Почему ржавеют автомобильные кузова. Немного теории и страшная сказка на ночь
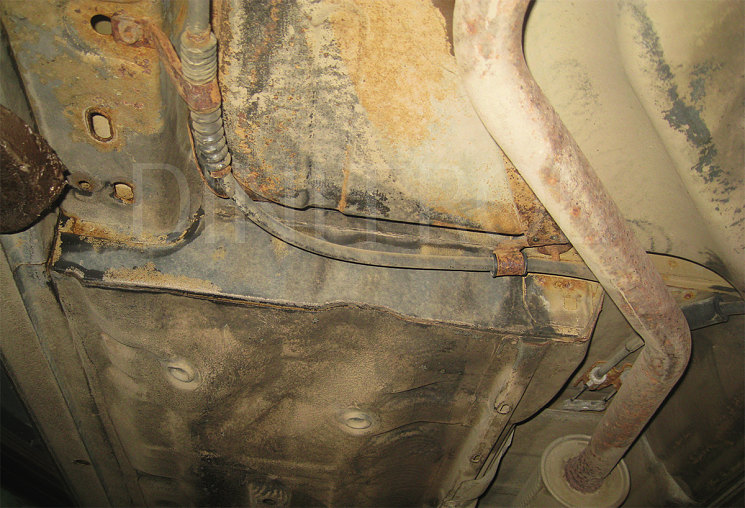
Проблема борьбы с коррозией стара как мир. И журнал «АБС-авто» уделяет ей самое пристальное внимание. Так, первая антикоррозионная статья увидела свет еще в марте 1997 года – одновременно с рождением журнала.
С той поры редакция опубликовала десятки статей по борьбе с коррозией. И даже выпустила тематическую брошюру совместно с компанией ЮВК, нашим давним партнером и консультантом. Сегодня мы предлагаем вам фрагменты из этого издания, посвященные теории коррозионных процессов. Знания – сила, и чтобы победить врага, надо хорошо изучить его повадки.
Терминология
Что такое коррозия металлов? Это слово происходит от латинского «corrodo – грызу». В литературе встречаются ссылки и на позднелатинское «corrosio – разъедание». Но так, или иначе, коррозия – это процесс разрушения металлов в результате химического и электрохимического взаимодействия с внешней средой.
Мы не зря подчеркнули слово процесс в определении коррозии. Дело в том, что многие водители и механики в бытовых и даже в профессиональных разговорах частенько отождествляют термины «коррозия» и «ржавчина». Однако это не синонимы, разница в следующем.
Слово «коррозия» применимо ко многим металлам (включая цветные), сплавам, а также бетону и некоторым пластмассам. А ржавчина – это результат коррозионного процесса. Этот термин относится только к железу, входящему в состав стали и чугуна. И говоря «ржавеет (или корродирует) сталь», мы подразумеваем, что ржавеет (окисляется) железо, входящее в ее состав.
Столь подробное разъяснение тривиальных, в общем-то, вещей, приводится с единственной целью: подчеркнуть, что бороться надлежит не со ржавчиной, а именно с коррозией. Иными словами, не с результатом, а с процессом, на что и нацелены все современные системы антикоррозионной защиты. И чем раньше начата эта борьба, тем дольше проживет авомобильный кузов.
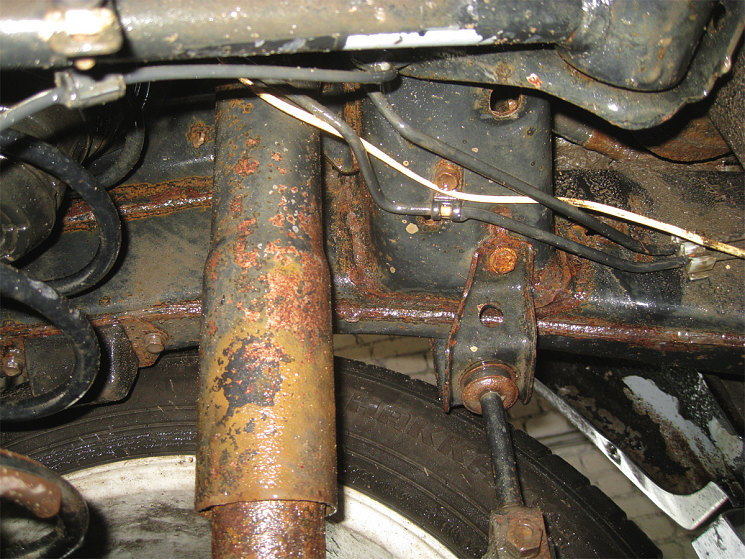
И еще. В определении коррозии мы подчеркнули слова химического и электрохимического взаимодействия. Это тоже не зря. В некоторых публикациях, включая рекламные, встречается мнение, что коррозия – процесс сугубо химический. Дескать, окисление кислородом воздуха, и все тут. Это далеко не так – едва ли не главную роль в разрушении автомобильного кузова играют электрохимические процессы, и мы подробно поговорим об этом ниже. А пока немного истории.
«От Ромула до наших дней…»
Коррозия отравляет жизнь человечеству уже давно. Еще в первом веке нашей эры римский ученый Плиний-старший писал: «На железо обрушилась месть человеческой крови… Оно ржавеет быстрее, когда соприкасается с нею».
Немало воды утекло с момента высказывания Плиния. А сколько железа превратилось в бурый порошок! Зато процесс коррозии металлов получил теоретическое объяснение – правда, не сразу.
Например, Лавуазье рассматривал коррозию железа как процесс простого окисления – прямо как некоторые наши современники, упомянутые в предыдущем разделе. Однако и великие иногда ошибаются – в 1837 году М. Пайен показал, что при температуре ниже 200 °С в атмосфере сухого кислорода (т.е. среде, не содержащей водяных паров) железо практически не ржавеет! Значит, дело не только в наличии кислорода?
Волей-неволей от взглядов Лавуазье на коррозию пришлось отказаться. Но что предложить взамен, ведь «природа на терпит пустоты»? Какое-то время механизм коррозии увязывали с кислотностью соприкасающейся с железом среды. И лишь электрохимическая теория коррозии металлов смогла объяснить все тонкости этого коварного процесса.
В заключение этого раздела отметим, что в результате коррозии по разным данным теряется от 10 до 25% мировой добычи железа. Значит, железная руда, изначально сконцентрированная в земной коре, в поте лица добытая и искусно переработанная в чугун и сталь, безвозвратно рассеивается, распыляется по всему белому свету. И не борясь с коррозией, мы наказываем не только себя, любимых, но и потомков своих, оставляя их без ценнейшего конструкционного материала – железа. А оно, несмотря на успешные опыты с алюминиевыми сплавами и пластиками, пока что играет ведущую роль в производстве автомобильных кузовов.
Химическая коррозия
Итак, коррозия может быть химической и электрохимической. Их отличие в следующем: первая протекает в среде, не проводящей электрический ток, вторая – в водных растворах электролитов.
В документации некоторых фирм, производящих защитные антикоррозионные материалы, химическую коррозию иногда называют «сухой», а электрохимическую – «мокрой». Однако следует знать, что в присутствии влаги, углекислого газа и кислорода воздуха химическая коррозия также активизируется.
В результате окислительных процессов на поверхности железных изделий образуется ржавчина, состоящая из слоя частично гидратированных оксидов железа. Формула ржавчины – Fe3O4 (или FeO•Fe2O3), а под действием кислорода во влажном воздухе образуется соединение Fe2O3•nh3O. Слой этот хрупок и порист, поэтому не предохраняет железо (сталь) от дальнейшего корродирования.
Электрохимическая коррозия
В отличие от окислительных, процессы электрохимической коррозии протекают по законам электрохимической кинетики. Вспомним тот же курс химии, посмотрев на рисунок внизу.
Элементы, расположенные в указанном на схеме порядке, образуют электрохимический ряд напряжений металлов. Смысл его в следующем: металл, стоящий в этом ряду левее, способен вытеснить из растворов электролитов металл, стоящий правее. Поэтому, глядя на рисунок, можно с уверенностью сказать, что железо будет вытеснять медь из раствора ее солей.

В электрохимический ряд напряжений металлов включен также водород. Казалось бы, зачем? А вот зачем: его положение показывает, какие металлы могут вытеснять водород из растворов кислот, а какие – нет. Так, железо вытесняет водород из растворов кислот, поскольку находится левее его. Медь же на такой подвиг не способна, так как находится правее. Из этого следует вывод: кислотные дожди для железа опасны, а для чистой меди – нет. Чего нельзя сказать о бронзе и других сплавах на основе меди: они содержат алюминий, олово и другие металлы, расположенные левее водорода.
Но вернемся к электрохимической коррозии как таковой. Все, в общем-то, просто: если в каком-либо узле имеется соединение двух металлов с различными потенциалами, то в присутствии электролита они образуют гальваническую пару. И чем дальше разнесены металлы в электрохимическом ряду напряжений, тем больше гальванический ток, активнее переход электронов и, соответственно, сильнее разрушения металла – какого? Правильно, «левого».
Проиллюстрируем это простым примером. Положим, в стальной автомобильной панели появилась медная заклепка. Она будет являться катодом, а стальной лист – анодом. Коррозионное разрушение железа в месте соединения обеспечено.
Итак, контакт данного «левого» металла с менее активным «правым» усиливает коррозию первого. Теперь понятно, почему цинковое покрытие защищает железо от коррозии, а поврежденное медное – усиливает его коррозионное разрушение в местах, медью не покрытых.
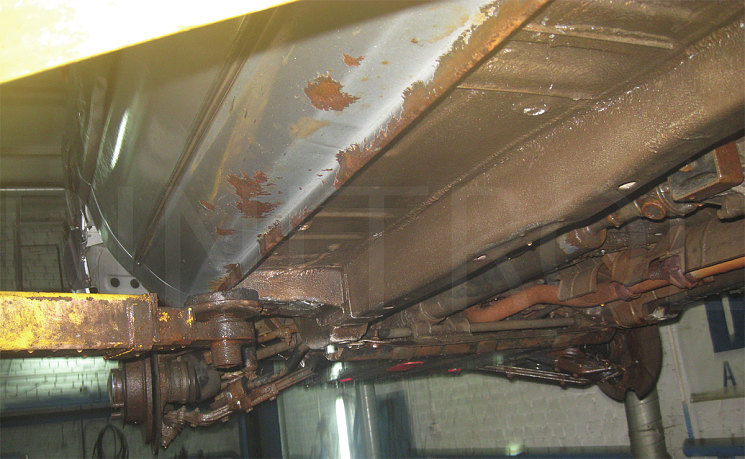
Покрытия слоем более активных металлов называют «безопасными», а слоем менее активных – «опасными». Безопасные покрытия давно и успешно применяют в мировом автомобилестроении. Это, в частности, оцинковка кузовных панелей и хромирование некоторых деталей.
Заканчивая этот раздел, еще раз подчеркнем, что автомобильный кузов подвергается действию обоих видов коррозии – химической и электрохимической. Но главная роль все же принадлежит электрохимическим процессам. Дело в том, что при относительной влажности воздуха более 60% на металлической поверхности образуется слой влаги, играющий роль электролита. А для средних широт показатель 60%, как правило, превышается в течение всего года.
Кроме того, в реальных условиях эксплуатции оба вида коррозии усиливаются неоднородностью металла, воздействием напряжений, деформаций, трения, износа и других факторов. А теперь посмотрим, что влияет на коррозию автомобильного кузова.
Химический состав и структура металла
Если бы кузовные панели штамповались из технически чистого железа, их коррозионная стойкойсть была бы выше всяких похвал. Но по многим причинам это невозможно. В частности, применяющееся в электротехнической промышленности железо ARMKO (99,85% Fe), для автомобиля слишком дорого и недостаточно прочно. Хотя оно обладает великолепной пластичностью и ржавеет крайне неохотно – в чем автор убедился лично, работая в свое время с этим материалом.
А вот конструкционные металлы и тем более сплавы пасуют перед коррозией. Например, сталь марки 08КП, широко применяемая в нашей стране для штамповки деталей автомобильных кузовов, при исследовании под микроскопом являет такую картину: мелкие зерна чистого железа, обильно перемешанные с зернами карбида железа (цементита Fe3C) и другими включениями.
Думаем, дальше все понятно: подобная структура порождает множество гальванических пар, в которых примеси играют роль положительных электродов, а зерна железа – отрицательных. При соприкосновении с влажным воздухом в этой системе возникают гальванические токи, вызывающие коррозию железа. Аналогично работают на коррозию примеси и в других металлах.
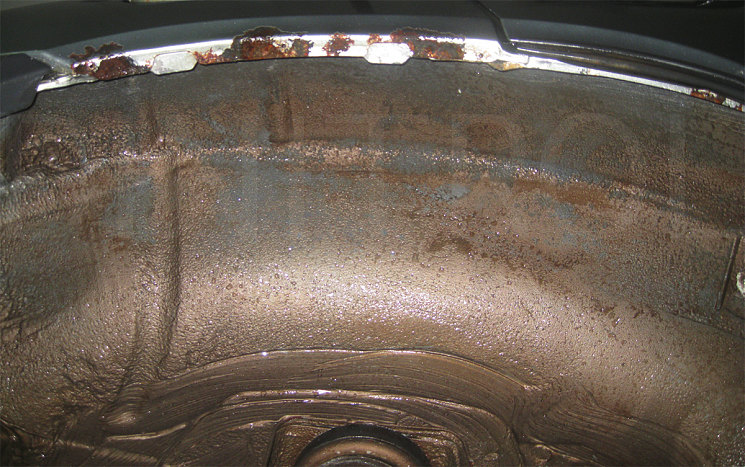
Так что в рассуждениях опытных мастеров и водителей – дескать, раньше металл был чище, кузова долго не ржавели, содержится изрядная доля истины. Любые отклонения от стандартов и ТУ при изготовлении стального листа сулят будущему автомобилю весьма недолгую жизнь.
Кстати, почему, извините за невольный каламбур, не ржавеют нержавеющие стали? Да потому, что фактически это сплавы, по составу близкие к однородным твердым растворам. Кроме того, в их состав входят изрядные порции хрома и никеля, стоящих в электрохимическом ряду напряжений рядом с железом. И еще: хром и никель на воздухе почти не окисляются, поскольку образуют на своей поверхности прочную оксидную пленку. Поэтому гальванические и окислительные процессы на поверхности нержавеющей стали практически не возникают.
Конструкция кузова и его технологи
Кузов современного легкового автомобиля состоит из большого числа деталей (панелей), собранных в единое целое. Толщина листовой стали, из которой эти детали изготавливаются, как правило, менее 1 мм. Кроме того, в процессе штамповки эта толщина в некоторых местах уменьшается.
Теория обработки металлов давлением гласит, что в любом технологическом процесе – будь то вытяжка, гибка и тому подобные операции, пластическая деформация металла сопровождается возникновением нежелательных остаточных напряжений. Если оборудование и скорости деформирования подобраны правильно, а штамповая оснастка не изношена, эти напряжения незначительны.
В противном случае в кузовную панель закладывается этакая «бомба замедленного действия»: атомы в некоторых кристаллических зернах располагаютя нехарактерно, поэтому механически напряженный металл корродирует интенсивнее, чем ненапряженный. Кстати, нечто подобное поисходит в панелях, востановленных после аварии, а также в старых «уставших» кузовах.
Но вернемся к заводским технологиям. После сборки (сварки) в кузове образуется множество щелей, полостей, нахлестов, кромок, в которых скапливается грязь и влага. И что очень важно – сварные швы образуют с основным металлом все те же гальванические пары. Надо ли указывать, что перечисленные факторы способствуют возникновению и развитию коррозионных процессов?
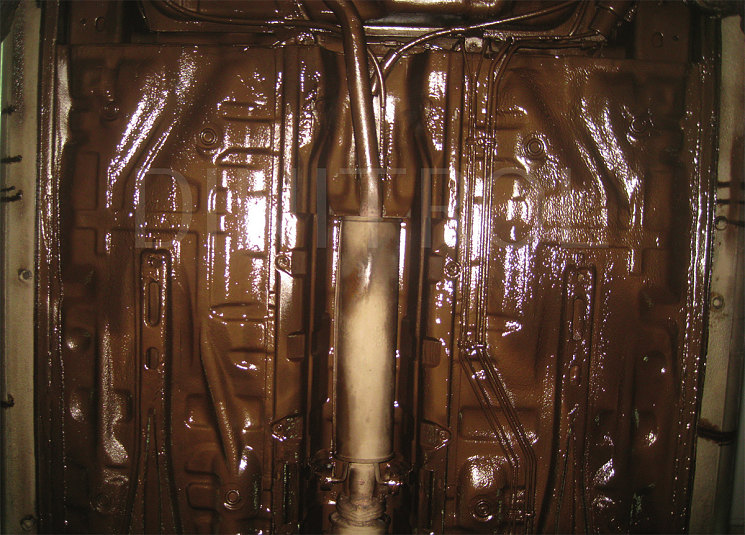
Влияние окружающей среды при эксплуатации
В результате человеческой деятельности, прежде всего развития промышленности, окружающая среда становится все более агрессивной. В последние годы в атмосфере повысилось содержание оксидов серы, азота, углерода. А значит, автомобиль омывается кислотными дождями, фактически – электролитом, ускоряюющим коррозионные процессы.
Можно и формально утверждать, что в городских условиях кузова живут меньше. Здесь мы можем сослаться на Шведский институт коррозии (о нем будет рассказано далее), опубликовавший следующие данные:
- скорость разрушения стали и цинка в сельской местности в Швеции составляет 8 и 0,8 мкм в год;
- для города эти цифры составляют соответственно 30 и 5 мкм в год.
Немалую роль играет и географическое положение местности, где эксплуатируется автомобиль. Так, морской климат делает коррозию примерно в 2 раза активнее, чем резкоконтинентальный.
Влияние доступа воздуха
В теории коррозии есть так называемый принцип дифференциальной аэрации, гласящий: неравномерный доступ воздуха к различным участкам металлической поверхности приводит к образованию гальванического элемента.
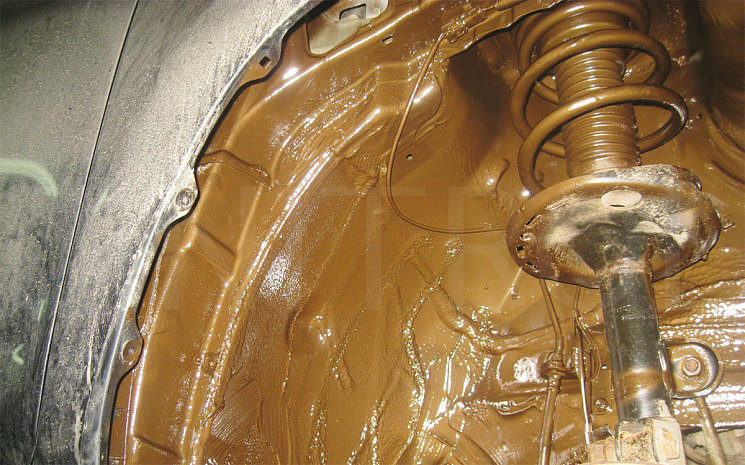
При этом участок, хуже снабжаемый кислородом, будет разъедаться, а участок, интенсивно снабжаемый им, наоборот, останется невредимым. Так, блестящая поверхность витого стального троса вовсе не означает, что он не проржавел внутри: в местах, куда доступ воздуха затруднен, угроза коррозии больше.
Проецируя сказанное на внутренние полости автомобильных кузовов, можно представить, сколько возможностей существует для возникновения коррозии в скрытых, плохо вентилируемых сечениях.
Кроме того, коррозия скрытых полостей начинает свою разрушительную деятельность невидимкой. Когда же она «выходит наружу» в виде перфорированной ржавчины, бороться с ней уже бесполезно. Зачастую ответственные участки кузова становятся ненадежными и дальнейшая эксплуатация такого автомобиля может иметь катастрофические последствия.
Влияние влажности и температуры
Важнейшим фактором, влияющим на скорость коррозии, является время, в течение которого металлическая поверхность остается влажной.
Ясно, что внутренние поверхности коробов, щелей, кромок, отбортовок сохнут гораздо медленнее открытых частей кузова. Немалую роль здесь играет посыпание зимних дорог солью, особенно хлоридом натрия NaCl. Когда снег и лед подтаивают, в результате электролитической диссоциации образуется очень сильный электролит. А поскольку внутренние полости не герметичны, он проникает и в них. Тем самым создаются прекрасные условия для электрохимической коррозии.
Вот еще важный пример: холодное время года. Утром водитель прогревает машину, ночью она остывает – в дверях и порожках образуется конденсат. И так каждый день. А вот, казалось бы, мелочь: в машине мы дышим, выдыхаем углекислый газ, а коррозии это только на руку.
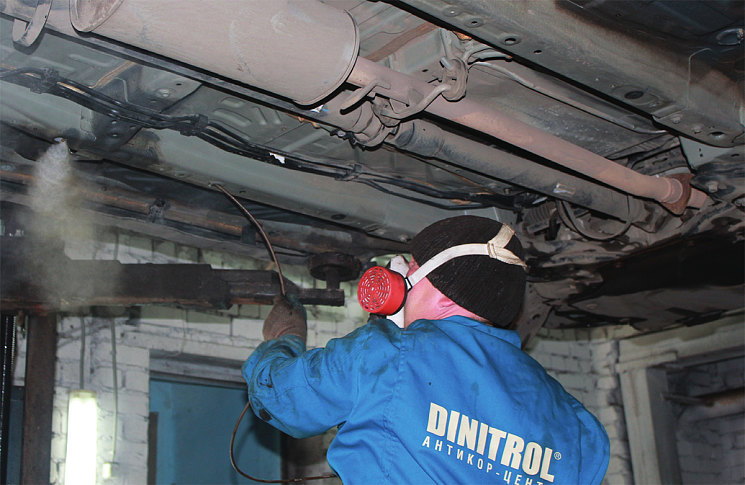
Отметим также, что повышение температуры активизирует коррозию. Так, вблизи выхлопной системы следов коррозии всегда больше.
Ржавеют любые кузова
Как писали сатирики, «статистика знает все». Есть в Стокгольме такая организация – Шведский институт коррозии, далее просто ШИК. Его экспертизы пользуются огромным авторитетом, причем не только в Скандинавии.
Раз в три-четыре года шведские ученые организуют масштабное изучение коррозионного поражения автомобильных кузовов. В этих работах участвуют и автопроизводители, охотно предоставляющие автомобили на испытания. Не остались в стороне и металлургические компании, поставляющие листовой прокат для изготовления кузовов, а также разработчики технологий цинковых и цинко-никелевых покрытий.
Для определения степени коррозионного поражения шведские ученые выбирают сотни кузовов хорошо потрудившихся автомобилей. Вырезают участки вблизи порогов, угловых участков дверей, соединений арок колеса с порогом и тому подобных местах, и оценивают степень их поражения.
Исследованные кузовные панели были защищены от коррозии оцинковкой и (или) антикоррозионными препаратами. Итак, оцинковка и антикор.
Поделим оцинковку на три группы: «толстый» слой – от 7 до 10 мкм; «тонкий» слой – от 2 до 5 мкм; и «нулевой» слой (панель не оцинкована).
Под словом «антикор» будем понимать современные профессиональные антикоррозионные материалы. Получается шесть видов обработки панели:
- «толстая» оцинковка плюс антикор;
- «толстая» оцинковка без антикора;
- «тонкая» оцинковка плюс антикор;
- «тонкая» оцинковка без антикора;
- «нулевая» оцинковка плюс антикор;
- «нулевая» оцинковка без антикора, что означает просто окрашенную панель без дополнительной защиты.
ШИК утверждает, что пять вариантов из шести – плохи. Лишь владелец автомобиля с «толстой» оцинковкой и (внимание!) дополнительной антикоррозионной обработкой может ездить спокойно – 5%-ная поверхностная коррозия грозит ему лишь через семь лет эксплуатации. Выводы очевидны: оцинковка – не панацея; основа долголетия кузова – регулярная дополнительная антикоррозионная защита.
Работы ШИКа дают колоссальный статистический материал по коррозионной стойкости автомобильных кузовов. Именно он ложится в основу совершенствования технологий защиты от коррозии – как заводских, так и послепродажных.
К сожалению, у нас в России столь масштабные исследования не проводятся. А тем временем многие популярные иномарки (новые, «с иголочки»!) прибывают к российским дилерам с голым днищем. Катафорезный грунт, штатная окраска да скромные полоски пластизоля на сварных швах – вот и вся защита. Надолго ли ее хватит на наших дорогах?
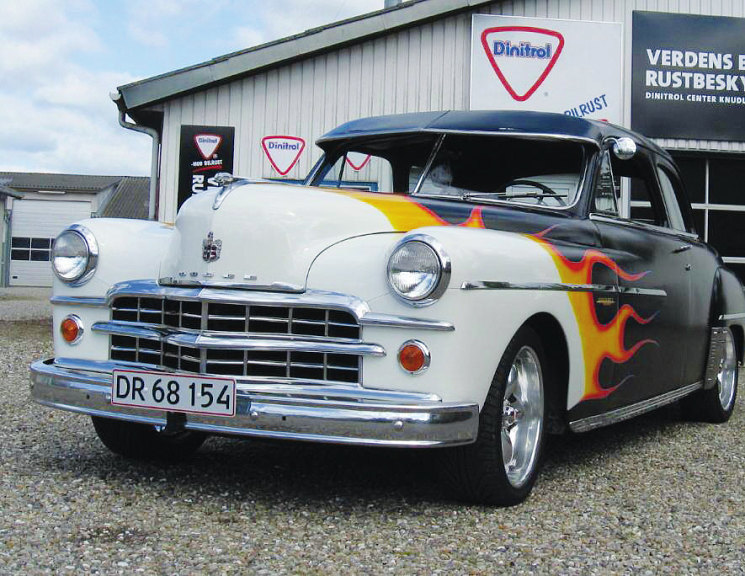
Столь же безрадостно выглядят скрытые сечения кузова, если заглянуть в них с помощью соединенного с компьютером технического эндоскопа. Редко, очень редко в автомобильных внутренностях можно встретить антикоррозионный барьер из воскообразного ML-препарата. Чаще монитор показывает точки и даже очаги ржавчины – и в порогах, и в дверях, и в полостях капота и багажника. Вот тебе, бабушка, и новая иномарка…
Но автомобильные мифы живучи, иномарки заманчиво блестящи, а сознание потребителя инертно. Значит, будем развенчивать мифы: рассказывать, доказывать, убеждать.
Опасен ли ржавый кузов?
Регламентирует ли государство эксплуатацию ржавых автомобилей? Много лет назад появился ГОСТ Р 51709–2001 «Автотранспортные средства. Требования безопасности к техническому состоянию и методы проверки». Иными словами – руководство для проведения Государственного технического осмотра. Все было в этом ГОСТе – только вот о коррозии кузова ничего не говорилось.
В марте 2006 года родилась новая редакция документа. Среди многочисленных поправок и дополнений появились и такие:
«4.7.25. Нe допускаются:
- ненадежное крепление амортизаторов вследствие сквозной коррозии мест или деталей крепления;
- чрезмерная общая коррозия рамы и связанных с ней деталей крепления или элементов усиления прочности основания кузова автобуса, грозящая разрушением всей конструкции;
- сквозная коррозия или разрушение пола пассажирского помещения автобуса, способные служить причиной травмы;
- коррозия либо трещины и разрушения стоек кузова, нарушающие их прочность;
- вмятины и разрушения кузова, нарушающие внешние очертания и узнаваемость модели АТС.
4.7.26. Грозящие разрушением грубые повреждения и трещины или разрушения лонжеронов и поперечин рамы, щек кронштейнов подвески, стоек либо каркасов бортов и приспособлений для крепления грузов не допускаются».
Мы еще в 2006 году отметили: в документе нет количественных оценок коррозионного поражения! И методик нет, и приборы не прописаны. Вот для двигателя есть свои нормативы и оборудование. И для тормозов, и для фар… А для коррозии – нет. Сплошь визуальные, а значит, субъективные оценки.
Старый ГОСТ…
Вдумаемся. Что такое «ненадежное крепление амортизаторов вследствие сквозной коррозии мест или деталей крепления»? Поговорку помните: «Поздно пить ”боржоми“»?
А чего стоит сентенция «вмятины и разрушения кузова, нарушающие внешние очертания и узнаваемость модели АТС»? Это как? Несется по шоссе смятый и разрушенный кузов. Внешние очертания настолько нарушены, что его и опознать-то невозможно. Это значит нельзя. А если не совсем разрушенный, очертания сохранивший, это значит – можно…
Господа разработчики! Тревогу надо бить задолго до потери внешних очертаний. И до появления сквозной коррозии. Необходимо периодически защищать автомобиль специализированными антикоррозионными препаратами, о чем наш журнал пишет регулярно. Но вы же не читатели, а писатели. Вам не до журналов.
По уму надо было делать так. Прописать в ГОСТе обязательный контроль скрытых полостей кузова и прежде всего лонжеронов, порогов, стоек и других силовых элементов. В несущем кузове они играют роль каркаса, скелета. Именно от него зависит, способен кузов что-либо «нести» или пора выносить его самого. В последний путь под шредеры и прессы.
Проконтролировать скрытые полости просто: надо лишь обзавестись уже упомянутым эндоскопом. Подключенный к компьютеру, он дает возможность наблюдать на экране любую внутреннюю поверхность. И оценить степень коррозионного поражения. И тогда можно решать – опасен данный кузов или нет. Неужели разработчики ГОСТов о них ничего не знают? Похоже, что нет. То ли дело «узнаваемость модели», «сквозная коррозия» и прочие страшные сказки на ночь…
…и новый Регламент
Впрочем, ГОСТы – это пройденный этап. Теперь во всех отраслях живут по новым нормативным документам: Техническим регламентам Таможенного союза «О безопасности колесных транспортных средств». Когда он готовился, затеплилась надежда: теперь методика инструментального контроля состояния кузова уж точно появится. Но когда Регламент вышел, оказалось, что о коррозии кузова в нем не сказано ничего.
Правда, Правительство РФ распоряжением от 12 октября 2010 года № 1750-р утвердило перечень документов для исполнения Технического регламента. И оказалось тех документов целых 139. И под номером 35 там значится… внимание! – все тот же ГОСТ Р 51709–2001. С теми же страшилками о потере узнаваемости и сквозной коррозии. И опять ни слова об инструментальных методах контроля коррозионных поражений. Не проваливается пол в автобусе, и ладно… Авось, доедет.
Смотрите: Технический регламент разрабатывали не один год. Как тут не вспомнить блестящий скетч Аркадия Райкина. «А работал он в тресте ”Заготбревно“. Они там за год бревно выпускали. За год – бревно!»
Знаете, для треста бревно за год – это нормально. Тут за несколько лет громадный коллектив два десятка строк для Технического регламента не осилил. Вот это я понимаю – темпы! Значит, так у нас и будет: кузов отдельно, коррозия отдельно, нормативные документы отдельно, а безопасность… да кого она волнует, безопасность?
Иллюстрации предоставлены компанией ЮВК
Причины коррозии автомобиля

Коррозия — это физико-химический процесс, в котором на металл действует вода и кислород. Результатом коррозии является переход металла в химически стабильные оксиды и соли. Ржавчина является продуктом, который получается в результате коррозии. Практически все металлические элементы автомобиля имеют тенденцию к появлению коррозии. Быстрее всего она появляется в местах повреждения лакокрасочного покрытия (сколы от камней, глубокие царапины до металла и др.). У грязного автомобиля повышается риск возникновения коррозии. Грязь с влагой образуют электролит. Как известно, при наличии электролитов коррозия протекает быстрее. Особенно это справедливо для осенне-зимнего сезона использования транспортного средства.
Коррозия может появляться на отдельных местах кузова в виде пятен (местная коррозия). Примером может являться контактная коррозия, которая возникает в местах соединения деталей (точечная сварка, болты и клёпки). Высокому риску возникновения коррозии подвергаются щели и зазоры кузова машины, в которых скапливается и остаётся влага.
Влажность воздуха, а также его загрязнение выхлопными и промышленными газами, химическими продуктами и пылью, оказывают влияние на скорость атмосферной коррозии. Таким образом, коррозия в промышленных районах, с высоким уровнем загрязнения воздуха может развиваться быстрее.
Кроме ухудшения декоративных свойств лакокрасочного покрытия, коррозия ослабляет металл. Он теряет свою прочность, а при коррозии силовых элементов ухудшаться безопасность кузова.
Лакокрасочное покрытие
Основным защитным барьером металла от влаги и кислорода является лакокрасочное покрытие. Оно имеет необходимые антикоррозионные свойства, такие как водоотталкивание, низкую газо- и паропроницаемость. Значение имеют адгезия, толщина и целостность покрытия. При нанесении и отвердевании краски могут возникать дефекты. В дальнейшем они ухудшат защитные свойства покрытия, повысится проницаемость. Сама структура плёнки ЛКП может иметь поры. Это обусловлено строением, химическим составом молекул и плотностью их расположения. Вообще, любое лакокрасочное покрытие имеет поры. Их размер чрезвычайно мал. Также, причиной пористости ЛКП может стать испаряющийся растворитель при отверждении, а также разрушение структуры плёнки краски в результате старения. Важным параметром является толщина ЛКП. Покрытие должно иметь определённую толщину. Если этот параметр будет уменьшен, то покрытие будет иметь поры, и увеличивается вероятность возникновения коррозии. При нанесении лакокрасочного покрытия, чтобы соблюсти нужную толщину, правильнее наносить несколько тонких слоёв, вместо одного толстого. Нужно также помнить, что увеличение толщины плёнки выше оптимальных параметров, приведёт к ухудшению адгезионных и защитных свойств. Как только нарушится адгезия (прилипание), сразу возникает опасность возникновения коррозии.
Почему ржавеет окрашенная поверхность?
Как было сказано выше, лакокрасочные покрытия нельзя назвать абсолютно непроницаемыми. Они имеют низкую проницаемость влаги и кислорода, но всё же имеют. Слишком долгое нахождение во влажной среде неминуемо запустит процесс коррозии.
Важным фактором возникновения коррозии является воздействие агрессивной окружающей среды. Перепады температур, повышенная влажность и загрязнённый воздух, солнечная радиация, всё это действует на краску и состаривает её. Кроме того, во время движения на скорости на кузов с дороги летят мелкие и крупные твёрдые частицы, которые постепенно повреждают краску.
На появление и развитие коррозии оказывает влияние то, где хранится транспортное средство. Автомобиль должен храниться в сухом проветриваемом помещении. Но, к примеру, если выбирать между хранением на открытом воздухе и непроветриваемым сырым гаражом, то лучше выбрать первый вариант.
Песчано-солевая смесь на дорогах
В районах, где низкие температуры зимой посыпают скользкие дороги составами, содержащими соль. Это смесь технической соли и песка, которая предназначена для предотвращения гололёда и действия на уже заледенелые дороги. Песок помогает не разлетаться и не расползаться соли, а также уменьшает скольжение на дороге.
В результате действия этой смеси получается «каша» из соли и талого снега. Всё это агрессивно действует на защитное покрытие кузова, а особенно на места, имеющие микроповреждения этого покрытия. В районах, где дороги посыпают песчано-солевой смесью, отдельные части автомобиля, без своевременного ухода и обработки, ржавеют достаточно быстро.
Преобразователи ржавчины
Преобразователи ржавчины необходимы для борьбы с коррозией. Они содержат в своём составе ортофосфорную кислоту и другие добавки, которые действуют на ржавчину, приостанавливают её распространение и образуют из неё защитный слой. По сути ржавчина становится инертным соединением, никак не действующим на металл. Перед нанесением преобразователя очень важно убрать рыхлую ржавчину. Должно остаться только минимальное количество ржавчины, которую невозможно убрать инструментами.
Существуют, также, грунты-преобразователи. Они преобразуют ржавчину и подготавливают поверхность к нанесению следующего слоя необходимого покрытия.
Как предотвратить коррозию?
Лучше предотвращать появление коррозии, так как бороться с ней достаточно сложно. В большинстве случаев приходится вырезать проржавевшие места и вваривать ремонтные вставки, либо менять всю панель целиком. О способах устранения ржавчины можете прочитать статью “как убрать ржавчину с автомобиля”.
Регулярный уход за лакокрасочным покрытием автомобиля и своевременное восстановление антигравийных и антикоррозионных покрытий поможет продлить срок службы кузова и предотвратить возникновение коррозии.
Итак, можно дать следующие рекомендации и советы:
- Мойте машину каждые две недели или 1 раз в неделю, особенно в сезон гололёда, когда слякоть и соль на дорогах.
- Не забывайте мыть места под машиной и колёсные арки хотя бы 1 раз в неделю.
- Старайтесь быстро устранять повреждения краски. Если появились признаки коррозии, то сразу устраняйте их. Если скол успеть покрыть ремонтной краской до появления коррозии, то это предотвратит её появление. Если в сколе ржавчина начала появляться, то нужно счистить её наждачной бумагой (можно использовать размер абразива P220 или мельче), обезжирить и покрыть (замазать кисточкой) ремонтной краской цвета кузова.
- Наносите восковый защитный слой. Правильное нанесение воска повысит коррозионную стойкость кузова, а также даст защиту от повреждений. Воски или специальные синтетические защитные герметики заполнят поры и трещинки лакокрасочного покрытия, образуя плёнку.
- Днище и арки нужно по мере необходимости покрывать антикором.
- Большинство моющих средств смывают защитный воск с кузова. Нужно не забывать периодически восстанавливать защитное покрытие кузова.
- Если автомобиль перед мойкой весь в соли, добавьте в воду соду, чтобы нейтрализовать соль.
Примечание: Нужно помнить, что любые защитные покрытия нужно наносить на тщательно очищенную, обезжиренную и высушенную поверхность. Защитные покрытия, нанесённые не по правилам, могут навредить лакокрасочному покрытию и только ускорить возникновение коррозии.
[adsp-pro‑4]
Печатать статью
Ещё интересные статьи:
Как развивается коррозия кузова автомобиля
Коррозия кузова – одна из самых опасных «болезней» автомобиля. Этот элемент конструкции машины трудно заменить, он является самым дорогостоящим, и более уязвим к разрушению, чем закрепленная на нем механика. При благоприятных для процесса обстоятельствах ржавчина может разъесть металл в считанные месяцы и даже недели.
Проявления сухой и влажной атмосферной коррозий
Потускнение металлической поверхности, не разрушающее его структуры – внешнее проявление сухой коррозии. Всем известно, что в мегаполисах и индустриальных населенных пунктах не бывает чистого воздуха без вредных примесей. Причинами атмосферной коррозии чаще всего становятся такие факторы, как:
- Неблагоприятная экологическая обстановка региона
- Испарения активных веществ, используемых в автомобилях
- Загазованность городского воздуха выхлопами машин
- Насыщенность атмосферы отходами промышленных предприятий
- Качество покрытия дорог
Газообразные реагенты, в том числе кислород, оказывают химическое влияние на металл. Но, даже если в воздухе окажутся агрессивные газы, железу и стали не грозят структурные изменения в сухой атмосфере. Однако стоит только уровню влажности пойти вверх, резко начинает увеличиваться толщина влажной пленки на кузове, а сопротивление поверхности, напротив, уменьшается. При достижении определенной критической точки этого процесса развивается электрохимическая коррозия. Ее причины – неоднородность всех без исключения металлических поверхностей. Они могут иметь в разных случаях:
- Макровключения
- Микровключения
- Структурную неоднородность металла
- Неравномерные по толщине пленки адсорбированных веществ
- Внутреннее напряжение
- Разность температур на отдельных участках
- Рельефную деформацию металла
Таким образом, на металлическом кузове сконцентрированы множественные гальванические элементы, работающие непрерывно. Коррозийное разрушение происходит на анодных участках поверхности.
При каких обстоятельствах сухая коррозия становится влажной
Критический момент перехода сухой атмосферной коррозии во влажную электрохимическую фазу наступает тогда, когда уровень влажности достигает определенного показателя. Это время зависит от того, насколько загрязнен окружающий воздух, а также от состояния металла.
Если железо снаружи абсолютно чистое, как и окружающий воздух, то коррозия автомобиля начинает развиваться при показателе критической влажности около 70%. Но это – идеальные условия, которых на практике никогда не встречается.
Гораздо чаще разрушения начинаются при показателе 50%, а это именно тот распространенный случай, когда днище автомобиля чистится от грязи крайне редко, от случая к случаю. Постоянное присутствие на поверхности мелких пылевых и грязевых частиц приводит к конденсации влаги и адсорбции. Развитие коррозии ускоряется, если:
- Возрастает температура окружающего воздуха (например, в гараже)
- Увеличивается степень влажности воздуха
- Отсутствует вентиляция в помещении
Это следует хорошо помнить тем автолюбителям, которые не считают сильным вредом загон грязной мокрой машины в обогреваемый, но не оснащенный вентиляцией гараж. А ведь такие владельцы, по сути, помещают свой автомобиль в стабильно работающий термостат, в котором бурно разовьется процесс активного ржавления металла.
Поэтому, если сравнить холодный, но хорошо продуваемый гараж с теплым, но невентилируемым помещением, преимущества будут на стороне первого варианта. Электрохимическая коррозия кузова автомобиля ощутимо затормозится, если температура в гараже будет ниже точки замерзания. А вот температурные перепады – благоприятное условие для интенсивной конденсации влаги в полостях. И высохнуть конденсат не может, если в гараже нет вентиляции.
Атмосферная коррозия в основном имеет электрохимическую природу, то есть происходит, когда металл соприкасается с электролитом. Незащищенная поверхность кузова адсорбирует молекулы хлора, кислорода, оксидов серы и углерода и другие окислительные соединения из окружающего воздуха. Это приводит к формированию оксидной пленки различной толщины на поверхности. Контактируя с воздухом, она содержит в своем составе конденсированную влагу.
Газовая коррозия иногда имеет химическую природу. Например, разрушение двигателя в области выпускного тракта развивается в зоне повышенных температур при контакте отработанных газов и металла. Это может произойти в камере сгорания на выпускных клапанах (фасках тарелок), на разрушенном глушителе и т. д. В топливной и масляной системах может возникнуть и развиться неэлектролитическая коррозия.
Географические негативные факторы
https://www.youtube.com/watch?v=3oeKnFBHMGc
Влажность воздуха и температура влияют на толщину оксидного образования. Поэтому кузов может активно корродировать в регионах с высокой плотностью промышленных предприятий и активно развитым производством. В таких местах даже дождевая влага имеет кислый состав. В ней растворяется масса газообразных примесей, интенсивно подкисляющих воду.
Воздух вблизи крупных предприятий часто содержит повышенный объем диоксида серы (или сернистого газа). Коррозия металла ощутимо ускоряется в таких районах, даже если содержание диоксида серы составляет меньше чем 0,0001%. А анализы порой показывают намного большее содержание. Так же опасны для поверхности кузова газообразные примеси типа оксидов азота, аммиака, хлора.
Другой пример – приморские районы. Активным фактором ускоренной коррозии кузова являются в этих местах соляные взвеси в воздухе, то есть мельчайшие частички раствора морской соли. Разрушающая способность такого вещества не зависит от концентрации соли в растворе. Поэтому даже крохотная, до 1%, примесь в электролитной пленке быстро вызывает серьезные разрушения поверхности.
Ускоренная коррозия кузова автомобиля наблюдается в районах, прилегающих к химическим комбинатам. В обычной дорожной грязи и пыли содержится большая часть агрессивных соединений. Это могут быть угольная, силикатная или цементная пыль, фосфаты, хлориды, сульфаты. Все эти вредные вещества попадают в зазоры, пазы, щели, закрытые полости и постепенно скапливаются там. Достаточно автомобилю попасть под дождь, как создается коррозионно-активная среда, и кузов начинает разрушаться.
В крупных городах и мегаполисах в зимнее время на дороге образуется некий коричневый кисель из талого снега, льда, грязи, реагентов, которыми посыпают трассы для профилактики обледенения. В составе такого вещества присутствуют хлориды кальция и натрия. При контактах кузова с ними происходит активное разрушение металла. Итак, разрушительная коррозия кузова автомобиля может происходить быстрее или медленнее в зависимости от таких факторов, как:
- Условия эксплуатации машины
- Географическая область постоянного использования
- Текущее время года, сезон
- Климатическая зона
Местный и сплошной типы развития коррозии
Обширные, плохо защищенные поверхности легко подвергаются сплошной коррозии. Если это случилось, необходимо полностью обработать кузов, после чего перекрасить его. Более распространен местный тип разрушения, возникающий на отдельно расположенных участках, и поражающий металл по-разному.
- Местная щелевая коррозия
Развивается в области узких зазоров и щелей с усиленной капиллярной конденсацией воды и скоплением дорожных загрязнений. Анодные участки поверхности внутри зазоров подвергаются разрушению. Внешние кромки щелей под воздействием свободно поступающего воздуха становятся катодами. Выявить этот тип коррозии на начальном этапе трудно из-за скрытого расположения очага.
- Местная усталостная коррозия
Возникает на участках усиленного влияния знакопеременной нагрузки и агрессивной среды
- Локальная и нитевидная подпленочная коррозия
Может возникнуть в виде вздувшихся пузырей краски, под которыми образовался очаг ржавчины, или в виде покрывающей поверхность сетки трещин. Видимые разрушения находятся под слоем лакокрасочного покрытия, поэтому обнаруживаются трудно. «Нити» расходятся активно по всем направлением. При этом глубинного разрушения металла почти не происходит. Центр очага усиленно подвергается разъеданию, в том числе и до сквозной стадии.
- Местная контактная коррозия
Развивается на стыках деталей из разнородных металлов.
Так поражается кузов, если принимать во внимание причины и локализацию разрушений.
Дополнительно:
- Подпленочная коррозия может также развиться на том месте, где поврежден лакокрасочный слой. Поэтому после ударов, царапин или актов вандализма необходимо сразу принять меры. Микротрещины, сколы, царапины становятся проходными путями к поверхности металла для влаги и атмосферных загрязнений. Такой участок по отношению к примыкающему материалу становится анодным. Разрушение металла может произойти и в том случае, когда нет сколов и царапин, но ЛКП нанесено тонким слоем, с той разницей, что процесс будет протекать медленнее.
- Сварные швы – место возникновения межкристаллитной коррозии. Эта разновидность поражения особо опасна, так как при этом процессе происходит почти незаметная потеря пластичности и прочности металла. Границы зерна разрушаются избирательно, и область структурных превращений преобразуется в усиленно растворяющийся анод. Такое явление можно наблюдать и на нержавеющих сталях, и на хромистых, хромоникелевых, алюминиевых сплавах. Эти металлы легко становятся пассивными. После нарушения связей между зернами металла начинается выкрашивание, и кузов теряет свои свойства, быстро приходит в негодность.
- Многослойные сварные швы могут стать благоприятным местом для развития ножевой коррозии (местного разрушения в узкой зоне на границе кузовного металла и шва). Заводская сварка ведется при температуре расплавленного металла примерно 1300 градусов. И этот горячий материал входит в контакт с холодным металлом. Расплавленная формация растворяет карбиды титана или хрома, а после охлаждения не успевает выделить новые карбидные соединения. В твердом растворе сохраняется углерод, а из-за медленного остывания большая часть хромовых карбидов выпадает. Таким образом, узкая зона около сварного шва постепенно растворяется на межкристаллитном уровне в агрессивной среде.
- Нержавеющая сталь может подвергаться межкристаллитной коррозии, если на границах образовались примеси хромовых карбидов, резко снижающих ударную вязкость и пластичность стали. Карбиды хрома, являясь анодами, резко ускоряют протекание разрушительного воздействия. Если в технологическом процессе нарушен температурный режим, то атомы углерода подвижно перемещаются к границам. Происходит концентрация карбидов в виде сплошной цепочки, в результате чего образуется обеднение хромом. Агрессивная среда растворяет карбиды хрома, что также приводит к разрушению.
- Есть также редкая разновидность – биокоррозия, то есть разрушение материалов биологическими факторами, микроорганизмами, продуктами их жизнедеятельности
Как выглядит коррозия визуально?
- Поражение в виде пятен. Развитие происходит не вглубь, а в стороны.
- Разрушения в виде язв. Поражение развивается одновременно вглубь и по поверхности.
- Сквозные отверстия. Крайняя степень запущенности процесса – появление дыр малого и среднего диаметров, имеющих ржавые неровные края.
- Петтинговая коррозия. Другое название – точечная. Мелко иссеченная точками поверхность обманчиво целая внешне, но повреждения затрагивают глубокие слои.
Области повышенного риска
Ряд конструктивных элементов машины можно считать «группой риска». На них коррозия появляется чаще и активнее, чем на других деталях и участках. По степени разрушения коррозия кузова может быть нескольких типов:
- Проникающая
- Косметическая
- Структурная
При косметической коррозии опасность можно считать незначительной. Но, тем не менее, необходимо периодически внимательно осматривать места повреждений или растрескивания лакокрасочного слоя. В особенности – лицевые панели в нижней части, на которые постоянно попадает гравий, щебень и песок. Осмотру следует подвергнуть машину и в том случае, если она только что куплена и с конвейера сошла месяц или два назад. Возможно, при транспортировке или из-за заводского дефекта она получила повреждения, и вы уже купили машину с невидимым очагом косметической коррозии. И она проявится в первые месяцы, иногда – в первые 2-3 года эксплуатации.
Области повышенного риска образования косметических коррозийных дефектов:
- Места прикрепления молдингов
- Участки соединения фонарей и кузова
- Фланцы дверей в области кромок
- Крышка багажника
- Водосточные желоба
- Капот
- Места крепления ручек и замков
- Область контакта радиаторной решетки с кузовом
- Все сварные швы и кромки металла
Дело в том, что в местах сварочных точек защита самая слабая. Наплывы, микрозаусенцы, выплески от резки и сварки листового металла плохо удерживают лаки и краски. Если не следить за состоянием швов и участков присоединения мелких деталей, со временем косметическая коррозия станет более серьезной – проникающей. Распространенные участки поражения проникающей коррозией:
- Нижняя часть дверных панелей
- Передние крылья
- Пороги
- Коробчатые сечения нижней области кузова
Из-за труднодоступной локализации этих зон коррозия может протекать незамеченной. Кроме того, перечисленные участки сложно обработать или окрасить.
Места монтажа силовых агрегатов, элементы жесткости кузова часто подвергаются структурной коррозии. Поскольку основная часть силовых деталей расположена на днище, оно и страдает от коррозии больше других поверхностей. Абразивно-коррозионное воздействие в большей степени оказывается также на днище.
Разрушение силовых элементов приводит обычно к потере прочности и жесткости кузова. На автомобиле с таким поврежденным кузовом ездить чрезвычайно опасно. Деформация и смещение узлов, закрепленных на поверхности, делают невозможной эксплуатацию машины.
Следует учитывать тот факт, что трансмиссия, передняя подвеска, задняя подвеска и другие подкузовные детали постоянно подвергаются сильному коррозионному воздействию. Эксплуатационные характеристики этих узлов при поражении сохраняются благодаря значительной толщине металла, из которого они производятся. А вот товарный вид автомобиля сильно проигрывает.
Серьезную опасность для жизни водителя и пассажиров представляет коррозия таких участков, как гидравлическая тормозная система, сцепление, охлаждающий механизм. Эти отделы конструкции закрыты, поэтому их защищают добавками ингибиторов в рабочие жидкости. Материалы важно менять своевременно.
Как защитить автомобиль от коррозии
Этот вопрос надо решать уже на этапе покупки. Приобретая транспортное средство, учитывайте следующее. Производители разных марок автомобилей используют при изготовлении кузова разные металлы. Самый устойчивый к разрушению – тот, в составе которого есть легирующий материал. Если сравнить подверженность коррозии машин разных марок, например, Mersedes, BMW, Opel, то можно видеть, что в одинаковых условиях эти модели реагируют на вредное воздействие по-разному.
Мерседес и БМВ более крепкие, поскольку производители придают огромное значение антикоррозийной стойкости материалов. Опель быстро ржавеет даже при окружающей сухости атмосферы. Следовательно, надо приобретать машину не из соображений внешнего престижа, а с учетом будущей эксплуатации.
Если вы покупаете дешевое авто, имейте в виду, что производители такого товара все чаще используют в производстве кузова тонкую сталь, которая разрушится намного раньше, чем хотелось бы владельцу. Также при покупке недорогой машины больше вероятности, что при сварке использовались несовершенные технологии, или они были нарушены. Заводские дефекты могут существенно сократить срок жизни транспортного средства, а вовремя заметить их может только опытный мастер, имеющий профессиональное тестовое оборудование.
Машину необходимо всегда содержать в чистоте и сухости, не лениться почистить и просушить днище после поездки в дождливую и слякотную погоду. Гараж лучше оборудовать системой регулировки температуры и хорошей вентиляцией.
Многие неправильно моют свои автомобили. Ни в коем случае не рекомендуется в зимнее время мыть кузов горячей водой. Такая процедура принесет кузову больше вреда, чем пользы. Микроскопическая пленка на поверхности, которая защищает автомобиль, будет смыта струей горячей воды, и внешний вид покрытия изменится в худшую сторону.
При контакте лакокрасочного покрытия с водой высокой температуры происходит быстрое, хоть и незначительное нагревания краски или лака. А поскольку нижняя часть кузова остается холодной, начинается перепад температуры. Это приводит к отслоению краски и образованию микротрещин. Даже если для мытья зимой используется теплая вода, это представляет опасность.
При окрашивании кузова не следует стремиться нанести много слоев и утолщить тем самым покрытие. Многие ошибочно считают, что, чем больше краски нанесено на поверхность, тем лучше защищена машина от ржавчины. Но это абсолютно не так. Основная причина коррозии – не тонкий слой покрытия, а трещины и сколы на нем. Когда они появились на поверхности, локальное нанесение антикоррозийного препарата не спасет от дальнейшего повреждения.
Чтобы ржавчина не расползлась дальше, придется снять полностью защитный слой, очистить поверхность до голого металла. Только после этой операции можно приступать к антикоррозийной обработке. Нанести средство, загрунтовать, покрасить участок. А если есть вмятина или дыра – придется поработать и шпаклевкой.
Любой уважающий себя хозяин автомобиля имеет в гараже или мастерской средства по уходу за салоном, покрытием, автостеклом. У внимательного и ответственного владельца коррозия кузова автомобиля не остается долго незамеченной. Профилактический осмотр транспортного средства на предмет коррозийных разрушений надо проводить часто, хоть это может показаться затратным мероприятием. Обработка кузова нужна один раз в 2-3 года и, конечно же, при возникновении проблем – незамедлительно.
Коррозия автомобиля — самые вопиющие случаи
Немцы, французы, японцы – чьи машины ржавеют больше? На какой срок сегодня производители дают гарантию от коррозии? Что дешевле – ремонт или гарантия? Чем опасна коррозия? Вопросов очень много.
Рано или поздно ржавеет все!
Коррозия или разрушение металла естественным химическим и электрохимическим путем угрожает практически каждому транспортному средству. Она не страшна только пластику и высококачественной нержавеющей стали, неповрежденной термообработкой (например, сваркой).
Алюминий не дает надежной защиты, так как со временем окисляется, а недостаточная изоляция от стали приводит к образованию гальванической пары. Сервисы Audi, хорошо об этом знают. Крышка багажника А8 второго поколения активно корродировала в районе накладки над регистрационным знаком.
Коррозия – естественный процесс, хотя некоторые автомобили ржавеют гораздо сильнее других. Например, Skoda. Felicia второй половины 90-х годов «разрушается»медленно, а старая Октавия — быстро. Решающим фактором являются, как качество исходного материала и дополнительная защита от коррозии, так и дизайнерские линии. Слишком сложные профили в зонах риска, неправильное расположение дренажных каналов или даже чересчур большой сварочный ток приводят к развитию коррозии.
Ржавый ад Мерседес
До сих пор многие автомобилисты оценивают качество машины в зависимости от страны ее происхождения. Преждевременная коррозия Lada и Dacia сегодня никого не удивляет, как и долголетняя стойкость кузова Volvo. Коррозия автомобилей итальянских и французских брендов в восьмидесятых годах считались стандартом. Сегодня же владельцы «французов» и «итальянцев» смотрят свысока на машины именитых брендов. В частности продукция PSA (Peugeot/Citroen) с начала нового тысячелетия имела лучшую защиту от коррозии, чем автомобили концерна VW. В то время как 15-летний Fiat Punto обзаведется всего лишь парой «бородавок», старый Mercedes E-Class становился похож на «металлом».
Mercedes E-Class W210
В свое время многие клиенты Мерседес были потеряны на всегда. Одинаково быстро ржавели и А-класс, и S-класс, и Vito. Не так давно, до 2006 года проблема касалась A-Class (W169) второго поколения. Самой не стойкой к коррозии была модель E-Class W210 (1995-2003). Чуть реже проблема затрагивала C-Class W203 — до 2003 года. Но по факту зацвести мог любой Mercedes до 2005 года выпуска, даже новый W211. Наилучшим образом семя зарекомендовал ML, который собирался в Америке.
Mercedes E-Class W210
Немцы тоже ржавеют
Многие без лишних слов считают немецкие автомобили качественными. Однако они тоже ржавеют довольно часто. Например, Ford Mondeo III (2000-2007), Ford Focus I и чуть меньше Focus II. Opel Astra G тоже в аутсайдерах: найти дырявые колесные арки, а иногда и крышку багажника несложно. Обо всех предыдущих моделях этих брендов даже не стоит и говорить.
Ford Focus II
Старые машины Volkswagen тоже страдали от коррозии. Ситуация значительно улучшилась в 1997 году с приходом Passat B5 и Golf VI. Но как это ни парадоксально, сегодня в Passat B6 2005-2010 года порой обнаруживаются небольшие очаги под тонкими боковыми молдингами дверей. Не эпидемия, но все же.
Стабильное качество с середины 80-х годов демонстрируют лишь Audi и Porsche, за исключением Boxster. В то время в автомобилях бренда BMW довольно часто встречалась коррозия задней части порогов, задних крыльев и крышки багажника. Даже у сравнительно молодых BMW 3 E46 (1998-2005), 5 E39 (1995-2003). Более поздние модели пока таких недугов не показывают.
Азиатские бренды
Коррозия считается распространенным явлением среди автомобилей японских брендов, примерно до 2002 года. Самыми устойчивыми себя зарекомендовали модели Toyota и Lexus. Лишь эпизодически обнаруживается коррозия порогов в Toyota Urban Cruiser.
С Honda все стало в порядке после 2003 года (Accord, Legend и CR-V второго поколения). В случае с Civic выраженная коррозия существовала только у модели Civic 6G (до 2001 года). В Сивик седьмого поколения лишь иногда обнаруживались точечные очаги.
Огромное разочарование принес Nissan Almera N16 (2000-2006). Удивляли и молодые модели Mazda. Помимо пожилого родстера MX-5, который эксплуатируется преимущественно в сухую погоду, коррозия атаковала Mazda 3 и Mazda 6 первого поколения (2002-2007). Во всех этих трех моделях через несколько лет зацветали края задних крыльев.
Mazda MX-5
У автомобилей корейских марок ситуация немного лучше, чем обычно принято считать. «Ржавые куски» остались в середине 90-х годов. Более поздние модели имеют лишь незначительные проблемы. Например, первое поколение Hyundai i30 и Kia Ceed: коррозия кромок задних дверей и двери багажника, рамки стекол.
Внедорожники ржавеют чаще
Внедорожники находятся в группе риска. Причины очевидны – ссадины после контакта с различными предметами и преодоление грязи и воды. Самый известный пример – Suzuki Jimny. Внешние кузовные панели в период шестилетней гарантии выдержат все что угодно. Но шасси, рама и вакуумные трубки подключения переднего моста могут измениться до неузнаваемости.
Лишь немногим лучше ситуация с Mitsubishi Pajero III (2000-2006 года). Из корейских внедорожников чаще страдает Kia Sorento первого поколения (2002-2009). В его случае виноваты скопление грязи и воды под пластиковыми накладками и плохая защита по краям дверей.
Suzuki Jimny
Гарантия – защита или хитрость?
Гарантия производителя от сквозной коррозии не отражает реальное качество антикоррозионной защиты. К тому же следовало бы уточнить, на что же все-таки дается гарантия производителя. Реальная гарантия подразумевает защиту «от сквозной коррозии изнутри», т.е. отсутствие коррозии под оригинальной краской, неповрежденной в результате аварии или воздействия агрессивной среды.
Кроме того, гарантия распространяется обычно на пороги, крылья, двери, капот и т.п., т.е. на локальные детали, которые не потребуют больших финансовых затрат и много времени на демонтаж и восстановление. Лишь некоторые производители готовы сделать исключение. Например, Jeep прямо заявляет, что гарантирует компенсацию стоимости ремонта и замены любых элементов, покрытых ржавчиной, лишь в том случае, если коррозия не стала следствием внешних повреждений.
Mercedes готов предоставить длительную гарантию защиты от коррозии лишь в том случае, если автомобиль на протяжении всего времени будет обслуживаться в официальном сервисе.
Mercedes Vito
Что дешевле: длительная гарантия или ремонт за свой счет?
Большинство брендов, как и Мерседес, готовы за свой счет заменить ржавое крыло на автомобиле старше 10 лет лишь в том случае, если вы каждый год будете терпеливо оплачивать счета за техобслуживание в официальном сервисе.
Но есть несколько оговорок. Во-первых, не все дилеры будут готовы признать коррозию старого автомобиля производственным дефектом. Во-вторых, отремонтировать небольшой дефект гораздо дешевле, чем каждый год ездить в сервис к «официалам» на ТО.
Mitsubishi Pajero (2000-2006)
Профилактика
Многие автомобилисты не раз замечали интересный парадокс. Автомобили, хранящиеся в гараже, имеют лучшее состояние лакокрасочного покрытия, чем те, что стоят на улице. Но именно гаражные автомобили нередко зацветают быстрей. Этому способствуют плохо проветриваемые гаражи. Зимой соленая слякоть остается внутри всевозможных кузовных щелей и ниш. Теплый двигатель нагревает воздух, создавая благодатные условия для разрушительного воздействия соли. Стоянка на улице под солнцем и ветром – самая дешевая и простая профилактика коррозии.
Сегодня существует большое количество средств для защиты кузова, как снаружи, так и внутри. Многие сервисы готовы выполнить трудоемкую и длительную процедуру антикоррозионной защиты, но не всегда с хорошим качеством.
Dacia Logan
Гарантия от сквозной коррозии
В настоящее время производители гарантируют следующие сроки от сквозной коррозии.
- Alfa Romeo — 8 лет
- Audi — 12 лет
- BMW — 12 лет
- Citroën — 12 лет (Грузопассажирские модели – 6 лет)
- Chevrolet — 6 лет
- Chrysler — 8 лет
- Dacia — 6 лет
- Fiat — 8 лет
- Ford — 12 лет (Ка — 8 лет)
- Honda — 12 лет
- Hyundai — 12 лет
- Jaguar — 6 лет
- Jeep — 7 лет
- Kia — 12 лет
- Lancia — 8 лет
- Land Rover — 6 лет
- Lada — 3 года (Нива) или 6 лет (остальные)
- Mazda — 12 лет (BT-50 — 6 лет)
- Mercedes-Benz — 30 лет
- Mini — 12 лет
- Mitsubishi — 12 лет
- Nissan — 12 лет
- Opel — 12 лет
- Peugeot — 12 лет (Грузопассажирские модели – 6 лет)
- Renault — 12 лет (Master — 6 лет)
- Seat — 12 лет
- Subaru — 12 лет
- Suzuki — 12 лет (Jimny — 6 лет)
- Skoda — 12 лет
- Toyota — 12 лет
- Volkswagen — 12 лет
- Volvo — 12 лет (1-е поколение XC90 8 лет)
Где искать ржавчину?
Mazda 6 II
Еще «шестерка» первого поколения имела огромные проблемы с коррозией. Удивительно, что Мазда не сделала правильные выводы, и вторая версия Мазда 6 тоже ржавеет.
Проблемные места:
- Задние крылья. Обычно первые следы коррозии появляются в этом месте. Здесь пластик трется о крыло и повреждает лакокрасочное покрытие. Остальное делает вода.
- Передние крылья. Здесь коррозия атакует стык крыла и порога. Проблему вызывают внешние факторы, для борьбы с которыми владельцы устанавливают брызговики.
- Капот и крыша. Камни повреждают слишком тонкий лак. На незащищенные места попадает вода, которая вступает в реакцию с металлом, и появляется ржавчина.
Dacia Logan I
Дачия Логан – бюджетный автомобиль. Производитель использовал дешевые технологии Рено (но у нее есть и свои преимущества). Модель недостаточно хорошо защищена от коррозии. Сегодня это уже не просто проблема, так как речь идет о машине, которая стоит мало, а качественный кузовной ремонт обходится дорого.
Проблемные места:
- Шасси. В некоторых случаях это может быть опасно. Например, ржавеют места крепления задних амортизаторов.
- Кузов. Как правило, сначала будет ржаветь металл вокруг заливной горловины, а затем желоба под уплотнениями.
- Моторный щит. Это одно из сложных в ремонте мест. Коррозию можно встретить и в других труднодоступных местах.
Ford S-Max I
В последнее время Форд улучшил защиту своих моделей. После очень сильно коррозирующего Escort и менее проблемного Focus I настало время для лучших, хотя и все еще не идеально защищенных от коррозии автомобилей (например, Focus II).
Среди последних моделей выделяется S-Max. У него есть проблемы с защитой кузова. На данный момент они не слишком распространенны, но упоминания о коррозии встречается все чаще. Причем, симптомы наблюдаются даже в рестайлинговых образцах.
Проблемные места:
- Капот и крыша. Проблема касается экземпляров, выпущенных после фейслифтинга (с 2011 года). Слишком слабая оцинковка металла.
- Под дверными уплотнителями.
- Ходовая часть. Проблема не так велика, но перед покупкой внимательно осмотреть низ будет не лишним.
Suzuki Grand Vitara
Коррозия сеет хаос в основном в экземплярах начального периода производства. Это не единственный Сузуки, плохо защищенный от «коричневой чумы». Она наблюдается в SX4 и его близнеце Fiat Sedici, а так же в Swift и Jimny.
Проблемные места:
- Днище. Коррозия в первую очередь воздействует на места соединения листового металла. Проблема проявляется в основном в машинах начального периода производства. На данный момент, до сквозной коррозии еще далеко, но в будущем это может стать серьезной проблемой.
- Вспомогательная балка. Коррозия этой детали пока не оказывает влияния на безопасность, но может вызвать трудности при ослаблении болтов, используемых для регулировки подвески.
- Поверхностная ржавчина наблюдается и на всей выхлопной системе.
Mitsubishi L200
К сожалению, коррозия здесь явление частое. Если вспучивания краски на кузовных элементах не столь опасны с точки зрения эксплуатации, то коррозия рамы в будущем может стать реальной проблемой.
Проблемные места:
- Рама. Очаги ржавчины пока еще не угрожают безопасности, но со временем коррозия рамы будет развиваться.
- Грузовой отсек. Листовой металл недостаточно хорошо защищен от погодных условий.
- Кузовные элементы. В большинстве случаев коррозия сначала атакует капот автомобиля.
Hyundai i30 I
Наиболее уязвимы машины начального периода производства. Коррозия встречается и в экземплярах, собранных после 2010 года.
Проблемные места:
- Крышка багажника. Ржавчина чаще всего появляется в районе 3-го стоп-сигнала, по краям крышки, а так же возле крепления номера.
- Двери – передние и задние. Обычно коррозия наблюдается под уплотнителями и в местах соединения листового металла. Ее также можно обнаружить в нижней части дверей – по краям.
- Пороги и ходовая. Помимо порогов и закрытых профилей, ржавчина развивается и на элементах шасси.
Kia Ceed I
Киа Сид первого поколения не относится к автомобилям, особо устойчивым к коррозии. Как и в родственном Hyundai i30 (они имеют общую техническую базу) ржавчина появляется на задней двери. Есть вопросы и к защите днища. Ряд автомобилей имели дефект окраски – слезало покрытие. Те же проблемы затронули Venga и Soul начального периода производства.
Проблемные места:
- Крышка багажника. Это одно из самых чувствительных мест. Коррозия обнаруживается вокруг третьего стоп-сигнала, по нижнему краю дверей, а иногда и вместе стыка со стеклом.
- Днище. Плохо защищены замкнутые профили и элементы ходовой. Коррозия чаще всего поражает места стыков листового металла, а так же точек крепления.
Skoda Superb I
Проблемы затронули автомобили, выпущенные до августа 2006 года, т.е. до рестайлинга. Следы коррозии можно обнаружить на крышке багажника (в непосредственной близости от номера, по краям дверей) и на стойках кузова.
Дополнительного внимания требуют копии, произведенные в 2004 году. Именно в этот период Шкода боролась с дефектным ЛКП – пузыри появлялись очень быстро. Производитель устранял дефект по гарантии.
Проблемные места:
- Крышка багажника. Типичное место. Обычно ржавчина появляется в точках крепления номера и по краям крышки.
- Передние и средние стойки кузова. Сначала возникают небольшие точки, которые со временем прогрессируют.
- Края дверей.
Volkswagen Passat B6
Недомогание в основном касается автомобилей начального периода производства, собранных до 2007 года. Характерные области – передние крылья и крышка багажника.
Проблемные места:
- Передние крылья. В копиях начального периода производства влага скапливалась под подкрылком, что вызывало коррозию.
- Крышка багажника. Ржавчина появлялась рядом с эмблемой и лампой подсветки номера.
- Края дверей. Рыжие пятна часто возникают в нижней части дверей, куда попадает вода и соль.
Неприятность затрагивает автомобили, собранные на испанском заводе в 2005-2007 годах. Дорожная соль оказывает вредное воздействие на несущие элементы – прежде всего раму, что в будущем может угрожать безопасности. Подвержен коррозии и кузов. Да, производитель давал 12-летнюю гарантию от сквозной коррозии, но требовал ежегодной проверки кузова в официальном сервисе. Кроме того, как показала практика, дилеры не всегда чувствовали ответственность и не спешили устранять ржавчину.
Проблемные места:
- Рама и ходовая часть. Помимо рамы ржавчина атакует подвеску, тормоза, компоненты трансмиссии и почти всю выхлопную систему.
- Грузовой отсек. Из-за скопления влаги здесь тоже процветает ржавчина. Некоторые автомобили подлежали ремонту в рамках гарантийного ремонта.
- Крыша. Коррозия возникает не только на рамке ветрового стекла, но и в месте крепления рейлингов. Это распространенная проблема, хотя пока и не слишком серьезная. Но что будет через несколько лет?
Коррозия кузова автомобиля. Защита и профилактика.

Коррозия кузова автомобиля — это, как минимум один раз в пару лет собственник эксплуатируемого им авто понимает, что его любимцу необходима защита кузова от коррозии. Он с сожалением отмечает небольшие пятна ржавчины, размножение грибка на лакокрасочном покрытии или порыжение сварных мест, на краях дверей, на порогах и арках.
Независимо от того, стоит ли автотранспорт в гараже на консервации, или постоянно в пути, появление коррозии неизбежно.
Прежде чем рассматривать варианты разрешения проблемы, лучше всего ознакомиться с причинами ее возникновения.
В чем причины возникновения коррозии? Почему из двух совершенно одинаковых автомобилей один будет десятки лет ездить не поврежденный, а другой начнёт разрушаться уже через пару лет эксплуатации? Как найти виновного в этом?
Если два авто используются идентично, а их кузова поражаются по-разному, то причины заключаются исключительно в следующем:
- Качество металла, который использует завод — производитель.
- Неправильное хранение и уход за автомобилем самим собственником.
- Первопричина появления коррозии любого отечественного автомобиля заложена еще в металле. Для изготовления кузовных деталей заводы — производители зачастую используют некачественный металл, в котором уже заложены грибки и ржавчина. Это результат использования вторичного сырья, которое не подвергается никакому контролю соблюдения стандартов. Кроме этого, отечественный автором попросту пренебрегает антикоррозийной защитой, или она очень слабая. Старые же иномарки просто разрушаются от езды по нашим «трассам», щедро усыпанным всевозможными реогентами, от неправильного ухода и от неблагоприятных климатических условий.
- Даже при покупке новой иномарки водитель может столкнуться с таким явлением, как коррозия кузова, через небольшой промежуток времени. Многие автозаводы сейчас просто экономят на оцинковке кузова и установке защитных элементов.
Так что, как всегда, решение проблем, связанных с защитой кузова от коррозии или устранением уже образовавшихся дефектов лежит исключительно на собственнике автомобиля. Главное — вовремя предупредить образование коррозии или принять меры для борьбы с ней.
Коррозия кузова автомобиля — методы защиты.
Еще при приобретении новенького автомобиля в салоне, его владелец должен позаботиться о приобретении и установке механических средств защиты от повреждений.
Это подкрылки, пластиковые накладки, брызговики, металлическая защита двигателя.
Нелишними будут специальные пленки на порогах и крыльях автомобиля.
Также следует менять в осенне-зимний период текстильные коврики на резиновые с бортиками. Это поможет избежать промокания ковра и образования между ним и кузовом влаги.
Далее выполняются профилактические меры с применением защитных антикоррозийных химических средств. Ошибочно думать, что защита кузова необходима только снаружи. Основная профиактика заключается в обработке именно труднодоступных мест внутри кузова.
Для этого нам понадобится:
- Помещение с подъемником;
- Набор инструментов для демонтажа/монтажа салона;
- Компрессор;
- Пистолет под мовиль и мастику;
- Пистолет под жидкую резину;
- Мовиль;
- Мастика.
В мастику можно добавлять бензин и отработку масла для лучшего разжижения смеси и удобства её использования при нанесении пистолетом.
Приступим к работе:
- Для начала полностью разбираем салон, снимая дверные карты, сидения, ковёр с полов.
- После демонтажа салона мы увидим, что в порогах, лонжеронах и стойках с внутренней стороны есть резиновые пробки. Открываем их и видим, что внутри сухо. Технологические отверстия также есть и с обратной стороны.
- Берём специальный пистолет с резиновой шлангой, и заливаем эти отверстия, нажимая и вытягивая шланг постепенно. В это время большой слой мовиль обволакивает все труднодоступные поверхности.
- Повторяем ту же процедуру в стойках и лонжеронах через технологические отверстия.
- В задних стаканах есть большие продольные отверстия по крыло с внутренней стороны. Заливаем мовиль в арку с внутренней стороны заднего крыла. Оно не съёмное, поэтому доступ к нему только с внутренней стороны кузова.
- Переходим к передней части кузова. Если возможен съем крыла, снимаем его. Под крылом и в стаканах есть труднодоступные места, не обработав которые в итоге получаем разрушения. В них тоже есть технологические отверстия, о которых многие и не догадываются. Обрабатываем крыло с внутренней стороны мастикой и устанавливаем его на место.
- На днище наносим мастику равномерным слоем по всей поверхности.
- Собираем салон, устанавливаем брызговики, подкрылки и другие аксессуары для механической защиты.
После длительной эксплуатации автомобиль уже столкнулся с коррозией. Скорее всего тут не избежать сварочных работ. Их лучше всего доверить специалистам. Возможно, некоторые детали придется полностью вырезать и заменить. Все новые детали необходимо предварительно подготовить к сварке, прогрунтовав их внутренние части. После сварки грунтуются все наружные поверхности деталей, наносится лакокрасочное покрытие. На скрытые от ЛКП детали наносится жидкая резина и мастика. Далее можно готовить авто к дальнейшей эксплуатации. Для этого проводятся те же самые профилактические меры, что и в новом авто.
Коррозия кузова автомобиля и химические средства защиты.
Современный рынок предлагает автолюбителям множество разнообразных способов защиты металлических деталей кузова автомобиля от коррозии. Их использование может способствовать более продолжительной эксплуатации авто. Лучше всего обработку проводить сразу же после ремонтных работ или непосредственно после покупки автомобиля. Среди них и мастики, и грунты с различными назначениями, например, цинкосодержащие грунты.
Важно! Т.к. зачастую используется обычный Мовиль, то следует знать, что он не совместим с многими синтетическими мастиками.
Коррозия кузова автомобиля — профилактика.
- Традиционное гаражное хранение автомобиля, где присутствуют подвалы с овощами, где есть перепады температуры, разная степь влажности — все это только способствует развитию коррозии кузова.
Специфический микроклимат гаража способствует росту грибков и появлению ржавчины. Мы пытаемся спрятать транспорт в гараже от неблагоприятных внешних воздействий и воров, а сами крадем у своего автомобиля его здоровье.
2. Доказано, что стоянка на открытых площадках под навесом куда полезнее, чем в герметичном гараже. Ведь в таких условиях машина постоянно находится в естественных климатических условиях.
При хранении автомобиля на открытой площадке в зимний период нельзя использовать чехлы из промокающих тканей. Намокший чехол может прилипать к внутренним частям кузова и повреждать ЛКП.
3. Чистота — залог здоровья. Также и с автомобилями. Смесь воды, пыли, дорожных регентом и химикатов представляет прямую опасность для кузова, особенно если автомобиль редко подвергается обычной мойке.
Рекомендуется чаще мыть автотранспорт, желательно с применением восковых покрытий, которые имеют свойство отталкивать от поверхностей влагу и грязь.
4. Установка на авто специальных «кенгурятников», дуг, отбойников, является не только элементом тюнинга, но и дополнительной защитой кузова от механических повреждений. Не забывайте, что каждая царапина на металле — путь к его разрушению.
5. Существуют специальные средства защиты хромированных деталей. Например, специальный лак Антикор. При его применении на поверхности образуется блестящая тонкая , защищающая хромированное покрытие от внешних воздействий.
Можно защитить и резиновые уплотнители или детали на кузове. Делается это с помощью нанесения специальных паст, которые после нанесения должны сутки сохнуть. Можно просто протирать резиновые поверхности силиконом или глицерином.
В процессе эксплуатации автомобиля, независимо от того, старый он или новый, стоит внимательно относиться к ухожу за ним и его хранению.
Любые профилактические меры, направленные на защиту кузова авто от коррозии позволит сэкономить немалые средства, которые придётся потом вложить в его капитальный ремонт. Желательно каждые полгода проводить профилактических осмотр, направленный на выявление очагов коррозии.
Как и почему появляется ржавчина на автомобиле, и как ее избежать (основные правила)
Ржавчина может появиться на любом автомобиле: причины, последствия, варианты борьбы
Зловещее коричневое пятно на крыле, пузырь на краске в нижней части двери, внезапно намокшие коврики в салоне автомобиля после проезда большой лужи – все это явные признаки того, что вашу машину начала подтачивать такая медленная убийца, как ржавчина.
Ржавчина. Многие ее недооценивают. Многие не знают, что именно эта несерьёзная на первый взгляд беда регулярно отправляет на свалку десятки тысяч автомобилей. Но проблема предотвратима, и с ней можно и нужно бороться!
С металлами на основе железа борьба с окислением может быть Сизифовым трудом, ведь даже несмотря на передовые покрытия и сплавы, разработанные профессиональными химиками и инженерами, нестабильный химический состав стали в своей изначальной форме означает, что она всегда будет подвергаться ржавлению в естественной среде. Впрочем, это вовсе не означает, что ваша машина обречена. Понимая процесс окисления металла и зная проблемные участки на кузове вашего автомобиля, вы сможете продлить жизнь своему автомобилю.
Можно ли избежать встречи с ржавчиной?
«Ржавчина» – термин неспециалиста для электрохимического разрушения металла, основанного на железе, называемого окислением. В этом процессе молекулы на поверхности вступают в реакцию с кислородом воздуха и производят новую молекулу Fe2O3, известную также как оксид железа. Железо и большинство сталей рано или поздно полностью распадутся на оксид железа и составные элементы, дайте им достаточно времени.
Примеров использования в автопромышленности сталей разного качества можно привести массу. Это не только набившие оскомину автолюбителям 90-х годов «Жигули» и «Москвичи», которые, кажется, ржавели еще на сборочной линии. Схожие проблемы были у автопроизводителей США 70-х годов, когда ржавчина начинала распространяться по автомобилям, которые еще не успели выехать за ворота дилерского центра. Или проблемы с ЛКП и металлом на совсем современных моделях. Например, Hyundai Creta. Помните? (Топ-5 самых ужасающих фактов о Hyundai Creta).
В то же время необработанная сырая листовая сталь может очень долго сопротивляться ржавлению, не рассыпаясь на составные части в течение нескольких лет.
Отсюда мы можем сделать первый вывод: если вы покупаете автомобиль (даже если это новая модель и машину забираете из салона), обязательно пробегитесь по форумам и поищите, ржавеют ли данные модели автомобилей конкретного года выпуска. Иначе вам может очень не повезти и вы попадете на какую-нибудь партию машин, в которой, по неизвестной причине, была применена сталь ненадлежащего качества. Как вы понимаете, такие автомобили будут гнить. Такие случаи редки, но бывают. Поэтому будьте бдительны.
Вот вы стали обладателем или давно являлись владельцем автомобиля. Если вы приобрели новую машину и рассчитываете использовать ее на протяжении долгого периода времени – от пяти лет и выше, поздравляем, у вас есть шанс увидеть все этапы развития разрушения кузова.
Рассмотрим три основных вида ржавчины, а затем обсудим, как ее можно избежать или «вылечить».
Поверхностная ржавчина (первая стадия)
Первые признаки проблемы появляются в трещинах и царапинах на краске. Уровень сложности: легко исправить.
Ржавчина «охотится» на структурные и химические примеси в металлических сплавах на микроскопическом и молекулярном уровнях. Чистое железо не окисляется так агрессивно, как более дешевый материал с большим количеством примесей. Это легко понять, если взглянуть на старые детали от премиальных немецких автомобилей 70-х, 80-х годов. Даже неокрашенные элементы, находясь на открытом воздухе, под дождем и снегом, хоть со временем и покроются ржавчиной, но проникновение окисления будет не настолько глубоким, как в случае с машинами 90-х и нулевых годов XXI века.
Дело в том, как вы понимаете, что в дорогих моделях престижных марок использовались более качественные сплавы, что помогало заложить большую износостойкость во все детали автомобиля, в том числе и кузов.
К сожалению, железо не особенно хороший материал для создания автомобилей. Добавление небольшого количества углерода в железо создает сталь, которая предлагает значительное улучшение гибкости, прочности на растяжение и формуемости при прессовании панелей. Но по определению это добавляет примеси – примеси, которые ускоряют процесс ржавления.
Вторая стадия (начинается проникновение в структуру металла)
Химический процесс разрушает поверхность и уменьшает прочность металла.
Распространение ржавчины вглубь стали зависит от множества разнообразных факторов:
сплава, толщины детали, окружающей среды (наличие снега, реагентов, ускоряющих процесс разложения, перепадов температуры) и типа термообработки детали.
Легирующие элементы, такие как никель и хром, могут добавляться для предотвращения ржавчины, но ничто не способно на 100% защитить деталь — все в конечном итоге корродирует.
Реагент – это вообще отдельная тема. Эффект ржавления ускоряется наличием любого вида соли. Соли с дороги и другие загрязняющие элементы, растворенные в воде, действуют как электролиты. Попадая на незащищенное место, где происходит химическая реакция, они значительно ускоряют обмен молекулярных компонентов.
На практике можно сказать следующее: грязный автомобиль ржавеет быстрее чистого. Это также объясняет давно отмеченный факт, почему автомобили в странах с северным климатом, где соли и реагенты используется зимой, склонны к гниению.
Проникающая ржавчина (третья стадия)
После длительного воздействия процесса окисления сталь превращается в хрупкий оксид железа. Образуются сквозные отверстия.
Смотрите также: Топ-10 самых лучших в мире суперкаров
Автопроизводители много делают, чтобы попытаться предотвратить коррозию. Огромное количество испытаний и целые разделы материаловедения посвящены сохранению кузова вашего автомобиля. Компоненты из алюминия и магния очень помогают в борьбе с ржавчиной. Они практически не подвержены окислению, а их запаса прочности хватит на десятилетия вперед. Однако эти металлы достаточно дороги, чтобы их можно было использовать для такой большой детали, как кузов.
Современная листовая сталь еще на этапе ее производства на сталелитейном заводе выходит с разнообразными защитными покрытиями. На автомобильном заводе к этому добавляются дополнительные защитные покрытия, в том числе оцинковка и толстый слой поверхностной защиты днища автомобиля, который в буквальном смысле запечатывает кузов от воздействия элементов кислорода и разрушительной внешней среды.
Увы, со временем любая нанесенная на металл защита стирается, истончается и в некоторых местах полностью уходит. Металл оголяется, начинается процесс разрушения.
Совет: немногие так делают, но важно минимум раз в год, после зимы, обследовать чисто вымытый (в идеале вымыть нужно и днище) автомобиль на наличие повреждений защитного слоя. В том случае если обнаружен скол или глубокая царапина, дошедшая до металла, потребуется нейтрализовать повреждение, прекратив доступ воздуха к поврежденной части поверхности.
В зависимости от глубины и места повреждения для этих целей возможно использование грунтовки с последующим нанесением краски (при небольшом повреждении), преобразователя ржавчины, с герметизацией очага от доступа кислорода, нанесение антикора на днище, если защитный слой внизу был поврежден в нескольких местах. При среднестатистической эксплуатации его повреждение происходит через три года.
Бдительность и уход за автомобилем – вот залог длительной работы кузова.
Профилактика
Лучший совет самый очевидный: регулярно мойте автомобиль, чтобы очистить кузов и днище (хотя бы раз в год, после зимы) от грязи и солей, которые приводят к коррозии. Не столь очевидный совет – проверить дренажные отверстия в нижней части дверей и порогах. Если там будет застаиваться вода, это приведет к неминуемому ржавлению.
Но если ржавчина все же появилась, это не такая уже великая проблема. Дело в том, что ржавление можно остановить на любом этапе.
Поверхностная ржавчина
В большинстве случаев поверхностная ржавчина образуется на месте слома краски из-за механического или ультрафиолетового повреждения. Первая стадия ржавления не принесет больших проблем кузову вашего автомобиля. В зависимости от толщины металла и качества сплава до третьей стадии может пройти не один год.
Несмотря на это, лучше всего избавиться от поверхностной ржавчины, как только вы ее обнаружите. Исправление не отличается от общего ремонта ЛКП. О том, как заделывать царапины и другие повреждения, мы много писали.
Начните с использования абразивного круга или наждачной бумаги, чтобы снять слой краски и счистить коррозию до тех пор, пока не появится металл. Затем нанесите грунтовку, затем краску, затем покройте лаком. Готово! Подробности читайте здесь: Как самостоятельно покрасить свой автомобиль: подробная инструкция к действию
Вторая стадия
Вы не зачистили ржавчину на первой стадии, и теперь на кузове красуется ржавый пузырь под краской. Молекулы ржавчины физически больше, чем молекулы железа или стали. В результате ржавчина самораспространяется путем расширения, затрагивая и разрушая свежий металл. Если ее полностью не убрать, процесс гниения не остановится.
При ремонте детали нужно использовать преобразователь ржавчины, а также щетку с жесткой металлической щетиной, наждачку или абразивный диск. Зачищаем очаг до ровной поверхности, затем наносим грунтовку и краску.
Проникающая ржа
В конце концов основной металл отслаивается и на его месте образуется отверстие. Теперь у вас есть большая проблема, и у вас есть два варианта. Вы можете заменить панель (если есть такая возможность), или придется вырезать сгнившие части и просить вварить заплатки из нормального металла.
Полезно сравнить (немецкий опыт): Вот что происходит с кузовом автомобиля, даже если вы о нем заботитесь
А вот если проржавела рама, это означает, что структурная целостность автомобиля может быть нарушена. Раму своими силами не починить. Либо менять на новую, либо обращаться за советом к профессионалам.
Коррозия металлов. Почему ржавеют автомобильные кузова?
Коррозия металлов, как известно, приносит много бед. Уж не вам ли, уважаемые автовладельцы, объяснять, чем она грозит: дай ей волю, так от машины одни покрышки останутся. Поэтому, чем раньше начнется борьба с этим бедствием, тем дольше проживет автомобильный кузов.
Чтобы быть успешными в борьбе с коррозией, необходимо выяснить, что же это за «зверь» и понять причины ее возникновения.
Сегодня вы узнаете
Есть ли надежда?
Ущерб, наносимый человечеству коррозией, колоссален. По разным данным коррозия «съедает» от 10 до 25% мировой добычи железа. Превращаясь в бурый порошок, оно безвозвратно рассеивается по белому свету, в результате чего не только мы, но и наши потомки остаемся без этого ценнейшего конструкционного материала.
Но беда не только в том, что теряется металл как таковой, нет — разрушаются мосты, машины, крыши, памятники архитектуры. Коррозия не щадит ничего.
Неизлечимо больна та же Эйфелева башня — символ Парижа. Изготовленная из обычной стали, она неизбежно ржавеет и разрушается. Башню приходится красить каждые 7 лет, отчего ее масса каждый раз увеличивается на 60-70 тонн.
К сожалению, полностью предотвратить коррозию металлов невозможно. Ну, разве что полностью изолировать металл от окружающей среды, например поместить в вакуум. 🙂 Но какой прок от таких «консервированных» деталей? Металл должен «работать». Поэтому единственным способом защиты от коррозии является поиск путей ее замедления.
В незапамятные времена для этого применяли жир, масла, позднее начали покрывать железо другими металлами. Прежде всего, легкоплавким оловом. В трудах древнегреческого историка Геродота (V в. до н.э.) и римского ученого Плиния-старшего уже есть упоминания о применении олова для защиты железа от коррозии.
Интересный случай произошел в 1965 году на Международном симпозиуме по борьбе с коррозией. Некий индийский ученый рассказал об обществе по борьбе с коррозией, которое существует около 1600 лет и членом которого он является. Так вот, полторы тысячи лет назад это общество принимало участие в постройке храмов Солнца на побережье у Конарака. И несмотря на то, что эти храмы некоторое время были затоплены морем, железные балки прекрасно сохранились. Так что и в те далекие времена люди знали толк в борьбе с коррозией. Значит, не все так безнадежно.
Что такое коррозия?
Слово «коррозия» происходит от латинского «corrodo – грызу». Встречаются ссылки и на позднелатинское «corrosio – разъедание». Но так или иначе:
Коррозия – это процесс разрушения металла в результате химического и электрохимического взаимодействия с окружающей средой.
Хотя коррозию чаще всего связывают с металлами, ей также подвергаются бетон, камень, керамика, дерево, пластмассы. Применительно к полимерным материалам, правда, чаще используется термин деструкция или старение.
Коррозия и ржавчина — не одно и то же
В определении коррозии абзацем выше не зря выделено слово «процесс». Дело в том, коррозию частенько отождествляют с термином «ржавчина». Однако это не синонимы. Коррозия — это именно процесс, в то время как ржавчина — один из результатов этого процесса.
Также стоит отметить, что ржавчина — продукт коррозии исключительно железа и его сплавов (таких как сталь или чугун). Поэтому, когда говорим «ржавеет сталь», мы подразумеваем, что ржавеет железо в ее составе.
Если ржавчина относится только к железу, значит другие металлы не ржавеют? Не ржавеют, но это не значит, что они не корродируют. Просто продукты коррозии у них другие.
Например, медь, корродируя, покрывается красивым по цвету зеленоватым налетом (патиной). Серебро на воздухе тускнеет — это на его поверхности образуется налет сульфида, чья тонкая пленка придает металлу характерную розоватую окраску.
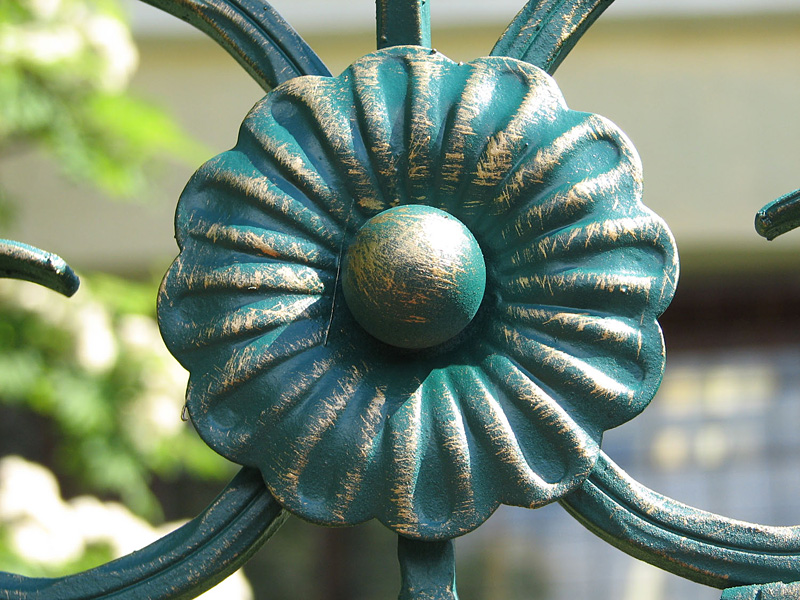
Патина — продукт коррозии меди и ее сплавов
Механизм протекания коррозионных процессов
Разнообразие условий и сред, в которых протекают коррозионные процессы, очень широко, поэтому сложно дать единую и всеобъемлющую классификацию встречающихся случаев коррозии. Но не смотря на это, все коррозионные процессы имеют не только общий результат — разрушение металла, но и единую химическую сущность — окисление.
Упрощенно окисление можно назвать процессом обмена веществ электронами. Когда одно вещество окисляется (отдает электроны), другое, наоборот, восстанавливается (получает электроны).
Например, в реакции…
… атом цинка теряет два электрона (окисляется), а молекула хлора присоединяет их (восстанавливается).
Частицы, которые отдают электроны и окисляются, называются восстановителями, а частицы, которые принимают электроны и восстанавливаются, называются окислителями. Два этих процесса (окисление и восстановление) взаимосвязаны и всегда протекают одновременно.
Такие вот реакции, которые в химии называются окислительно-восстановительными, лежат в основе любого коррозионного процесса.
Естественно, склонность к окислению у разных металлов неодинакова. Чтобы понять, у каких она больше, а у каких меньше, вспомним школьный курс химии. Было там такое понятие как электрохимический ряд напряжений (активности) металлов, в котором все металлы расположены слева направо в порядке повышения «благородности».
Так вот, металлы, расположенные в ряду левее, более склонны к отдаче электронов (а значит и к окислению), чем металлы, стоящие правее. Например, железо (Fe) больше подвержено окислению, чем более благородная медь (Cu). Отдельные металлы (например, золото), могут отдавать электроны только при определенных экстремальных условиях.
К ряду активности вернемся немного позднее, а сейчас поговорим об основных видах коррозии.
Виды коррозии
Как уже говорилось, критериев классификация коррозионных процессов существует множество. Так, различают коррозию по виду распространения (сплошная, местная), по типу коррозионной среды (газовая, атмосферная, жидкостная, почвенная), по характеру механических воздействий (коррозионное растрескивание, явление Фреттинга, кавитационная коррозия) и так далее.
Но основным способом классификации коррозии, позволяющим наиболее полно объяснить все тонкости этого коварного процесса, является классификация по механизму протекания.
По этому критерию различают два вида коррозии:
- химическую
- электрохимическую
Химическая коррозия
Химическая коррозия отличается от электрохимической тем, что протекает в средах, не проводящих электрический ток. Поэтому при такой коррозии разрушение металла не сопровождается возникновением электрического тока в системе. Это обычное окислительно-восстановительное взаимодействие металла с окружающей средой.
Наиболее типичным примером химической коррозии является газовая коррозия. Газовую коррозию еще называют высокотемпературной, поскольку обычно она протекает при повышенных температурах, когда возможность конденсации влаги на поверхности металла полностью исключена. К такому виду коррозии можно отнести, например, коррозию элементов электронагревателей или сопел ракетных двигателей.
Скорость химической коррозии зависит от температуры — при ее повышении коррозия ускоряется. Из-за этого, например, в процессе производства металлического проката, во все стороны от раскаленной массы разлетаются огненные брызги. Это с поверхности металла скалываются частички окалины.
Окалина — типичный продукт химической коррозии, — оксид, возникающий в результате взаимодействия раскаленного металла с кислородом воздуха.
Помимо кислорода и другие газы могут обладать сильными агрессивными свойствами по отношению к металлам. К таким газам относятся диоксид серы, фтор, хлор, сероводород. Так, например, алюминий и его сплавы, а также стали с высоким содержанием хрома (нержавеющие стали) устойчивы в атмосфере, которая содержит в качестве основного агрессивного агента кислород. Но картина кардинально меняется, если в атмосфере присутствует хлор.
В документации к некоторым антикоррозионным препаратам химическую коррозию иногда называют «сухой», а электрохимическую — «мокрой». Однако химическая коррозия может протекать и в жидкостях. Только в отличие от электрохимической коррозии эти жидкости — неэлектролиты (т.е. не проводящие электрический ток, например спирт, бензол, бензин, керосин).
Примером такой коррозии является коррозия железных деталей двигателя автомобиля. Присутствующая в бензине в качестве примесей сера взаимодействует с поверхностью детали, образуя сульфид железа. Сульфид железа очень хрупок и легко отслаивается, освобождая свежую поверхность для дальнейшего взаимодействия с серой. И так, слой за слоем, деталь постепенно разрушается.
Электрохимическая коррозия
Если химическая коррозия представляет собой не что иное, как простое окисление металла, то электрохимическая — это разрушение за счет гальванических процессов.
В отличие от химической, электрохимическая коррозия протекает в средах с хорошей электропроводностью и сопровождается возникновением тока. Для «запуска» электрохимической коррозии необходимы два условия: гальваническая пара и электролит.
В роли электролита выступает влага на поверхности металла (конденсат, дождевая вода и т.д.). Что такое гальваническая пара? Чтобы понять это, вернемся к ряду активности металлов.
Смотрим. Cлева расположены более активные металлы, справа — менее активные.
Если в контакт вступают два металла с различной активностью, они образуют гальваническую пару, и в присутствии электролита между ними возникает поток электронов, перетекающих от анодных участков к катодным. При этом более активный металл, являющийся анодом гальванопары, начинает корродировать, в то время как менее активный коррозии не подвергается.
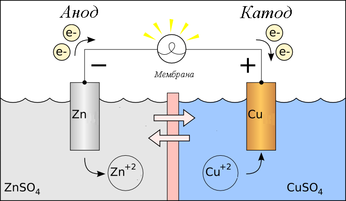
Схема гальванического элемента
Для наглядности рассмотрим несколько простых примеров.
Допустим, стальной болт закреплен медной гайкой. Что будет корродировать, железо или медь? Смотрим в ряд активности. Железо более активно (стоит левее), а значит именно оно будет разрушаться в месте соединения.
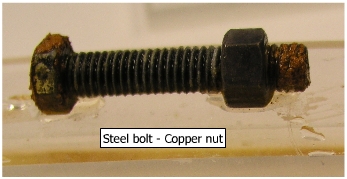
Стальной болт — медная гайка (корродирует сталь)
А если гайка алюминиевая? Снова смотрим в ряд активности. Здесь картина меняется: уже алюминий (Al), как более активный металл, будет терять электроны и разрушаться.
Таким образом, контакт более активного «левого» металла с менее активным «правым» усиливает коррозию первого.
В качестве примера электрохимической коррозии можно привести случаи разрушения и затопления кораблей, железная обшивка которых была скреплена медными заклепками. Также примечателен случай, который произошел в декабре 1967 года с норвежским рудовозом «Анатина», следовавшим из Кипра в Осаку. В Тихом океане на судно налетел тайфун и трюмы заполнились соленой водой, в результате чего возникла большая гальваническая пара: медный концентрат + стальной корпус судна. Через некоторое время стальной корпус судна начал размягчаться и оно вскоре подало сигнал бедствия. К счастью, экипаж был спасен подоспевшим немецким судном, а сама «Анатина» кое-как добралась до порта.
Олово и цинк. «Опасные» и «безопасные покрытия
Возьмем еще пример. Допустим, кузовная панель покрыта оловом. Олово — очень стойкий к коррозии металл, кроме того, оно создает пассивный защитный слой, ограждая железо от взаимодействия с внешней средой. Значит, железо под слоем олова находится в целости и сохранности? Да, но только до тех пор, пока слой олова не получит повреждение.
А коль уж такое случается, между оловом и железом тут же возникает гальваническая пара, и железо, являющееся более активным металлом, под воздействием гальванического тока начнет корродировать.
Кстати, в народе до сих пор ходят легенды о якобы «вечных» луженых кузовах «Победы». Корни этой легенды таковы: ремонтируя аварийные машины, мастера использовали паяльные лампы для нагрева. И вдруг, ни с того ни с сего, из-под пламени горелки начинает «рекой» литься олово! Отсюда и пошла молва, что кузов «Победы» был полностью облужен.
На самом деле все гораздо прозаичнее. Штамповая оснастка тех лет была несовершенной, поэтому поверхности деталей получались неровными. Вдобавок тогдашние стали не годились для глубокой вытяжки, и образование морщин при штамповке стало обычным делом. Сваренный, но еще не окрашенный кузов приходилось долго готовить. Выпуклости сглаживали наждачными кругами, а вмятины заполняли оловяным припоем, особенно много которого было вблизи рамки ветрового стекла. Только и всего.
Ну, а так ли «вечен» луженый кузов, вы уже знаете: он вечен до первого хорошего удара острым камешком. А их на наших дорогах более чем достаточно.
А вот с цинком картина совсем иная. Здесь, по сути, мы бьем электрохимическую коррозию ее же оружием. Защищающий металл (цинк) в ряду напряжений стоит левее железа. А значит при повреждении будет разрушаться уже не сталь, а цинк. И только после того, как прокорродирует весь цинк, начнет разрушаться железо. Но, к счастью, корродирует он очень и очень медленно, сохраняя сталь на долгие годы.
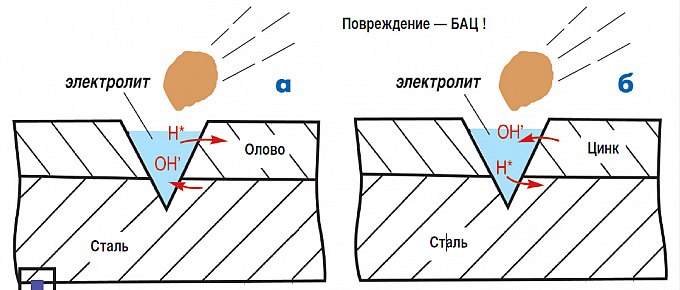
а) Коррозия луженой стали: при повреждении покрытия разрушается сталь. б) Коррозия оцинкованной стали: при повреждении покрытия разрушается цинк, защищая от коррозии сталь.
Покрытия, выполненные из более активных металлов называются «безопасными», а из менее активных — «опасными». Безопасные покрытия, в частности оцинковка, давно и успешно применяются как способ защиты от коррозии автомобильных кузовов.
Почему именно цинк? Ведь помимо цинка в ряду активности относительно железа более активными являются еще несколько элементов. Здесь подвох вот в чем: чем дальше в ряду активности находятся друг от друга два металла, тем быстрее разрушение более активного (менее благородного). А это, соответственно, сокращает долговечность антикоррозионной защиты. Так что для автомобильных кузовов, где помимо хорошей защиты металла важно достичь и продолжительного срока действия этой защиты, оцинковка подходит как нельзя лучше. Тем более, что цинк доступен и недорог.
Кстати, а что будет, если покрыть кузов, например, золотом? Во-первых, будет ох как дорого! 🙂 Но даже если золото стало бы самым дешевым металлом, такого делать нельзя, поскольку оно окажет нашей «железке» плохую услугу.
Золото ведь стоит очень далеко от железа в ряду активности (дальше всего), и при малейшей царапине железо вскоре превратится в груду ржавчины, покрытую золотой пленкой.
Автомобильный кузов подвергается воздействию как химической, так электрохимической коррозии. Но главная роль все же отводится электрохимическим процессам.
Ведь, чего греха таить, гальванических пар в автомобильном кузове воз и маленькая тележка: это и сварные швы, и контакты разнородных металлов, и посторонние включения в листовом прокате. Не хватает только электролита, чтобы «включить» эти гальванические элементы.
А электролит тоже найти легко — хотя бы влага, содержащаяся в атмосфере.
Кроме того, в реальных условиях эксплуатации оба вида коррозии усиливаются множеством других факторов. Поговорим о главных из них поподробнее.
Факторы, влияющие на коррозию автомобильного кузова
Металл: химический состав и структура
Конечно, если бы автомобильные кузова изготавливались из технически чистого железа, их коррозионная стойкость была бы безупречной. Но к сожалению, а может быть и к счастью, это невозможно. Во-первых, такое железо для автомобиля слишком дорого, во-вторых (что важнее) — недостаточно прочно.
Впрочем, не будем о высоких идеалах, а вернемся к тому, что имеем. Возьмем, к примеру, сталь марки 08КП, широко применяемую в России для штамповки кузовных элементов. При изучении под микроскопом эта сталь представляет собой следующее: мелкие зерна чистого железа перемешаны с зернами карбида железа и другими включениями.
Как вы уже догадались, подобная структура порождает множество микрогальванических элементов, и как только в системе появится электролит, коррозия потихоньку начнет свою разрушительную деятельность.
Интересно, что процесс коррозии железа ускоряется под действием серосодержащих примесей. Обычно она попадает в железо из каменного угля при доменной выплавке из руд. Кстати, в далеком прошлом для этой цели использовался не каменный, а древесный уголь, практически не содержащий серы.
В том числе и по этой причине некоторые металлические предметы древности за свою многовековую историю практически не пострадали от коррозии. Взгляните, к примеру, на эту железную колонну, которая находится во дворе минарета Кутуб-Минар в Дели.
Она стоит уже 1600 (!) лет, и хоть бы что. Наряду с низкой влажностью воздуха в Дели, одной из причин такой поразительной коррозионной стойкости индийского железа является, как раз-таки, низкое содержание в металле серы.
Так что в рассуждениях на манер «раньше металл был чище и кузов долго не ржавел», все-таки есть доля правды, и немалая.
Кстати, почему же тогда не ржавеют нержавеющие стали? А потому, что хром и никель, используемые в качестве легирующих компонентов этих сталей, стоят в электрохимическом ряду напряжений рядом с железом. Кроме того, при контакте с агрессивной средой они образуют на поверхности прочную оксидную пленку, предохраняющую сталь от дальнейшего корродирования.
Хромоникелевая сталь — наиболее типичная нержавейка, но кроме нее есть и другие марки нержавеющих сталей. Например, легкие нержавеющие сплавы могут включать алюминий или титан. Если вы были во Всероссийском выставочном центре, вы наверняка видели перед входом обелиск «Покорителям космоса». Он облицован пластинками из титанового сплава и на его блестящей поверхности нет ни единого пятнышка ржавчины.
Заводские кузовные технологии
Толщина листовой стали, из которой изготавливаются кузовные детали современного легкового автомобиля, составляет, как правило, менее 1 мм. А в некоторых местах кузова эта толщина — и того меньше.
Особенностью процесса штамповки кузовных панелей, да и вообще, любой пластической деформации металла, является возникновение в ходе деформации нежелательных остаточных напряжений. Эти напряжения незначительны, если шпамповочное оборудование не изношено, и скорости деформирования настроены правильно.
В противном случае в кузовную панель закладывается этакая «часовая бомба»: порядок расположения атомов в кристаллических зернах меняется, поэтому металл в состоянии механического напряжения корродирует интенсивнее, чем в нормальном состоянии. И, что характерно, разрушение металла происходит именно на деформированных участках (изгибах, отверстиях), играющих роль анода.
Кроме того, при сварке и сборке кузова на заводе в нем образуется множество щелей, нахлестов и полостей, в которых скапливается грязь и влага. Не говоря уже о сварных швах, образующих с основным металлом все те же гальванические пары.
Влияние окружающей среды при эксплуатации
Среда, в которой эксплуатируются металлические конструкции, в том числе и автомобили, с каждым годом становится все более агрессивной. В последние десятилетия в атмосфере повысилось содержание сернистого газа, оксидов азота и углерода. А значит, автомобили омываются уже не просто водичкой, а кислотными дождями.
Коль уж зашла речь о кислотных дождях, вернемся еще раз к электрохимическому ряду напряжений. Наблюдательный читатель подметил, что в него включен также и водород. Резонный вопрос: зачем? А вот зачем: его положение показывает, какие металлы вытесняют водород из растворов кислот, а какие — нет. Например, железо расположено левее водорода, а значит вытесняет его из растворов кислот, в то время как медь, стоящая правее, на подобный подвиг уже не способна.
Отсюда следует, что кислотные дожди для железа опасны, а для чистой меди — нет. А вот о бронзе и других сплавах на основе меди этого сказать нельзя: они содержат алюминий, олово и другие металлы, находящиеся в ряду левее водорода.
Замечено и доказано, что в условиях большого города кузова живут меньше. В этой связи показательны данные Шведского института коррозии (ШИК), установившего, что:
- в сельской местности Швеции скорость разрушения стали составляет 8 мкм в год, цинка — 0,8 мкм в год;
- для города эти цифры составляют 30 и 5 мкм в год соответственно.
Немаловажны и климатические условия, в которых эксплуатируется автомобиль. Так, в условиях морского климата коррозия активизируется примерно в два раза.
Влажность и температура
Насколько велико влияние влажности на коррозию мы можем понять на примере ранее упомянутой железной колонны в Дели (вспомним сухость воздуха, как одну из причин ее коррозионной стойкости).
Поговаривают, что один иностранец решил раскрыть тайну этого нержавеющего железа и каким-то образом отколол небольшой кусочек от колонны. Каково же было его удивление, когда еще на корабле по пути из Индии этот кусочек покрылся ржавчиной. Оказывается, на влажном морском воздухе нержавеющее индийское железо оказалось не таким уж и нержавеющим. Кроме того, аналогичную колонну из Конарака, расположенного поблизости моря, коррозия поразила очень сильно.
Скорость коррозии при относительной влажности до 65% сравнительно невелика, но когда влажность возрастает выше указанного значения — коррозия резко ускоряется, поскольку при такой влажности на металлической поверхности образуется слой влаги. И чем дольше поверхность остается влажной, тем быстрее распространяется коррозия.
Вот почему основные очаги коррозии всегда обнаруживаются в скрытых полостях кузова: cохнут-то они гораздо медленнее открытых частей. Как результат — в них образуются застойные зоны, — настоящий рай для коррозии.
Кстати, применение химических реагентов для борьбы с гололедом коррозии тоже на руку. Вперемешку с подтаявшими снегом и льдом антигололедные соли образуют очень сильный электролит, способный проникнуть куда угодно, в том числе и в скрытые полости.
Что касается температуры, то мы уже знаем, что ее повышение активизирует коррозию. По этой причине вблизи выхлопной системы следов коррозии всегда будет больше.
Доступ воздуха
Интересная все-таки вещь эта коррозия. Насколько интересна, настолько же и коварна. К примеру, не удивляйтесь, что блестящий стальной трос, с виду абсолютно не тронутый коррозией, внутри может оказаться проржавевшим. Так происходит из-за неравномерного доступа воздуха: в тех местах, где он затруднен, угроза коррозии больше. В теории коррозии это явление называется дифференциальной аэрацией.
Принцип дифференциальной аэрации: неравномерный доступ воздуха к разным участкам металлической поверхности приводит к образованию гальванического элемента. При этом участок, интенсивно снабжаемый кислородом, остается невредимым, а участок хуже снабжаемый им, корродирует.
Яркий пример: капля воды, попавшая на поверхность металла. Участок, находящийся под каплей и потому хуже снабжаемый кислородом, играет роль анода. Металл на этом участке окисляется, а роль катода выполняют края капли, более доступные влиянию кислорода. В результате на краях капли начинает осаждаться гидроксид железа — продукт взаимодействия железа, кислорода и влаги.
Кстати, гидроксид железа (Fe2O3·nH2O) и является тем, что мы называем ржавчиной. Поверхность ржавчины, в отличие от патины на медной поверхности или оксидной пленки алюминия, не защищает железо от дальнейшего корродирования. Изначально ржавчина имеет структуру геля, но затем постепенно происходит ее кристаллизация.
Кристаллизация начинается внутри слоя ржавчины, при этом внешняя оболочка геля, который в сухом состоянии очень рыхлый и хрупкий, отслаивается, и воздействию подвергается следующий слой железа. И так до тех пор, пока все железо не будет уничтожено или в системе не закончится весь кислород с водой.
Возвращаясь к принципу дифференциальной аэрации, можно представить, сколько существует возможностей для развития коррозии в скрытых, плохо проветриваемых участках кузова.
Ржавеют… все!
Как говорится, статистика знает все. Ранее мы упоминали о таком известном центре борьбы с коррозией, как Шведский институт коррозии (ШИК) — одной из наиболее авторитетных организаций в данной области.
Раз в несколько лет ученые института проводят интересное исследование: берут кузова хорошо потрудившихся автомобилей, вырезают из них наиболее полюбившиеся коррозии «фрагменты» (участки порогов, колесных арок, кромок дверей и т.д.) и оценивают степень их коррозионного поражения.
Важно отметить, что среди исследуемых кузовов есть как защищенные (оцинковкой и/или антикором), так и кузова без какой либо дополнительной антикоррозионной защиты (просто окрашенные детали).
Так вот, ШИК утверждает, что наилучшей защитой автомобильного кузова является лишь сочетание «цинк плюс антикор». А вот все остальные варианты, включая «просто оцинковку» или «просто антикор», по словам ученых — плохи.
Оцинковка — не панацея
Сторонники отказа от дополнительной антикоррозионной обработки часто ссылаются на заводскую оцинковку: с ней, мол, никакая коррозия автомобилю не грозит. Но, как показали шведские ученые, это не совсем так.
Действительно, цинк может служить в качестве самостоятельной защиты, но только на ровных и плавных поверхностях, к тому же не подверженных механическим атакам. А на кромках, краях, стыках, а также местах, регулярно подвергающихся «обстрелу» песком и камнями, оцинковка перед коррозией пасует.
К тому же, далеко не у всех автомобилей кузова оцинкованы полностью. Чаще всего цинком покрыто лишь несколько панелей.
Ну и не нужно забывать, что цинк хоть и защищает сталь, но в процессе защиты неизбежно расходуется сам. Поэтому толщина цинкового «щита» со временем будет постепенно снижаться.
Так что легенды о долгожительстве оцинкованных кузовов правдивы лишь в тех случаях, когда цинк становится частью общего барьера, дополнением к регулярной дополнительной антикоррозионной обработке кузова.
Пора заканчивать, но на этом тема коррозии далеко не исчерпана. О борьбе с ней мы продолжим говорить в следующих статьях рубрики «Антикоррозионная защита».
