ΅Π½Π½ΡΠΉ ΠΌΠ°ΡΠ΅ΡΠΈΠ°Π», Ρ ΡΡΠ΄ΠΎΠΌ Π½Π΅ΠΎΡΠΏΠΎΡΠΈΠΌΡΡ Π΄ΠΎΡΡΠΎΠΈΠ½ΡΡΠ² β ΠΊΠ°ΡΠ±ΠΎΠ½.
ΠΠ»ΡΡΡ ΠΈ ΠΌΠΈΠ½ΡΡΡ ΠΊΠ°ΡΠ±ΠΎΠ½ΠΎΠ²ΡΡ Π΄ΠΈΡΠΊΠΎΠ²
ΠΠΎΠ»ΠΎΠΆΠΈΡΠ΅Π»ΡΠ½ΡΠ΅ ΡΡΠΎΡΠΎΠ½Ρ Π΄ΠΈΡΠΊΠΎΠ² ΠΈΠ· ΠΊΠ°ΡΠ±ΠΎΠ½Π°:
- ΠΠ°ΡΠ΅ΡΠΈΠ°Π»Ρ Π½Π΅ ΡΡΡΠ°ΡΠ½Π° ΠΎΠ³ΡΠΎΠΌΠ½Π°Ρ Π½Π°Π³ΡΡΠ·ΠΊΠ°. ΠΡΠΈ ΡΠ»ΠΈΡΠΊΠΎΠΌ Π²ΡΡΠΎΠΊΠΎΠΉ ΡΠΊΠΎΡΠΎΡΡΠΈ ΠΎΠ±ΡΠΊΠ½ΠΎΠ²Π΅Π½Π½ΡΠ΅ Π΄ΠΈΡΠΊΠΈ ΠΌΠΎΠ³ΡΡ ΠΏΠΎΠ»ΡΡΠΈΡΡ ΠΏΠΎΠ²ΡΠ΅ΠΆΠ΄Π΅Π½ΠΈΡ, Π² ΡΠΎ Π²ΡΠ΅ΠΌΡ ΠΊΠ°ΠΊ ΠΌΠΎΠ΄Π΅Π»ΠΈ ΠΈΠ· ΠΊΠ°ΡΠ±ΠΎΠ½Π° ΡΡΠ²ΡΡΠ²ΡΡΡ ΡΠ΅Π±Ρ Π² ΡΠ°ΠΊΠΎΠΉ ΡΠΈΡΡΠ°ΡΠΈΠΈ Π½Π°ΠΌΠ½ΠΎΠ³ΠΎ ΡΡΡΠ½Π΅ΠΉ.
- ΠΠ΅Π³ΠΊΠΎΡΡΡ ΠΌΠ°ΡΠ΅ΡΠΈΠ°Π»Π°. ΠΠΎΠΊΠ»ΠΎΠ½Π½ΠΈΠΊΠΈ Π±ΠΎΠ»ΡΡΠΈΡ ΡΠΊΠΎΡΠΎΡΡΠ΅ΠΉ ΠΏΠΎ Π΄ΠΎΡΡΠΎΠΈΠ½ΡΡΠ²Ρ ΠΎΡΠ΅Π½ΡΡ ΡΡΠΎ ΠΊΠ°ΡΠ΅ΡΡΠ²ΠΎ. Π’Π°ΠΊΠΆΠ΅ ΡΡΠΎΠΈΡ ΡΠΏΠΎΠΌΡΠ½ΡΡΡ, ΡΡΠΎ ΠΌΠ°ΡΠΈΠ½Π° ΠΌΠ΅Π½ΡΡΠ΅Π³ΠΎ Π²Π΅ΡΠ° ΠΏΠΎΠ·Π²ΠΎΠ»ΡΠ΅Ρ ΡΡΠΊΠΎΠ½ΠΎΠΌΠΈΡΡ Π½Π° Π³ΠΎΡΡΡΠ΅ΠΌ.
- ΠΡΠ»ΠΈΡΠ½ΡΠ΅ Π°ΡΡΠΎΠ΄ΠΈΠ½Π°ΠΌΠΈΡΠ΅ΡΠΊΠΈΠ΅ Ρ Π°ΡΠ°ΠΊΡΠ΅ΡΠΈΡΡΠΈΠΊΠΈ. ΠΡΡΡΡΡΡΠ²ΠΈΠ΅ ΡΠΎΠΏΡΠΎΡΠΈΠ²Π»Π΅Π½ΠΈΡ Π²ΠΎΠ·Π΄ΡΡ Π° ΡΠ½ΠΈΠΆΠ°Π΅Ρ ΠΏΠΎΡΡΠ΅Π±Π»Π΅Π½ΠΈΠ΅ ΡΠΎΠΏΠ»ΠΈΠ²Π° ΠΈ ΡΡΠΎΠΊ ΠΈΠ·Π½Π°ΡΠΈΠ²Π°Π½ΠΈΡ Π΄ΠΈΡΠΊΠΎΠ².
- ΠΡΡΠΎΠΊΠ°Ρ ΡΠ΅ΠΌΠΏΠ΅ΡΠ°ΡΡΡΠ½Π°Ρ ΡΡΠΎΠΉΠΊΠΎΡΡΡ. ΠΠ°ΡΠ΅ΡΠΈΠ°Π» Π½Π΅ ΠΏΠ»Π°Π²ΠΈΡΡΡ Π΄Π°ΠΆΠ΅ ΠΏΡΠΈ ΡΠ΅ΠΏΠ΅ΡΠ°ΡΡΡΠ΅ 1500 Π³ΡΠ°Π΄ΡΡΠΎΠ².
Π Π½Π΅Π΄ΠΎΡΡΠ°ΡΠΊΠ°ΠΌ ΠΌΠΎΠΆΠ½ΠΎ ΠΎΡΠ½Π΅ΡΡΠΈ ΡΠ»Π΅Π΄ΡΡΡΠ΅Π΅:
- ΠΠ°ΡΠ±ΠΎΠ½ΠΎΠ²ΡΠ΅ Π΄ΠΈΡΠΊΠΈ, Π½Π΅ΡΠΌΠΎΡΡΡ Π½Π° ΠΎΠ±ΡΡΡ ΠΏΡΠΎΡΠ½ΠΎΡΡΡ, Π½Π΅ ΠΏΠ΅ΡΠ΅Π½ΠΎΡΡΡ ΡΠΎΡΠ΅ΡΠ½ΡΠ΅ ΡΠ΄Π°ΡΡ, ΠΊΠΎΡΠΎΡΡΠ΅ ΠΌΠΎΠ³ΡΡ ΠΏΡΠΈΠ²Π΅ΡΡΠΈ ΠΊ ΡΠ°ΡΠΊΠ°Π»ΡΠ²Π°Π½ΠΈΡ ΠΌΠ°ΡΠ΅ΡΠΈΠ°Π»Π° Π½Π° ΠΌΠ΅Π»ΠΊΠΈΠ΅ ΠΎΡΠΊΠΎΠ»ΠΊΠΈ, Π½Π΅ ΠΏΠΎΠ΄Π»Π΅ΠΆΠ°ΡΠΈΠ΅ ΡΠ΅ΠΌΠΎΠ½ΡΡ.
- ΠΡΠΎΠΈΠ·Π²ΠΎΠ΄ΡΡΠ²ΠΎ Π΄ΠΈΡΠΊΠΎΠ² ΠΈΠ· ΡΡΠΎΠ³ΠΎ ΠΌΠ°ΡΠ΅ΡΠΈΠ°Π»Π° Π·Π°Π½ΠΈΠΌΠ°Π΅Ρ Π±ΠΎΠ»ΡΡΠΎΠ΅ ΠΊΠΎΠ»ΠΈΡΠ΅ΡΡΠ²ΠΎ Π²ΡΠ΅ΠΌΠ΅Π½ΠΈ.
- Π‘ΠΎΠ»Π½Π΅ΡΠ½ΡΠ΅ Π»ΡΡΠΈ ΠΏΡΠΈΠ²ΠΎΠ΄ΡΡ ΠΊ Π²ΡΠ³ΠΎΡΠ°Π½ΠΈΡ ΡΠ³Π»Π΅ΠΏΠ»Π°ΡΡΠΈΠΊΠ°, ΡΡΠΎ ΡΠΊΠ°Π·ΡΠ²Π°Π΅ΡΡΡ Π½Π° ΠΏΡΠΈΠ²Π»Π΅ΠΊΠ°ΡΠ΅Π»ΡΠ½ΠΎΡΡΠΈ Π²Π½Π΅ΡΠ½Π΅Π³ΠΎ Π²ΠΈΠ΄Π° ΠΈΠ·Π΄Π΅Π»ΠΈΡ. ΠΠΎΡΡΠΎΠΌΡ ΡΡΠ΅Π±ΡΠ΅ΡΡΡ Π΄ΠΎΠΏΠΎΠ»Π½ΠΈΡΠ΅Π»ΡΠ½Π°Ρ Π·Π°ΡΠΈΡΠ° ΠΎΡ ΡΠ»ΡΡΡΠ°ΡΠΈΠΎΠ»Π΅ΡΠ°.
- ΠΠ°ΡΡΠΎΠ»ΡΠΊΠΎ Π²ΡΡΠΎΠΊΠ°Ρ ΡΡΠΎΠΈΠΌΠΎΡΡΡ, ΡΡΠΎ ΠΏΠΎ ΡΡΠ°Π²Π½Π΅Π½ΠΈΡ Ρ ΠΊΠ°ΡΠ±ΠΎΠ½ΠΎΠ²ΡΠΌΠΈ Π΄ΠΈΡΠΊΠ°ΠΌΠΈ, Π΄Π°ΠΆΠ΅ ΡΠΈΡΠ°Π½ΠΎΠ²ΡΠ΅ ΠΌΠΎΠ΄Π΅Π»ΠΈ ΠΏΠΎΠΊΠ°ΠΆΡΡΡΡ Π΄Π΅ΡΠ΅Π²ΡΠΌΠΈ.
Π‘ΡΠΎΠΈΡ Π»ΠΈ ΠΏΠΎΠΊΡΠΏΠ°ΡΡ ΠΊΠ°ΡΠ±ΠΎΠ½ΠΎΠ²ΡΠ΅ Π΄ΠΈΡΠΊΠΈ?
ΠΠ°ΡΠ±ΠΎΠ½ΠΎΠ²ΡΠ΅ Π΄ΠΈΡΠΊΠΈ ΠΏΠΎΠ΄Ρ ΠΎΠ΄ΡΡ Π΄Π»Ρ Π²ΡΠ΅Ρ Π²ΠΈΠ΄ΠΎΠ² Π°Π²ΡΠΎΠΌΠΎΠ±ΠΈΠ»Π΅ΠΉ, Π² ΡΠΎΠΌ ΡΠΈΡΠ»Π΅ ΠΈ Π΄Π»Ρ Π₯Π΅Π½Π΄Π°ΠΉ Π‘ΠΎΠ»ΡΡΠΈΡ, ΠΏΠΎΡΠΎΠΌΡ ΡΡΠΎ ΠΊΠΎΠ»Π΅ΡΠΎ ΠΈΠ· ΡΠ³Π»Π΅ΠΏΠ»Π°ΡΡΠΈΠΊΠ° ΠΌΠΎΠΆΠ½ΠΎ ΠΈΠ·Π³ΠΎΡΠΎΠ²ΠΈΡΡ Π°Π±ΡΠΎΠ»ΡΡΠ½ΠΎ Π»ΡΠ±ΠΎΠ³ΠΎ ΡΠ°Π·ΠΌΠ΅ΡΠ° ΠΈ ΡΠΎΡΠΌΡ. ΠΠ»Π°Π³ΠΎΠ΄Π°ΡΡ ΠΊΠΎΠΌΠΏΡΡΡΠ΅ΡΠ½ΠΎΠΌΡ ΠΎΠ±ΠΎΡΡΠ΄ΠΎΠ²Π°Π½ΠΈΡ Π΄ΠΎΡΡΠΈΠ³Π°Π΅ΡΡΡ Π²ΡΡΠΎΠΊΠ°Ρ ΡΠΎΡΠ½ΠΎΡΡΡ ΠΏΡΠΎΠΈΠ·Π²ΠΎΠ΄ΡΡΠ²Π°.
ΠΠ° Π³ΠΎΠ½ΠΎΡΠ½ΠΎΠΉ ΡΡΠ°ΡΡΠ΅ ΠΌΠΎΠΆΠ½ΠΎ ΡΠ°ΡΡΠΎ Π²ΡΡΡΠ΅ΡΠΈΡΡ Π±ΠΎΠ»ΠΈΠ΄Ρ, ΠΎΡΠ½Π°ΡΠ΅Π½Π½ΡΠ΅ ΠΊΠ°ΡΠ±ΠΎΠ½ΠΎΠ²ΡΠΌΠΈ Π΄ΠΈΡΠΊΠ°ΠΌΠΈ. Π ΡΠ²ΠΎΡ ΠΎΡΠ΅ΡΠ΅Π΄Ρ, ΠΏΠΎΠΊΡΠΏΠΊΡ ΡΠ°ΠΊΠΈΡ ΠΊΠΎΠ»Π΅Ρ Π΄Π»Ρ ΠΎΠ±ΡΡΠ½ΠΎΠΉ ΠΌΠ°ΡΠΈΠ½Ρ ΡΠ»ΠΎΠΆΠ½ΠΎ Π½Π°Π·Π²Π°ΡΡ ΡΠ°ΡΠΈΠΎΠ½Π°Π»ΡΠ½ΠΎΠΉ, Ρ.ΠΊ. ΡΠ΅Π½Π° ΠΎΠ΄Π½ΠΎΠ³ΠΎ Π΄ΠΈΡΠΊΠ° ΠΈΠ·ΠΌΠ΅ΡΡΠ΅ΡΡΡ ΡΡΡΡΡΠ°ΠΌΠΈ Π΄ΠΎΠ»Π»Π°ΡΠΎΠ². Π Π΅ΡΠ»ΠΈ ΠΌΡ ΠΈΠΌΠ΅Π΅ΠΌ Π΄Π΅Π»ΠΎ Ρ Π΄ΠΈΠ·Π°ΠΉΠ½Π΅ΡΡΠΊΠΈΠΌΠΈ ΠΌΠΎΠ΄Π΅Π»ΡΠΌΠΈ, ΡΠΎ ΡΠΈΡΡΡ Π½Π° ΡΠ΅Π½Π½ΠΈΠΊΠ΅ ΡΠ²Π΅Π»ΠΈΡΠ°ΡΡΡ Π² ΡΠ°Π·Ρ.
ΠΠ΄Π½Π°ΠΊΠΎ Π½Π° ΡΡΠ½ΠΊΠ΅ ΡΠΆΠ΅ ΠΌΠΎΠΆΠ½ΠΎ Π²ΡΡΡΠ΅ΡΠΈΡΡ Π»Π΅Π³ΠΊΠΎΠ²ΡΠ΅ ΠΌΠ°ΡΠΈΠ½Ρ Ρ ΡΠ³Π»Π΅ΠΏΠ»Π°ΡΡΠΈΠΊΠΎΠ²ΡΠΌΠΈ Π΄ΠΈΡΠΊΠ°ΠΌΠΈ. ΠΠΎ ΠΌΠ½Π΅Π½ΠΈΡ ΡΠΏΠ΅ΡΠΈΠ°Π»ΠΈΡΡΠΎΠ², Π² Π±Π»ΠΈΠΆΠ°ΠΉΡΠ΅ΠΌ Π±ΡΠ΄ΡΡΠ΅ΠΌ Π²ΡΠ΅ Π°Π²ΡΠΎΠΌΠΎΠ±ΠΈΠ»ΠΈ Π±ΡΠ΄ΡΡ ΠΎΡΠ½Π°ΡΠ΅Π½Ρ ΠΏΠΎΠ΄ΠΎΠ±Π½ΡΠΌΠΈ ΠΊΠΎΠ»Π΅ΡΠ°ΠΌΠΈ. Π’Π°ΠΊΠΈΠΌ ΠΎΠ±ΡΠ°Π·ΠΎΠΌ, Π½Π° Π΄Π°Π½Π½ΡΠΉ ΠΌΠΎΠΌΠ΅Π½Ρ Π³Π»Π°Π²Π½Π°Ρ ΠΎΠ±Π»Π°ΡΡΡ ΠΏΡΠΈΠΌΠ΅Π½Π΅Π½ΠΈΡ ΠΊΠΎΠ»Π΅Ρ ΠΈΠ· ΡΠ³Π»Π΅ΠΏΠ»Π°ΡΡΠΈΠΊΠ° β ΡΡΠΎ ΠΏΡΠΎΠΈΠ·Π²ΠΎΠ΄ΡΡΠ²ΠΎ Π³ΠΎΠ½ΠΎΡΠ½ΡΡ Π°Π²ΡΠΎΠΌΠΎΠ±ΠΈΠ»Π΅ΠΉ.
Π·Π°Π³ΡΡΠ·ΠΊΠ°…
solarisavto.com
ΠΠ°ΡΠ±ΠΎΠ½ΠΎΠ²ΡΠ΅ Π΄ΠΈΡΠΊΠΈ β Ρ Π°ΡΠ°ΠΊΡΠ΅ΡΠΈΡΡΠΈΠΊΠΈ, ΠΏΡΠ΅ΠΈΠΌΡΡΠ΅ΡΡΠ²Π°, ΠΏΠ΅ΡΡΠΏΠ΅ΠΊΡΠΈΠ²Ρ Π½Π° ΡΡΠ½ΠΊΠ΅
Π§ΡΠΎ ΡΠ°ΠΊΠΎΠ΅ ΠΊΠ°ΡΠ±ΠΎΠ½, ΠΈ ΡΠ΅ΠΌ ΠΎΠ½ Π»ΡΡΡΠ΅ ΡΡΠ°Π΄ΠΈΡΠΈΠΎΠ½Π½ΡΡ ΡΠΏΠ»Π°Π²ΠΎΠ²
ΠΡΠ½ΠΎΠ²Ρ ΠΊΠ°ΡΠ±ΠΎΠ½Π° ΡΠΎΡΡΠ°Π²Π»ΡΡΡ Π²ΠΎΠ»ΠΎΠΊΠ½Π° ΡΠ³Π»Π΅ΡΠΎΠ΄Π°, ΠΊΠΎΡΠΎΡΡΠ΅ ΡΠ°ΡΡΠΎ ΡΠΎΠ΅Π΄ΠΈΠ½ΡΡΡ Ρ ΡΠ΅Π·ΠΈΠ½ΠΎΠ²ΡΠΌΠΈ Π½ΠΈΡΡΠΌΠΈ. ΠΠ»ΠΎΡΠ½ΠΎΡΡΡ ΡΠ³Π»Π΅ΡΠΎΠ΄Π½ΡΡ Π½ΠΈΡΠ΅ΠΉ β 1600 ΠΊΠ³/ΠΌΒ³, Π½ΠΎ ΡΠΏΠΎΡΠΎΠ±Π½ΠΎΡΡΡ ΡΠΎΠΏΡΠΎΡΠΈΠ²Π»ΡΡΡΡΡ ΡΠ°ΡΡΡΠΆΠ΅Π½ΠΈΡ ΠΈ ΡΠ°Π·ΡΡΠ²Ρ Π²ΡΡΠ΅, ΡΠ΅ΠΌ Ρ ΡΡΠ°Π»ΠΈ. ΠΠΎ ΡΠ³Π»Π΅ΡΠΎΠ΄ β Π΅ΡΠ΅ Π½Π΅ ΠΊΠ°ΡΠ±ΠΎΠ½. Π§ΡΠΎΠ±Ρ ΠΏΠΎΠ»ΡΡΠΈΡΡ ΠΈΡΡ ΠΎΠ΄Π½ΡΠΉ ΠΊΠΎΠΌΠΏΠΎΠ·ΠΈΡΠ½ΡΠΉ ΠΌΠ°ΡΠ΅ΡΠΈΠ°Π» Π΄Π»Ρ ΠΊΠ°ΡΠ±ΠΎΠ½ΠΎΠ²ΡΡ Π΄ΠΈΡΠΊΠΎΠ², Π²ΠΎΠ»ΠΎΠΊΠ½Π° ΡΠ³Π»Π΅ΡΠΎΠ΄Π° ΠΈ ΡΠ΅Π·ΠΈΠ½Ρ ΠΏΠ΅ΡΠ΅ΠΏΠ»Π΅ΡΠ°ΡΡ ΠΏΠΎΠ΄ ΡΡΡΠΎΠ³ΠΎ Π²ΡΠ²Π΅ΡΠ΅Π½Π½ΡΠΌ ΡΠ³Π»ΠΎΠΌ, ΠΏΠΎΠ»ΡΡΠ°Ρ ΡΠΊΠ°Π½Ρ. Π Π·Π°ΡΠ΅ΠΌ ΡΠ»ΠΎΠΈ ΡΠΊΠ°Π½ΠΈ ΡΠΊΠ»Π΅ΠΈΠ²Π°ΡΡ ΠΌΠ΅ΠΆΠ΄Ρ ΡΠΎΠ±ΠΎΠΉ ΡΠΏΠΎΠΊΡΠΈΠ΄Π½ΠΎΠΉ ΡΠΌΠΎΠ»ΠΎΠΉ. Π’Π°ΠΊ ΠΈΠ·Π³ΠΎΡΠ°Π²Π»ΠΈΠ²Π°ΡΡ ΡΠ°ΠΌΡΠΉ Π΄ΠΎΡΠΎΠ³ΠΎΠΉ Π² ΠΌΠΈΡΠ΅ ΠΌΠ°ΡΠ΅ΡΠΈΠ°Π» Π΄Π»Ρ ΠΈΠ·Π³ΠΎΡΠΎΠ²Π»Π΅Π½ΠΈΡ ΠΊΠΎΠ»Π΅ΡΠ½ΡΡ Π΄ΠΈΡΠΊΠΎΠ².
ΠΠΎΡΠ΅ΠΌΡ ΠΊΠ°ΡΠ±ΠΎΠ½ ΡΠ°ΠΊ Π΄ΠΎΡΠΎΠ³? ΠΡΠΎ ΡΠ²ΡΠ·Π°Π½ΠΎ Ρ ΡΠ΅Ρ Π½ΠΎΠ»ΠΎΠ³ΠΈΠ΅ΠΉ ΠΏΠΎΠ»ΡΡΠ΅Π½ΠΈΡ Π²ΠΎΠ»ΠΎΠΊΠΎΠ½ ΡΠ³Π»Π΅ΡΠΎΠ΄Π°. Π‘ΡΡΠ΅ΡΡΠ²ΡΠ΅Ρ Π½Π΅ΡΠΊΠΎΠ»ΡΠΊΠΎ ΡΠΏΠΎΡΠΎΠ±ΠΎΠ² Π²ΡΡΠ°ΡΠΈΠ²Π°Π½ΠΈΡ Π΄Π»ΠΈΠ½Π½ΡΡ Π½ΠΈΡΠ΅ΠΉ: Π²ΡΡΠ°ΡΠΈΠ²Π°Π½ΠΈΠ΅ Π² ΡΠ²Π΅ΡΠΎΠ²ΠΎΠΉ Π΄ΡΠ³Π΅, Π°Π²ΡΠΎΠΊΠ»Π°Π²Π΅, Ρ ΠΈΠΌΠΈΡΠ΅ΡΠΊΠΎΠ΅ ΠΎΡΠ°ΠΆΠ΄Π΅Π½ΠΈΠ΅ Π½Π° ΡΠΏΠ΅ΡΠΈΠ°Π»ΡΠ½ΡΠΉ Π½ΠΎΡΠΈΡΠ΅Π»Ρ. Π ΠΏΡΠΎΡΠ΅ΡΡΠ΅ ΠΈΠ·Π³ΠΎΡΠΎΠ²Π»Π΅Π½ΠΈΡ ΡΠ°ΠΌΡΡ Π΄ΠΎΡΠΎΠ³ΠΈΡ Π²ΠΈΠ΄ΠΎΠ² ΡΠ΅ΠΌΠΏΠ΅ΡΠ°ΡΡΡΠ° Π½Π°Π³ΡΠ΅Π²Π° Π΄ΠΎΡΡΠΈΠ³Π°Π΅Ρ 3500 Π³ΡΠ°Π΄ΡΡΠΎΠ², Π° ΠΌΠ΅Π½Π΅Π΅ ΠΏΡΠΎΡΠ½ΡΠ΅ ΡΠΎΡΡΠ° ΡΡΠ΅Π±ΡΡΡ ΡΠ΅ΠΌΠΏΠ΅ΡΠ°ΡΡΡΡ ΠΊΠ°ΠΊ ΠΌΠΈΠ½ΠΈΠΌΡΠΌ Π΄ΠΎ 260 Π³ΡΠ°Π΄ΡΡΠΎΠ². Π Π°Π·ΠΎΠ³ΡΠ΅Π²Π°ΡΡ ΠΈΡΡ ΠΎΠ΄Π½ΠΎΠ΅ ΡΡΡΡΠ΅ (ΠΏΠΎΠ»ΠΈΠ°ΠΊΡΠΈΠ»ΠΎΠ½ΠΈΡΡΠΈΠ½) Π½ΡΠΆΠ½ΠΎ ΡΠΎΠ»ΡΠΊΠΎ Π² ΠΈΠ½Π΅ΡΡΠ½ΠΎΠΉ Π³Π°Π·ΠΎΠ²ΠΎΠΉ ΡΡΠ΅Π΄Π΅, ΡΡΠΎ ΠΏΡΠΈΠ²ΠΎΠ΄ΠΈΡ ΠΊ Π΄ΠΎΠΏΠΎΠ»Π½ΠΈΡΠ΅Π»ΡΠ½ΡΠΌ ΡΠ°ΡΡ ΠΎΠ΄Π°ΠΌ.
ΠΠΏΡΠΎΡΠ΅ΠΌ, Π·Π°ΡΡΠ°ΡΡ ΠΎΠΊΡΠΏΠ°ΡΡΡΡ Π·Π° ΡΡΠ΅Ρ ΡΠ½ΠΈΠΊΠ°Π»ΡΠ½ΡΡ Ρ Π°ΡΠ°ΠΊΡΠ΅ΡΠΈΡΡΠΈΠΊ ΡΠ³Π»Π΅ΠΏΠ»Π°ΡΡΠΈΠΊΠ°. Π£Π³Π»Π΅Π²ΠΎΠ»ΠΎΠΊΠ½ΠΎ Π½Π° 40% Π»Π΅Π³ΡΠ΅ ΡΡΠ°Π»ΠΈ, ΠΌΠΎΠΆΠ΅Ρ Π²ΡΠ΄Π΅ΡΠΆΠΈΠ²Π°ΡΡ Π½Π°Π³ΡΡΠ·ΠΊΡ Π΄ΠΎ 70 000 ΠΊΠ³ Π½Π° ΠΊΠ²Π°Π΄ΡΠ°ΡΠ½ΡΠΉ ΠΌΠΈΠ»Π»ΠΈΠΌΠ΅ΡΠΎΡ, ΠΏΡΠΎΡΠ½ΠΎΡΡΡ Π½Π° ΡΠ°Π·ΡΡΠ² ΡΠΎΡΡΠ°Π²Π»ΡΠ΅Ρ ΠΎΠΊΠΎΠ»ΠΎ 5 ΠΠΏΠ°. ΠΠΎΠ»Π΅ΡΠ½ΡΠ΅ Π΄ΠΈΡΠΊΠΈ ΠΈΠ· ΡΠ³Π»Π΅ΠΏΠ»Π°ΡΡΠΈΠΊΠ° ΠΏΠΎΠ»ΡΡΠ°ΡΡΡΡ Π»Π΅Π³ΠΊΠΈΠΌΠΈ ΠΈ ΠΈΡΠΊΠ»ΡΡΠΈΡΠ΅Π»ΡΠ½ΠΎ ΠΏΡΠΎΡΠ½ΡΠΌΠΈ, Π° ΠΏΡΠΈΠ²Π»Π΅ΠΊΠ°ΡΠ΅Π»ΡΠ½ΡΠΉ Π²Π½Π΅ΡΠ½ΠΈΠΉ Π²ΠΈΠ΄ ΠΏΠΎΠ²Π΅ΡΡ Π½ΠΎΡΡΠΈ ΠΏΡΠΈΠ²Π΅Π» ΠΊ ΠΏΠΎΡΠ²Π»Π΅Π½ΠΈΡ Π΄ΠΈΠ·Π°ΠΉΠ½Π° ΠΌΠΎΠ΄Π΅Π»Π΅ΠΉ ΠΈΠ· ΡΠΏΠ»Π°Π²ΠΎΠ² Β«ΠΏΠΎΠ΄ ΠΊΠ°ΡΠ±ΠΎΠ½Β».
ΠΠ»ΡΡΡ ΠΈ ΠΌΠΈΠ½ΡΡΡ ΡΠ³Π»Π΅ΠΏΠ»Π°ΡΡΠΈΠΊΠΎΠ²ΡΡ Π΄ΠΈΡΠΊΠΎΠ²
ΠΠ½Π°ΡΠ°Π»Π΅ ΠΊΠ°ΡΠ±ΠΎΠ½ΠΎΠ²ΡΠ΅ ΠΊΠΎΠ»Π΅ΡΠ° ΡΡΡΠ°Π½Π°Π²Π»ΠΈΠ²Π°Π»ΠΈ ΡΠΎΠ»ΡΠΊΠΎ Π½Π° Π³ΠΎΠ½ΠΎΡΠ½ΡΠ΅ ΡΠΏΠΎΡΡΠΈΠ²Π½ΡΠ΅ ΠΌΠ°ΡΠΈΠ½Ρ. ΠΠ΅Π³ΠΊΠΈΠ΅ ΠΈ ΠΏΡΠΎΡΠ½ΡΠ΅ ΠΊΠΎΠ»Π΅ΡΠ° ΠΎΠ±Π΅ΡΠΏΠ΅ΡΠΈΠ²Π°Π»ΠΈ ΠΏΡΠ΅ΠΊΡΠ°ΡΠ½ΡΡ ΡΠΏΡΠ°Π²Π»ΡΠ΅ΠΌΠΎΡΡΡ Π±ΠΎΠ»ΠΈΠ΄ΠΎΠ², Π½Π΅ Π±ΠΎΡΠ»ΠΈΡΡ ΠΏΠ΅ΡΠ΅Π³ΡΠ΅Π²Π° ΠΈΠ·-Π·Π° Π²ΡΡΠΎΠΊΠΈΡ ΡΠΊΠΎΡΠΎΡΡΠ΅ΠΉ, ΠΈΠΌΠ΅Π»ΠΈ Π±ΠΎΠ»Π΅Π΅ Π²ΡΡΠΎΠΊΠΈΠΉ ΡΠ΅ΡΡΡΡ ΠΏΡΠΎΡΠ½ΠΎΡΡΠΈ. ΠΡΡΠ°ΡΠΈ, ΠΈΠ· ΡΠΎΠ³ΠΎ ΠΆΠ΅ ΠΌΠ°ΡΠ΅ΡΠΈΠ°Π»Π° ΠΈΠ·Π³ΠΎΡΠ°Π²Π»ΠΈΠ²Π°ΡΡ Π΄Π΅ΡΠ°Π»ΠΈ ΡΠΎΡΠΌΠΎΠ·Π½ΠΎΠΉ ΡΠΈΡΡΠ΅ΠΌΡ, ΠΊΠ°ΠΏΠΎΡΡ, ΡΡΠΈΠΊΡΠΈΠΎΠ½Π½ΡΠ΅ Π½Π°ΠΊΠ»Π°Π΄ΠΊΠΈ, ΠΊΡΡΠ»ΡΡ, Π΄Π΅ΡΠ°Π»ΠΈ ΡΠ°Π»ΠΎΠ½Π°.
ΠΠ΅Π³ΠΊΠΎΡΡΡ ΠΈ ΠΊΡΠ°ΡΠΎΡΠ° ΠΊΠΎΠ»Π΅Ρ ΠΈΠ· ΠΊΠ°ΡΠ±ΠΎΠ½Π° β Π½Π΅ Π΅Π΄ΠΈΠ½ΡΡΠ²Π΅Π½Π½ΡΠ΅ Π΅Π³ΠΎ Π΄ΠΎΡΡΠΎΠΈΠ½ΡΡΠ²Π°. ΠΠΈΡΠΊΠΈ Π½Π΅ ΡΠΊΠ»ΠΎΠ½Π½Ρ ΠΊ Π΄Π΅ΡΠΎΡΠΌΠ°ΡΠΈΠΈ, Π²ΡΠ΄Π΅ΡΠΆΠΈΠ²Π°ΡΡ Π²ΡΡΠΎΠΊΠΈΠ΅ ΡΠ΅ΠΌΠΏΠ΅ΡΠ°ΡΡΡΡ, Π½Π΅ Π±ΠΎΡΡΡΡ ΠΊΠΎΡΡΠΎΠ·ΠΈΠΈ. Π’Π΅ΠΎΡΠ΅ΡΠΈΡΠ΅ΡΠΊΠΈ, Π½Π° ΠΏΡΠΎΠ³ΡΠ°ΠΌΠΌΠΈΡΡΠ΅ΠΌΠΎΠΌ ΠΎΠ±ΠΎΡΡΠ΄ΠΎΠ²Π°Π½ΠΈΠΈ ΠΌΠΎΠΆΠ½ΠΎ ΠΈΠ·Π³ΠΎΡΠΎΠ²ΠΈΡΡ ΠΌΠΎΠ΄Π΅Π»ΠΈ Π»ΡΠ±ΡΡ ΡΠΈΠΏΠΎΡΠ°Π·ΠΌΠ΅ΡΠΎΠ² Ρ ΠΊΠ°ΠΊΠΈΠΌ ΡΠ³ΠΎΠ΄Π½ΠΎ Π΄ΠΈΠ·Π°ΠΉΠ½ΠΎΠΌ. ΠΠΎ Π½Π° ΠΏΡΠ°ΠΊΡΠΈΠΊΠ΅ Π²ΡΡΠΎΠΊΠ°Ρ ΡΡΠΎΠΈΠΌΠΎΡΡΡ ΠΎΡΠΏΡΠ³ΠΈΠ²Π°Π΅Ρ Π΄Π°ΠΆΠ΅ ΡΠΎΡΡΠΎΡΡΠ΅Π»ΡΠ½ΡΡ ΠΏΠΎΠΊΡΠΏΠ°ΡΠ΅Π»Π΅ΠΉ.
Π’Π΅ΠΌ Π½Π΅ ΠΌΠ΅Π½Π΅Π΅ Ρ ΠΊΠ°ΡΠ±ΠΎΠ½ΠΎΠ²ΡΡ ΠΊΠΎΠ»Π΅ΡΠ½ΡΡ Π΄ΠΈΡΠΊΠΎΠ² Π΅ΡΡΡ Π½Π΅ΡΠΊΠΎΠ»ΡΠΊΠΎ ΡΠ΅ΡΡΠ΅Π·Π½ΡΡ ΠΌΠΈΠ½ΡΡΠΎΠ². Π‘Π°ΠΌΠΈ ΠΎΠ½ΠΈ Π½Π΅ ΠΏΠΎΠ΄Π²Π΅ΡΠΆΠ΅Π½Ρ ΠΊΠΎΡΡΠΎΠ·ΠΈΠΈ, Π½ΠΎ Π²ΠΎΡ Π²ΡΠ΅ ΠΌΠ΅ΡΠ°Π»Π»ΠΈΡΠ΅ΡΠΊΠΈΠ΅ Π΄Π΅ΡΠ°Π»ΠΈ ΠΎΡ ΠΊΠΎΠ½ΡΠ°ΠΊΡΠ° Ρ ΡΠ³Π»Π΅ΠΏΠ»Π°ΡΡΠΈΠΊΠΎΠΌ ΠΏΡΠΈΠ΄Π΅ΡΡΡ ΡΡΠ°ΡΠ΅Π»ΡΠ½ΠΎ Π·Π°ΡΠΈΡΠ°ΡΡ. ΠΡΠ»ΠΈ ΠΏΠΎΠ»ΠΎΠΆΠΈΡΡ Π²ΠΏΠ»ΠΎΡΠ½ΡΡ Π΄ΡΡΠ³ ΠΊ Π΄ΡΡΠ³Ρ ΡΡΠ°Π³ΠΌΠ΅Π½Ρ ΠΊΠ°ΡΠ±ΠΎΠ½Π° ΠΈ ΡΡΠ°Π»ΡΠ½ΡΡ Π΄Π΅ΡΠ°Π»Ρ ΠΈ ΡΠ±ΡΡΠ·Π½ΡΡΡ ΠΈΡ ΡΠΎΠ»Π΅Π½ΠΎΠΉ Π²ΠΎΠ΄ΠΎΠΉ, ΠΊΠΎΡΡΠΎΠ·ΠΈΡ Π±ΡΠ΄Π΅Ρ ΡΠ°ΡΠΏΡΠΎΡΡΡΠ°Π½ΡΡΡΡΡ ΡΠΎ ΡΠΊΠΎΡΠΎΡΡΡΡ Π»Π΅ΡΠ½ΠΎΠ³ΠΎ ΠΏΠΎΠΆΠ°ΡΠ°. Π’Π°ΠΊ ΡΡΠΎ Π² ΠΌΠ΅ΡΡΠ°Ρ ΠΊΠΎΠ½ΡΠ°ΠΊΡΠ° Ρ ΠΌΠ΅ΡΠ°Π»Π»ΠΈΡΠ΅ΡΠΊΠΈΠΌΠΈ Π΄Π΅ΡΠ°Π»ΡΠΌΠΈ ΠΏΡΠΈΠ΄Π΅ΡΡΡ ΡΡΡΠ°Π½Π°Π²Π»ΠΈΠ²Π°ΡΡ Π½Π°ΠΊΠ»Π°Π΄ΠΊΠΈ ΠΈΠ· Π½Π΅ΠΉΡΡΠ°Π»ΡΠ½ΠΎΠ³ΠΎ ΠΌΠ°ΡΠ΅ΡΠΈΠ°Π»Π° ΠΈΠ»ΠΈ Π½Π°Π½ΠΎΡΠΈΡΡ Π·Π°ΡΠΈΡΠ½ΡΠ΅ Π»Π°ΠΊΠΈ ΠΏΠΎΠ²ΡΡΠ΅Π½Π½ΠΎΠΉ ΠΏΡΠΎΡΠ½ΠΎΡΡΠΈ.
ΠΡΠΎΡΠΎΠΉ Π²Π°ΠΆΠ½ΡΠΉ Π½Π΅Π΄ΠΎΡΡΠ°ΡΠΎΠΊ β Π½Π΅ΡΠ΅ΠΌΠΎΠ½ΡΠΎΠΏΡΠΈΠ³ΠΎΠ΄Π½ΠΎΡΡΡ. Π‘ΠΎΠ³Π»Π°ΡΠΈΡΠ΅ΡΡ, ΠΎΡΠ΄Π°ΡΡ Π½Π΅ΡΠΊΠΎΠ»ΡΠΊΠΎ ΡΡΡΡΡ Π΄ΠΎΠ»Π»Π°ΡΠΎΠ² Π·Π° ΠΊΠΎΠ»Π΅ΡΠ½ΡΠΉ Π΄ΠΈΡΠΊ ΠΈ Π²ΡΠ±ΡΠΎΡΠΈΡΡ Π΅Π³ΠΎ Π² ΡΠ»ΡΡΠ°Π΅ ΠΏΠΎΠ²ΡΠ΅ΠΆΠ΄Π΅Π½ΠΈΡ Π±ΡΠ΄Π΅Ρ ΠΎΠ±ΠΈΠ΄Π½ΠΎ. Π’ΡΡ Π½Π΅ ΡΠΏΠ°ΡΡΡ Π½ΠΈ ΡΠΊΠΎΠ½ΠΎΠΌΠΈΡ ΡΠΎΠΏΠ»ΠΈΠ²Π° Π·Π° ΡΡΠ΅Ρ ΠΌΠ°Π»ΠΎΠ³ΠΎ Π²Π΅ΡΠ°, Π½ΠΈ Π²Π΅Π»ΠΈΠΊΠΎΠ»Π΅ΠΏΠ½ΡΠ΅ Π°ΡΡΠΎΠ΄ΠΈΠ½Π°ΠΌΠΈΡΠ΅ΡΠΊΠΈΠ΅ Ρ Π°ΡΠ°ΠΊΡΠ΅ΡΠΈΡΡΠΈΠΊΠΈ. ΠΠ°ΠΊΠΎΠ½Π΅Ρ, ΠΊΠΎΠ»Π΅ΡΠ° ΠΈΠ· ΡΠ³Π»Π΅ΠΏΠ»Π°ΡΡΠΈΠΊΠ° Π±ΠΎΡΡΡΡ ΡΠ»ΡΡΡΠ°ΡΠΈΠΎΠ»Π΅ΡΠ°. ΠΡ ΡΠ²ΠΎΠΉΡΡΠ²Π° ΠΎΡΡΠ°ΡΡΡΡ ΠΏΡΠ΅ΠΆΠ½ΠΈΠΌΠΈ, Π½ΠΎ ΠΏΠΎΠ²Π΅ΡΡ Π½ΠΎΡΡΡ Π²ΡΡΠ²Π΅ΡΠ°Π΅Ρ ΠΈ ΡΡΠ°Π½ΠΎΠ²ΠΈΡΡΡ Π½Π΅ ΡΠ°ΠΊΠΎΠΉ ΠΊΡΠ°ΡΠΈΠ²ΠΎΠΉ.
Π‘Π΅Π½ΡΠ°ΡΠΈΠΎΠ½Π½ΠΎΠ΅ Π·Π°ΡΠ²Π»Π΅Π½ΠΈΠ΅ ΠΎΡ Porsche
ΠΠ΅Π΄Π°Π²Π½ΠΎ ΠΊΠΎΠΌΠΏΠ°Π½ΠΈΡ ΠΠΎΡΡΠ΅ Π·Π°ΡΠ²ΠΈΠ»Π° ΠΎ ΡΠΎΠ·Π΄Π°Π½ΠΈΠΈ Π½ΠΎΠ²ΠΎΠΉ ΡΠ΅Ρ Π½ΠΎΠ»ΠΎΠ³ΠΈΠΈ ΠΈΠ·Π³ΠΎΡΠΎΠ²Π»Π΅Π½ΠΈΡ ΠΊΠ°ΡΠ±ΠΎΠ½ΠΎΠ²ΡΡ ΠΊΠΎΠ»Π΅ΡΠ½ΡΡ Π΄ΠΈΡΠΊΠΎΠ². ΠΡΠΎΠ΄ΡΠΊΡ ΠΏΠΎΠ»ΡΡΠΈΠ»ΡΡ Π½Π° 20% Π»Π΅Π³ΡΠ΅ ΠΈ Π½Π° ΡΡ ΠΆΠ΅ Π²Π΅Π»ΠΈΡΠΈΠ½Ρ ΠΆΠ΅ΡΡΡΠ΅, ΡΠ΅ΠΌ Π»ΡΡΡΠΈΠ΅ ΡΠΏΠΎΡΡΠΈΠ²Π½ΡΠ΅ ΠΌΠΎΠ΄Π΅Π»ΠΈ ΠΈΠ· ΡΡΠ°Π»ΠΈ. ΠΠΎΠ½ΡΡΡΡΠΊΡΠΎΡΡ ΡΠΎΠ±ΠΈΡΠ°ΡΡΡΡ ΠΏΠΎΡΡΠ°Π²ΠΈΡΡ ΠΊΠΎΠ»Π΅ΡΠ° Π½Π° Π½ΠΎΠ²ΡΡ ΠΌΠΎΠ΄Π΅Π»Ρ 911 Turbo S Exclusive Series.
Π‘ΡΠΎΠΈΠΌΠΎΡΡΡ ΡΠ³Π»Π΅ΠΏΠ»Π°ΡΡΠΈΠΊΠΎΠ²ΡΡ Π΄ΠΈΡΠΊΠΎΠ² Π±ΡΠ΄Π΅Ρ ΡΡΡΡ Π±ΠΎΠ»ΡΡΠ΅ ΠΏΡΡΠ½Π°Π΄ΡΠ°ΡΠΈ ΡΡΡΡΡ Π΅Π²ΡΠΎ β Π΄ΠΎΡΠΎΠ³ΠΎ, Π½ΠΎ Π·Π½Π°ΡΠΈΡΠ΅Π»ΡΠ½ΠΎ Π½ΠΈΠΆΠ΅ ΠΎΠ±ΡΡΠ½ΡΡ ΡΠ΅Π½ Π½Π° ΠΊΠ°ΡΠ±ΠΎΠ½. Π£Π΄Π΅ΡΠ΅Π²ΠΈΡΡ ΠΏΡΠΎΠΈΠ·Π²ΠΎΠ΄ΡΡΠ²ΠΎ Π±Π΅Π· ΠΏΠΎΡΠ΅ΡΠΈ Ρ Π°ΡΠ°ΠΊΡΠ΅ΡΠΈΡΡΠΈΠΊ ΠΊΠ°ΡΠ±ΠΎΠ½ΠΎΠ²ΡΡ ΠΊΠΎΠ»Π΅Ρ ΡΠ΄Π°Π»ΠΎΡΡ Π·Π° ΡΡΠ΅Ρ ΠΈΡΠΏΠΎΠ»ΡΠ·ΠΎΠ²Π°Π½ΠΈΡ ΠΏΡΠΈΠ½ΡΠΈΠΏΠΈΠ°Π»ΡΠ½ΠΎ Π½ΠΎΠ²ΠΎΠ³ΠΎ ΠΏΠΎΠ΄Ρ ΠΎΠ΄Π°. ΠΠ° ΠΏΡΠΎΠΈΠ·Π²ΠΎΠ΄ΡΡΠ²Π΅ ΡΡΡΠ°Π½ΠΎΠ²ΠΈΠ»ΠΈ Π³ΠΈΠ³Π°Π½ΡΡΠΊΠΈΠΉ Π΄Π΅Π²ΡΡΠΈΠΌΠ΅ΡΡΠΎΠ²ΡΠΉ ΡΡΠ°Π½ΠΎΠΊ Π΄Π»Ρ ΠΏΠ»Π΅ΡΠ΅Π½ΠΈΡ Π½ΠΈΡΠ΅ΠΉ. ΠΠΌΠ΅Π½Π½ΠΎ Π½Π° Π½Π΅ΠΌ ΠΈΠ·Π³ΠΎΡΠ°Π²Π»ΠΈΠ²Π°Π΅ΡΡΡ ΠΎΡΠ½ΠΎΠ²Π°, ΠΊΠΎΡΠΎΡΡΡ ΠΏΡΠΎΠΏΠΈΡΡΠ²Π°ΡΡ ΡΠΌΠΎΠ»ΠΎΠΉ, ΠΎΠ±ΠΆΠΈΠ³Π°ΡΡ Π² Π°Π²ΡΠΎΠΊΠ»Π°Π²Π΅ ΠΈ ΠΊΡΠ°ΡΡΡ.
ΠΡΠ΅Π΄ΡΡΠ°Π²ΠΈΡΠ΅Π»ΠΈ Π±ΡΠ΅Π½Π΄Π° Porsche ΡΡΠΈΡΠ°ΡΡ, ΡΡΠΎ Ρ Π΄ΠΈΡΠΊΠΎΠ² ΠΈΠ· ΡΠ³Π»Π΅ΠΏΠ»Π°ΡΡΠΈΠΊΠ°Π±ΠΎΠ»ΡΡΠΎΠ΅ Π±ΡΠ΄ΡΡΠ΅Π΅. Π ΠΏΡΠ΅Π΄ΡΠΊΠ°Π·ΡΠ²Π°ΡΡ ΠΈΡ ΡΠΊΠΎΡΡΠΉ Π²ΡΡ ΠΎΠ΄ Π² ΡΠ΅ΡΠΈΠΉΠ½ΠΎΠ΅
ΠΏΡΠΎΠΈΠ·Π²ΠΎΠ΄ΡΡΠ²ΠΎ. ΠΡΡΠ°Π»ΠΎΡΡ Π΄ΠΎΠΆΠ΄Π°ΡΡΡΡ ΡΠ½ΠΈΠΆΠ΅Π½ΠΈΡ ΡΠ΅Π½.
megawheel.ru
ΠΠ΅ΡΠ²ΡΠ΅ Π² ΠΌΠΈΡΠ΅ ΠΊΠΎΠ»Π΅ΡΠ½ΡΠ΅ Π΄ΠΈΡΠΊΠΈ ΠΈΠ· ΠΊΠ°ΡΠ±ΠΎΠ½Π° (10 ΡΠΎΡΠΎ)
zubrilov
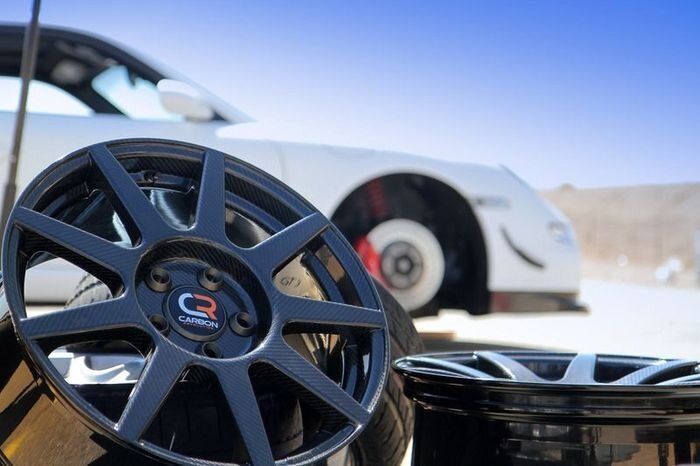
ΠΠ½ΠΎΠ½ΠΈΠΌ
11 ΠΎΠΊΡΡΠ±ΡΡ 2012 11:01
ΠΡΠ»ΠΈ Π²Ρ Ρ
ΠΎΡΠΈΡΠ΅ ΡΠΊΠ°Π·Π°ΡΡ, ΡΡΠΎ ΡΠΆΠ΅ ΡΠ»ΡΡΠ°Π»ΠΈ ΠΏΡΠΎ ΡΠΎ, ΡΡΠΎ ΡΠ°ΠΊΠΈΠ΅ ΡΡΡΠ΅ΡΡΠ²ΡΡΡ, ΡΠΎ ΡΠΏΠ΅ΡΡ Π²Π°Ρ ΠΎΠ³ΠΎΡΡΠΈΡΡ — ΡΠΎ ΡΡΠΎ Π²Ρ ΡΠ»ΡΡΠ°Π»ΠΈ Π±ΡΠ»ΠΈ Π²ΡΠΏΠΎΠ»Π½Π΅Π½Ρ Π½Π΅ ΡΠ΅Π»ΠΈΠΊΠΎΠΌ ΠΈΠ· ΡΠ³Π»Π΅ΡΠΎΠ΄Π½ΠΎΠ³ΠΎ Π²ΠΎΠ»ΠΎΠΊΠ½Π°, Π° Π»ΠΈΡΡ ΠΎΡΠ΄Π΅Π»ΡΠ½ΡΠ΅ ΠΈΡ
ΡΠ°ΡΡΠΈ. ΠΡΠΈ ΠΆΠ΅ Π΄ΠΈΡΠΊΠΈ ΡΠ΄Π΅Π»Π°Π½Ρ Π½Π° 100% ΠΈΠ· ΠΊΠ°ΡΠ±ΠΎΠ½Π° — ΠΈΠΌΠ΅Π½Π½ΠΎ ΡΡΠΈΠΌ ΠΎΠ½ΠΈ ΠΈ ΡΠ½ΠΈΠΊΠ°Π»ΡΠ½Ρ!
ΠΠΎΠΌΠΏΠ°Π½ΠΈΠΈ Π²ΡΠ΅Π³ΠΎ ΠΌΠΈΡΠ° ΡΡΠ°Π½ΠΎΠ²ΡΡΡΡ ΠΎΠ΄Π΅ΡΠΆΠΈΠΌΡΠΌΠΈ ΠΈΠ΄Π΅ΡΠΌΠΈ Π² ΠΏΡΠΈΠΌΠ΅Π½Π΅Π½ΠΈΠΈ ΡΠ³Π»Π΅ΡΠΎΠ΄Π½ΠΎΠ³ΠΎ Π²ΠΎΠ»ΠΎΠΊΠ° Π²Π΅Π·Π΄Π΅ Π³Π΄Π΅ ΡΠΎΠ»ΡΠΊΠΎ ΠΌΠΎΠΆΠ½ΠΎ. ΠΠ²ΡΡΡΠ°Π»ΠΈΠΉΡΠΊΠ°Ρ ΠΊΠΎΠΌΠΏΠ°Π½ΠΈΡ Carbon Revolution ΠΏΠ΅ΡΠ²ΠΎΠΉ ΠΏΡΠ΅Π΄ΡΡΠ°Π²ΠΈΠ»Π° ΡΠ²ΠΎΡ Π½ΠΎΠ²ΡΡ ΡΠ΅ΡΠΈΡ Π΄ΠΈΡΠΊΠΎΠ² CR9, ΠΊΠΎΡΠΎΡΠ°Ρ Π²ΡΠΏΠΎΠ»Π½Π΅Π½Π° ΡΠ΅Π»ΠΈΠΊΠΎΠΌ ΠΈ ΠΏΠΎΠ»Π½ΠΎΡΡΡΡ ΠΈΠ· ΠΊΠ°ΡΠ±ΠΎΠ½Π°!
ΠΡΠΎ ΠΏΠ΅ΡΠ²ΡΠ΅ Π²ΠΎ Π²ΡΡΠΌ ΠΌΠΈΡΠ΅ ΠΏΠΎΠ΄ΠΎΠ±Π½ΡΠ΅ ΠΊΠΎΠ»ΡΡΠ°, Π²Π΅Π΄Ρ ΡΠ°Π½ΡΡΠ΅ ΡΠ°Π·Π²Π΅ ΡΡΠΎ ΠΎΠ±ΠΎΠ΄ ΠΈΠ»ΠΈ ΠΎΡΠ΄Π΅Π»ΡΠ½ΡΠ΅ ΡΠ»Π΅ΠΌΠ΅Π½ΡΡ Π΄Π΅Π»Π°Π»ΠΈ ΠΈΠ· ΡΠ³Π»Π΅ΡΠΎΠ΄Π½ΠΎΠ³ΠΎ Π²ΠΎΠ»ΠΎΠΊΠ½Π°, Π° Π²ΡΡ ΠΎΡΡΠ°Π»ΡΠ½ΠΎΠ΅ Π±ΡΠ» ΠΌΠ΅ΡΠ°Π»Π».
ΠΠ°ΡΡΠ΅ΡΠ° Carbon Revolution ΡΠ°Π±ΠΎΡΠ°Π»ΠΈ Π½Π°Π΄ ΡΡΠΈΠΌΠΈ Π΄ΠΈΡΠΊΠ°ΠΌΠΈ ΠΏΠΎΡΡΠΈ ΡΠ΅Π»ΡΡ
10 Π»Π΅Ρ!
ΠΠ΅Π½Π΅ΡΠ°Π»ΡΠ½ΡΠΉ Π΄ΠΈΡΠ΅ΠΊΡΠΎΡ ΠΊΠΎΠΌΠΏΠ°Π½ΠΈΠΈ ΠΠΈΠ½Π³Π» ΠΠΆΠ΅ΠΉΠΊ ΡΡΠ²Π΅ΡΠΆΠ΄Π°Π΅Ρ, ΡΡΠΎ ΡΠ°ΠΊΠΈΠ΅ Β«ΠΊΠ°ΡΠΊΠΈΒ» Π½Π° 40-50% Π»Π΅Π³ΡΠ΅ ΡΠ²ΠΎΠΈΡ
Π°Π»ΡΠΌΠΈΠ½ΠΈΠ΅Π²ΡΡ
ΡΠΎΠ±ΡΠ°ΡΡΠ΅Π² ΠΈ ΠΏΡΠΈ ΡΡΠΎΠΌ ΠΎΠ½ΠΈ Π½Π°ΡΡΠΎΠ»ΡΠΊΠΎ ΠΆΠ΅ ΠΊΡΠ΅ΠΏΠΊΠΈΠ΅.
Π’Π°ΠΊ ΡΡΠΎ ΠΈΠ»ΠΈ Π½Π΅Ρ, ΠΌΡ ΡΠ²ΠΈΠ΄ΠΈΠΌ ΡΠΎΠ²ΡΠ΅ΠΌ ΡΠΊΠΎΡΠΎ, ΠΊΠΎΠ³Π΄Π° ΡΡΠΈ Π΄ΠΈΡΠΊΠΈ ΠΏΡΠΎΡΠ΅ΡΡΠΈΡΡΠ΅Ρ ΠΊΡΠΎ-ΡΠΎ ΠΈΠ· Π½Π΅Π·Π°Π²ΠΈΡΠΈΠΌΡΡ
ΡΠΊΡΠΏΠ΅ΡΡΠΎΠ²! ΠΠΎ ΡΠ°ΠΌΠΎΠ΅ ΠΈΠ½ΡΠ΅ΡΠ΅ΡΠ½ΠΎΠ΅ ΠΡ ΡΠ·Π½Π°Π΅ΡΠ΅ Π½Π°ΡΠΈΠ½Π°Ρ Ρ ΡΡΠΎΠΉ ΡΡΡΠΎΡΠΊΠΈ, Π²Π΅Π΄Ρ ΠΏΠΎ ΡΠ»ΠΎΠ²Π°ΠΌ ΡΠ°Π·ΡΠ°Π±ΠΎΡΡΠΈΠΊΠΎΠ² ΡΠ°ΠΊΠΈΠ΅ Π΄ΠΈΡΠΊΠΈ ΠΏΠΎΠ·Π²ΠΎΠ»ΡΡ Π½Π° 2-4% ΡΠ½ΠΈΠ·ΠΈΡΡ ΡΠ°ΡΡ
ΠΎΠ΄ ΡΠΎΠΏΠ»ΠΈΠ²Π°, Π° ΡΠ°ΠΊΠΆΠ΅ ΡΠ»ΡΡΡΠΈΡΡ Π°ΡΡΠΎΠ΄ΠΈΠ½Π°ΠΌΠΈΡΠ΅ΡΠΊΠΈΠ΅ ΡΠ²ΠΎΠΉΡΡΠ²Π° Π°Π²ΡΠΎΠΌΠΎΠ±ΠΈΠ»Ρ Π½Π° ΡΠ΅Π»ΡΡ
5%. ΠΡΡ ΡΡΠΎ Π΄ΠΎΡΡΠΈΠ³Π°Π΅ΡΡΡ Π±Π»Π°Π³ΠΎΠ΄Π°ΡΡ ΡΠΎΠΌΡ, ΡΡΠΎ ΠΏΡΠΈ ΠΈΠ·Π³ΠΎΡΠΎΠ²Π»Π΅Π½ΠΈΠΈ ΡΡΠΈΡ
ΠΊΠΎΠ»ΡΡ ΠΏΡΠΎΠΈΠ·Π²ΠΎΠ΄ΠΈΡΠ΅Π»Ρ ΠΈΡΠΏΠΎΠ»ΡΠ·ΠΎΠ²Π°Π» Π½Π°ΡΠ°Π±ΠΎΡΠΊΠΈ ΡΠΏΠ΅ΡΠΈΠ°Π»ΠΈΡΡΠΎΠ² NASA.
Carbon Revolution Π΄Π΅Π»Π°Π΅Ρ Π°ΠΊΡΠ΅Π½Ρ Π½Π° ΡΠΎΠΌ, ΡΡΠΎ ΡΡΠΈ Π΄ΠΈΡΠΊΠΈ Π²ΡΠΏΠΎΠ»Π½Π΅Π½Ρ ΠΏΠΎ Π²ΡΠ΅ΠΌ ΡΡΠ΅Π±ΠΎΠ²Π°Π½ΠΈΡΠΌ, ΠΊΠΎΡΠΎΡΡΠ΅ ΠΏΡΠΎΡ
ΠΎΠ΄ΡΡ OEM Π΄ΠΈΡΠΊΠΈ, Π° ΡΠ°ΠΊΠΆΠ΅ ΠΏΡΠΎΡΠ»ΠΈ ΡΠ΅ΡΡΠΈΡΠΈΠΊΠ°ΡΠΈΡ ΠΏΠΎ ΡΠ°ΠΊΠΈΠΌ ΡΡΠ°Π½Π΄Π°ΡΡΠ°ΠΌ ΠΊΠ°ΠΊ SAE 2530,OEM AK-LH 08 ΠΈ TUV German Aftermarket. ΠΠ·Π½Π°ΡΠ°Π»ΡΠ½ΠΎ ΠΊΠ°ΡΠ±ΠΎΠ½ΠΎΠ²ΡΠ΅ Π΄ΠΈΡΠΊΠΈ CR9 Π±ΡΠ΄ΡΡ Π΄ΠΎΡΡΡΠΏΠ½Ρ Π² Π΄Π²ΡΡ
ΡΠ°Π·ΠΌΠ΅ΡΠ°Ρ
-19×8.5 ΠΈ 19×12 ΠΈ ΠΊΠ°ΠΊ Π²ΠΈΠ΄Π½ΠΎ ΠΏΠΎ ΡΠΎΡΠΎ, ΠΈΠ΄Π΅Π°Π»ΡΠ½ΠΎ ΠΏΠΎΠ΄Ρ
ΠΎΠ΄ΡΡ Π΄Π»Ρ Porsche 911 GT3 RS, Π° ΡΠ°ΠΊΠΆΠ΅ McLaren MP4-12C.
ΠΠ·-Π·Π° ΡΠ°Π·Π½ΠΈΡΡ Π² ΡΠΈΡΠΈΠ½Π΅ ΡΡΡΠΏΠΈΡΡ, ΠΏΠ΅ΡΠ΅Π΄Π½ΠΈΠ΅ Π΄ΠΈΡΠΊΠΈ Π²Π΅ΡΡΡ Π²ΡΠ΅Π³ΠΎ 7 ΠΊΠ³, Π° Π·Π°Π΄Π½ΠΈΠ΅ 8.2 ΠΊΠ³! Π§Π΅ΡΠ΅Π· Π½Π΅ΠΊΠΎΡΠΎΡΠΎΠ΅ Π²ΡΠ΅ΠΌΡ ΠΏΡΠΎΠΈΠ·Π²ΠΎΠ΄ΠΈΡΠ΅Π»Ρ ΠΏΠΎΠΎΠ±Π΅ΡΠ°Π» Π²ΡΠΏΡΡΡΠΈΡΡ ΡΠ΅Π»ΡΡ ΡΠ°Π·ΠΌΠ΅ΡΠ½ΡΡ Π»ΠΈΠ½Π΅ΠΉΠΊΡ CR9.
ΠΡΡΠΎΡΠ½ΠΈΠΊ: carscoop.blogspot.com, www.autofaq.com.ua
ΠΠ²ΡΠΎΡΡΠΊΠΈΠΉ ΠΏΠΎΡΡ

ΠΠΎΠ½ΡΠ°Π²ΠΈΠ»ΡΡ ΠΏΠΎΡΡ? ΠΠΎΠ΄Π΄Π΅ΡΠΆΠΈ Π€ΠΈΡΠΊΠΈ, Π½Π°ΠΆΠΌΠΈ:
ΠΠΎΠ²ΠΎΡΡΠΈ ΠΏΠ°ΡΡΠ½ΡΡΠΎΠ²

ΠΠ°ΠΊ Π²Π΅ΡΠ½ΡΡΡΡΡ Π² ΡΠ΅ΠΆΠΈΠΌ ΠΏΠΎΡΠ»Π΅ Π½ΠΎΠ²ΠΎΠ³ΠΎΠ΄Π½ΠΈΡ ΠΏΡΠ°Π·Π΄Π½ΠΈΠΊΠΎΠ²

ΠΠ΅Π½ΠΈΡΡΠ±Π° Π³ΠΎΠ΄Π°. Π’ΠΎΠΏ Π·Π²Π΅Π·Π΄Π½ΡΡ ΡΠ²Π°Π΄Π΅Π±-2019 (16 ΡΠΎΡΠΎ+Π²ΠΈΠ΄Π΅ΠΎ)
fishki.net
Porsche ΡΠΎΠ·Π΄Π°Π»Π° ΠΏΠΎΠ»Π½ΠΎΡΡΡΡ ΠΊΠ°ΡΠ±ΠΎΠ½ΠΎΠ²ΡΠΉ ΠΊΠΎΠ»Π΅ΡΠ½ΡΠΉ Π΄ΠΈΡΠΊ
Porsche
ΠΠ°ΡΠ±ΠΎΠ½ΠΎΠ²ΡΠΉ ΠΊΠΎΠ»Π΅ΡΠ½ΡΠΉ Π΄ΠΈΡΠΊ
ΠΠ΅ΠΌΠ΅ΡΠΊΠ°Ρ ΠΊΠΎΠΌΠΏΠ°Π½ΠΈΡ Porsche ΡΠ°Π·ΡΠ°Π±ΠΎΡΠ°Π»Π° Π½ΠΎΠ²ΡΠ΅ ΠΊΠΎΠ»Π΅ΡΠ½ΡΠ΅ Π΄ΠΈΡΠΊΠΈ, ΠΏΠΎΠ»Π½ΠΎΡΡΡΡ Π²ΡΠΏΠΎΠ»Π½Π΅Π½Π½ΡΠ΅ ΠΈΠ· ΡΠ³Π»Π΅ΠΏΠ»Π°ΡΡΠΈΠΊΠ°. Π‘ΠΎΠ³Π»Π°ΡΠ½ΠΎ ΡΠΎΠΎΠ±ΡΠ΅Π½ΠΈΡ ΠΊΠΎΠΌΠΏΠ°Π½ΠΈΠΈ, Π½ΠΎΠ²ΡΠ΅ Π΄ΠΈΡΠΊΠΈ ΠΈΠ·Π³ΠΎΡΠ°Π²Π»ΠΈΠ²Π°ΡΡΡΡ Π½Π° ΡΠΏΠ΅ΡΠΈΠ°Π»ΡΠ½ΠΎΠΌ ΡΡΠ°Π½ΠΊΠ΅ Π΄ΠΈΠ°ΠΌΠ΅ΡΡΠΎΠΌ ΠΎΠΊΠΎΠ»ΠΎ Π΄Π΅Π²ΡΡΠΈ ΠΌΠ΅ΡΡΠΎΠ², ΠΊΠΎΡΠΎΡΡΠΉ Π±ΡΠΊΠ²Π°Π»ΡΠ½ΠΎ ΠΏΠ»Π΅ΡΠ΅Ρ ΠΈΡ ΠΈΠ· ΡΠ³Π»Π΅Π²ΠΎΠ»ΠΎΠΊΠ½Π°. ΠΡΠΈΠΌΠ΅Π½Π΅Π½ΠΈΠ΅ ΡΡΠΎΠ³ΠΎ ΠΌΠ°ΡΠ΅ΡΠΈΠ°Π»Π° ΠΏΠΎΠ·Π²ΠΎΠ»ΠΈΠ»ΠΎ Π½Π° 20 ΠΏΡΠΎΡΠ΅Π½ΡΠΎΠ² ΡΠ½ΠΈΠ·ΠΈΡΡ ΠΌΠ°ΡΡΡ ΠΊΠΎΠ»Π΅Ρ.
Π£Π³Π»Π΅ΠΏΠ»Π°ΡΡΠΈΠΊ ΡΠΆΠ΅ Π΄ΠΎΠ²ΠΎΠ»ΡΠ½ΠΎ Π΄Π°Π²Π½ΠΎ ΠΈΡΠΏΠΎΠ»ΡΠ·ΡΠ΅ΡΡΡ ΠΏΡΠΈ ΠΈΠ·Π³ΠΎΡΠΎΠ²Π»Π΅Π½ΠΈΠΈ Π°Π²ΡΠΎΠΌΠΎΠ±ΠΈΠ»Π΅ΠΉ. ΠΠ°ΠΈΠ±ΠΎΠ»Π΅Π΅ ΡΠΈΡΠΎΠΊΠΎ ΡΡΠΎΡ ΠΌΠ°ΡΠ΅ΡΠΈΠ°Π» ΠΏΡΠΈΠΌΠ΅Π½ΡΡΡ ΠΏΡΠΈ ΠΏΡΠΎΠΈΠ·Π²ΠΎΠ΄ΡΡΠ²Π΅ ΡΠΏΠΎΡΡΠΈΠ²Π½ΡΡ ΠΌΠ°ΡΠΈΠ½. ΠΠ΅Π»ΠΎ Π² ΡΠΎΠΌ, ΡΡΠΎ ΡΠ³Π»Π΅ΠΏΠ»Π°ΡΡΠΈΠΊ ΠΏΠΎ ΡΠ²ΠΎΠ΅ΠΉ ΠΏΡΠΎΡΠ½ΠΎΡΡΠΈ ΡΠΎΠΎΡΠ²Π΅ΡΡΡΠ²ΡΠ΅Ρ, Π° ΠΈΠ½ΠΎΠ³Π΄Π° ΠΈ ΠΏΡΠ΅Π²ΠΎΡΡ ΠΎΠ΄ΠΈΡ ΡΡΠ°Π½Π΄Π°ΡΡΠ½ΡΠ΅ Π°Π»ΡΠΌΠΈΠ½ΠΈΠ΅Π²ΡΠ΅ ΡΠΏΠ»Π°Π²Ρ, Π½ΠΎ ΠΏΡΠΈ ΡΡΠΎΠΌ ΠΎΠ½ ΡΡΡΠ΅ΡΡΠ²Π΅Π½Π½ΠΎ Π»Π΅Π³ΡΠ΅.
ΠΠΎ ΡΠΈΡ ΠΏΠΎΡ ΠΊΠΎΠ»Π΅ΡΠ½ΡΠ΅ Π΄ΠΈΡΠΊΠΈ Π΄Π»Ρ Π°Π²ΡΠΎΠΌΠΎΠ±ΠΈΠ»Π΅ΠΉ ΡΡΠ°Π΄ΠΈΡΠΈΠΎΠ½Π½ΠΎ ΠΈΠ·Π³ΠΎΡΠ°Π²Π»ΠΈΠ²Π°Π»ΠΈΡΡ ΠΈΠ· Π°Π»ΡΠΌΠΈΠ½ΠΈΠ΅Π²ΠΎΠ³ΠΎ ΠΈΠ»ΠΈ ΠΌΠ°Π³Π½ΠΈΠ΅Π²ΠΎΠ³ΠΎ ΡΠΏΠ»Π°Π²Π°. ΠΡΠΈ ΡΡΠΎΠΌ Π½Π΅ΠΊΠΎΡΠΎΡΡΠ΅ ΠΏΡΠΎΠΈΠ·Π²ΠΎΠ΄ΠΈΡΠ΅Π»ΠΈ ΡΠΆΠ΅ ΠΎΠ±ΡΡΠ²ΠΈΠ»ΠΈ ΠΎ Π½Π°ΠΌΠ΅ΡΠ΅Π½ΠΈΠΈ Π½Π°ΡΠ°ΡΡ ΠΈΠ·Π³ΠΎΡΠ°Π²Π»ΠΈΠ²Π°ΡΡ ΡΠ³Π»Π΅ΠΏΠ»Π°ΡΡΠΈΠΊΠΎΠ²ΡΠ΅ Π΄ΠΈΡΠΊΠΈ Π΄Π»Ρ ΡΠ²ΠΎΠΈΡ ΡΠΏΠΎΡΡΠΊΠ°ΡΠΎΠ². Π ΠΈΡ ΡΠΈΡΠ»Π΅, Ford ΠΈ BAC, ΠΊΠΎΡΠΎΡΡΠ΅ ΠΏΠ»Π°Π½ΠΈΡΡΡΡ ΡΠ΅ΡΠΈΠΉΠ½ΠΎ ΠΏΡΠΎΠΈΠ·Π²ΠΎΠ΄ΠΈΡΡ Π΄ΠΈΡΠΊΠΈ ΠΈΠ· ΠΏΡΠ΅ΠΏΡΠ΅Π³ΠΎΠ².
Π‘ΡΠ°Π½ΠΎΠΊ Π΄Π»Ρ ΠΏΠ»Π΅ΡΠ΅Π½ΠΈΡ ΡΠ³Π»Π΅Π²ΠΎΠ»ΠΎΠΊΠΎΠ½Π½ΠΎΠΉ ΠΎΡΠ½ΠΎΠ²Ρ ΠΊΠΎΠ»Π΅ΡΠ½ΠΎΠ³ΠΎ Π΄ΠΈΡΠΊΠ°
Porsche
ΠΡΠ½ΠΎΠ²Π° ΠΊΠΎΠ»Π΅ΡΠ½ΠΎΠ³ΠΎ Π΄ΠΈΡΠΊΠ° ΠΈΠ· ΠΏΠ»Π΅ΡΠ΅Π½ΠΎΠ³ΠΎ ΡΠ³Π»Π΅Π²ΠΎΠ»ΠΎΠΊΠ½Π°
Porsche
ΠΠ°ΡΡΡΠΊΠΈ Ρ ΡΠ³Π»Π΅Π²ΠΎΠ»ΠΎΠΊΠ½ΠΎΠΌ Π½Π° ΡΡΠ°Π½ΠΊΠ΅
Porsche
ΠΡΠΏΡΡΠ°Π½ΠΈΡ ΠΊΠ°ΡΠ±ΠΎΠ½ΠΎΠ²ΠΎΠ³ΠΎ ΠΊΠΎΠ»Π΅ΡΠ½ΠΎΠ³ΠΎ Π΄ΠΈΡΠΊΠ°
Porsche
Π‘ΠΎΠ³Π»Π°ΡΠ½ΠΎ Π·Π°ΡΠ²Π»Π΅Π½ΠΈΡ Porsche, Π΅Π΅ ΠΊΠΎΠ»Π΅ΡΠ½ΡΠ΅ Π΄ΠΈΡΠΊΠΈ ΡΠ²Π»ΡΡΡΡΡ ΠΏΠ΅ΡΠ²ΡΠΌΠΈ Π² ΠΌΠΈΡΠ΅, ΠΈΠ·Π³ΠΎΡΠΎΠ²Π»Π΅Π½Π½ΡΠΌΠΈ ΠΈΠ· ΡΠ³Π»Π΅Π²ΠΎΠ»ΠΎΠΊΠ½Π° ΠΌΠ΅ΡΠΎΠ΄ΠΎΠΌ ΠΏΠ»Π΅ΡΠ΅Π½ΠΈΡ. Π’Π°ΠΊΠΎΠΉ ΡΠΏΠΎΡΠΎΠ± ΠΈΠ·Π³ΠΎΡΠΎΠ²Π»Π΅Π½ΠΈΡ ΠΏΠΎΠ·Π²ΠΎΠ»ΡΠ΅Ρ Π΄ΠΎΠ±ΠΈΡΡΡΡ Π±ΠΎΠ»ΡΡΠ΅ΠΉ ΠΏΡΠΎΡΠ½ΠΎΡΡΠΈ ΡΠ³Π»Π΅ΠΏΠ»Π°ΡΡΠΈΠΊΠ°, Π΅ΡΠ»ΠΈ Π½ΠΈΡΡ ΡΠΊΠ»Π°Π΄ΡΠ²Π°Π΅ΡΡΡ Π±Π΅Π· ΡΠΈΠ»ΡΠ½ΡΡ ΠΏΠ΅ΡΠ΅Π³ΠΈΠ±ΠΎΠ² ΠΈ Π½Π΅ ΠΏΠΎΠ²ΡΠ΅ΠΆΠ΄Π°Π΅ΡΡΡ.ΠΠΎ Π΄Π°Π½Π½ΡΠΌ Porsche, Π½ΠΎΠ²ΡΠ΅ ΠΊΠ°ΡΠ±ΠΎΠ½ΠΎΠ²ΡΠ΅ Π΄ΠΈΡΠΊΠΈ ΠΏΠΎΠ»ΡΡΠΈΠ»ΠΈ Π½Π° 20 ΠΏΡΠΎΡΠ΅Π½ΡΠΎΠ² ΠΏΡΠΎΡΠ½Π΅Π΅ ΡΡΠ°Π½Π΄Π°ΡΡΠ½ΡΡ Π»Π΅Π³ΠΊΠΎΡΠΏΠ»Π°Π²Π½ΡΡ ΠΊΠΎΠ»Π΅Ρ. ΠΡΠΈ ΡΡΠΎΠΌ ΠΌΠ°ΡΡΠ° ΠΎΠ΄Π½ΠΎΠ³ΠΎ Π΄ΠΈΡΠΊΠ° ΠΎΠΊΠ°Π·Π°Π»Π°ΡΡ Π½Π° 2,1 ΠΊΠΈΠ»ΠΎΠ³ΡΠ°ΠΌΠΌΠ° ΠΌΠ΅Π½ΡΡΠ΅. ΠΠ°ΠΊ ΠΎΠΆΠΈΠ΄Π°Π΅ΡΡΡ, ΠΊΠ°ΡΠ±ΠΎΠ½ΠΎΠ²ΡΠ΅ Π΄ΠΈΡΠΊΠΈ Π±ΡΠ΄ΡΡ ΠΏΡΠ΅Π΄Π»Π°Π³Π°ΡΡΡΡ Π² ΠΊΠ°ΡΠ΅ΡΡΠ²Π΅ ΠΎΠΏΡΠΈΠΈ ΠΊ Π°Π²ΡΠΎΠΌΠΎΠ±ΠΈΠ»ΡΠΌ 911 Turbo S Exclusive Series Ρ 2018 Π³ΠΎΠ΄Π°.
Π 2015 Π³ΠΎΠ΄Ρ ΠΊΠΎΠΌΠΏΠ°Π½ΠΈΡ Ford Π·Π°ΠΏΠ°ΡΠ΅Π½ΡΠΎΠ²Π°Π»Π° ΡΠ½ΠΈΡΠΈΠΊΠ» ΠΈΠ· Π°Π²ΡΠΎΠΌΠΎΠ±ΠΈΠ»ΡΠ½ΠΎΠ³ΠΎ ΠΊΠΎΠ»Π΅ΡΠ°, ΠΊΠΎΡΠΎΡΠΎΠ΅ ΠΌΠΎΠΆΠ½ΠΎ ΡΠ½ΠΈΠΌΠ°ΡΡ Ρ ΠΏΡΠΈΠΏΠ°ΡΠΊΠΎΠ²Π°Π½Π½ΠΎΠΉ ΠΌΠ°ΡΠΈΠ½Ρ. Π‘ΠΎΠ³Π»Π°ΡΠ½ΠΎ ΠΏΠ°ΡΠ΅Π½ΡΡ, Π² ΠΊΠΎΠ»Π΅ΡΠΎ ΠΏΡΠ΅Π΄ΠΏΠΎΠ»Π°Π³Π°Π΅ΡΡΡ Π²ΡΡΡΠΎΠΈΡΡ ΡΠ»Π΅ΠΊΡΡΠΎΠ΄Π²ΠΈΠ³Π°ΡΠ΅Π»Ρ, ΡΡΠΊΠΎΡΡΠΊΠΈ ΡΠΏΡΠ°Π²Π»Π΅Π½ΠΈΡ, ΠΊΠ°ΡΠΊΠ°Ρ, Π±Π°ΡΠ°ΡΠ΅Ρ ΠΈ ΠΏΠΎΠ΄Π½ΠΎΠΆΠΊΠΈ.
Π ΠΏΡΠΈΠΏΠ°ΡΠΊΠΎΠ²Π°Π½Π½ΠΎΠΌ Π°Π²ΡΠΎΠΌΠΎΠ±ΠΈΠ»Π΅ Π½ΡΠΆΠ½ΠΎ Π±ΡΠ΄Π΅Ρ Π²ΠΊΠ»ΡΡΠΈΡΡ ΡΠΈΡΡΠ΅ΠΌΡ Π°Π²ΡΠΎΠΌΠ°ΡΠΈΡΠ΅ΡΠΊΠΎΠ³ΠΎ Π΄ΠΎΠΌΠΊΡΠ°ΡΠ°, ΠΊΠΎΡΠΎΡΠ°Ρ ΠΏΡΠΈΠΏΠΎΠ΄Π½ΠΈΠΌΠ΅Ρ ΠΌΠ°ΡΠΈΠ½Ρ. ΠΠΎΡΠ»Π΅ ΡΡΠΎΠ³ΠΎ Π²Π»Π°Π΄Π΅Π»Π΅Ρ ΡΠΌΠΎΠΆΠ΅Ρ ΡΠ½ΡΡΡ ΠΊΠΎΠ»Π΅ΡΠΎ ΠΈ ΡΠ°Π·Π»ΠΎΠΆΠΈΡΡ ΠΊΠ°ΡΠΊΠ°Ρ ΡΠ½ΠΈΡΠΈΠΊΠ»Π°.
ΠΠ°ΡΠΈΠ»ΠΈΠΉ Π‘ΡΡΡΠ²
nplus1.ru
ΠΠΎΠ»Π΅ΡΠ½ΡΠ΅ Π΄ΠΈΡΠΊΠΈ ΠΈΠ· ΠΊΠ°ΡΠ±ΠΎΠ½Π° | AUTO-GL.ru
ΠΡΠΏΠΎΠ»ΡΠ·ΠΎΠ²Π°ΡΡ Π»Π΅Π³ΠΊΠΎΡΠΏΠ»Π°Π²Π½ΡΠ΅ ΠΊΠΎΠ»Π΅ΡΠ½ΡΠ΅ Π΄ΠΈΡΠΊΠΈ Π² Π°Π²ΡΠΎΠΌΠΎΠ±ΠΈΠ»ΡΠ½ΠΎΠΉ ΠΏΡΠΎΠΌΡΡΠ»Π΅Π½Π½ΠΎΡΡΠΈ Π½Π°ΡΠ°Π»ΠΈ Π½Π΅ ΡΠ°ΠΊ Π΄Π°Π²Π½ΠΎ. ΠΠΎΠ»Π³ΠΎΠ΅ Π²ΡΠ΅ΠΌΡ Π°Π»ΡΠΌΠΈΠ½ΠΈΠ΅Π²ΡΠ΅ ΠΈ ΠΌΠ°Π³Π½ΠΈΠ΅Π²ΡΠ΅ Π΄ΠΈΡΠΊΠΈ Π±ΡΠ»ΠΈ ΡΠ΄Π΅Π»ΠΎΠΌ Π°Π²ΠΈΠ°ΡΠΈΠΎΠ½Π½ΠΎΠΉ ΡΠ΅Ρ Π½ΠΈΠΊΠΈ. ΠΠΎΠ½ΡΡΠ½ΠΎ, ΡΡΠΎ Π΄Π΅ΡΠ°Π»Ρ, ΠΈΠ·Π³ΠΎΡΠΎΠ²Π»Π΅Π½Π½Π°Ρ ΠΈΠ· Π°Π»ΡΠΌΠΈΠ½ΠΈΡ, Π½Π΅ ΠΌΠΎΠΆΠ΅Ρ ΠΎΠ±Π»Π°Π΄Π°ΡΡ Ρ ΠΎΡΠΎΡΠΈΠΌ Π·Π°ΠΏΠ°ΡΠΎΠΌ ΠΏΡΠΎΡΠ½ΠΎΡΡΠΈ, ΡΠΎΠ³Π΄Π° ΠΊΠ°ΠΊ ΠΌΠ°Π³Π½ΠΈΠ΅Π²ΡΠ΅ ΡΠΏΠ»Π°Π²Ρ ΠΎΡΡΠ°ΡΡΡΡ ΡΠ»ΠΈΡΠΊΠΎΠΌ Π΄ΠΎΡΠΎΠ³ΠΈΠΌΠΈ. Π‘Π΅ΠΉΡΠ°Ρ, Π±Π»Π°Π³ΠΎΠ΄Π°ΡΡ ΡΠ°Π·Π²ΠΈΡΠΈΡ ΡΠ΅Ρ Π½ΠΎΠ»ΠΎΠ³ΠΈΠΉ, ΠΏΠΎΡΠ²ΠΈΠ»Π°ΡΡ Π²ΠΎΠ·ΠΌΠΎΠΆΠ½ΠΎΡΡΡ ΠΈΠ·Π³ΠΎΡΠΎΠ²Π»ΡΡΡ Π»Π΅Π³ΠΊΠΈΠ΅ ΠΈ ΠΏΡΠΎΡΠ½ΡΠ΅ Π΄Π΅ΡΠ°Π»ΠΈ ΠΈΠ· ΠΌΠ°ΡΠ΅ΡΠΈΠ°Π»ΠΎΠ² Π½ΠΎΠ²ΠΎΠ³ΠΎ ΠΏΠΎΠΊΠΎΠ»Π΅Π½ΠΈΡ, ΡΠ²Π»ΡΡΡΠΈΡ ΡΡ ΠΊΠΎΠΌΠΏΠΎΠ·ΠΈΡΠ°ΠΌΠΈ. Π‘Π°ΠΌΡΠΌ ΠΏΠ΅ΡΡΠΏΠ΅ΠΊΡΠΈΠ²Π½ΡΠΌ ΠΈΠ· ΡΠ°ΠΊΠΈΡ ΠΌΠ°ΡΠ΅ΡΠΈΠ°Π»ΠΎΠ² ΡΡΠΈΡΠ°Π΅ΡΡΡ ΠΊΠ°ΡΠ±ΠΎΠ½.
ΠΠΎΠΌΠΏΠ°Π½ΠΈΡ Carbon Revolution, Π±Π°Π·ΠΈΡΡΡΡΠ°ΡΡΡ Π² ΠΠ²ΡΡΡΠ°Π»ΠΈΠΈ, Π½Π΅Π΄Π°Π²Π½ΠΎ ΠΏΡΠ΅Π΄ΡΡΠ°Π²ΠΈΠ»Π° Π½ΠΎΠ²ΡΠΉ ΠΏΡΠΎΠ΄ΡΠΊΡ β Π°Π²ΡΠΎΠΌΠΎΠ±ΠΈΠ»ΡΠ½ΡΠ΅ ΠΊΠΎΠ»Π΅ΡΠ½ΡΠ΅ Π΄ΠΈΡΠΊΠΈ, Π²ΡΠΏΠΎΠ»Π½Π΅Π½Π½ΡΠ΅ ΠΈΠ· ΠΊΠ°ΡΠ±ΠΎΠ½Π°. ΠΡΠΌΠ΅ΡΠΈΠΌ, ΡΡΠΎ ΠΊΠ°ΠΆΠ΄ΡΠΉ ΡΠ°ΠΊΠΎΠΉ Π΄ΠΈΡΠΊ ΡΠ²Π»ΡΠ΅ΡΡΡ ΠΌΠΎΠ½ΠΎΠ»ΠΈΡΠ½ΠΎΠΉ Π΄Π΅ΡΠ°Π»ΡΡ, Π° Π½Π΅ ΡΠΎΡΡΠ°Π²Π½ΠΎΠΉ ΠΊΠΎΠ½ΡΡΡΡΠΊΡΠΈΠ΅ΠΉ, ΡΡΠΎ ΠΎΠ±Π΅ΡΠΏΠ΅ΡΠΈΡ Π°Π²ΡΠΎΠ²Π»Π°Π΄Π΅Π»ΡΡΡ Π½Π΅ΠΎΠ±Ρ ΠΎΠ΄ΠΈΠΌΡΡ Π±Π΅Π·ΠΎΠΏΠ°ΡΠ½ΠΎΡΡΡ. ΠΠ»Π°Π²Π½ΠΎΠ΅, ΡΡΠΎ ΠΊΠ°ΡΠ±ΠΎΠ½ΠΎΠ²ΡΠ΅ Π΄ΠΈΡΠΊΠΈ ΠΏΠΎΠ»ΡΡΠ°ΡΡΡΡ Π½Π° 40-50 ΠΏΡΠΎΡΠ΅Π½ΡΠΎΠ² Π»Π΅Π³ΡΠ΅, ΡΠ΅ΠΌ ΠΈΡ Π°Π½Π°Π»ΠΎΠ³ΠΈ ΠΈΠ· Π±ΠΎΠ»Π΅Π΅ Π΄ΠΎΡΡΡΠΏΠ½ΡΡ ΠΌΠ°ΡΠ΅ΡΠΈΠ°Π»ΠΎΠ². ΠΡΠΈ ΡΠΊΡΠΏΠ»ΡΠ°ΡΠ°ΡΠΈΠΈ ΠΊΠ°ΡΠ±ΠΎΠ½ΠΎΠ²ΡΡ ΠΊΠΎΠ»Π΅ΡΠ½ΡΡ Π΄ΠΈΡΠΊΠΎΠ² ΡΠ°ΡΡ ΠΎΠ΄ ΡΠΎΠΏΠ»ΠΈΠ²Π° ΡΠ½ΠΈΠΆΠ°Π΅ΡΡΡ Π½Π° 2-4% (ΡΠΎΠ³Π»Π°ΡΠ½ΠΎ ΠΏΠΎΠ΄ΡΡΠ΅ΡΠ°ΠΌ Carbon Revolution).
ΠΠ°ΡΡΠΎΡΡΠ°Ρ ΡΠ΅Ρ Π½ΠΎΠ»ΠΎΠ³ΠΈΡΠ΅ΡΠΊΠ°Ρ ΡΠ΅Π²ΠΎΠ»ΡΡΠΈΡ
Π Π°Π²ΡΡΡΠ°Π»ΠΈΠΉΡΠΊΠΎΠΉ ΠΊΠΎΠΌΠΏΠ°Π½ΠΈΠΈ ΡΡΠΈΡΠ°ΡΡ, ΡΡΠΎ Π΅ΡΠ»ΠΈ Π΄ΠΈΠ·Π°ΠΉΠ½ Π΄ΠΈΡΠΊΠΎΠ² ΡΠ°Π·ΡΠ°Π±Π°ΡΡΠ²Π°ΡΡ ΡΠΎΠ²ΠΌΠ΅ΡΡΠ½ΠΎ Ρ Π°Π²ΡΠΎΠΏΡΠΎΠΈΠ·Π²ΠΎΠ΄ΠΈΡΠ΅Π»Π΅ΠΌ, ΡΠΎ ΠΌΠΎΠΆΠ½ΠΎ ΠΏΠΎΠ»ΡΡΠΈΡΡ Π²ΡΠΈΠ³ΡΡΡ Π² ΡΠΊΠΎΠ½ΠΎΠΌΠΈΠΈ ΡΠΎΠΏΠ»ΠΈΠ²Π°, ΡΠ°Π²Π½ΡΠΉ 6-ΡΠΈ ΠΏΡΠΎΡΠ΅Π½ΡΠ°ΠΌ. ΠΡ Π° ΡΠ΅ ΠΊΠ°ΡΠ±ΠΎΠ½ΠΎΠ²ΡΠ΅ Π΄ΠΈΡΠΊΠΈ, ΠΊΠΎΡΠΎΡΡΠ΅ ΡΡΡΠ΅ΡΡΠ²ΡΡΡ ΡΠ΅ΠΉΡΠ°Ρ, Π²ΡΠΏΡΡΠΊΠ°ΡΡΡΡ Π² Π΄Π²ΡΡ ΡΠΈΠΏΠΎΡΠ°Π·ΠΌΠ΅ΡΠ°Ρ β 19Γ8,5 (R19 W8,5) ΠΈ 19Γ12. ΠΠ°Π»Ρ, ΡΡΠΎ ΠΏΡΠΎΠ΄ΡΠΊΡΠΈΡ Carbon Revolution Π½Π΅ ΡΠΎΠ²ΠΌΠ΅ΡΡΠΈΠΌΠ° Ρ ΠΊΠΎΠ½ΡΡΡΡΠΊΡΠΈΠ΅ΠΉ Π°Π²ΡΠΎΠΌΠΎΠ±ΠΈΠ»Π΅ΠΉ ΠΠΠ. ΠΠ΅Ρ ΠΊΠ°ΡΠ±ΠΎΠ½ΠΎΠ²ΡΡ Π΄ΠΈΡΠΊΠΎΠ², Π½Π΅ΡΠΌΠΎΡΡΡ Π½Π° Π·Π½Π°ΡΠΈΡΠ΅Π»ΡΠ½ΡΠΉ Π΄ΠΈΠ°ΠΌΠ΅ΡΡ, ΡΠΎΡΡΠ°Π²Π»ΡΠ΅Ρ 6,8 ΠΊΠ³ Π΄Π»Ρ ΠΏΠ΅ΡΠ²ΠΎΠΉ ΠΌΠΎΠ΄Π΅Π»ΠΈ ΠΈ 7,9 ΠΊΠ³ Π΄Π»Ρ Π²ΡΠΎΡΠΎΠΉ.
ΠΡΠ΅Π΄ΡΡΠ°Π²ΠΈΡΠ΅Π»ΠΈ Carbon Revolution Π½Π΅ ΡΠΊΡΡΠ²Π°ΡΡ, ΡΡΠΎ ΠΈΡ ΠΏΡΠΎΠ΄ΡΠΊΡΠΈΡ ΡΠΎΠ·Π΄Π°Π²Π°Π»Π°ΡΡ ΠΈΠ· ΡΠ°ΡΡΠ΅ΡΠ° Π½Π° ΡΠΎ, ΡΡΠΎ Π±ΡΠ΄Π΅Ρ ΠΈΡΠΏΠΎΠ»ΡΠ·ΠΎΠ²Π°ΡΡΡΡ ΡΠΎΠ²ΠΌΠ΅ΡΡΠ½ΠΎ Ρ ΡΠΎΠ΄ΡΡΠ΅ΡΠΎΠΌ Porsche 911. ΠΠΈΡΠΊΠΈ, Π²ΡΠΏΡΡΠΊΠ°Π΅ΠΌΡΠ΅ ΡΡΠΎΠΉ ΠΊΠΎΠΌΠΏΠ°Π½ΠΈΠ΅ΠΉ, ΠΏΠΎΠ΄Ρ ΠΎΠ΄ΡΡ Π΄Π»Ρ ΡΡΡΠ°Π½ΠΎΠ²ΠΊΠΈ Π½Π° Π½Π΅ΠΊΠΎΡΠΎΡΡΠ΅ ΠΌΠΎΠ΄Π΅Π»ΠΈ ΡΠΏΠΎΡΡΠΊΠ°ΡΠΎΠ², Π½ΠΎ ΠΈ ΡΠΎΠ»ΡΠΊΠΎ. Π Β«Π³ΡΠ°ΠΆΠ΄Π°Π½ΡΠΊΠΎΠΌΒ» Π°Π²ΡΠΎΠΌΠΎΠ±ΠΈΠ»Π΅ΡΡΡΠΎΠ΅Π½ΠΈΠΈ, ΠΊΠ°ΠΊ ΠΌΡ Π·Π½Π°Π΅ΠΌ, ΡΠΈΠΏΠΎΡΠ°Π·ΠΌΠ΅Ρ R19 ΠΈΡΠΏΠΎΠ»ΡΠ·ΡΠ΅ΡΡΡ ΡΠ΅Π΄ΠΊΠΎ. Π’Π°ΠΊ ΡΡΠΎ, ΠΊΠΎΠ»Π΅ΡΠ½ΡΠ΅ Π΄ΠΈΡΠΊΠΈ ΠΈΠ· ΠΊΠ°ΡΠ±ΠΎΠ½Π° ΡΠ΅ΠΉΡΠ°Ρ ΠΎΡΡΠ°ΡΡΡΡ Π°ΡΡΠΈΠ±ΡΡΠΎΠΌ Π΄ΠΎΡΠΎΠ³ΠΈΡ Π°Π²ΡΠΎΠΌΠ°ΡΠΈΠ½, ΡΠ΅Ρ , ΠΊΠΎΡΠΎΡΡΠ΅ Π½Π΅ ΠΏΡΠ΅Π΄Π½Π°Π·Π½Π°ΡΠ΅Π½Ρ Π΄Π»Ρ Π΅ΠΆΠ΅Π΄Π½Π΅Π²Π½ΡΡ ΠΏΠΎΠ΅Π·Π΄ΠΎΠΊ.
ΠΠ° Π΄ΠΎΡΠΎΠ³Π°Ρ ΠΎΠ±ΡΠ΅Π³ΠΎ ΠΏΠΎΠ»ΡΠ·ΠΎΠ²Π°Π½ΠΈΡ
ΠΠ°ΡΠ±ΠΎΠ½ΠΎΠ²ΡΠ΅ Π΄ΠΈΡΠΊΠΈ, ΠΎ ΠΊΠΎΡΠΎΡΡΡ ΡΠ»Π° ΡΠ΅ΡΡ Π²ΡΡΠ΅, ΠΏΠΎΠΊΠ° ΠΏΡΠΎΡΠ»ΠΈ ΡΠ΅ΡΡΠΈΡΠΈΠΊΠ°ΡΠΈΡ Π½Π΅ Π² ΠΊΠ°ΠΆΠ΄ΠΎΠΉ ΠΈΠ· ΡΡΡΠ°Π½. ΠΠΎ ΡΠΎΠ³Π»Π°ΡΠ½ΠΎ Π²ΡΠ²ΠΎΠ΄Π°ΠΌ ΡΠΊΡΠΏΠ΅ΡΡΠΎΠ², ΠΏΡΠΎΠ΄ΡΠΊΡΠΈΡ Carbon Revolution Π΄Π΅ΠΉΡΡΠ²ΠΈΡΠ΅Π»ΡΠ½ΠΎ ΡΠΎΠΎΡΠ²Π΅ΡΡΡΠ²ΡΡΡ ΡΡΠ°Π½Π΄Π°ΡΡΠ°ΠΌ ΠΈ ΡΡΠ΅Π±ΠΎΠ²Π°Π½ΠΈΡΠΌ, ΠΏΡΠ΅Π΄ΡΡΠ²Π»ΡΠ΅ΠΌΡΠΌ ΠΊ ΠΊΠΎΠ»Π΅ΡΠ½ΡΠΌ Π΄ΠΈΡΠΊΠ°ΠΌ Π΄ΠΎΡΠΎΠΆΠ½ΡΡ Π°Π²ΡΠΎ. ΠΡΠΌΠ΅ΡΠΈΠΌ, ΡΡΠΎ ΡΠ΅ΡΡΠΈΡΠΈΠΊΠ°ΡΠΈΡ ΡΠΆΠ΅ ΠΏΡΠΎΠΉΠ΄Π΅Π½Π° Π² ΠΠ΅ΡΠΌΠ°Π½ΠΈΠΈ, Π° ΡΠ°ΠΊΠΆΠ΅ Π² ΠΠ±ΡΠ΅Π΄ΠΈΠ½Π΅Π½Π½ΡΡ ΠΡΠ°Π±ΡΠΊΠΈΡ ΠΠΌΠΈΡΠ°ΡΠ°Ρ . Π ΠΌΠΎΠΆΠ½ΠΎ Π½Π°Π΄Π΅ΡΡΡΡΡ, ΡΡΠΎ ΡΠ°ΡΡΠΌΠΎΡΡΠ΅Π½Π½Π°Ρ ΡΠ΅Ρ Π½ΠΎΠ»ΠΎΠ³ΠΈΡ ΠΏΠΎΠ»ΡΡΠΈΡ ΡΠ²ΠΎΠ΅ ΡΠ°Π·Π²ΠΈΡΠΈΠ΅ Π² Π±ΡΠ΄ΡΡΠ΅ΠΌ.
auto-gl.ru
ΠΠ°ΠΊ ΠΈΠ·Π³ΠΎΡΠ°Π²Π»ΠΈΠ²Π°ΡΡ ΠΊΠ°ΡΠ±ΠΎΠ½ΠΎΠ²ΡΠ΅ ΡΠΎΡΠΌΠΎΠ·Π½ΡΠ΅ Π΄ΠΈΡΠΊΠΈ
Π’ΠΎΡΠΌΠΎΠ·Π° ΠΏΡΠΈΠ΄ΡΠΌΠ°Π»ΠΈ ΡΡΡΡΡ. Π ΠΊΠ°ΡΠ±ΠΎΠ½ΠΎΠ²ΡΠ΅ ΡΠΎΡΠΌΠΎΠ·Π° β ΡΡΡΡΡ, ΡΠΏΠ΅ΡΠΈΠ°Π»ΡΠ½ΠΎ ΠΎΠ±ΡΡΠ΅Π½Π½ΡΠ΅, ΡΠ³Π»Π΅ΡΠΎΠ΄Π½ΡΠ΅ π
ΠΡΠ΄ΡΡΠΈ, Π½Π° Π΄Π°Π½Π½ΡΠΉ ΠΌΠΎΠΌΠ΅Π½Ρ, Π΅Π΄ΠΈΠ½ΡΡΠ²Π΅Π½Π½ΡΠΌ ΡΡΠ°ΡΡΠ»ΠΈΠ²ΡΠΌ ΠΎΠ±Π»Π°Π΄Π°ΡΠ΅Π»Π΅ΠΌ ΡΠ°ΠΊΠΈΡ ΡΠΎΡΠΌΠΎΠ·ΠΈΠ»ΠΎΠΊ Π² Π ΠΎΡΡΠΈΠΈ, ΡΡΠ²ΡΡΠ²ΡΡ ΡΠΎΡΠΈΠ°Π»ΡΠ½ΡΡ ΠΎΡΠ²Π΅ΡΡΡΠ²Π΅Π½Π½ΠΎΡΡΡ ΠΏΠ΅ΡΠ΅Π΄ ΠΊΠΎΠ»Π»Π΅Π³Π°ΠΌΠΈ ΠΈ ΠΏΡΠΎΡΡΠΎ ΠΎΠ±ΡΠ·Π°Π½ ΡΠ°ΡΠΊΡΡΡΡ Π½ΡΠ°Π½ΡΡ ΡΠΊΡΠΏΠ»ΡΠ°ΡΠ°ΡΠΈΠΈ. Π§ΡΠΎΠ±Ρ ΠΎΡΠΎΠ±ΠΎ Π½Π΅ ΡΠΎΠΌΠΈΡΡ, ΡΡΠ°Π·Ρ ΡΠΊΠ°ΠΆΡ: ΠΏΠΎΡΡΠ°ΡΠ΅Π½Π½ΡΡ Π΄Π΅Π½Π΅Π³ Π½Π΅ ΠΆΠ°Π»ΠΊΠΎ ΠΈ ΡΠ²Π΅ΡΠ΅Π½, ΡΡΠΎ Π²Π΅ΡΡ Π΄Π»Ρ ΡΡΠ΅ΠΊΠ° ΠΏΡΠΎΡΡΠΎ Π½Π΅Π·Π°ΠΌΠ΅Π½ΠΈΠΌΠ°Ρ. ΠΠ°Π»Π΅Π΅ ΠΏΠΎΠ΄ΡΠΎΠ±Π½Π΅ΠΉ.
ΠΠ°ΡΠ±ΠΎΠ½-ΠΊΠ°ΡΠ±ΠΎΠ½ΠΎΠ²ΡΠ΅ ΡΠΎΡΠΌΠΎΠ·Π° ΠΏΡΠΎΠΈΠ·Π²ΠΎΠ΄ΡΡΠ²Π° ΠΊΠΎΠΌΠΏΠ°Π½ΠΈΠΈ Freno (frenocarbon.com/home/). ΠΠΎ Π·Π°ΡΠ²Π»Π΅Π½ΠΈΡ ΠΏΡΠΎΠΈΠ·Π²ΠΎΠ΄ΠΈΡΠ΅Π»Ρ ΡΠΎΡΠΌΠΎΠ·Π° ΠΈΡΠΏΠΎΠ»ΡΠ·ΡΡΡΡΡ Π² Π€ΠΎΡΠΌΡΠ»Π΅β¦ ΠΠΈΠ°ΠΌΠ΅ΡΡ ΡΠΎΡΠΎΡΠ° 280 ΠΌΠΌ (ΠΎΠΏΡΡΡ ΠΆΠ΅, ΠΏΠΎ Π·Π°Π²Π΅ΡΠ΅Π½ΠΈΡΠΌ ΠΏΡΠΎΠΈΠ·Π²ΠΎΠ΄ΠΈΡΠ΅Π»Ρ, ΠΈΠΌΠ΅Π½Π½ΠΎ ΡΠ°ΠΊΠΎΠΉ ΠΈΡΠΏΠΎΠ»ΡΠ·ΡΡΡ Π² Π€ΠΎΡΠΌΡΠ»Π΅) ΠΏΠΎΠ·Π²ΠΎΠ»ΠΈΠ» ΠΏΡΠΈΡΠΏΠΎΡΠΎΠ±ΠΈΡΡ Π΄Π°Π½Π½ΡΠ΅ Π΄ΠΈΡΠΊΠΈ Π΄Π»Ρ ΠΠΎΡΡΡΠ°.
ΠΠΎΡ ΡΡΡ, ΠΏΠΎΠΆΠ°Π»ΡΠΉ, ΡΡΠΎΠΈΡ ΡΠ΄Π΅Π»Π°ΡΡ ΠΌΠ΅Π»Π΅Π½ΡΠΊΠΎΠ΅ Π»ΠΈΡΠΈΡΠ΅ΡΠΊΠΎΠ΅ ΠΎΡΡΡΡΠΏΠ»Π΅Π½ΠΈΠ΅. ΠΠ΅Π»ΠΎ Π² ΡΠΎΠΌ, ΡΡΠΎ ΡΠΎΠ΄Π½ΡΠ΅ ΡΠΎΡΠΌΠΎΠ·Π° Π½Π° ΠΠΎΡΡΡΠ΅ ΡΠΆΠ΅ ΡΠ°ΠΌΠΈ ΠΏΠΎ ΡΠ΅Π±Π΅ Π½Π΅ΠΏΠ»ΠΎΡ
ΠΈ. ΠΡΠΈ ΠΈΡΠΏΠΎΠ»ΡΠ·ΠΎΠ²Π°Π½ΠΈΠΈ ΠΏΡΠ°Π²ΠΈΠ»ΡΠ½ΡΡ
ΠΊΠΎΠ»ΠΎΠ΄ΠΎΠΊ ΠΎΠ½ΠΈ Π»Π΅Π³ΠΊΠΎ ΡΠΏΡΠ°Π²Π»ΡΡΡΡΡ Ρ Π½Π΅Π±ΠΎΠ»ΡΡΠΎΠΉ ΠΌΠ°ΡΡΠΎΠΉ Π°Π²ΡΠΎΠΌΠΎΠ±ΠΈΠ»Ρ. ΠΡΠΎΠ±Π΅Π½Π½ΠΎ, Π΅ΡΠ»ΠΈ ΡΡΡΠ°Π½ΠΎΠ²Π»Π΅Π½Ρ 308-ΠΌΠΌ BigBrakes ΠΎΡ AP Racing, ΠΊΠ°ΠΊ ΡΡΠΎ Π±ΡΠ»ΠΎ ΡΠ΄Π΅Π»Π°Π½ΠΎ Π½Π° Exige 240. ΠΠ½Π΅, ΠΊΠΎΠ½Π΅ΡΠ½ΠΎ, ΡΠ΄Π°Π»ΠΎΡΡ ΠΈΡ
ΠΏΠ΅ΡΠ΅Π³ΡΠ΅ΡΡ Π·Π° ΠΎΠ΄Π½Ρ ΡΡΠ΅ΠΊΠΎΠ²ΡΡ ΡΠ΅ΡΡΠΈΡ, Π½ΠΎ, ΠΊΠ°ΠΊ ΠΈΠ·Π²Π΅ΡΡΠ½ΠΎ, Ρ Π΄ΡΡΡ ΠΌΠΎΠΆΠ½ΠΎ Π²ΡΠ΅ ΡΠ»ΠΎΠΌΠ°ΡΡ:) Π ΠΏΡΠΈΠ½ΡΠΈΠΏΠ΅, Π΄ΠΎΡΡΠ°ΡΠΎΡΠ½ΠΎ Π±ΡΠ»ΠΎ ΡΠ΄Π΅Π»Π°ΡΡ ΠΏΡΠ°Π²ΠΈΠ»ΡΠ½ΡΠΉ ΠΎΠ±Π΄ΡΠ² β ΠΈ ΠΎ ΡΡΠ½ΠΈΠ½Π³Π΅ ΡΠΎΡΠΌΠΎΠ·ΠΎΠ² ΠΌΠΎΠΆΠ½ΠΎ Π±ΡΠ»ΠΎ Π±Ρ Π·Π°Π±ΡΡΡ. ΠΠΎ Π΄ΡΡΠ° Ρ
ΠΎΡΠ΅Π»Π° ΡΠΎΠΌΠ°Π½ΡΠΈΠΊΠΈ, Π° ΠΆ$ΠΏΠ° β ΠΏΡΠΈΠΊΠ»ΡΡΠ΅Π½ΠΈΠΉ:)
Π‘ΠΎΠ³Π»Π°ΡΠΈΡΠ΅ΡΡ, ΠΏΡΠΈΡΡΠ½ΠΎ Π½Π° ΡΠ²ΠΎΠ΅ΠΉ ΡΠΊΡΡΠ΅ ΠΎΠΏΡΠΎΠ±ΠΎΠ²Π°ΡΡ ΠΊΠ°ΠΊΡΡ-ΡΠΎ Π½ΠΎΠ²ΡΡ ΡΠ΅Π½ΡΠΊΡ ΠΈ ΠΏΠΎΡΠΎΠΌ Ρ ΡΠ΅ΡΡΠ΅Π·Π½ΡΠΌ Π²ΠΈΠ΄ΠΎΠΌ ΡΡΠ°ΡΠΈΡΡ ΡΠ°Π±ΠΎΡΠ΅Π΅ Π²ΡΠ΅ΠΌΡ Π½Π° ΡΠΎ, ΡΡΠΎΠ±Ρ Π΅Π΅ ΡΠ°ΡΡ Π²Π°Π»ΠΈΠ²Π°ΡΡ, Π²ΡΠ·ΡΠ²Π°Ρ ΠΏΡΠ°Π²ΠΈΠ»ΡΠ½ΡΡ Π·Π°Π²ΠΈΡΡΡ:) Π’Π΅ΠΌ Π±ΠΎΠ»Π΅Π΅, Ρ Π²Π°Π»ΠΈΡΡ Π΅ΡΡΡ ΡΡΠΎ.
ΠΡΠ°ΠΊ, ΠΊΠΎΠΌΠΏΠ»Π΅ΠΊΡ ΡΠΎΡΠΌΠΎΠ·ΠΎΠ² Π½Π° ΠΌΠΎΡΠ΄Ρ ΡΠΎΡΡΠΎΠΈΡ ΠΈΠ· ΡΠ°ΠΌΠΈΡ ΠΊΠ°ΡΠ±ΠΎΠ½ΠΎΠ²ΡΡ Π΄ΠΈΡΠΊΠΎΠ², ΡΠ°ΠΊΠΈΡ ΠΆΠ΅ ΠΊΠΎΠ»ΠΎΠ΄ΠΎΠΊ ΠΈ Π°Π»ΡΠΌΠΈΠ½ΠΈΠ΅Π²ΡΡ ΡΡΠΏΠΏΠΎΡΡΠΎΠ² ΠΏΡΠΎΠΈΠ·Π²ΠΎΠ΄ΡΡΠ²Π° Freno. Π’ΠΎ Π΅ΡΡΡ, Ρ Π»Π΅Π³ΠΊΠΎΠΉ Π³ΡΡΡΡΡΡ Π² Π³Π»Π°Π·Π°Ρ , ΠΏΡΠΈΡΠ»ΠΎΡΡ ΡΠ½ΡΡΡ Π·Π°ΠΌΠ΅ΡΠ°ΡΠ΅Π»ΡΠ½ΡΠ΅ 4-Ρ ΡΡΡΡΡΠΊΠΎΠ²ΡΠ΅ ΡΡΠΏΠΏΠΎΡΡΠ° AP Racing ΠΈ Π·Π°ΠΌΠ΅Π½ΠΈΡΡ ΠΈΡ Π½Π° ΠΏΠΎΠΊΠ°-Π½Π΅ΠΏΠΎΠ½ΡΡΠ½ΠΎ-ΡΡΠΎ:)
ΠΠ°Π΄Π½ΠΈΠ΅ ΡΠΎΡΠΌΠΎΠ·Π° β ΡΡΠΎ ΡΠΎΠ»ΡΠΊΠΎ ΠΊΠ°ΡΠ±ΠΎΠ½ΠΎΠ²ΡΠ΅ Π΄ΠΈΡΠΊΠΈ ΠΈ ΠΊΠΎΠ»ΠΎΠ΄ΠΊΠΈ, ΡΡΡΠ°Π½Π°Π²Π»ΠΈΠ²Π°Π΅ΠΌΡΠ΅ Π½Π° ΡΠΎΠ΄Π½ΡΠ΅ ΡΡΠΏΠΏΠΎΡΡΠ°
ΠΠ΅ΡΠ²ΠΎΠ΅, ΡΡΠΎ Π±ΡΠΎΡΠ°Π΅ΡΡΡ Π² Π³Π»Π°Π·Π° ΠΏΠΎΡΠ»Π΅ ΡΠ°ΡΠΏΠ°ΠΊΠΎΠ²ΠΊΠΈ ΠΊΠΎΡΠΎΠ±ΠΊΠΈ β ΡΡΠΎ ΠΎΡΡΡΡΡΡΠ²ΠΈΠ΅ Π²Π΅ΡΠ° ΡΠ°ΠΌΠΎΠ³ΠΎ ΡΠΎΡΠΌΠΎΠ·Π½ΠΎΠ³ΠΎ Π΄ΠΈΡΠΊΠ°. ΠΠ°ΠΆΠ΅ ΡΠ΅Π»ΠΎΠ²Π΅ΠΊ, ΠΊΠΎΡΠΎΡΡΠΉ ΡΠΆΠ΅ ΠΏΠ΅ΡΠ΅ΡΡΠ°Π» Π΄ΡΠΌΠ°ΡΡ, ΡΡΠΎ ΠΠΎΡΡΡ β ΠΈΠ³ΡΡΡΠΊΠ°, Π½Π΅ ΠΌΠΎΠΆΠ΅Ρ ΠΏΠΎΠ²Π΅ΡΠΈΡΡ, ΡΡΠΎ ΠΎΠ½ΠΈ Π½Π°ΡΡΠΎΡΡΠΈΠ΅:) ΠΡΠΆΠ½ΠΎ Π»ΠΈ ΡΠ°ΡΡΠΊΠ°Π·ΡΠ²Π°ΡΡ, ΠΊΠ°ΠΊ ΠΏΠΎΠ»ΠΎΠΆΠΈΡΠ΅Π»ΡΠ½ΠΎ ΡΠΊΠ°Π·ΡΠ²Π°Π΅ΡΡΡ ΡΠΊΠΎΠ½ΠΎΠΌΠΈΡ Π² Π²Π΅ΡΠ΅ Π½Π΅ΠΏΠΎΠ΄ΡΠ΅ΡΡΠΎΡΠ΅Π½Π½ΡΡ ΠΌΠ°ΡΡ Π½Π° ΡΠΏΡΠ°Π²Π»ΡΠ΅ΠΌΠΎΡΡΠΈ Π°Π²ΡΠΎΠΌΠΎΠ±ΠΈΠ»Ρ? ΠΡΠ»ΠΈ Π½Π΅Ρ, ΠΈΠΌΠ΅Π΅ΠΌ ΠΏΠ΅ΡΠ²ΡΠΉ ΠΏΠ»ΡΡ Π² ΠΎΠ±ΠΎΡΠ½ΠΎΠ²Π°Π½ΠΈΠ΅ ΠΏΠΎΠΊΡΠΏΠΊΠΈ:)
Π‘Π»Π΅Π΄ΡΡΡΠΈΠΉ ΡΡΡΠΏΡΠΈΠ· ΠΎΠΆΠΈΠ΄Π°Π» ΡΡΠ°Π·Ρ Π·Π° Π²ΠΎΡΠΎΡΠ°ΠΌΠΈ Π³Π°ΡΠ°ΠΆΠ°. ΠΠΊΠ°Π·Π°Π»ΠΎΡΡ, ΡΡΠΎ Π½Π΅Ρ Π½Π΅ ΡΠΎΠ»ΡΠΊΠΎ Π²Π΅ΡΠ° ΡΠΎΡΠΎΡΠΎΠ². ΠΠ° Ρ
ΠΎΠ»ΠΎΠ΄Π½ΡΡ Π½Π΅Ρ ΡΠ°ΠΌΠΈΡ
ΡΠΎΡΠΌΠΎΠ·ΠΎΠ²! Π‘ΠΎΠ²ΡΠ΅ΠΌ! ΠΠΎΡ ΡΡΠ° Π½ΠΎΠ²ΠΎΡΡΡ Π±ΡΠ»Π° ΡΠΎΠ²ΡΠ΅ΠΌ Π½Π΅ΠΎΠΆΠΈΠ΄Π°Π½Π½ΠΎΠΉ ΠΈ ΠΌΠ°Π»ΠΎΠΏΡΠΈΡΡΠ½ΠΎΠΉ. Π― ΠΊΠΎΠ½Π΅ΡΠ½ΠΎ, ΡΠ»ΡΡΠ°Π», ΡΡΠΎ ΠΊΠ°ΡΠ±ΠΎΠ½ΠΎΠ²ΡΠ΅ ΡΠΎΡΠΌΠΎΠ·Π° Π½Π°ΡΠΈΠ½Π°ΡΡ ΡΠ°Π±ΠΎΡΠ°ΡΡ ΡΠΎΠ»ΡΠΊΠΎ, ΠΊΠΎΠ³Π΄Π° ΠΏΡΠΎΠ³ΡΠ΅ΡΡΡΡ. ΠΠΎ Ρ ΠΏΡΠ΅Π΄ΡΡΠ°Π²ΠΈΡΡ Π½Π΅ ΠΌΠΎΠ³, ΡΡΠΎ Π΄ΠΎ ΡΡΠΎΠ³ΠΎ ΠΈΡ
Π½Π΅ Π±ΡΠ΄Π΅Ρ ΡΠΎΠ²ΡΠ΅ΠΌ:( Π ΡΡΠ°ΡΡΡΡ, ΡΡΡΠ΅ΠΊΡ Π½Π΅Π΄ΠΎΠ»Π³ΠΈΠΉ, Π΅ΡΠ»ΠΈ ΠΈΡ
Π±ΡΡΡΡΠΎ ΠΏΡΠΎΠ³ΡΠ΅ΡΡ. ΠΠ΅Π»Π°Π΅ΡΡΡ ΡΡΠΎ ΡΠ»Π΅Π΄ΡΡΡΠΈΠΌ ΠΎΠ±ΡΠ°Π·ΠΎΠΌ:
1. ΠΡΠ±ΠΈΡΠ°Π΅ΠΌ ΡΠΎΠ²Π½ΡΠΉ, ΠΏΡΡΡΠΎΠΉ ΡΡΠ°ΡΡΠΎΠΊ Π΄ΠΎΡΠΎΠ³ΠΈ.
2. Π Π°Π·Π³ΠΎΠ½ΡΠ΅ΠΌΡΡ Π΄ΠΎ 60-70 ΠΊΠΌ/Ρ (Π΄ΠΎ 80 Π½Π΅ ΡΡΡΠ°ΡΡΡΡ;))
3. Π’ΠΎΡΠΌΠΎΠ·ΠΈΠΌ Π² ΠΏΠΎΠ», ΠΏΠΎΡΡΠΈ Π΄ΠΎ ΠΎΡΡΠ°Π½ΠΎΠ²ΠΊΠΈ (ΡΠ΄ΠΈΠ²Π»ΡΠ΅ΠΌΡΡ, ΠΊΠ°ΠΊ Π½Π΅ Π±ΡΡΡΡΠΎ ΡΡΠΎ ΠΏΡΠΎΠΈΡΡ
ΠΎΠ΄ΠΈΡ)
4. ΠΠΎΠ²ΡΠΎΡΡΠ΅ΠΌ Π²Π΅ΡΡ ΡΠΈΠΊΠ» 2-3 ΡΠ°Π·Π°
5. Π Π°Π΄ΡΠ΅ΠΌΡΡ, ΡΡΠΎ Π½Π΅ ΠΎΠ±ΡΠ·Π°ΡΠ΅Π»ΡΠ½ΠΎ ΡΠΎΡΠΌΠΎΠ·ΠΈΡΡ ΠΎΠ± Π΄ΡΡΠ³ΡΡ ΠΌΠ°ΡΠΈΠ½Ρ ΠΈΠ»ΠΈ Π΄Π΅ΡΠ΅Π²ΠΎ:)
ΠΡΠΊΡΠΎΠ²Π΅Π½Π½ΠΎ Π³ΠΎΠ²ΠΎΡΡ, ΠΏΠ°ΡΡ Π½Π΅Π΄Π΅Π»Ρ Ρ Π½Π΅ ΠΌΠΎΠ³ ΠΏΠΎΠ½ΡΡΡ, ΠΏΡΠ°Π²ΠΈΠ»ΡΠ½ΠΎ Π»ΠΈ Ρ ΡΠ΄Π΅Π»Π°Π». ΠΠ°ΡΠ°ΡΡΡ ΠΏΠΎ Π³ΠΎΡΠΎΠ΄Ρ, ΡΠ»ΠΎΠΆΠ½ΠΎ ΠΏΠΎΠ½ΡΡΡ ΡΠ°Π·Π½ΠΈΡΡ ΠΌΠ΅ΠΆΠ΄Ρ ΠΊΠ°ΡΠ±ΠΎΠ½ΠΎΠ²ΡΠΌΠΈ ΠΈ ΡΠΎΠ΄Π½ΡΠΌΠΈ ΡΠΎΡΠΌΠΎΠ·Π°ΠΌΠΈ. Π’ΠΎΡΠ½Π΅Π΅, ΡΠ»ΠΎΠΆΠ½ΠΎ ΠΏΠΎΠ²Π΅ΡΠΈΡΡ Π² ΠΈΡ
ΠΏΡΠ΅ΠΈΠΌΡΡΠ΅ΡΡΠ²ΠΎ. ΠΠ° ΡΡΠΈ ΠΏΠ°ΡΡ Π½Π΅Π΄Π΅Π»Ρ Ρ Π½Π°ΡΠ°Π» Π΄ΡΠΌΠ°ΡΡ, ΡΡΠΎ ΡΠΎΠ²Π΅ΡΡΠΈΠ» ΠΎΡΠΈΠ±ΠΊΡ.
ΠΡΠ΅ ΠΈΠ·ΠΌΠ΅Π½ΠΈΠ»ΠΎΡΡ ΠΎΠ΄Π½ΠΈΠΌ ΡΠ°Π½Π½ΠΈΠΌ ΡΡΡΠΎΠΌ, ΠΊΠΎΠ³Π΄Π° Ρ Π²ΡΠ΅Ρ
Π°Π» Π½Π° ΠΠΠΠ Π² Π½Π°ΠΏΡΠ°Π²Π»Π΅Π½ΠΈΠΈ ΠΡΡΠΈΠΊΠ°. ΠΠΎΡΠΎΠ³Π° ΠΏΡΡΠΌΠ°Ρ ΠΈ ΠΏΠΎΡΡΠΈ ΠΏΡΡΡΠ°Ρ. Π‘ΡΡ
ΠΎ. ΠΠ΄Π΅Π°Π»ΡΠ½ΡΠ΅ ΡΡΠ»ΠΎΠ²ΠΈΡ Π΄Π»Ρ Π½Π°Π±ΠΎΡΠ° ΠΌΠ°ΠΊΡΠΈΠΌΠ°Π»ΡΠ½ΠΎ ΡΠ°Π·ΡΠ΅ΡΠ΅Π½Π½ΠΎΠΉ ΠΡΠ°Π²ΠΈΠ»Π°ΠΌΠΈ ΠΠΎΡΠΎΠΆΠ½ΠΎΠ³ΠΎ ΠΠ²ΠΈΠΆΠ΅Π½ΠΈΡ ΡΠΊΠΎΡΠΎΡΡΠΈ:) Π ΠΊΠ°ΠΊΠΎΠΉ-ΡΠΎ ΠΌΠΎΠΌΠ΅Π½Ρ, ΡΠΆΠ΅ ΠΏΡΠΈΠ²ΡΡΠ½ΠΎ Π»Π΅Π³ΠΊΠΎ Π½Π°ΠΆΠ°Π² Π½Π° ΡΠΎΡΠΌΠΎΠ·, Π·Π°Π΄ΠΎΠ»Π³ΠΎ Π΄ΠΎ Π²ΠΏΠ΅ΡΠ΅Π΄ΠΈ ΠΈΠ΄ΡΡΠ΅Π³ΠΎ Π°Π²ΡΠΎ, Ρ ΠΏΠΎΠ½ΡΠ», ΡΡΠΎ ΡΠΆΠ΅ Π»ΠΎΠ²Π»Ρ ΠΠΎΡΡΡ Π½Π΅ ΠΏΠΎΡΡΠΈ Π·Π°Π±Π»ΠΎΠΊΠΈΡΠΎΠ²Π°Π½Π½ΡΡ
ΠΊΠΎΠ»Π΅ΡΠ°Ρ
! ΠΡΠ΄ΡΡΠ°Π²ΡΠΈΡΡ, Ρ ΠΏΠΎΠΏΡΠΎΠ±ΠΎΠ²Π°Π» Π΅ΡΠ΅ ΡΠ°Π· Π»Π΅Π³ΠΎΠ½ΡΠΊΠΎ Π½Π°ΠΆΠ°ΡΡ Π½Π° ΡΠΎΡΠΌΠΎΠ· β ΡΠ½ΠΎΠ²Π° ΠΏΠΎΠ²ΠΈΡ Π½Π° ΡΠ΅ΠΌΠ½ΡΡ
, ΠΊΠ°ΠΊ ΠΌΠ°Π½Π΄Π°ΡΠΈΠ½ΠΊΠ° Π½Π° Π½ΠΎΠ²ΠΎΠ³ΠΎΠ΄Π½Π΅ΠΉ Π΅Π»ΠΊΠ΅:) ΠΡ ΠΏΠΎΠΌΠ½ΠΈΡΠ΅, ΠΊΠ°ΠΊ ΠΏΠ°ΠΏΠ° ΠΏΡΠΈΠ½Π΅Ρ ΠΠ°ΠΌ ΠΏΠ΅ΡΠ²ΡΠΉ Π²Π΅Π»ΠΎΡΠΈΠΏΠ΅Π΄? ΠΠΎΡ ΡΠ°Π΄ΠΎΡΡΡ Π² ΡΡΠΎΡ ΠΌΠΎΠΌΠ΅Π½Ρ Π±ΡΠ»Π° ΡΠ°ΠΊΠΎΠΉ ΠΆΠ΅:)) Π‘ ΡΠΎΠ³ΠΎ Π΄Π½Ρ Ρ Π±ΠΎΠ»ΡΡΠ΅ Π½ΠΈ ΡΠ°Π·Ρ Π½Π΅ ΡΠΎΠΌΠ½Π΅Π²Π°Π»ΡΡ Π² ΠΏΡΠ°Π²ΠΈΠ»ΡΠ½ΠΎΡΡΠΈ Π²ΡΠ±ΠΎΡΠ°. ΠΠ°ΡΠΈΠ½Π° ΡΡΠ°Π»Π° ΡΠΎΡΠΌΠΎΠ·ΠΈΡΡ Π½Π΅ΡΠ΅Π°Π»ΡΠ½ΠΎ:) ΠΠΎΠ½Π΅ΡΠ½ΠΎ ΠΆΠ΅, ΡΡΠΎΠ±Ρ Π² ΠΏΠΎΠ»Π½ΠΎΠΉ ΠΌΠ΅ΡΠ΅ Π½Π°ΡΠ»Π°Π΄ΠΈΡΡΡΡ ΡΡΠΈΠΌ ΡΠΎΡΠΌΠΎΠΆΠ΅Π½ΠΈΠ΅ΠΌ, Π½Π°Π΄ΠΎ Π΅Ρ
Π°ΡΡ Π½Π° ΡΡΠ΅ΠΊ. Π’ΠΎΠ»ΡΠΊΠΎ ΡΠ°ΠΌ ΠΌΠΎΠΆΠ½ΠΎ, Π½Π°ΡΠ°Π² ΡΠΎΡΠΌΠΎΠΆΠ΅Π½ΠΈΠ΅ Π³ΠΎΡΠ°Π·Π΄ΠΎ ΠΏΠΎΠ·ΠΆΠ΅ ΠΊΠΎΠ»Π»Π΅Π³, Π ΠΠΠ¬Π¨Π Π²ΠΎΠΉΡΠΈ Π² ΠΏΠΎΠ²ΠΎΡΠΎΡ Π½Π° ΡΠΆΠ΅ ΡΠ±Π°Π»Π°Π½ΡΠΈΡΠΎΠ²Π°Π½Π½ΠΎΠΉ ΠΌΠ°ΡΠΈΠ½Π΅. Π, ΡΡΠΎ Π½Π΅ΠΌΠ°Π»ΠΎ Π²Π°ΠΆΠ½ΠΎ, ΡΠ΄Π΅Π»Π°ΡΡ ΡΡΠΎ Π±Π΅Π·ΠΎΠΏΠ°ΡΠ½ΠΎ.
ΠΠΎ, ΠΏΠΎΡΠΊΠΎΠ»ΡΠΊΡ ΠΏΠΎΡΡ Π½Π΅ ΡΠ΅ΠΊΠ»Π°ΠΌΠ½ΡΠΉ ΠΈ Π΄Π»Ρ Π±Π°Π»Π°Π½ΡΠ° ΠΏΠΎΠ²Π΅ΡΡΠ²ΠΎΠ²Π°Π½ΠΈΡ, Π΄Π°Π²Π°ΠΉΡΠ΅ ΠΎΡ ΠΏΠΎΠ»ΠΎΠΆΠΈΡΠ΅Π»ΡΠ½ΡΡ
ΡΠΌΠΎΡΠΈΠΉ ΠΏΠ΅ΡΠ΅ΠΉΠ΄Π΅ΠΌ ΠΊ Π³ΡΡΡΡΠ½ΡΠΌ ΡΠ°ΠΊΡΠ°ΠΌ. ΠΠ° ΠΏΠ°ΡΡ ΠΌΠ΅ΡΡΡΠ΅Π² ΡΠΊΡΠΏΠ»ΡΠ°ΡΠ°ΡΠΈΠΈ ΠΈ Π½Π΅ΡΠ°ΡΡΡΡ
ΠΏΠΎΠΊΠ°ΡΡΡΠ΅ΠΊ Π½Π° ΡΡΠ΅ΠΊ Π²ΡΡΠ²ΠΈΠ»ΠΈΡΡ ΠΊΠΎΠ΅-ΠΊΠ°ΠΊΠΈΠ΅ Π½Π΅Π΄ΠΎΡΡΠ°ΡΠΊΠΈ.
1. Π‘ΡΠ°ΡΡΠΉ Π΄ΡΡΠ³ Π»ΡΡΡΠ΅ Π½ΠΎΠ²ΡΡ
Π΄Π²ΡΡ
. Π‘ΡΠΏΠΏΠΎΡΡΠ° AP Racing ΡΠΆΠ΅ Π΄Π°Π²Π½ΠΎ Π·Π°ΡΠ΅ΠΊΠΎΠΌΠ΅Π½Π΄ΠΎΠ²Π°Π»ΠΈ ΡΠ΅Π±Ρ ΠΊΠ°ΠΊ ΡΡΡΠ΅ΠΊΡΠΈΠ²Π½ΡΠ΅ ΠΈ Π½Π°Π΄Π΅ΠΆΠ½ΡΠ΅. Freno ΠΏΠΎΡΠ»Π΅Π΄Π½ΠΈΠΌ ΠΏΠΎΠΊΠ°Π·Π°ΡΠ΅Π»Π΅ΠΌ (ΠΏΠΎΠΊΠ°) ΠΏΠΎΡ
Π²Π°ΡΡΠ°ΡΡΡΡ Π½Π΅ ΠΌΠΎΠΆΠ΅Ρ. Π ΠΎΠ΄ΠΈΠ½ ΠΈΠ· ΡΡΠ΅ΠΊ-Π΄Π½Π΅ΠΉ Π½Π° ΠΠ Π Ρ ΠΌΠ΅Π½Ρ ΠΏΠΎΡΠ΅ΠΊΠ»ΠΎ ΡΠΎΠ΅Π΄ΠΈΠ½Π΅Π½ΠΈΠ΅ ΡΠΎΡΠΌΠΎΠ·Π½ΠΎΠ³ΠΎ ΡΠ»Π°Π½Π³Π° ΠΈ ΡΡΠΏΠΏΠΎΡΡΠ°. ΠΠΎΠ·ΠΌΠΎΠΆΠ½ΠΎ, ΡΡΠΏΠΏΠΎΡΡ Π½Π΅ ΡΠΏΡΠ°Π²Π»ΡΠ΅ΡΡΡ Ρ ΡΠΎΠΉ ΡΠ΅ΠΌΠΏΠ΅ΡΠ°ΡΡΡΠΎΠΉ, Π½Π° ΠΊΠΎΡΠΎΡΠΎΠΉ ΡΠΎΡΠΌΠΎΠ·Π° ΠΎΡΠ΅Π½Ρ ΡΡΡΠ΅ΠΊΡΠΈΠ²Π½ΠΎ ΡΠ°Π±ΠΎΡΠ°ΡΡ. Π ΠΌΠΎΠΆΠ΅Ρ, Π½Π΅Π΄ΠΎΡΡΠ°ΡΠΊΠΈ ΡΠ±ΠΎΡΠΊΠΈ. Π€Π°ΠΊΡ Π΅ΡΡΡ ΡΠ°ΠΊΡ. Π’ΠΎΡΠΌΠΎΠ·Π° ΠΏΠΎΡΠ»Π΅ ΡΡΠΎΠ³ΠΎ Π΄ΠΎΡΡΠ°ΡΠΎΡΠ½ΠΎ Π±ΡΡΡΡΠΎ Π·Π°ΠΊΠΈΠΏΠ΅Π»ΠΈ.
2. ΠΠΎΡΠ»Π΅ ΡΠ΅Π²ΠΈΠ·ΠΈΠΈ/ΡΠ΅ΠΌΠΎΠ½ΡΠ° ΡΠΎΡΠΌΠΎΠ·ΠΎΠ² ΠΈ Π·Π°ΠΌΠ΅Π½Ρ ΠΆΠΈΠ΄ΠΊΠΎΡΡΠΈ ΡΠ½ΠΎΠ²Π° ΠΏΠΎΠ΅Ρ
Π°Π» Π½Π° ΡΡΠ΅ΠΊ. ΠΡΠ»ΠΈ Π΅Ρ
Π°ΡΡ Π΄Π²Π΅ ΡΠ΅ΡΡΠΈΠΈ ΠΏΠΎΠ΄ΡΡΠ΄, ΠΊ ΠΊΠΎΠ½ΡΡ Π²ΡΠΎΡΠΎΠΉ ΡΠΎΡΠΌΠΎΠ·Π° Π½Π°ΡΠΈΠ½Π°ΡΡ ΠΊΠΈΠΏΠ΅ΡΡ. Π ΡΡΠΎ ΠΏΡΠΈ ΡΠΎΠΌ, ΡΡΠΎ ΠΆΠΈΠ΄ΠΊΠΎΡΡΡ β Motul RBF 660 Ρ ΡΠ΅ΠΌΠΏΠ΅ΡΠ°ΡΡΡΠΎΠΉ ΠΊΠΈΠΏΠ΅Π½ΠΈΡ 325Π‘. ΠΠ°ΠΊ Ρ ΡΡΠΈΠΌ Π±ΡΡΡ ΠΏΠΎΠΊΠ° Π½Π΅ Π·Π½Π°Ρ. ΠΠ΅Π»Π°ΡΡ ΠΎΠ±Π΄ΡΠ² ΡΠΎΡΠΌΠΎΠ·ΠΎΠ²? Π° Π½Π΅ ΠΏΠ΅ΡΠ΅ΡΡΠ°Π½ΡΡ Π»ΠΈ ΠΎΠ½ΠΈ ΡΠΎΠ³Π΄Π° ΡΠ°Π±ΠΎΡΠ°ΡΡ? Π ΠΎΠ±ΡΠ΅ΠΌ, Π΅ΡΡΡ Π½Π°Π΄ ΡΠ΅ΠΌ ΠΏΠΎΠ΄ΡΠΌΠ°ΡΡ.
3. ΠΠΎΡΡΡΠΈΠ΅ ΡΠΎΡΠΌΠΎΠ·Π° ΡΠΊΡΠΈΠΏΡΡ Π½Π΅ΡΠ°Π΄Π½ΠΎ. ΠΠΎ Ρ ΡΡΠΈΠΌ ΠΌΠΎΠΆΠ½ΠΎ ΠΆΠΈΡΡ. ΠΠ»ΠΈ ΡΠΌΠ°Π·Π°ΡΡ:)))
Π ΠΈΡΠΎΠ³Π΅, Π½Π° ΡΠ΅Π³ΠΎΠ΄Π½ΡΡΠ½ΠΈΠΉ Π΄Π΅Π½Ρ ΠΈΠΌΠ΅Π΅ΠΌ ΡΠ»Π΅Π΄ΡΡΡΠΈΠΉ Π±Π°Π»Π°Π½Ρ.
ΠΠ»ΡΡΡ:
1. ΠΠ΅ΡΠ΅Π°Π»ΡΠ½Π°Ρ ΡΡΡΠ΅ΠΊΡΠΈΠ²Π½ΠΎΡΡΡ, ΠΊΠΎΠ³Π΄Π° ΠΏΡΠΎΠ³ΡΠ΅ΡΡ
2. ΠΠ°Π»ΡΠΉ Π²Π΅Ρ
3. ΠΠΎΠ»Π³ΠΎΠ²Π΅ΡΠ½ΠΎΡΡΡ. ΠΠΎ Π·Π°Π²Π΅ΡΠ΅Π½ΠΈΡ ΠΏΡΠΎΠΈΠ·Π²ΠΎΠ΄ΠΈΡΠ΅Π»Ρ, ΠΌΠΎΠ³ΡΡ ΠΏΡΠΎΠΉΡΠΈ Π΄ΠΎ 100 ΡΡΡ Π² ΡΡΠ΅ΠΊΠΎΠ²ΠΎΠΌ ΡΠ΅ΠΆΠΈΠΌΠ΅. Π‘ΠΎΠΌΠ½Π΅Π²Π°ΡΡΡ ΠΈ Π±ΡΠ΄Ρ ΡΠΌΠΎΡΡΠ΅ΡΡ. ΠΠΎ ΠΏΡΠΎΡΠ΅ΡΡΠ²ΠΈΠΈ 2 ΠΌΠ΅ΡΡΡΠ΅Π² ΠΈ 2 ΡΡΡ ΠΊΠΌ Ρ Π½Π΅ΡΠ°ΡΡΡΠΌ Π²ΡΠ΅Π·Π΄ΠΎΠΌ Π½Π° ΡΡΠ΅ΠΊ (5-6 ΡΡΠ΅ΠΊ-Π΄Π½Π΅ΠΉ) Π΄ΠΈΡΠΊΠΈ ΠΏΠΎΠ΄ΡΠ΅Π»ΠΈΡΡ ΠΌΠ΅Π½Π΅Π΅, ΡΠ΅ΠΌ Π½Π°1 ΠΌΠΌ
4. ΠΡΠ°ΡΠΎΡΠ°:)) ΠΠ΅ΡΡΠ΅Π½Π½ΠΎ:)
ΠΠΈΠ½ΡΡΡ:
1. Π¦Π΅Π½Π°. ΠΡΠ΅Π½Ρ ΡΡΠ±ΡΠ΅ΠΊΡΠΈΠ²Π½ΠΎ. ΠΠΈΡΠ½ΠΎ Ρ ΡΡΠΈΡΠ°Ρ, ΡΡΠΎ ΠΎΠ½ΠΈ ΡΠ²ΠΎΠΈΡ
Π΄Π΅Π½Π΅Π³ ΡΡΠΎΡΡ.
2. ΠΡΠ°ΠΉΠ½Π΅ Π½ΠΈΠ·ΠΊΠ°Ρ ΡΡΡΠ΅ΠΊΡΠΈΠ²Π½ΠΎΡΡΡ, ΠΏΠΎΠΊΠ° Π½Π΅ ΠΏΡΠΎΠ³ΡΠ΅ΡΡ. ΠΡΠΎ ΠΏΡΠΎΡΡΠΎ Π½Π°Π΄ΠΎ ΠΏΠΎΠΌΠ½ΠΈΡΡ, ΠΠΠΠΠ«Π ΡΠ°Π· ΡΠ°Π΄ΡΡΡ Π·Π° ΡΡΠ»Ρ
3. ΠΠ°Π΄Π΅ΠΆΠ½ΠΎΡΡΡ? ΠΠ°Π΄Π΅ΡΡΡ, Ρ ΡΡΠΈΠΌ Π²ΡΠ΅ Π² ΠΏΠΎΡΡΠ΄ΠΊΠ΅ ΠΈ ΠΏΡΠΎΡΠ΅ΡΠΊΠ° Π±ΡΠ»Π° ΡΠ²ΡΠ·Π°Π½Π° Ρ ΠΊΡΠΈΠ²ΡΠΌΠΈ ΡΡΠΊΠ°ΠΌΠΈ Π½Π΅Π΄ΠΎΡΡΠ°ΡΠΊΠ°ΠΌΠΈ ΡΠ±ΠΎΡΠΊΠΈ. ΠΡΠ΄Ρ ΡΠ»Π΅Π΄ΠΈΡΡ
4. ΠΡΡΡΡΡΡΠ²ΠΈΠ΅ ΡΠΎΡΠΌΠΎΠ·Π½ΠΎΠΉ ΠΆΠΈΠ΄ΠΊΠΎΡΡΠΈ, Π²ΡΠ΄Π΅ΡΠΆΠΈΠ²Π°ΡΡΠ΅ΠΉ Π²ΡΡΠΎΠΊΡΡ ΡΠ΅ΠΌΠΏΠ΅ΡΠ°ΡΡΡΡ, ΠΏΡΠΈ ΠΊΠΎΡΠΎΡΠΎΠΉ ΡΠΎΡΠΌΠΎΠ·Π° ΡΠ°Π±ΠΎΡΠ°ΡΡ ΠΊΡΠ°ΠΉΠ½Π΅ ΡΡΡΠ΅ΠΊΡΠΈΠ²Π½ΠΎ. ΠΠΎΠ·ΠΌΠΎΠΆΠ½ΠΎ, Π²ΡΠ»Π΅ΡΠΈΡΡΡ ΠΎΠ±Π΄ΡΠ²ΠΎΠΌ ΠΈΠ»ΠΈ ΠΎΡΠΊΠ°Π·ΠΎΠΌ ΠΎΡ Π΄Π²ΡΡ
ΡΠ΅ΡΡΠΈΠΉ ΠΏΠΎΠ΄ΡΡΠ΄:)
5. Π¨ΡΠΌ. Π½Ρ, Ρ ΡΡΠΈΠΌ Π²ΠΎΠΎΠ±ΡΠ΅ Π²ΡΠ΅ ΠΏΡΠΎΡΡΠΎ. ΠΠΎΠΆΠ½ΠΎ Π½Π΅ Π·Π°ΠΌΠ΅ΡΠ°ΡΡ ΠΈΠ»ΠΈ ΡΡΠΈΡΠ°ΡΡ, ΡΡΠΎ ΡΡΠΎ ΡΠ°ΠΊΠΎΠΉ ΡΠ°ΡΠΌ, ΠΏΡΠΈΠ²Π»Π΅ΠΊΠ°ΡΡΠΈΠΉ Π²Π½ΠΈΠΌΠ°Π½ΠΈΠ΅ ΠΎΠΊΡΡΠΆΠ°ΡΡΠΈΡ
. ΠΠΊΡΡΡΠ΅ΠΌΠ°Π»Ρ ΠΌΠΎΠ³ΡΡ ΡΠΌΠ°Π·Π°ΡΡ:))
Π Π΄Π°Π»ΡΡΠ΅, ΠΊΠ°ΠΊ ΠΎΠ±ΡΡΠ½ΠΎ, Π±ΡΠ΄Π΅ΠΌ ΠΊΠ°ΡΠ°ΡΡ ΠΏΡΠΎΠΊΠ»Π°Π΄ΠΊΡ:)
ΠΡΡΠΎΡΠ½ΠΈΠΊ www.drive2.ru
- ΠΠ°ΠΊΠΎΠ²Ρ ΠΏΡΠ΅ΠΈΠΌΡΡΠ΅ΡΡΠ²Π° ΠΊΠ°ΡΠ±ΠΎΠ½ΠΎ-ΠΊΠ΅ΡΠ°ΠΌΠΈΡΠ΅ΡΠΊΠΈΡ ΡΠΎΡΠΌΠΎΠ·ΠΎΠ²?
- ΠΠ΅ΡΠ°ΠΌΠΈΡΠ΅ΡΠΊΠΈΠ΅ ΡΠΎΡΠΌΠΎΠ·Π½ΡΠ΅ ΡΠΈΡΡΠ΅ΠΌΡ
- ΠΡΠ½ΠΎΠ²Π½ΡΠ΅ ΠΏΡΠ΅ΠΈΠΌΡΡΠ΅ΡΡΠ²Π° ΠΈ Π½Π΅Π΄ΠΎΡΡΠ°ΡΠΊΠΈ
- ΠΡΠ΅Π΄ΡΡ Π»ΠΈ ΠΊΠΎΠ»ΠΎΠ΄ΠΊΠΈ ΠΈΠ· ΠΊΠ΅ΡΠ°ΠΌΠΈΠΊΠΈ ΡΠΎΡΠΌΠΎΠ·Π½ΠΎΠΌΡ Π΄ΠΈΡΠΊΡ
- ΠΠΏΡΠ΅Π΄Π΅Π»ΡΠ΅ΠΌΡΡ Ρ Π²ΡΠ±ΠΎΡΠΎΠΌ: ΠΊΠ΅ΡΠ°ΠΌΠΈΡΠ΅ΡΠΊΠΈΠ΅ ΠΊΠΎΠ»ΠΎΠ΄ΠΊΠΈ ΠΈΠ»ΠΈ ΠΌΠ΅ΡΠ°Π»Π»ΠΈΡΠ΅ΡΠΊΠΈΠ΅
Π’ΠΎΡΠΌΠΎΠ·Π½Π°Ρ ΡΠΈΡΡΠ΅ΠΌΠ°, Π² ΠΏΠ΅ΡΠ²ΡΡ ΠΎΡΠ΅ΡΠ΅Π΄Ρ, Π΄ΠΎΠ»ΠΆΠ½Π° Π±ΡΡΡ Π½Π°Π΄Π΅ΠΆΠ½ΠΎΠΉ, Π²ΡΠ΄Π΅ΡΠΆΠΈΠ²Π°ΡΡ ΠΌΠ°ΠΊΡΠΈΠΌΠ°Π»ΡΠ½ΡΠ΅ Π½Π°Π³ΡΡΠ·ΠΊΠΈ ΠΈ Π±ΡΡΡΡΠΎ ΠΏΡΠ΅ΡΡΠ²Π°ΡΡ Π΄Π²ΠΈΠΆΠ΅Π½ΠΈΠ΅. Π‘Π΅Π³ΠΎΠ΄Π½Ρ ΠΌΡ ΠΏΠΎΠΏΡΠΎΠ±ΡΠ΅ΠΌ ΡΠ°Π·ΠΎΠ±ΡΠ°ΡΡΡΡ Π² ΠΊΠ΅ΡΠ°ΠΌΠΈΡΠ΅ΡΠΊΠΎΠΉ ΡΠΎΡΠΌΠΎΠ·Π½ΠΎΠΉ ΡΠΈΡΡΠ΅ΠΌΠ΅ ΠΈ ΡΠ·Π½Π°Π΅ΠΌ, ΡΠ΅ΠΌ ΠΆΠ΅ Π»ΡΡΡΠ΅ ΠΌΠ΅ΡΠ°Π»Π»ΠΈΡΠ΅ΡΠΊΠΈΡ
ΠΊΠ΅ΡΠ°ΠΌΠΈΡΠ΅ΡΠΊΠΈΠ΅ ΡΠΎΡΠΌΠΎΠ·Π½ΡΠ΅ ΠΊΠΎΠ»ΠΎΠ΄ΠΊΠΈ.
ΠΠ΅ΡΠ°ΠΌΠΈΡΠ΅ΡΠΊΠΈΠ΅ ΡΠΎΡΠΌΠΎΠ·Π½ΡΠ΅ ΡΠΈΡΡΠ΅ΠΌΡ
Π‘Π°ΠΌΠΎΠΉ ΡΠ°ΡΠΏΡΠΎΡΡΡΠ°Π½Π΅Π½Π½ΠΎΠΉ ΡΠΎΡΠΌΠΎΠ·Π½ΠΎΠΉ ΡΠΈΡΡΠ΅ΠΌΠΎΠΉ Π½Π° ΡΠ΅Π³ΠΎΠ΄Π½ΡΡΠ½ΠΈΠΉ Π΄Π΅Π½Ρ ΡΠ²Π»ΡΠ΅ΡΡΡ Π΄ΠΈΡΠΊΠΎΠ²Π°Ρ, Π³Π΄Π΅ Π³Π»Π°Π²Π½ΡΠΉ ΡΠ»Π΅ΠΌΠ΅Π½Ρ β ΡΠΎΡΠΌΠΎΠ·Π½ΠΎΠΉ Π΄ΠΈΡΠΊ, ΠΈ ΠΊ Π½Π΅ΠΌΡ ΠΏΡΠΈΠΊΠ»Π°Π΄ΡΠ²Π°Π΅ΡΡΡ ΡΡΠΈΠ»ΠΈΠ΅ ΠΈΡΠΏΠΎΠ»Π½ΠΈΡΠ΅Π»ΡΠ½ΠΎΠ³ΠΎ ΠΌΠ΅Ρ Π°Π½ΠΈΠ·ΠΌΠ°. Π ΡΡΡΠ΅ΡΡΠ²ΡΡΡΠΈΡ ΡΠΎΡΠΌΠΎΠ·Π½ΡΡ ΡΠΈΡΡΠ΅ΠΌΠ°Ρ ΡΠΎΡΠΌΠΎΠΆΠ΅Π½ΠΈΠ΅ Π²ΡΠΏΠΎΠ»Π½ΡΠ΅ΡΡΡ Π·Π° ΡΡΠ΅Ρ ΡΠ½ΠΈΠΆΠ΅Π½ΠΈΡ ΠΊΡΡΡΡΡΠ΅Π³ΠΎ ΠΌΠΎΠΌΠ΅Π½ΡΠ° ΠΊΠΎΠ»Π΅Ρ ΠΏΡΡΠ΅ΠΌ ΡΡΠ΅Π½ΠΈΡ ΡΠ»Π΅ΠΌΠ΅Π½ΡΠΎΠ² ΡΠΎΡΠΌΠΎΠ·Π½ΡΡ ΠΌΠ΅Ρ Π°Π½ΠΈΠ·ΠΌΠΎΠ². ΠΡΠ½ΠΎΠ²Π½Π°Ρ ΠΎΠΏΠ°ΡΠ½ΠΎΡΡΡ ΠΎΡΠΊΠ°Π·Π° ΡΠΎΡΠΌΠΎΠ·ΠΎΠ² β ΠΏΠ΅ΡΠ΅Π³ΡΠ΅Π²: ΠΏΠ°Ρ, ΠΎΠ±ΡΠ°Π·ΡΡΡΠΈΠΉΡΡ Π² ΡΠ΅Π·ΡΠ»ΡΡΠ°ΡΠ΅ ΡΡΠ΅Π½ΠΈΡ, ΠΌΠ΅ΡΠ°Π΅Ρ ΠΏΠΎΠ²ΡΡΠ΅Π½ΠΈΡ ΡΡΡΠ΅ΠΊΡΠΈΠ²Π½ΠΎΡΡΠΈ ΡΠΎΡΠΌΠΎΠ·Π½ΠΎΠΉ ΡΠΈΠ»Ρ. ΠΡΠΈ ΠΏΠ΅ΡΠ΅Π³ΡΠ΅Π²Π΅ ΡΠΎΡΠΌΠΎΠ·Π½ΠΎΠ³ΠΎ Π΄ΠΈΡΠΊΠ° ΠΎΠ½ Π΄Π΅ΡΠΎΡΠΌΠΈΡΡΠ΅ΡΡΡ (Π½Π°ΡΡΡΠ°Π΅ΡΡΡ ΡΠΎΡΠΌΠ° Π΅Π³ΠΎ ΠΏΠΎΠ²Π΅ΡΡ Π½ΠΎΡΡΠΈ), Π²ΡΠ»Π΅Π΄ΡΡΠ²ΠΈΠ΅ ΡΡΠΎΠ³ΠΎ ΠΏΡΠΎΠΈΡΡ ΠΎΠ΄ΠΈΡ Π±ΠΈΠ΅Π½ΠΈΠ΅ Π΄ΠΈΡΠΊΠ°, ΠΏΠ΅ΡΠ΅Π΄Π°ΡΡΠ΅Π΅ΡΡ Π½Π° ΡΡΠ»Π΅Π²ΠΎΠ΅ ΠΊΠΎΠ»Π΅ΡΠΎ ΠΈ ΡΠΎΡΠΌΠΎΠ·Π½ΡΡ ΠΏΠ΅Π΄Π°Π»Ρ, ΠΈ ΡΠ°ΠΊΠΆΠ΅ ΡΠ΄Π»ΠΈΠ½ΡΠ΅ΡΡΡ ΡΠΎΡΠΌΠΎΠ·Π½ΠΎΠΉ ΠΏΡΡΡ ΠΌΠ°ΡΠΈΠ½Ρ. ΠΠΎΡΡΠΎΠΌΡ ΠΊ ΠΌΠ°ΡΠ΅ΡΠΈΠ°Π»Π°ΠΌ Π΄Π»Ρ ΠΏΡΠΎΠΈΠ·Π²ΠΎΠ΄ΡΡΠ²Π° ΡΠΎΡΠΌΠΎΠ·Π½ΡΡ ΡΠΈΡΡΠ΅ΠΌ ΠΏΡΠ΅Π΄ΡΡΠ²Π»ΡΡΡ ΠΎΡΠΎΠ±ΡΠ΅ ΡΡΠ΅Π±ΠΎΠ²Π°Π½ΠΈΡ: ΠΎΠ½ΠΈ Π½Π΅ Π΄ΠΎΠ»ΠΆΠ½Ρ ΠΈΡΡΠΈΡΠ°ΡΡΡΡ, Π΄Π΅ΡΠΎΡΠΌΠΈΡΠΎΠ²Π°ΡΡΡΡ, ΠΈ Π΄ΠΎΠ»ΠΆΠ½Ρ ΠΈΠΌΠ΅ΡΡ Π²ΡΡΠΎΠΊΡΡ ΡΠ΅ΡΠΌΠΎΡΡΠΎΠΉΠΊΠΎΡΡΡ.
Π 70-Ρ Π³ΠΎΠ΄Π°Ρ ΠΏΠΎΡΠ²Π»ΡΡΡΡΡ ΠΊΠ°ΡΠ±ΠΎΠ½ΠΎΠ²ΡΠ΅ ΡΠΎΡΠΌΠΎΠ·Π½ΡΠ΅ ΡΠΈΡΡΠ΅ΠΌΡ, ΠΊΠΎΡΠΎΡΡΠ΅ ΡΡΡΠ°Π½Π°Π²Π»ΠΈΠ²Π°Π»ΠΈΡΡ Π»ΠΈΡΡ Π½Π° ΡΠΏΠΎΡΡΠΈΠ²Π½ΡΠ΅ Π°Π²ΡΠΎ Π€ΠΎΡΠΌΡΠ»Ρ-1. Π’ΠΎΠ»ΡΠΊΠΎ Ρ 1998 Π³ΠΎΠ΄Π° ΠΊΠ°ΡΠ±ΠΎΠ½ΠΎ-ΠΊΠ΅ΡΠ°ΠΌΠΈΡΠ΅ΡΠΊΠΈΠ΅ ΡΠΎΡΠΌΠΎΠ·Π½ΡΠ΅ ΡΠΈΡΡΠ΅ΠΌΡ Π½Π°ΡΠ°Π»Π° ΡΡΡΠ°Π½Π°Π²Π»ΠΈΠ²Π°ΡΡ Π½Π° ΡΠ²ΠΎΠΈ Π°Π²ΡΠΎΠΌΠΎΠ±ΠΈΠ»ΠΈ ΠΊΠΎΠΌΠΏΠ°Π½ΠΈΡ Ferrari. ΠΠ΅ΡΠ°ΠΌΠΈΡΠ΅ΡΠΊΠΈΠ΅ ΡΠΎΡΠΌΠΎΠ·Π½ΡΠ΅ Π΄ΠΈΡΠΊΠΈ ΠΈΠ·Π³ΠΎΡΠΎΠ²Π»ΡΡΡΡΡ ΠΈΠ· ΠΊΠ°ΡΠ±ΠΎΡΡΠ½Π΄Π°, ΠΈΠ½ΡΠΌΠΈ ΡΠ»ΠΎΠ²Π°ΠΌΠΈ ΠΊΠ°ΡΠ±ΠΈΠ΄Π° ΠΊΡΠ΅ΠΌΠ½ΠΈΡ. Π’Π°ΠΊΠΈΠ΅ ΡΠΎΡΠΌΠΎΠ·Π° ΠΎΠΊΠ°Π·Π°Π»ΠΈΡΡ Π½Π°ΠΌΠ½ΠΎΠ³ΠΎ ΡΡΡΠ΅ΠΊΡΠΈΠ²Π½Π΅Π΅ ΡΡΠ³ΡΠ½Π½ΡΡ : ΠΎΠ½ΠΈ Π»Π΅Π³ΡΠ΅, ΠΊΠΎΡΡΡΠΈΡΠΈΠ΅Π½Ρ ΡΡΠ΅Π½ΠΈΡ Π²ΡΡΠ΅ Π½Π° ΠΏΠΎΡΡΠ΄ΠΎΠΊ, ΠΎΠ½ΠΈ Π½Π΅ ΠΊΠΎΡΠΎΠ±ΡΡΡΡ, ΡΠ°Π±ΠΎΡΠΈΠΉ Π΄ΠΈΠ°ΠΏΠ°Π·ΠΎΠ½ ΡΠ΅ΠΌΠΏΠ΅ΡΠ°ΡΡΡ 1200-1400ΠΎC; Π½ΠΎ ΠΎΠ½ΠΈ Π±ΠΎΠ»Π΅Π΅ Π΄ΠΎΡΠΎΠ³ΠΈΠ΅, ΠΈ Π½Π°ΡΠΈΠ½Π°ΡΡ ΡΠ°Π±ΠΎΡΠ°ΡΡ, Π»ΠΈΡΡ Ρ ΠΎΡΠΎΡΠΎ ΠΏΡΠΎΠ³ΡΠ΅Π²ΡΠΈΡΡ, Π° Π΄ΠΎ ΡΡΠΎΠ³ΠΎ ΠΊΠΎΡΡΡΠΈΡΠΈΠ΅Π½Ρ ΡΡΠ΅Π½ΠΈΡ ΠΈΡ Π΅ΡΠ΅ Π½ΠΈΠΆΠ΅ ΠΎΠ±ΡΡΠ½ΡΡ .
ΠΡΠ½ΠΎΠ²Π½ΡΠ΅ ΠΏΡΠ΅ΠΈΠΌΡΡΠ΅ΡΡΠ²Π° ΠΈ Π½Π΅Π΄ΠΎΡΡΠ°ΡΠΊΠΈ
ΠΠΎΠΆΠ½ΠΎ Π²ΡΠ΄Π΅Π»ΠΈΡΡ ΡΠ°ΠΊΠΈΠ΅ ΠΎΡΠ½ΠΎΠ²Π½ΡΠ΅ ΠΏΡΠ΅ΠΈΠΌΡΡΠ΅ΡΡΠ²Π° ΠΊΠ΅ΡΠ°ΠΌΠΈΡΠ΅ΡΠΊΠΈΡ ΡΠΎΡΠΌΠΎΠ·Π½ΡΡ ΡΠΈΡΡΠ΅ΠΌ:
1. ΠΠ°ΠΆΠ΅ ΠΏΡΠΈ ΠΈΠ½ΡΠ΅Π½ΡΠΈΠ²Π½ΠΎΠΉ ΡΠ°Π±ΠΎΡΠ΅ ΠΊΠ΅ΡΠ°ΠΌΠΈΡΠ΅ΡΠΊΠΈΠΉ Π΄ΠΈΡΠΊ Π½Π΅ ΠΊΠΎΡΠΎΠ±ΠΈΡΡΡ, Π² ΠΎΡΠ»ΠΈΡΠΈΠ΅ ΠΎΡ ΠΌΠ΅ΡΠ°Π»Π»ΠΈΡΠ΅ΡΠΊΠΈΡ Π΄ΠΈΡΠΊΠΎΠ².
2. ΠΠ°Π½Π½ΡΠ΅ ΡΠΎΡΠΌΠΎΠ·Π½ΡΠ΅ Π΄ΠΈΡΠΊΠΈ ΡΡΠ°Π±ΠΈΠ»ΡΠ½Ρ Π² ΡΠ°Π±ΠΎΡΠ΅ Π² ΡΠΈΡΠΎΠΊΠΎΠΌ Π΄ΠΈΠ°ΠΏΠ°Π·ΠΎΠ½Π΅ ΡΠ΅ΠΌΠΏΠ΅ΡΠ°ΡΡΡ (1200-1400ΠΎC), Π° ΡΡΠΎ Π³ΠΎΠ²ΠΎΡΠΈΡ ΠΎ ΡΠΎΠΌ, ΡΡΠΎ ΡΠ°Π·Π»ΠΈΡΠ½ΡΠ΅ ΠΏΠΎΠ³ΠΎΠ΄Π½ΡΠ΅ ΡΡΠ»ΠΎΠ²ΠΈΡ Π±ΡΠ΄ΡΡ Π½Π΅ΡΡΡΠ΅ΡΡΠ²Π΅Π½Π½ΠΎ Π²Π»ΠΈΡΡΡ Π½Π° ΡΠ°Π±ΠΎΡΡ ΡΠΎΡΠΌΠΎΠ·Π½ΠΎΠ³ΠΎ Π΄ΠΈΡΠΊΠ°, ΡΠ°Π·ΠΎΠ³ΡΠ΅ΡΠΎΠ³ΠΎ Π΄ΠΎ Π½Π΅ΠΎΠ±Ρ
ΠΎΠ΄ΠΈΠΌΠΎΠΉ ΡΠ΅ΠΌΠΏΠ΅ΡΠ°ΡΡΡΡ.
3. ΠΠ΅ΡΠ°ΠΌΠΈΡΠ΅ΡΠΊΠΈΠΌ ΡΠΎΡΠΌΠΎΠ·Π½ΡΠΌ ΡΠΈΡΡΠ΅ΠΌΠ°ΠΌ Ρ Π°ΡΠ°ΠΊΡΠ΅ΡΠ΅Π½ ΠΌΠΈΠ½ΠΈΠΌΠ°Π»ΡΠ½ΡΠΉ Π²ΡΠ±ΡΠΎΡ ΠΏΡΠ»ΠΈ, Π±Π»Π°Π³ΠΎΠ΄Π°ΡΡ ΡΠ΅ΠΌΡ Π½Π΅ ΡΠ½ΠΈΠΆΠ°ΡΡΡΡ ΡΠΎΡΠΌΠΎΠ·Π½ΡΠ΅ Ρ Π°ΡΠ°ΠΊΡΠ΅ΡΠΈΡΡΠΈΠΊΠΈ Π°Π²ΡΠΎΠΌΠΎΠ±ΠΈΠ»Ρ.
4. ΠΠ΅ΡΠ°ΠΌΠΈΡΠ΅ΡΠΊΠΈΠΉ ΡΠΎΡΠΌΠΎΠ·Π½ΠΎΠΉ Π΄ΠΈΡΠΊ Π½Π° 50% Π»Π΅Π³ΡΠ΅ ΠΌΠ΅ΡΠ°Π»Π»ΠΈΡΠ΅ΡΠΊΠΎΠ³ΠΎ, ΠΈ ΠΊΠ΅ΡΠ°ΠΌΠΈΡΠ΅ΡΠΊΠ°Ρ ΡΠΎΡΠΌΠΎΠ·Π½Π°Ρ ΡΠΈΡΡΠ΅ΠΌΠ° ΠΌΠΎΠΆΠ΅Ρ ΡΠΌΠ΅Π½ΡΡΠΈΡΡ ΠΌΠ°ΡΡΡ ΠΌΠ°ΡΠΈΠ½Ρ Π½Π° 20 ΠΊΠ³, ΡΠ»Π΅Π΄ΠΎΠ²Π°ΡΠ΅Π»ΡΠ½ΠΎ, ΡΠΌΠ΅Π½ΡΡΠ°Π΅ΡΡΡ ΠΈ Π½Π΅ΠΏΠΎΠ΄ΡΠ΅ΡΡΠΎΡΠ΅Π½Π½Π°Ρ ΠΌΠ°ΡΡΠ°, Π° ΡΠ°ΠΊΠΆΠ΅ Π½Π°Π³ΡΡΠ·ΠΊΠ° Π½Π° ΠΏΠΎΠ΄Π²Π΅ΡΠΊΡ.
5. ΠΡΠΏΠΎΠ»ΡΠ·ΠΎΠ²Π°Π½ΠΈΠ΅ ΠΊΠ΅ΡΠ°ΠΌΠΈΡΠ΅ΡΠΊΠΈΡ ΡΠΎΡΠΌΠΎΠ·ΠΎΠ² Π΄Π°Π΅Ρ Π²ΠΎΠ·ΠΌΠΎΠΆΠ½ΠΎΡΡΡ ΠΏΠΎΠ²ΡΡΠΈΡΡ Π½Π° 25% ΠΊΠΎΡΡΡΠΈΡΠΈΠ΅Π½Ρ ΡΡΠ΅Π½ΠΈΡ ΠΈ ΡΠ²Π΅Π»ΠΈΡΠΈΡΡ ΡΠ΅Π·ΡΠ»ΡΡΠ°ΡΠΈΠ²Π½ΠΎΡΡΡ ΡΠΎΡΠΌΠΎΠΆΠ΅Π½ΠΈΡ Π² Π½Π°Π³ΡΠ΅ΡΠΎΠΌ ΡΠΎΡΡΠΎΡΠ½ΠΈΠΈ Π΄ΠΎ Π²ΡΡΠΎΠΊΠΈΡ ΡΠ΅ΠΌΠΏΠ΅ΡΠ°ΡΡΡ.
6. ΠΡΠ΅ ΠΊΠ΅ΡΠ°ΠΌΠΈΡΠ΅ΡΠΊΠΈΠ΅ Π΄ΠΈΡΠΊΠΈ Π΄ΠΎΠ»Π³ΠΎΠ²Π΅ΡΠ½Ρ, ΠΈ ΠΈΡ Π½Π΅ ΡΡΠ΅Π±ΡΠ΅ΡΡΡ ΠΌΠ΅Π½ΡΡΡ Π½Π° ΠΏΡΠΎΡΡΠΆΠ΅Π½ΠΈΠΈ 300 ΡΡΡ. ΠΊΠΌ.
ΠΠ΅ΡΠ°ΠΌΠΈΡΠ΅ΡΠΊΠΈΠ΅ ΠΊΠΎΠ»ΠΎΠ΄ΠΊΠΈ ΠΈΠΌΠ΅ΡΡ Π½Π΅ ΡΠΎΠ»ΡΠΊΠΎ ΠΏΠ»ΡΡΡ, Π½ΠΎ ΠΈ ΠΌΠΈΠ½ΡΡΡ:
1. ΠΠ°ΡΠ±ΠΎΠ½ΠΎ-ΠΊΠ΅ΡΠ°ΠΌΠΈΡΠ΅ΡΠΊΠΈΠ΅ ΡΠΎΡΠΌΠΎΠ·Π½ΡΠ΅ Π΄ΠΈΡΠΊΠΈ ΠΏΠ»ΠΎΡ ΠΎ ΡΠ°Π±ΠΎΡΠ°ΡΡ Π² Ρ ΠΎΠ»ΠΎΠ΄Π½ΠΎΠΌ ΡΠΎΡΡΠΎΡΠ½ΠΈΠΈ, ΠΎΡΡΠ°Π½Π°Π²Π»ΠΈΠ²Π°ΡΡ Π°Π²ΡΠΎΠΌΠΎΠ±ΠΈΠ»Ρ Π΄Π°ΠΆΠ΅ Ρ ΡΠΆΠ΅, ΡΠ΅ΠΌ Ρ ΠΎΠ»ΠΎΠ΄Π½ΡΠ΅ ΠΌΠ΅ΡΠ°Π»Π»ΠΈΡΠ΅ΡΠΊΠΈΠ΅ Π΄ΠΈΡΠΊΠΈ.
2. ΠΠΎΠ³ΡΡ ΠΈΠ·Π΄Π°Π²Π°ΡΡ ΠΏΡΠΈ ΡΠ°Π±ΠΎΡΠ΅ Π½Π΅ΠΏΡΠΈΡΡΠ½ΡΠΉ ΡΠΊΡΠΈΠΏ (Π½ΠΎ ΠΎΠ½ ΡΡΡΡΠ°Π½ΡΠ΅ΡΡΡ Π΄ΠΎΠ±Π°Π²Π»Π΅Π½ΠΈΠ΅ΠΌ Π² ΡΠΎΡΡΠ°Π² Π΄ΠΈΡΠΊΠΎΠ² ΡΠ°Π·Π½ΠΎΠΎΠ±ΡΠ°Π·Π½ΡΡ ΠΌΠ΅ΡΠ°Π»Π»ΠΈΡΠ΅ΡΠΊΠΈΡ ΠΏΡΠΈΠΌΠ΅ΡΠ΅ΠΉ).
3. ΠΠ»Π°Π²Π½ΡΠΌ Π½Π΅Π΄ΠΎΡΡΠ°ΡΠΊΠΎΠΌ ΠΊΠ΅ΡΠ°ΠΌΠΈΡΠ΅ΡΠΊΠΎΠΉ ΡΠΎΡΠΌΠΎΠ·Π½ΠΎΠΉ ΡΠΈΡΡΠ΅ΠΌΡ ΡΠ²Π»ΡΠ΅ΡΡΡ Π΅Π΅ ΡΠ΅Π½Π°.
ΠΡΠ΅Π΄ΡΡ Π»ΠΈ ΠΊΠΎΠ»ΠΎΠ΄ΠΊΠΈ ΠΈΠ· ΠΊΠ΅ΡΠ°ΠΌΠΈΠΊΠΈ ΡΠΎΡΠΌΠΎΠ·Π½ΠΎΠΌΡ Π΄ΠΈΡΠΊΡ
Π ΡΠ΅Π·ΡΠ»ΡΡΠ°ΡΠ΅ ΠΌΠ½ΠΎΠ³ΠΈΡ
ΠΈΡΠΏΡΡΠ°Π½ΠΈΠΉ Π½Π΅ Π±ΡΠ»ΠΎ ΠΎΠ±Π½Π°ΡΡΠΆΠ΅Π½ΠΎ, ΡΡΠΎ ΠΊΠ΅ΡΠ°ΠΌΠΈΡΠ΅ΡΠΊΠΈΠ΅ ΠΊΠΎΠ»ΠΎΠ΄ΠΊΠΈ ΠΌΠ°Π»ΠΎΡΡΡΠ΅ΠΊΡΠΈΠ²Π½ΠΎ ΡΠ°Π±ΠΎΡΠ°ΡΡ Π½Π° ΡΠΎΡΠΌΠΎΠ·Π½ΡΡ
Π΄ΠΈΡΠΊΠ°Ρ
. Π’ΠΎΡΠΌΠΎΠ·Π½ΡΠ΅ ΠΊΠΎΠ»ΠΎΠ΄ΠΊΠΈ ΠΈΠ· ΠΊΠ΅ΡΠ°ΠΌΠΈΠΊΠΈ Π½Π΅ ΡΠΎΠ΄Π΅ΡΠΆΠ°Ρ Π² ΡΠ²ΠΎΠ΅ΠΌ ΡΠΎΡΡΠ°Π²Π΅ ΡΠ΅ΡΡΠΎΡΠΏΠ»Π°Π²ΠΎΠ², ΠΈ Π±Π»Π°Π³ΠΎΠ΄Π°ΡΡ ΡΡΠΎΠΌΡ Π½Π΅ ΠΏΡΠΎΠΈΡΡ
ΠΎΠ΄ΠΈΡ ΠΊΠΎΠ½ΡΠ°ΠΊΡ ΠΌΠ΅ΡΠ°Π»Π»ΠΎΠ² ΠΌΠ΅ΠΆΠ΄Ρ ΠΊΠΎΠ»ΠΎΠ΄ΠΊΠ°ΠΌΠΈ ΠΈ Π΄ΠΈΡΠΊΠΎΠΌ, Π°, ΡΠ»Π΅Π΄ΠΎΠ²Π°ΡΠ΅Π»ΡΠ½ΠΎ, Π½Π΅Ρ ΠΏΠΎΠ²ΡΡΠ΅Π½Π½ΠΎΠ³ΠΎ ΠΈΠ·Π½ΠΎΡΠ° ΡΠΎΡΠΌΠΎΠ·Π½ΠΎΠ³ΠΎ Π΄ΠΈΡΠΊΠ° ΠΈ Β«Π·Π°Π»ΠΈΠΏΠ°Π½ΠΈΡΒ» ΠΏΠΎΠ²Π΅ΡΡ
Π½ΠΎΡΡΠ΅ΠΉ.
ΠΠΏΡΠ΅Π΄Π΅Π»ΡΠ΅ΠΌΡΡ Ρ Π²ΡΠ±ΠΎΡΠΎΠΌ: ΠΊΠ΅ΡΠ°ΠΌΠΈΡΠ΅ΡΠΊΠΈΠ΅ ΠΊΠΎΠ»ΠΎΠ΄ΠΊΠΈ ΠΈΠ»ΠΈ ΠΌΠ΅ΡΠ°Π»Π»ΠΈΡΠ΅ΡΠΊΠΈΠ΅
ΠΠ΅ΡΠ°ΠΌΠΈΡΠ΅ΡΠΊΠΈΠ΅ ΠΊΠΎΠ»ΠΎΠ΄ΠΊΠΈ ΠΎΠΏΡΠΈΠΌΠ°Π»ΡΠ½Ρ Π΄Π»Ρ Π°Π³ΡΠ΅ΡΡΠΈΠ²Π½ΠΎΠ³ΠΎ Π²ΠΎΠΆΠ΄Π΅Π½ΠΈΡ: ΠΊΠ΅ΡΠ°ΠΌΠΈΠΊΠ° ΠΈΠ·Π±Π°Π²ΠΈΡ ΠΎΡ ΠΎΠ±ΡΠ°Π·ΠΎΠ²Π°Π½ΠΈΡ ΠΎΡΡΠ°Π±ΠΎΡΠ°Π½Π½ΠΎΠΉ ΠΏΡΠ»ΠΈ, ΠΏΠΎΠ·Π²ΠΎΠ»ΠΈΡ Π΄ΠΎΠ»ΡΡΠ΅ ΡΠΊΡΠΏΠ»ΡΠ°ΡΠΈΡΠΎΠ²Π°ΡΡ ΡΠΎΡΠΌΠΎΠ·Π½ΡΠ΅ Π΄ΠΈΡΠΊΠΈ ΠΈ ΠΈΠΌΠ΅Π΅Ρ ΠΌΠ½ΠΎΠ³ΠΎ Π΄ΡΡΠ³ΠΈΡ ΠΏΡΠ΅ΠΈΠΌΡΡΠ΅ΡΡΠ², Π½ΠΎ ΠΎΠ½ΠΈ ΠΎΡΠ΅Π½Ρ Π΄ΠΎΡΠΎΠ³ΠΈΠ΅ Π΄Π»Ρ ΠΎΠ±ΡΡΠ½ΡΡ Π²ΠΎΠ΄ΠΈΡΠ΅Π»Π΅ΠΉ.
ΠΠΏΠΎΠ»Π½Π΅ ΠΎΡΠ΅Π²ΠΈΠ΄Π½ΠΎ, ΡΡΠΎ ΠΊΠ΅ΡΠ°ΠΌΠΈΡΠ΅ΡΠΊΠΈΠ΅ ΡΠΎΡΠΌΠΎΠ·Π½ΡΠ΅ ΠΊΠΎΠ»ΠΎΠ΄ΠΊΠΈ Π² Π±Π»ΠΈΠΆΠ°ΠΉΡΠ΅Π΅ Π²ΡΠ΅ΠΌΡ Π½Π΅ Π±ΡΠ΄ΡΡ ΠΏΡΠΈΠΌΠ΅Π½ΡΡΡΡΡ Π½Π° ΠΌΠ°ΡΠΈΠ½Π°Ρ
ΠΌΠ°ΡΡΠΎΠ²ΠΎΠ³ΠΎ ΠΏΡΠΎΠΈΠ·Π²ΠΎΠ΄ΡΡΠ²Π°, Π²ΠΎΠ΄ΠΈΡΠ΅Π»ΠΈ ΡΠ²ΠΎΠ΅ ΠΏΡΠ΅Π΄ΠΏΠΎΡΡΠ΅Π½ΠΈΠ΅ Π±ΡΠ΄ΡΡ ΠΎΡΠ΄Π°Π²Π°ΡΡ ΠΌΠ΅ΡΠ°Π»Π»ΠΈΡΠ΅ΡΠΊΠΈΠΌ; Π½ΠΎ ΡΠΏΠΎΡΡΠΈΠ²Π½ΡΠΌ Π°Π²ΡΠΎΠΌΠΎΠ±ΠΈΠ»ΡΠΌ ΠΎΠ½ΠΈ ΠΏΡΠΎΡΡΠΎ Π½Π΅ΠΎΠ±Ρ
ΠΎΠ΄ΠΈΠΌΡ, ΡΠ°ΠΊ ΠΊΠ°ΠΊ ΠΌΠΎΠ³ΡΡ Π·Π½Π°ΡΠΈΡΠ΅Π»ΡΠ½ΠΎ ΡΠΎΠΊΡΠ°ΡΠΈΡΡ ΡΠΎΡΠΌΠΎΠ·Π½ΠΎΠΉ ΠΏΡΡΡ.
ΠΠΎΠ΄ΠΏΠΈΡΡΠ²Π°ΠΉΡΠ΅ΡΡ Π½Π° Π½Π°ΡΠΈ Π»Π΅Π½ΡΡ Π² ΡΠ°ΠΊΠΈΡ ΡΠΎΡΠΈΠ°Π»ΡΠ½ΡΡ ΡΠ΅ΡΡΡ ΠΊΠ°ΠΊ, Facebook, ΠΠΊΠΎΠ½ΡΠ°ΠΊΡΠ΅ ΠΈ Instagram: Π²ΡΠ΅ ΡΠ°ΠΌΡΠ΅ ΠΈΠ½ΡΠ΅ΡΠ΅ΡΠ½ΡΠ΅ Π°Π²ΡΠΎΠΌΠΎΠ±ΠΈΠ»ΡΠ½ΡΠ΅ ΡΠΎΠ±ΡΡΠΈΡ ΡΠΎΠ±ΡΠ°Π½Π½ΡΠ΅ Π² ΠΎΠ΄Π½ΠΎΠΌ ΠΌΠ΅ΡΡΠ΅.
ΠΡΡΠΎΡΠ½ΠΈΠΊ auto.today
ΠΠ²ΠΎΠ»ΡΡΠΈΡ ΡΠΎΡΠΌΠΎΠ·Π½ΡΡ Π΄ΠΈΡΠΊΠΎΠ² Ρ ΡΠΎΡΠΊΠΈ Π·ΡΠ΅Π½ΠΈΡ ΡΡΡΠ΅ΠΊΡΠΈΠ²Π½ΠΎΡΡΠΈ
Π ΠΎΡΡΠ°ΡΠ»ΠΈ Π°Π²ΡΠΎΠΌΠΎΠ±ΠΈΠ»Π΅ΡΡΡΠΎΠ΅Π½ΠΈΡ Π²Π½Π΅Π΄ΡΠ΅Π½ΠΈΠ΅ Π΄ΠΈΡΠΊΠΎΠ²ΠΎΠΉ ΡΠΎΡΠΌΠΎΠ·Π½ΠΎΠΉ ΡΠΈΡΡΠ΅ΠΌΡ β ΡΡΠΎ Π½Π΅ΠΊΠ°Ρ ΠΎΡΠΏΡΠ°Π²Π½Π°Ρ ΡΠΎΡΠΊΠ°, ΠΊΠΎΡΠΎΡΠ°Ρ ΡΠ°Π·Π΄Π΅Π»ΠΈΠ»Π° ΡΡΠ΅ΡΡ Π½Π° ΠΠ ΠΈ ΠΠΠ‘ΠΠ, ΠΏΠΎΡΠ»Π΅ Π²Π½Π΅Π΄ΡΠ΅Π½ΠΈΡ βΠ½Π°ΡΠ°Π»ΡΡ Π½ΠΎΠ²Π°Ρ Π²Π΅Ρ Π°. Π‘ ΡΠΎΠ³ΠΎ ΠΌΠΎΠΌΠ΅Π½ΡΠ°, ΠΊΠ°ΠΊ Π΄ΠΈΡΠΊΠΎΠ²Π°Ρ ΡΠΈΡΡΠ΅ΠΌΠ° ΡΡΠ°Π»Π° ΡΡΡΠ°Π½Π°Π²Π»ΠΈΠ²Π°ΡΡΡΡ ΡΠ΅ΡΠΈΠΉΠ½ΠΎ β ΠΎΠ±ΡΠ»ΡΠΆΠΈΠ²Π°Π½ΠΈΠ΅ ΡΠΎΡΠΌΠΎΠ·ΠΎΠ² ΠΈ ΡΠ°ΠΌΠΎ ΡΠΎΡΠΌΠΎΠΆΠ΅Π½ΠΈΠ΅ ΡΠΈΠ»ΡΠ½ΠΎ ΠΈΠ·ΠΌΠ΅Π½ΠΈΠ»ΠΈΡΡ. Π£ΡΠ»ΠΎΠ²Π½ΠΎ Π³ΠΎΠ²ΠΎΡΡ, Ρ 1953 Π³ΠΎΠ΄Π° Π½Π°ΡΠ°Π»ΡΡ ΠΏΠ΅ΡΠΈΠΎΠ΄ ΡΠ²ΠΎΠ»ΡΡΠΈΠΈ ΡΠΎΡΠΌΠΎΠ·Π½ΡΡ ΠΊΠΎΠΌΠΏΠΎΠ½Π΅Π½ΡΠΎΠ². Π ΡΠ°ΡΡΠ½ΠΎΡΡΠΈ, ΡΠΎΡΠΌΠΎΠ·Π½ΡΡ Π΄ΠΈΡΠΊΠΎΠ².
ΠΠ»Π°ΡΡΠΈΡΠ΅ΡΠΊΠΈΠΉ ΡΠΎΡΠΌΠΎΠ·Π½ΠΎΠΉ Π΄ΠΈΡΠΊ ΠΈΠ·Π³ΠΎΡΠ°Π²Π»ΠΈΠ²Π°Π΅ΡΡΡ ΠΈΠ· ΡΠ΅ΡΠΎΠ³ΠΎ ΡΡΠ³ΡΠ½Π°. ΠΠΎΡΠ΅ΠΌΡ ΡΡΠ³ΡΠ½? ΠΠΎΡΠΎΠΌΡ ΡΡΠΎ, Π² ΠΎΡΠ»ΠΈΡΠΈΠΈ ΠΎΡ ΡΡΠ°Π»ΠΈ ΠΈΠ»ΠΈ Π°Π»ΡΠΌΠΈΠ½ΠΈΡ, ΡΡΠΎΡ ΡΠΏΠ»Π°Π² ΠΎΠ±Π»Π°Π΄Π°Π΅Ρ ΠΏΡΠ΅ΠΊΡΠ°ΡΠ½ΠΎΠΉ ΡΠ΅ΠΏΠ»ΠΎΠΏΡΠΎΠ²ΠΎΠ΄Π½ΠΎΡΡΡΡ ΠΈ ΡΠ»Π°ΡΡΠΈΡΠ½ΠΎΡΡΡΡ Π΄Π»Ρ Π²ΡΠΏΠ»Π°Π²ΠΊΠΈ ΡΠ»ΠΎΠΆΠ½ΡΡ ΡΠΎΡΠΌ. ΠΠ° ΡΠ°ΠΌΠΎΠΌ Π΄Π΅Π»Π΅, ΡΠΆΠ΅ Π΄Π°Π²Π½ΠΎ ΡΡΡΠ΅ΡΡΠ²ΡΠ΅Ρ ΠΌΠ½ΠΎΠ³ΠΎ ΡΠ°Π·Π»ΠΈΡΠ½ΡΡ ΠΏΡΠΎΠ΅ΠΊΡΠΎΠ² ΠΏΠΎ ΠΏΡΠΎΠΈΠ·Π²ΠΎΠ΄ΡΡΠ²Ρ ΠΊΠΎΠΌΠΏΠΎΠ½Π΅Π½ΡΠΎΠ² ΠΈΠ· Π°Π»ΡΠΌΠΈΠ½ΠΈΡ, ΡΡΠ°Π»ΠΈ ΠΈ Π΄ΡΡΠ³ΠΈΡ ΡΠΎΡΡΠ°Π²ΠΎΠ², Π½ΠΎ ΠΏΠΎΠΊΠ° ΡΡΠΎ Π·Π°Π²ΠΎΠ΄Ρ β ΠΏΡΠΎΠΈΠ·Π²ΠΎΠ΄ΠΈΡΠ΅Π»ΠΈ Π°Π²ΡΠΎ Π½Π΅ ΡΠΏΠ΅ΡΠ°Ρ ΠΈΡΠΊΠ°ΡΡ Π·Π°ΠΌΠ΅Π½Ρ. ΠΠΎΡΡΠΎΠΌΡ Π½Π° ΡΠ΅Π³ΠΎΠ΄Π½ΡΡΠ½ΠΈΠΉ Π΄Π΅Π½Ρ 99% Π°Π²ΡΠΎΠΌΠΎΠ±ΠΈΠ»Π΅ΠΉ ΠΎΡΠ½Π°ΡΠ°ΡΡΡΡ ΠΈΠΌΠ΅Π½Π½ΠΎ ΡΡΠ³ΡΠ½Π½ΡΠΌΠΈ ΡΠΎΡΠΌΠΎΠ·Π½ΡΠΌΠΈ Π΄ΠΈΡΠΊΠ°ΠΌΠΈ.
ΠΠ°ΡΠΈΠ½Π°Ρ Ρ ΠΏΠ΅ΡΠ²ΡΡ Π΄Π½Π΅ΠΉ Π·Π°ΠΏΡΡΠΊΠ° ΡΠ΅Ρ Π½ΠΎΠ»ΠΎΠ³ΠΈΠΈ Π½Π° ΠΊΠΎΠ½Π²Π΅ΠΉΠ΅Ρ ΡΠΎΡΠΌΠΎΠ·Π½ΠΎΠΉ Π΄ΠΈΡΠΊ ΠΏΡΠ΅ΡΠ΅ΡΠΏΠ΅Π» Π½Π΅ΠΌΠ°Π»ΠΎ ΠΈΠ·ΠΌΠ΅Π½Π΅Π½ΠΈΠΉ, Π² ΠΏΠΎΠΏΡΡΠΊΠ°Ρ ΠΏΠΎΠ²ΡΡΠΈΡΡ ΡΡΡΠ΅ΠΊΡΠΈΠ²Π½ΠΎΡΡΡ ΡΠΎΡΠΌΠΎΠΆΠ΅Π½ΠΈΡ. ΠΠ²ΠΎΠ»ΡΡΠΈΡ ΡΡΠΈΡ ΠΎΠΏΡΠΈΠΉ ΠΌΡ ΡΠ΅Π³ΠΎΠ΄Π½Ρ ΡΠ°ΡΡΠΌΠΎΡΡΠΈΠΌ.
ΠΡΠ°ΠΊ, Π²Π΅Π½ΡΠΈΠ»ΠΈΡΡΠ΅ΠΌΡΠΉ ΡΠΎΡΠΌΠΎΠ·Π½ΠΎΠΉ Π΄ΠΈΡΠΊ β ΡΡΠΎ ΠΊΠΎΠ½ΡΡΡΡΠΊΡΠΈΡ, ΡΠΎΡΡΠΎΡΡΠ°Ρ ΠΈΡ Π΄Π²ΡΡ ΠΏΠ»Π°ΡΡΠΈΠ½, Ρ Π²Π΅Π½ΡΠΈΠ»ΡΡΠΈΠΎΠ½Π½ΡΠΌΠΈ ΠΊΠ°Π½Π°Π»Π°ΠΌΠΈ ΠΌΠ΅ΠΆΠ΄Ρ Π½ΠΈΠΌΠΈ. ΠΠ°ΠΊ ΡΠ»Π΅Π΄ΡΠ΅Ρ ΠΈΠ· Π½Π°Π·Π²Π°Π½ΠΈΡ, ΠΎΡΠ½ΠΎΠ²Π½Π°Ρ ΡΠΌΡΡΠ»ΠΎΠ²Π°Ρ Π½Π°Π³ΡΡΠ·ΠΊΠ° ΡΡΠΎΠΉ ΡΠ°Π·ΡΠ°Π±ΠΎΡΠΊΠΈ β ΡΠ»ΡΡΡΠΈΡΡ ΠΎΡ Π»Π°ΠΆΠ΄Π°Π΅ΠΌΠΎΡΡΡ Π² ΡΠ΅ΠΆΠΈΠΌΠ΅ ΡΠ΅ΠΏΠ»ΠΎΠ²ΡΡ Π½Π°Π³ΡΡΠ·ΠΎΠΊ. ΠΡΠ΄Π΅ΠΌ ΡΡΠΈΡΠ°ΡΡ ΡΠ°ΠΊΠΎΠΉ Π²Π΅Π½ΡΠΈΠ»ΠΈΡΡΠ΅ΠΌΡΠΉ Π΄ΠΈΡΠΊ ΡΠΎΡΠΊΠΎΠΉ ΠΎΡΡΡΠ΅ΡΠ° Π½Π°ΡΠΈΡ Π½Π°Π±Π»ΡΠ΄Π΅Π½ΠΈΠΉ.
1. Π ΠΈΡΡΠ½ΠΎΠΊ Π²Π΅Π½ΡΠΈΠ»ΡΡΠΈΠΎΠ½Π½ΡΡ ΡΠ°Ρ Ρ Π΄ΠΈΡΠΊΠΎΠ².
Π§Π°ΡΠ΅ ΠΎΠΏΡΠΈΡ, Ρ
ΠΎΡΡ Π΄Π»Ρ Π½Π΅ΠΊΠΎΡΠΎΡΡΡ
ΠΌΠΎΠ΄Π΅Π»Π΅ΠΉ ΡΡΠΎ ΠΊΠΎΠ½Π²Π΅ΠΉΠ΅ΡΠ½ΠΎΠ΅ ΡΠ΅ΡΠ΅Π½ΠΈΠ΅. Π Π±Π°Π·ΠΎΠ²ΠΎΠΌ ΠΈΡΠΏΠΎΠ»Π½Π΅Π½ΠΈΠΈ β Π²Π΅Π½ΡΠΈΠ»ΡΡΠΈΠΎΠ½Π½ΡΠ΅ ΠΊΠ°Π½Π°Π»Ρ Π²Π½ΡΡΡΠΈ Π΄ΠΈΡΠΊΠΎΠ² ΠΈΠΌΠ΅ΡΡ Π»ΡΡΠ΅ΠΎΠ±ΡΠ°Π·Π½ΡΡ ΡΠΎΡΠΌΡ, Π½Π°ΠΏΡΠ°Π²Π»Π΅Π½Π½ΡΡ ΠΎΡ ΡΠ΅Π½ΡΡΠ° ΠΊ Π²Π½Π΅ΡΠ½Π΅ΠΌΡ ΠΊΡΠ°Ρ. ΠΠΎ Π²ΡΠ΅ΠΌΡ Π²ΡΠ°ΡΠ΅Π½ΠΈΡ Π΄ΠΈΡΠΊΠ° ΡΠ΅Π½ΡΡΠΎΠ±Π΅ΠΆΠ½Π°Ρ ΡΠΈΠ»Π° Π²ΡΡΠ°Π»ΠΊΠΈΠ²Π°Π΅Ρ Π³ΠΎΡΡΡΠΈΠΉ Π²ΠΎΠ·Π΄ΡΡ
Π½Π°ΡΡΠΆΡ, ΡΠ½ΠΈΠΆΠ°Ρ Π·Π° ΡΡΠ΅Ρ ΡΠ΅ΠΏΠ»ΠΎΠΎΠ±ΠΌΠ΅Π½Π° ΡΠ΅ΠΌΠΏΠ΅ΡΠ°ΡΡΡΡ Π±ΠΎΠ»Π²Π°Π½ΠΊΠΈ. ΠΡΠΎ Π±Π°Π·ΠΎΠ²Π°Ρ Π²Π΅Π½ΡΠΈΠ»ΡΡΠΈΡ. ΠΠΏΡΠΈΡ ΠΆΠ΅ ΠΏΡΠ΅Π΄Π»Π°Π³Π°Π΅Ρ ΠΎΡΠ½Π°ΡΠ΅Π½ΠΈΠ΅ ΡΠ°Π΄ΠΈΠ°Π»ΡΠ½ΠΎ Π½Π°ΠΏΡΠ°Π²Π»Π΅Π½Π½ΡΠΌΠΈ ΠΊΠ°Π½Π°Π»Π°ΠΌΠΈ ΠΈΠ·ΠΎΠ³Π½ΡΡΠΎΠΉ ΡΠΎΡΠΌΡ, ΡΡΠΊΠΎΡΡΡΡΠΈΠΌΠΈ Π΄Π²ΠΈΠΆΠ΅Π½ΠΈΠ΅ Π²ΠΎΠ·Π΄ΡΡ
Π°. Π ΡΠΎΠΆΠ°Π»Π΅Π½ΠΈΡ, ΠΏΡΠΎΠΈΠ·Π²ΠΎΠ΄ΠΈΡΠ΅Π»ΠΈ Π½Π΅ Π·Π°ΡΠ²Π»ΡΡΡ ΠΊΠΎΠ½ΠΊΡΠ΅ΡΠ½ΡΡ
ΡΠΊΡΠΏΠ΅ΡΠΈΠΌΠ΅Π½ΡΠ°Π»ΡΠ½ΡΡ
ΠΏΠΎΠΊΠ°Π·Π°ΡΠ΅Π»Π΅ΠΉ ΡΡΡΠ΅ΠΊΡΠΈΠ²Π½ΠΎΡΡΠΈ ΡΠ°ΠΊΠΎΠΉ ΠΈΠ½Π½ΠΎΠ²Π°ΡΠΈΠΈ, Π½ΠΎ ΠΏΡΠ΅Π΄ΠΏΠΎΠ»Π°Π³Π°Π΅ΠΌ ΡΡΠΎ ΡΠΊΠΎΡΠΎΡΡΡ ΠΎΡ
Π»Π°ΠΆΠ΄Π΅Π½ΠΈΡ Π΄ΠΈΡΠΊΠ° ΡΠ²Π΅Π»ΠΈΡΠΈΡΡΡΡ Π½Π° 5-7%Ρ
ΠΡΠ΅Π½Ρ ΠΏΠΎΠΏΡΠ»ΡΡΠ½ΠΎΠ΅, Π½ΠΎ Π²ΠΌΠ΅ΡΡΠ΅ Ρ ΡΠ΅ΠΌ β ΠΈ ΡΠΏΠΎΡΠ½ΠΎΠ΅ ΡΠ΅ΡΠ΅Π½ΠΈΠ΅, ΠΏΠΎΡΠΎΠΆΠ΄Π°ΡΡΠ΅Π΅ Π½Π΅ΠΌΠ°Π»ΠΎ Π΄ΠΈΡΠΊΡΡΡΠΈΠΉ. Π‘ΡΡΡ ΠΎΠΏΡΠΈΠΈ β ΡΠ²Π΅ΡΠ»Π΅Π½ΠΈΠ΅ ΡΠΊΠ²ΠΎΠ·Π½ΡΡ ΠΎΡΠ²Π΅ΡΡΡΠΈΠΉ Π΄ΠΈΠ°ΠΌΠ΅ΡΡΠΎΠΌ 3,7-3,9 ΠΌΠΌ . ΠΠ»Π°Π²Π½ΠΎΠ΅ Π½Π°Π·Π½Π°ΡΠ΅Π½ΠΈΠ΅ β ΠΏΠΎΠ²ΡΡΠ΅Π½ΠΈΠ΅ ΠΈΠ½ΡΠ΅Π½ΡΠΈΠ²Π½ΠΎΡΡΠΈ ΠΎΡ Π»Π°ΠΆΠ΄Π΅Π½ΠΈΡ ΡΠΎΡΠΌΠΎΠ·ΠΎΠ². ΠΡΠ½ΠΎΠ²Π½ΡΠ΅ ΡΠΎΠΌΠ½Π΅Π½ΠΈΡ Ρ ΠΏΡΠΎΡΠΈΠ²Π½ΠΈΠΊΠΎΠ² ΡΠ°ΠΊΠΎΠΉ ΡΠ΅Ρ Π½ΠΎΠ»ΠΎΠ³ΠΈΠΈ β ΠΏΠΎΠ²ΡΡΠ΅Π½ΠΈΠ΅ Π½Π°ΠΏΡΡΠΆΠ΅Π½Π½ΠΎΡΡΠΈ Π²ΠΎΠΊΡΡΠ³ ΠΎΡΠ²Π΅ΡΡΡΠΈΠΉ ΠΏΠ΅ΡΡΠΎΡΠ°ΡΠΈΠΈ. Π ΡΠ΅ΠΌ Π½Π΅ ΠΌΠ΅Π½Π΅Π΅, ΠΏΠ΅ΡΡΠΎΡΠΈΡΠΎΠ²Π°Π½Π½ΡΠ΅ ΡΠΎΡΠΌΠΎΠ·Π½ΡΠ΅ Π΄ΠΈΡΠΊΠΈ ΡΡΠ°ΡΠ½ΠΎ ΡΡΡΠ°Π½Π°Π²Π»ΠΈΠ²Π°ΡΡ Mercedes, Porsche ΠΈ Π΄ΡΡΠ³ΠΈΠ΅.
ΠΡΡΠΎΠ΄ΠΈΠ½Π°ΠΌΠΈΡΠ΅ΡΠΊΠΈΠ΅ Π·Π°ΠΌΠ΅ΡΡ ΠΏΠΎΠΊΠ°Π·ΡΠ²Π°ΡΡ ΡΡΠΊΠΎΡΠ΅Π½ΠΈΠ΅ ΠΎΡ Π»Π°ΠΆΠ΄Π΅Π½ΠΈΡ Π΄ΠΈΡΠΊΠ° Π΄ΠΎ 15-18%.
ΠΠ΄Π½ΠΎ ΠΈΠ· ΡΡΡΠ΅ΠΊΡΠΈΠ²Π½ΡΡ ΠΈ Π΄Π΅ΠΉΡΡΠ²Π΅Π½Π½ΡΡ ΡΠ΅ΡΠ΅Π½ΠΈΠΉ Π·Π° Π²ΡΡ ΡΡΡ Π΄ΠΈΡΠΊΠΎΠ²ΠΎΠΉ ΡΠΈΡΡΠ΅ΠΌΡ. Π‘ΡΡΡ ΡΠ΅Ρ Π½ΠΎΠ»ΠΎΠ³ΠΈΠΈ Π² Π½Π°ΡΠ΅Π·Π°Π½ΠΈΠΈ ΡΠ°Π΄ΠΈΠ°Π»ΡΠ½ΠΎ Π½Π°ΠΏΡΠ°Π²Π»Π΅Π½Π½ΡΡ ΠΎΡ ΡΡΡΠΏΠΈΡΡ ΠΊ Π²Π½Π΅ΡΠ½Π΅ΠΌΡ ΡΠ°Π΄ΠΈΡΡΡ ΠΊΠ°Π½Π°Π²ΠΎΠΊ, Π³Π»ΡΠ±ΠΈΠ½ΠΎΠΉ Π΄ΠΎ 1 ΠΌΠΌ. Π€ΡΠ½ΠΊΡΠΈΠΉ Ρ ΡΠ°ΠΊΠΎΠ³ΠΎ ΡΠ΅ΡΠ΅Π½ΠΈΡ Π½Π΅ΡΠΊΠΎΠ»ΡΠΊΠΎ:
β ΠΎΡΠΈΡΠ΅Π½ΠΈΠ΅ (ΠΎΠ±Π½ΠΎΠ²Π»Π΅Π½ΠΈΠ΅) ΠΏΠΎΠ²Π΅ΡΡ Π½ΠΎΡΡΠΈ ΠΊΠΎΠ»ΠΎΠ΄ΠΎΠΊ
β ΡΡΡΠ΅ΠΊΡΠΈΠ²Π½ΡΠΉ ΠΈ Π±ΡΡΡΡΡΠΉ ΠΎΡΠ²ΠΎΠ΄ ΠΎΡ ΠΏΡΡΠ½Π° ΠΊΠΎΠ½ΡΠ°ΠΊΡΠ° Π²ΠΎΠ΄Ρ ΠΈ Π³ΡΡΠ·ΠΈ Π² ΠΏΡΠΎΡΠ΅ΡΡΠ΅ ΡΠΎΡΠΌΠΎΠΆΠ΅Π½ΠΈΡ
β ΠΏΠΎΠ²ΡΡΠ°Π΅ΡΡΡ ΠΊΠΎΡΡΡΠΈΡΠΈΠ΅Π½Ρ ΡΡΠ΅Π½ΠΈΡ ΠΏΠ°ΡΡ Β«Π΄ΠΈΡΠΊ-ΠΊΠΎΠ»ΠΎΠ΄ΠΊΠ°Β»
ΠΡΠΈ ΡΡΠΎΠΌ, Π²Π°ΠΆΠ½ΡΠΌ Π΄ΠΎΡΡΠΎΠΈΠ½ΡΡΠ²ΠΎΠΌ ΠΈΠ½Π½ΠΎΠ²Π°ΡΠΈΠΈ Π½Π°ΡΠ΅ΡΠ΅ΠΊ Π² ΡΠΎΠΌ, ΡΡΠΎ ΠΊΠΎΠ½ΡΡΡΡΠΊΡΠΈΡ Π΄ΠΈΡΠΊΠ° Π½Π΅ ΠΎΡΠ»Π°Π±Π»ΡΠ΅ΡΡΡ ΠΈ Π½Π΅Ρ ΡΠΈΡΠΊΠ° ΡΠ°ΡΡΡΠ΅ΡΠΊΠΈΠ²Π°Π½ΠΈΡ.
Π£ΡΠΈΡΡΠ²Π°Ρ ΡΠΎ, ΡΡΠΎ Π½Π°ΡΠ΅ΡΠΊΠΈ Π²ΡΠΏΠΎΠ»Π½ΡΡΡ ΡΠ°Π·Π½ΠΎΠΏΠ»Π°Π½ΠΎΠ²ΡΠ΅ ΡΡΠ½ΠΊΡΠΈΠΈ β ΡΡΡΠ΄Π½ΠΎ Π²ΡΡΡΠΈΡΠ°ΡΡ ΠΊΠΎΠ½ΠΊΡΠ΅ΡΠ½ΡΠ΅ ΠΏΠΎΠΊΠ°Π·Π°ΡΠ΅Π»ΠΈ.
4. ΠΠ²ΡΡΠΎΡΡΠ°Π²Π½ΡΠ΅ Π΄ΠΈΡΠΊΠΈ.
ΠΡΠ΅Π½Ρ ΠΏΠ΅ΡΡΠΏΠ΅ΠΊΡΠΈΠ²Π½ΠΎΠ΅ ΠΈ ΡΡΡΠ΅ΠΊΡΠΈΠ²Π½ΠΎΠ΅ ΡΠ΅ΡΠ΅Π½ΠΈΠ΅. Π‘ΡΡΡ ΠΈΠ΄Π΅ΠΈ ΡΠΎΡΡΠΎΠΈΡ Π² ΡΠ°Π·Π΄Π΅Π»Π΅Π½ΠΈΠ΅ ΡΡΡΠΏΠΈΡΠ½ΠΎΠΉ ΡΠ°ΡΡΠΈ Π΄ΠΈΡΠΊΠ° ΠΈ ΡΠ°Π±ΠΎΡΠ΅Π³ΠΎ ΠΏΠΎΠ»ΠΎΡΠ½Π°. ΠΠ° ΠΏΡΠ°ΠΊΡΠΈΠΊΠ΅ ΡΡΠΎ Π°Π»ΡΠΌΠΈΠ½ΠΈΠ΅Π²Π°Ρ Β«ΡΠ»ΡΠΏΠ°Β» ΠΈ ΡΡΠ³ΡΠ½Π½ΠΎΠ΅ ΡΠ°Π±ΠΎΡΠ΅Π΅ ΠΏΠΎΠ»ΠΎΡΠ½ΠΎ, ΡΠΊΡΠ΅ΠΏΠ»ΡΠ΅ΠΌΡΠ΅ ΠΌΠ΅ΠΆΠ΄Ρ ΡΠΎΠ±ΠΎΠΉ Π±ΠΎΠ»ΡΠ°ΠΌΠΈ.
ΠΠ΄Π½ΠΈΠΌ ΠΈΠ· Π²Π°ΠΆΠ½ΡΠΉ ΡΠ»Π΅ΠΌΠ΅Π½ΡΠΎΠ² ΡΠ°ΠΊΠΎΠΉ ΠΊΠΎΠ½ΡΡΡΡΠΊΡΠΈΠΈ ΡΠ²Π»ΡΡΡΡΡ ΡΠ°ΠΊ Π½Π°Π·ΡΠ²Π°Π΅ΠΌΡΠ΅ Π±ΠΎΠ±ΠΈΠ½cΡ: ΡΠΏΠ΅ΡΠΈΠ°Π»ΡΠ½ΡΠ΅ ΠΊΡΠ΅ΠΏΠ»Π΅Π½ΠΈΡ, Π΄Π°ΡΡΠΈΠ΅ ΠΏΠΎΠ΄Π²ΠΈΠΆΠ½ΠΎΡΡΡ ΠΏΠΎΠ»ΠΎΡΠ½Ρ ΠΎΡΠ½ΠΎΡΠΈΡΠ΅Π»ΡΠ½ΠΎΠΉ ΡΡΡΠΏΠΈΡΠ½ΠΎΠΉ ΡΠ°ΡΡΠΈ. ΠΡΠ° ΠΈΠ½Π½ΠΎΠ²Π°ΡΠΈΡ ΠΏΠΎΠ·Π²ΠΎΠ»ΡΠ΅Ρ Π΄ΠΈΡΠΊΡ, ΠΏΡΠΈ Π½Π°Π³ΡΠ΅Π²Π°Π½ΠΈΠΈ, Π½Π΅ ΠΈΡΠΊΡΠΈΠ²Π»ΡΡΡΡΡ, Π° ΡΠΎΡ ΡΠ°Π½ΡΡΡ ΡΠ²ΠΎΡ Π·Π°Π²ΠΎΠ΄ΡΠΊΡΡ ΠΌΠΎΠ΄Π΅Π»Ρ.
5. Wave Π΄ΠΈΠ·Π°ΠΉΠ½.
ΠΡΠ΅Π½Ρ ΡΡΡΠ΅ΠΊΡΠ½ΠΎΠ΅ ΡΠ΅ΡΠ΅Π½ΠΈΠ΅. ΠΠΏΠ΅ΡΠ²ΡΠ΅ Π±ΡΠ»ΠΎ ΠΏΡΠΈΠΌΠ΅Π½Π΅Π½ΠΎ Π½Π° ΠΌΠΎΠ΄Π΅Π»ΠΈ ΡΠΏΠΎΡΡΠΊΡΠΏΠ΅ Audi R8. Π ΠΎΡΠ½ΠΎΠ²Ρ ΠΏΠΎΠ»ΠΎΠΆΠ΅Π½Π° Π·ΠΈΠ³Π·Π°Π³ΠΎΠΎΠ±ΡΠ°Π·Π½Π°Ρ ΠΎΠ±ΡΠ°Π±ΠΎΡΠΊΠ° Π²Π½Π΅ΡΠ½Π΅Π³ΠΎ ΠΊΡΠ°Ρ. Π ΡΠΏΠΈΡΠΎΠΊ Π΄ΠΎΡΡΠΎΠΈΠ½ΡΡΠ² ΡΠ°ΠΊΠΎΠΉ ΠΈΠ΄Π΅ΠΈ ΠΏΠΎΠΏΠ°Π»ΠΈ:
β ΡΠ»ΡΡΡΠ΅Π½ΠΈΠ΅ ΠΎΡ Π»Π°ΠΆΠ΄Π°Π΅ΠΌΠΎΡΡΠΈ Π΄ΠΈΡΠΊΠ° Π·Π° ΡΡΠ΅Ρ ΡΡΡΠ±ΡΠ»Π΅Π½ΡΠ½ΠΎΡΡΠΈ
β Π½Π΅Π·Π½Π°ΡΠΈΡΠ΅Π»ΡΠ½ΠΎΠ΅ ΡΠ½ΠΈΠΆΠ΅Π½ΠΈΠ΅ Π²Π΅ΡΠ° Π±Π΅Π· ΠΏΠΎΡΠ΅ΡΠΈ ΠΏΠ»ΠΎΡΠ°Π΄ΠΈ ΠΏΡΡΠ½Π° ΠΊΠΎΠ½ΡΠ°ΠΊΡΠ°
β Π±Π΅Π·ΡΡΠ»ΠΎΠ²Π½ΠΎ, ΡΡΡΠ΅ΠΊΡΠ½ΡΠΉ Π²Π½Π΅ΡΠ½ΠΈΠΉ Π²ΠΈΠ΄
Π’Π°ΠΊΠΎΠΉ Π²ΠΈΠ΄ ΡΡΠ½ΠΈΠ½Π³Π° ΡΡΠ°Π» ΠΏΠΎΠΏΡΠ»ΡΡΠ½ΡΠΌ Π½Π΅ ΡΠΎΠ»ΡΠΊΠΎ Ρ ΠΏΡΠΎΠΈΠ·Π²ΠΎΠ΄ΠΈΡΠ΅Π»Π΅ΠΉ Π½Π° ΠΊΠΎΠ½Π²Π΅ΠΉΠ΅ΡΠ΅, Π½ΠΎ ΠΈ Π½Π° ΡΡΠ½ΠΊΠ΅ aftermarket. Π ΡΠ΄ ΠΊΠΎΠΌΠΏΠ°Π½ΠΈΠΉ ΠΏΡΠΎΠΈΠ·Π²ΠΎΠ΄ΠΈΡ wave-Π΄ΠΈΡΠΊΠΈ Π² ΡΠΎΡΠΌΠΎΠ·Π½ΡΡ ΠΊΠΈΡΠ°Ρ β Π½Π°ΠΏΡΠΈΠΌΠ΅Ρ, WP Pro.
6. ΠΠ°ΡΠ±ΠΎΠ½-ΠΊΠ΅ΡΠ°ΠΌΠΈΡΠ΅ΡΠΊΠΈΠ΅ ΡΠΎΡΠΌΠΎΠ·Π½ΡΠ΅ Π΄ΠΈΡΠΊΠΈ.
ΠΡΡ ΡΠ΅Ρ Π½ΠΎΠ»ΠΎΠ³ΠΈΡ ΠΌΠΎΠΆΠ½ΠΎ ΡΠΌΠ΅Π»ΠΎ Π½Π°Π·Π²Π°ΡΡ ΠΏΡΠΎΡΡΠ²ΠΎΠΌ ΠΎΡΡΠ°ΡΠ»ΠΈ, ΡΠ°ΠΊ Π² ΡΡΠ°Π²Π½Π΅Π½ΠΈΠΈ Ρ Π»ΡΠ±ΡΠΌ ΡΡΠ½ΠΈΠ½Π³ΠΎΠΌ ΡΡΠ³ΡΠ½Π½ΡΡ Π΄ΠΈΡΠΊΠΎΠ² β ΡΡΠ° ΠΈΠ΄Π΅Ρ Π΄Π°Π΅Ρ Π½Π΅Π²Π΅ΡΠΎΡΡΠ½ΡΠ΅ Π±ΠΎΠ½ΡΡΡ. Π ΡΠ΅ΠΌ ΡΠ΅ΠΊΡΠ΅Ρ ΡΡΠΏΠ΅Ρ Π°?
ΠΠ΅ΠΊΠΎΡΠΎΡΡΠ΅ ΠΏΡΠ±Π»ΠΈΠΊΠ°ΡΠΈΠΈ Π² ΠΠ½ΡΠ΅ΡΠ½Π΅ΡΠ΅ ΠΏΠΈΡΡΡ ΠΏΡΠΎΡΡΠΎ β Β«ΠΊΠ°ΡΠ±ΠΎΠ½-ΠΊΠ΅ΡΠ°ΠΌΠΈΡΠ΅ΡΠΊΠΈΠ΅ Π΄ΠΈΡΠΊΠΈ ΠΈΠ·Π³ΠΎΡΠΎΠ²Π»Π΅Π½Ρ ΠΈΠ· ΡΠ³Π»Π΅ΡΠΎΠ΄Π° ΠΈ ΠΊΠ΅ΡΠ°ΠΌΠΈΠΊΠΈΒ», ΠΏΡΠΈ ΡΡΠΎΠΌ ΡΠΎΠ²ΡΠ΅ΠΌ Π½Π΅ ΠΏΠΎΡΡΠ½ΡΡ β ΡΡΠΎ ΡΠ°ΠΊΠΎΠ΅ ΡΡΠ° Π²ΠΎΠ»ΡΠ΅Π±Π½Π°Ρ Β«ΠΊΠ΅ΡΠ°ΠΌΠΈΠΊΠ°Β»? Π’Π°ΠΊ Π²ΠΎΡ. Π Π΄Π°Π½Π½ΠΎΠΌ ΡΠ»ΡΡΠ°Π΅ (ΠΊΠ°ΠΊ ΠΈ Π² ΡΠ»ΡΡΠ°Π΅ Ρ ΠΊΠ΅ΡΠ°ΠΌΠΈΡΠ΅ΡΠΊΠΈΠΌΠΈ ΡΠΎΡΠΌΠΎΠ·Π½ΡΠΌΠΈ ΠΊΠΎΠ»ΠΎΠ΄ΠΊΠ°ΠΌΠΈ) β ΠΏΡΠΈΡΡΠ°Π²ΠΊΠ° Β«ΠΊΠ΅ΡΠ°ΠΌΠΈΡΠ΅ΡΠΊΠΈΠΉΒ» ΠΎΠ±ΠΎΠ·Π½Π°ΡΠ°Π΅Ρ Β«ΠΏΠΎΡΠΎΡΠΊΠΎΠ²ΡΠΉΒ», ΠΈ Π½Π΅ Π±ΠΎΠ»Π΅Π΅. ΠΡΠΎΡΠ΅ Π³ΠΎΠ²ΠΎΡΡ, ΠΊΠ°ΡΠ±ΠΎΠ½-ΠΊΠ΅ΡΠ°ΠΌΠΈΡΠ΅ΡΠΊΠΈΠ΅ Π΄ΠΈΡΠΊΠΈ ΠΈΠ·Π³ΠΎΡΠΎΠ²Π»Π΅Π½Ρ ΠΈ ΡΠΌΠ΅ΡΠ΅Π½ΠΈΡ ΡΠΌΠΎΠ» ΠΈ Π²ΠΎΠ»ΠΎΠΊΠΎΠ½ ΡΠ³Π»Π΅ΡΠΎΠ΄Π°, ΠΌΠ΅Π»ΠΊΠΎ ΠΈΠ·ΠΌΠ΅Π»ΡΡΠ΅Π½Π½ΡΡ ΠΈ ΡΠΏΠ΅ΡΠ΅Π½Π½ΡΡ ΠΏΠΎΠ΄ Π²ΡΡΠΎΠΊΠΈΠΌ Π΄Π°Π²Π»Π΅Π½ΠΈΠ΅ΠΌ ΠΈ ΠΏΡΠΈ Π²ΡΡΠΎΠΊΠΎΠΉ ΡΠ΅ΠΌΠΏΠ΅ΡΠ°ΡΡΡΠ΅. ΠΠΌΠ΅Π½Π½ΠΎ ΡΠ°ΠΊΠΎΠΉ ΠΌΠ΅ΡΠΎΠ΄ ΠΏΠΎΠ·Π²ΠΎΠ»ΡΠ΅Ρ Π΄ΠΎΠ±ΠΈΡΡΡΡ Π±ΠΎΠ»Π΅Π΅ ΠΏΡΠΎΡΠ½ΡΡ ΡΠ²ΡΠ·Π΅ΠΉ ΠΌΠ΅ΠΆΠ΄Ρ ΠΊΠΎΠΌΠΏΠΎΠ½Π΅Π½ΡΠ°ΠΌΠΈ. ΠΠ°ΠΊ Π²ΠΈΠ΄ΠΈΡΠ΅, Π½ΠΈΠΊΠ°ΠΊΠΈΡ ΠΊΠ΅ΡΠ°ΠΌΠΈΡΠ΅ΡΠΊΠΈΡ ΡΠ°ΡΠ΅ΠΊ ΠΈ ΠΏΡΠΎΡΠ΅ΠΉ ΠΏΠΎΡΡΠ΄Ρ Π² ΡΠΎΡΡΠ°Π²Π΅ Π½Π΅Ρ.
ΠΠ»Π°Π³ΠΎΠ΄Π°ΡΡ Π²ΡΡΠ΅ΠΎΠΏΠΈΡΠ°Π½Π½ΠΎΠΉ ΡΠ΅Ρ Π½ΠΎΠ»ΠΎΠ³ΠΈΠΈ ΠΈ ΡΡΠΈΠ»Π΅Π½ΠΈΡ ΡΠ³Π»Π΅ΡΠΎΠ΄Π½ΡΠΌΠΈ Π²ΠΎΠ»ΠΎΠΊΠ½Π°ΠΌΠΈ β ΡΠ°ΠΊΠΈΠ΅ Π΄ΠΈΡΠΊΠΈ ΡΠΏΠΎΡΠΎΠ±Π½Ρ ΡΠ»ΡΠΆΠΈΡΡ Π΄ΠΎ 300-350 ΡΡΡΡΡ ΠΊΠΈΠ»ΠΎΠΌΠ΅ΡΡΠΎΠ². Π§ΡΠΎ ΠΈΠ½ΡΠ΅ΡΠ΅ΡΠ½ΠΎ β Π² ΠΏΡΠΎΡΠ΅ΡΡΠ΅ ΡΠΊΡΠΏΠ»ΡΠ°ΡΠ°ΡΠΈΠΈ ΡΠ°ΠΊΠΈΠ΅ Π΄ΠΈΡΠΊΠΈ Π½Π΅ ΡΠΌΠ΅Π½ΡΡΠ°ΡΡΡΡ Π² ΡΠΎΠ»ΡΠΈΠ½Π΅ (ΠΊΠ°ΠΊ ΠΊΠ»Π°ΡΡΠΈΡΠ΅ΡΠΊΠΈΠ΅ ΡΡΠ³ΡΠ½Π½ΡΠ΅). ΠΠ·Π½ΠΎΡ ΠΊΠ΅ΡΠ°ΠΌΠΈΡΠ΅ΡΠΊΠΈΡ ΡΠΎΡΠΌΠΎΠ·Π½ΡΡ Π΄ΠΈΡΠΊΠΎΠ² ΠΏΡΠΎΠ²Π΅ΡΡΡΡ Π²Π·Π²Π΅ΡΠΈΠ²Π°Π½ΠΈΠ΅ΠΌ β ΠΎΠ½ΠΈ ΡΠ΅ΡΡΡΡ Π² ΡΠ²ΠΎΠ΅ΠΉ ΠΌΠ°ΡΡΠ΅.
ΠΡΠΎΡΠΎΠ΅ Π²Π°ΠΆΠ½ΠΎΠ΅ ΠΏΡΠ΅ΠΈΠΌΡΡΠ΅ΡΡΠ²ΠΎ β Π²Π΅Ρ. Π’Π°ΠΊΠΎΠΉ Π΄ΠΈΡΠΊ ΠΈΠΌΠ΅Π΅Ρ ΠΌΠ°ΡΡΡ Π½Π° 50-70% ΠΌΠ΅Π½ΡΡΡΡ, Π½Π΅ΠΆΠ΅Π»ΠΈ ΡΡΠ³ΡΠ½Π½ΡΠΉ ΡΠΎΠ±ΡΠ°Ρ.
Π ΡΡΠ΅ΡΠΈΠΉ ΠΌΠΎΠΌΠ΅Π½Ρ β ΡΡΠΎΠΉΠΊΠΎΡΡΡ ΠΊ Π²ΡΡΠΎΠΊΠΈΠΌ ΡΠ΅ΠΌΠΏΠ΅ΡΠ°ΡΡΡΠ°ΠΌ. ΠΡΠΎΡΠ΅ Π³ΠΎΠ²ΠΎΡΡ β Π²Ρ ΠΌΠΎΠΆΠ΅ΡΠ΅ ΡΠΆΠ΅ΡΡ Π½Π°ΠΏΡΠΎΡΡ ΠΊΠΎΠ»ΠΎΠ΄ΠΊΠΈ, Π½ΠΎ Π΄ΠΎΠ²Π΅ΡΡΠΈ Π΄ΠΎ Π΄ΠΈΡΠΊΠΈ Π΄ΠΎ ΠΏΠ΅ΡΠ΅Π³ΡΠ΅Π²Π° ΡΠ»ΠΎΠΆΠ½ΠΎ.
ΠΠΈΠ½ΡΡΡ ΡΠ°ΠΊΠΎΠΉ ΡΠ°Π·ΡΠ°Π±ΠΎΡΠΊΠΈ: Π·Π°ΠΎΠ±Π»Π°ΡΠ½Π°Ρ ΡΠ΅Π½Π°, ΠΏΠΈΡΠΊ ΠΈ ΡΠΊΡΠΈΠΏ Π½Π° ΠΌΠ°Π»ΡΡ ΡΠΊΠΎΡΠΎΡΡΡΡ ΠΈ ΡΡΠ²ΡΡΠ²ΠΈΡΠ΅Π»ΡΠ½ΠΎΡΡΡ ΠΊΠΎΠΌΠΏΠΎΠ·ΠΈΡΠ½ΠΎΠ³ΠΎ ΡΠΎΡΡΠ°Π²Π° ΠΊ ΠΌΠ΅Ρ Π°Π½ΠΈΡΠ΅ΡΠΊΠΈΠΌ ΠΏΠΎΠ²ΡΠ΅ΠΆΠ΄Π΅Π½ΠΈΡΠΌ.
7. ΠΠ°ΡΠ±ΠΎΠ½ΠΎΠ²ΡΠ΅ ΡΠΎΡΠΌΠΎΠ·Π½ΡΠ΅ Π΄ΠΈΡΠΊΠΈ. Π‘ΡΡΠ΅ΡΡΠ²ΡΠ΅Ρ ΡΠ°ΠΊΠΆΠ΅ ΡΠ΅Ρ
Π½ΠΎΠ»ΠΎΠ³ΠΈΡ ΠΊΠ°ΡΠ±ΠΎΠ½ΠΎΠ²ΡΡ
ΡΠΎΡΠΌΠΎΠ·Π½ΡΡ
Π΄ΠΈΡΠΊΠΎΠ², Π½ΠΎ ΠΎΠ½Π° Π½Π΅ ΠΏΡΠΈΠΌΠ΅Π½ΡΠ΅ΡΡΡ Π΄Π»Ρ Π³ΡΠ°ΠΆΠ΄Π°Π½ΡΠΊΠΈΡ
Π°Π²ΡΠΎΠΌΠΎΠ±ΠΈΠ»Π΅ΠΉ Π½Π° Π΄ΠΎΡΠΎΠ³Π°Ρ
ΠΎΠ±ΡΠ΅Π³ΠΎ ΠΏΠΎΠ»ΡΠ·ΠΎΠ²Π°Π½ΠΈΡ. Π’Π΅Ρ
Π½ΠΎΠ»ΠΎΠ³ΠΈΡ ΡΠΈΡΠΎΠΊΠΎ ΠΏΡΠΈΠΌΠ΅Π½ΡΠ΅ΡΡΡ Π½Π° Π±ΠΎΠ»ΠΈΠ΄Π°Ρ
Π€ΠΎΡΠΌΡΠ»Ρ 1.
Π’Π°ΠΊΠΈΠ΅ ΡΠΎΡΠΌΠΎΠ·Π½ΡΠ΅ Π΄ΠΈΡΠΊΠΈ ΠΈΠ·Π³ΠΎΡΠΎΠ²Π»Π΅Π½Ρ (Π° ΡΠΎΡΠ½Π΅Π΅ Π±ΡΠ΄Π΅Ρ ΡΠΊΠ°Π·Π°ΡΡ β ΡΠΏΠ»Π΅ΡΠ΅Π½Ρ) Π½Π° 100% ΠΈΠ· Π²ΠΎΠ»ΠΎΠΊΠΎΠ½ ΡΠ³Π»Π΅ΡΠΎΠ΄Π°. Π’Π°ΠΊΠΈΠΌ ΠΎΠ±ΡΠ°Π·ΠΎΠΌ, ΡΡΠΎ Π½Π΅Π²Π΅ΡΠΎΡΡΠ½ΠΎ Π»Π΅Π³ΠΊΠΈΠ΅ ΠΈ Π² ΡΠΎ ΠΆΠ΅ Π²ΡΠ΅ΠΌΡ ΠΏΡΠΎΡΠ½ΡΠ΅ ΠΈ ΡΡΠΎΠΉΠΊΠΈΠ΅ ΠΊ Π½Π°Π³ΡΡΠ·ΠΊΠ°ΠΌ ΠΊΠΎΠΌΠΏΠΎΠ½Π΅Π½ΡΡ. ΠΠ΄Π½Π°ΠΊΠΎ, Π²ΡΠΉΡΠΈ Π½Π° Π΄ΠΎΡΠΎΠ³ΠΈ ΠΎΠ±ΡΠ΅Π³ΠΎ ΠΏΠΎΠ»ΡΠ·ΠΎΠ²Π°Π½ΠΈΡ ΡΡΠΈΠΌ Π΄ΠΈΡΠΊΠ°ΠΌ ΠΌΠ΅ΡΠ°ΡΡ Π΄Π²Π° Π½Π΅Π΄ΠΎΡΡΠ°ΡΠΊΠ°: Π½ΠΈΠ·ΠΊΠ°Ρ ΡΡΡΠ΅ΠΊΡΠΈΠ²Π½ΠΎΡΡΡ Π½Π° Π½Π΅ ΠΏΡΠΎΠ³ΡΠ΅ΡΡΡ ΡΠΎΡΠΌΠΎΠ·Π°Ρ ΠΈ ΡΠ»ΠΈΡΠΊΠΎΠΌ Π²ΡΡΠΎΠΊΠ°Ρ β Π½Π° Π³ΠΎΡΡΡΠΈΡ . ΠΠ½ΡΠΌΠΈ ΡΠ»ΠΎΠ²Π°ΠΌΠΈ, Π² ΠΎΡΠ»ΠΈΡΠΈΠΈ ΠΎΡ ΡΡΠ³ΡΠ½Π½ΡΡ Π΄ΠΈΡΠΊΠΎΠ², ΠΊΠ°ΡΠ±ΠΎΠ½ΠΎΠ²ΡΠ΅ Π½Π΅Π΅ ΠΏΠΎΠΊΠ°Π·ΡΠ²Π°ΡΡ Π»ΠΈΠ½Π΅ΠΉΠ½ΠΎΠ³ΠΎ ΡΠΎΡΡΠ° ΡΡΡΠ΅ΠΊΡΠΈΠ²Π½ΠΎΡΡΠΈ. ΠΠΎΡΠ»Π΅ Ρ ΠΎΡΠΎΡΠ΅Π³ΠΎ ΠΏΡΠΎΠ³ΡΠ΅Π²Π° ΡΡΡΠ΅ΠΊΡΠΈΠ²Π½ΠΎΡΡΡ ΡΠΎΡΠΌΠΎΠΆΠ΅Π½ΠΈΡ Ρ ΡΠ°ΠΊΠΎΠΉ ΡΠ°Π·ΡΠ°Π±ΠΎΡΠΊΠΎΠΉ Π²Π·Π»Π΅ΡΠ°Π΅Ρ ΠΊΠ°ΠΊ Β«ΡΠ²Π΅ΡΠΊΠ°Β». ΠΠΎΡΡΠΎΠΌΡ ΡΠΏΡΠ°Π²Π»ΡΡΡ ΡΠ°ΠΊΠΈΠΌΠΈ ΡΠΎΡΠΌΠΎΠ·Π°ΠΌΠΈ β ΡΡΠ΅Π±ΡΠ΅Ρ ΠΎΡΠΎΠ±ΠΎΠ³ΠΎ ΠΌΠ°ΡΡΠ΅ΡΡΡΠ²Π°.
ΠΡΡΠΎΡΠ½ΠΈΠΊ tormozi.ua
lubimauto.ru