Шарнир шаровой 06.000 СБ | Начертательная геометрия и Инженерная графика
Шарнир шаровой 06.000 СБ\Записка\2.1.docx
Шарнир шаровой 06.000 СБ\Записка\курсач.doc
Шарнир шаровой 06.000 СБ\Записка\принцип работы шарнир.docx
Шарнир шаровой 06.000 СБ\Записка\Содержание.doc
Шарнир шаровой 06.000 СБ\Записка\Титулная стр.doc
Шарнир шаровой 06.000 СБ\Чертежи DWG\Крышка (2).dwg
Шарнир шаровой 06.000 СБ\Чертежи DWG\крышка.dwg
Шарнир шаровой 06.000 СБ\Чертежи DWG\Палец шаровой.dwg
Шарнир шаровой 06.000 СБ\Чертежи DWG\Пружина.dwg
Шарнир шаровой 06.000 СБ\Чертежи DWG\СБ.dwg
Шарнир шаровой 06.000 СБ\Чертежи DWG\Спецификация.dwg
Шарнир шаровой 06.000 СБ\Чертежи DWG\Спецификация.spw
Шарнир шаровой 06.000 СБ\Чертежи DWG\Сухарь 3.dwg
Шарнир шаровой 06.000 СБ\Чертежи DWG\Сухарь 4.dwg
Шарнир шаровой 06.000 СБ\Чертежи DWG\Чертеж1.dwg
Шарнир шаровой 06.000 СБ\Чертежи Компас\Крышка нажимная.bak.cdw
Шарнир шаровой 06.000 СБ\Чертежи Компас\Наконечник тяговой.cdw
Шарнир шаровой 06.000 СБ\Чертежи Компас\Палец шаровой.bak.cdw
Шарнир шаровой 06.000 СБ\Чертежи Компас\Пружина.cdw
Шарнир шаровой 06.000 СБ\Чертежи Компас\СБ.cdw
Шарнир шаровой 06.000 СБ\Чертежи Компас\Спецификация.spw
Шарнир шаровой 06.000 СБ\Чертежи Компас\Сухарь 4.cdw
Шарнир шаровой 06.000 СБ\Записка
Шарнир шаровой 06.000 СБ\Чертежи DWG
Шарнир шаровой 06.000 СБ\Чертежи Компас
Шарнир шаровой 06.000 СБ
назначение, описание с фото, технические характеристики, размеры, возможные неисправности, демонтаж и правила установки
Когда речь заходит о шаровом пальце, то подразумевается шаровая опора подвески автомобиля. Однако это не единственное место, где применяется подобное техническое решение. Аналогичные устройства можно встретить в рулевом управлении, в направляющих капотов автомобилей. Все они работают по одному принципу, поэтому методы диагностики и ремонта одинаковые.
Где применяются шаровые опоры?
Основным местом применения шаровых пальцев является соединение поворотного кулака с рычагами подвески автомобиля. Это решение позволяет ступицам управляемых колес менять свое положение в горизонтальной плоскости, оставаясь неподвижными в вертикальной.
Раньше, когда на автомобилях применялась в основном зависимая подвеска, роль поворотных шарниров отводилась шкворням. Они были массивными и требовали постоянного обслуживания: чистки, смазки. Затем шкворни перекочевали на авто с независимой подвеской. Имея большой ресурс, эти узлы могли служить весь период эксплуатации машины. В связи с этим, возникает вопрос: «Какая необходимость была в замене шкворней шаровыми опорами?»
Причина заключалась в том, что кроме того, что шаровые пальцы улучшали управляемость машины, они не требовали обслуживания, в отличие от шкворней. Но расплатой за удобство стала частая замена этих элементов. Фактически они стали расходным материалом.
Кроме этого, существуют шаровые опоры в задней подвеске. Они применяются на автомобилях с независимой рычажной подвеской. Такая конструкция позволяет изменять положение одного колеса на неровной дороге, не меняя положения другого. За счет этого машина остается более устойчивой при движении.
Кроме подвески, эти узлы присутствуют в конструкции рулевой трапеции. Там они выполняют роль подвижных соединений рулевых тяг. Именно они передают усилие от рулевого механизма, изменяя угол поворотного кулака.
Устройство
На заре своего появления шаровая опора была разборной и представляла собой шарнир, помещенный в стальной бокс. Диаметр шарового пальца составлял от 7 до 25 мм. Снизу шарнир поджимался пружинами, а корпус имел возможность замены смазки во время технического обслуживания. С внедрением полимеров в автомобильной промышленности внутренние пружины были заменены упругими капроновыми вставками, внутри которых вращался шарнир. Чтобы сделать опору необслуживаемой, ее корпус сделали неразборным, а смазка стала набиваться при установке под резиновый чехол.
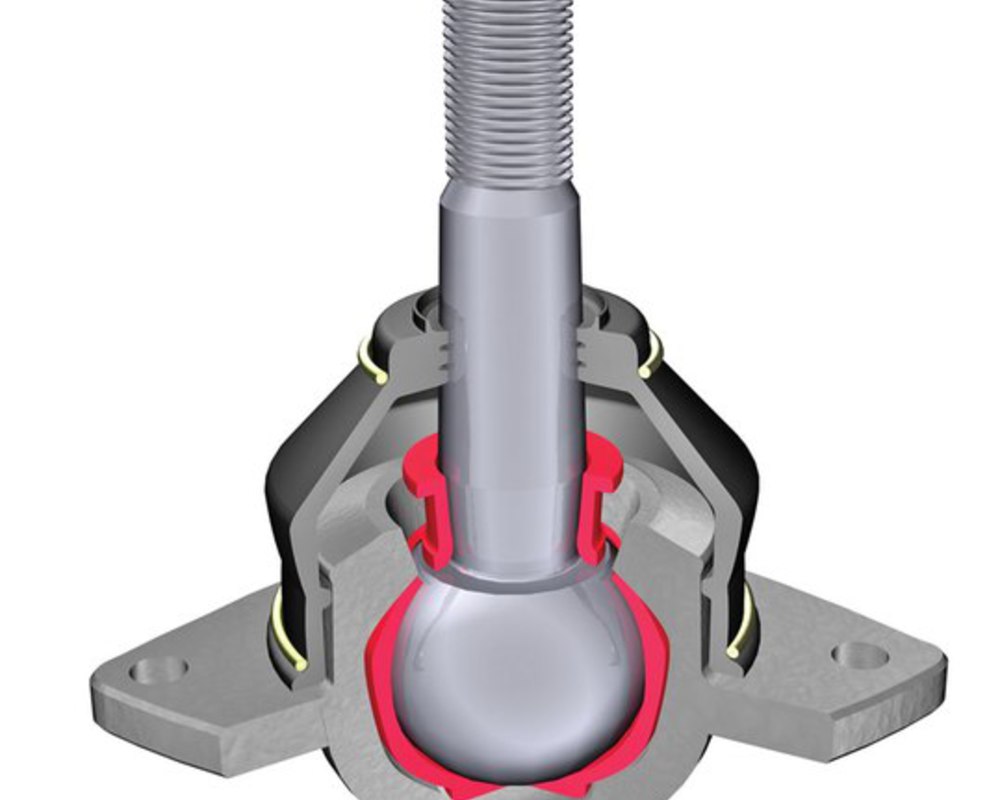
К настоящему времени почти все шаровые опоры на легковых автомобилях перешли в разряд необслуживаемых. То есть они не нуждаются в замене смазки в течение срока эксплуатации.
Шаровая опора в подвеске автомобиля
Палец шаровой опоры жестко закреплен на рычаге подвески. Есть несколько типов крепежа:
- Опора, прикрученная с помощью трех болтов или заклепок. Эта разновидность лояльна по отношению к автомобилистам. Ее можно легко заменить, не прибегая к методу прессования.
- Опора, интегрированная в рычаг. Этот вариант требует либо замены рычага в сборе, либо замены опоры с последующим прессованием.
Также бывает разновидность крепления опоры в рычаге при помощи стопорного кольца. Это вариант является компромиссным между первыми двумя.
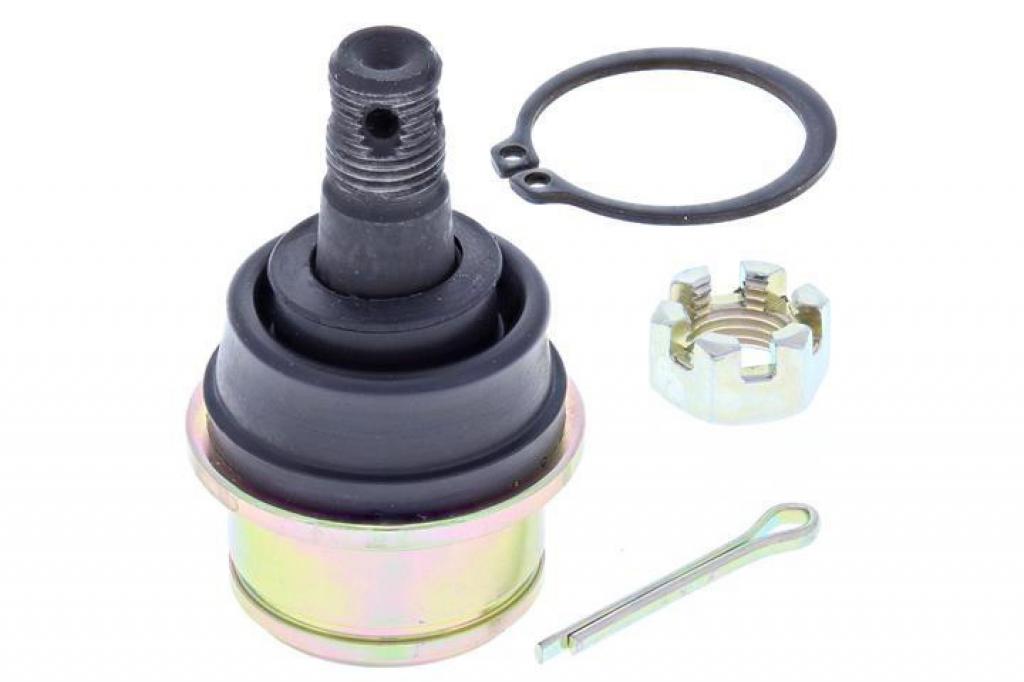
Есть мнение, что неразъемный вариант является маркетинговым ходом автомобильных компаний. Поскольку шаровой палец является расходным материалом, то меняя его, приходится менять и рычаг подвески, а заодно и сайлентблоки.
Нередко умельцы в целях экономии средств, меняя палец в неразборном соединении, приваривают корпус шаровой опоры к рычагу подвески для жесткости. Делать этого ни в коем случае нельзя по двум причинам. Во-первых, сварка не выдерживает динамические нагрузки, возникающие при движении по неровностям, во-вторых, при сваривании деталей возникает огромная температура, расплавляющая пластик внутри детали, а также изменяющая свойства смазки. Деталь после подобной фиксации работать долго не будет.
Способы крепления
Количество шаровых опор в подвеске зависит от ее конструкции. Наиболее часто встречающаяся подвеска «Макферсон» имеет одну опору со стороны каждого колеса. Тогда как двухрычажная подвеска включает в себя верхний и нижний шаровые пальцы. Это связано с тем, что в подвеске «Макферсон» функцию верхней шаровой берет на себя опорный подшипник стойки.
Крепление опоры к поворотному кулаку осуществляется при помощи гайки с пластиковыми вставками, препятствующими отворачиванию, либо гайкой со шплинтом. Есть более редкий вариант крепления, применяющийся в основном на автомобилях бизнес-класса, например, Audi A6. Здесь опора крепится при помощи зажимных болтов. Такое крепление обеспечивает более надежное соединение, но вместе с тем создает проблемы при демонтаже. Этот болт часто закисает настолько, что снять его не представляется возможным. Даже при помощи выпрессовки. Поэтому кроме опоры приходится менять поворотный кулак.
Палец в рулевом управлении
Рулевое управление к шаровому пальцу предъявляет другие требования, нежели подвеска. Если в последней этот элемент служит опорой и несет на себе вес автомобиля, то в рулевой трапеции он просто передает усилие, меняющее угол поворотных колес. Поэтому он выполнен в меньших размерах и имеет другую конструкцию.
Со стороны пальца эта деталь крепится в сошке поворотного кулака или в сошке колесных стоек (в случае подвески «Макферсон»), а корпус при помощи резьбового соединения фиксируется к рулевой тяге. Сам корпус имеет вытянутую форму с длинной резьбовой частью. Эта резьба служит не только для фиксации, но и для регулировки схождения управляемых колес. Поэтому после замены шаровых пальцев рулевых тяг необходимо делать развал-схождение.
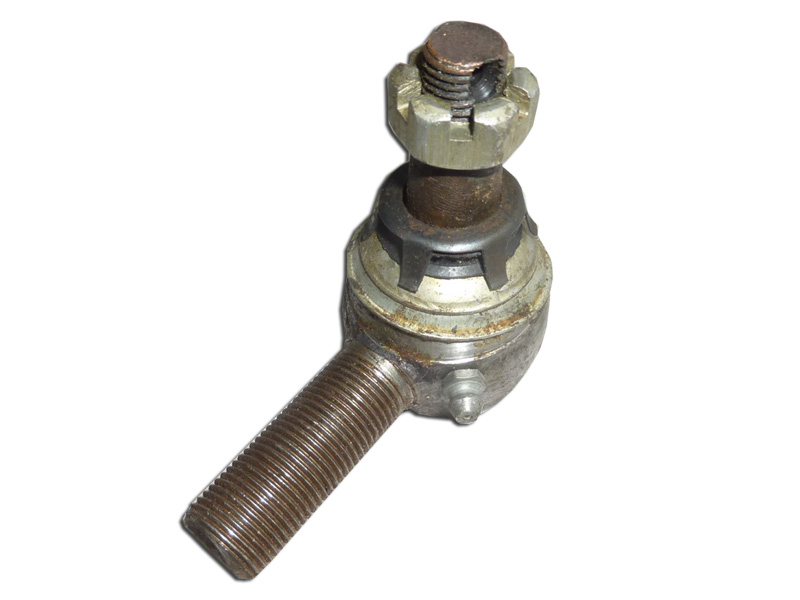
По типу конструкции рулевые наконечники могут различаться. Сам шаровой палец рулевой тяги располагается внутри либо цельного пластикового вкладыша, либо внутри разъемного металлического. Внутри наконечника между вкладышем и корпусом находится стальная пружина, обеспечивающая плотное прилегание вкладыша к пальцу по мере износа.
Защита при помощи пыльников
Во время работы шаровые пальцы постоянно подвергаются воздействию окружающей среды. Чтобы защитить деталь от грязи и пыли, а также сохранить смазку на поверхности шарнира, шаровая закрывается резиновым пыльником, который фиксируется при помощи стальных колец.
В процессе эксплуатации пыльники могут повредиться. Это приведет к неизбежному выходу из строя деталей. Поэтому во время каждого технического обслуживания необходимо осматривать резиновые пыльники. Растрескивание также недопустимо.
Причины неисправности
Причин, по которым шаровые опоры выходят из строя, несколько:
- Ударные нагрузки, связанные с неровностью дороги.
- Незамеченный вовремя порванный пыльник. Вследствие этого на трущиеся поверхности попадает грязь, являющаяся абразивом.
- Некачественные детали. Использование некачественных аналогов приводит к быстрому выходу из строя не только шаровых опор, но и подвески в целом.
Узнать о том, что пора менять шаровые опоры или рулевые наконечники, можно по биению колес. Проезжая через такое препятствие, как трамвайные пути, можно услышать характерные стуки, издаваемые шаровыми опорами, рулевыми наконечниками и сайлентблоками рычагов подвески. Чтобы уточнить, что именно вызывает стук, нужно вывесить управляемые колеса и покачать их из стороны в сторону. Если появляется люфт при покачивании в вертикальной плоскости, то изношены шаровые опоры, если люфт появляется в горизонтальной плоскости, значит, износ в рулевых наконечниках. К сожалению, этот люфт можно устранить лишь заменой деталей.
Демонтаж опоры в подвеске
В зависимости от конструктивных особенностей автомобиля демонтаж пальца шаровой опоры происходит в разной последовательности. Однако принцип используется один.
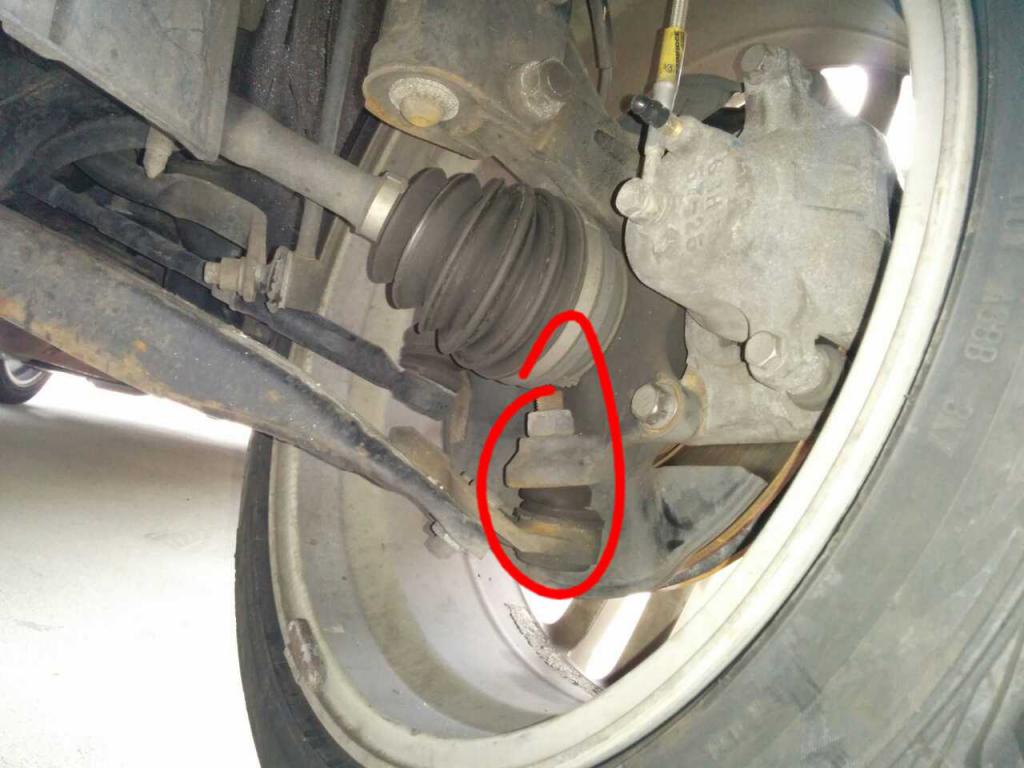
Рассмотрим замену этой детали на примере машины с подвеской «Макферсон». Замена здесь более простая, чем на двухрычажной подвеске, потому что на одно колесо приходится только одна опора. Последовательность действий:
- Вывесить машину на подъемнике. Если его нет, то поднять на домкрате автомобиль с одной стороны, после чего вывесить его на козлах, предварительно установив противооткатные упоры и стояночный тормоз.
- Выкрутить гайку, фиксирующую опору в рычаге. Если вместо гайки шаровая зафиксирована зажимным болтом, то выкрутить его. Зажимные болты часто прикипают, поэтому перед тем, как вынуть, его нужно обработать проникающей смазкой. Случается, что этот метод также не помогает, тогда остается нагрев болта при помощи газовой горелки.
- Отсоединить нижний рычаг подвески от подрамника. Этот этап выполняется в случае, если шаровая опора идет как единое целое с рычагом.
В случае фиксации опоры при помощи зажимного болта, посадочное место пальца разжимается клином. Если нет в наличии подходящего клина, его можно заменить слесарным зубилом.
При варианте, когда палец затягивается при помощи гайки, шаровая опора снимается при помощи съемника.
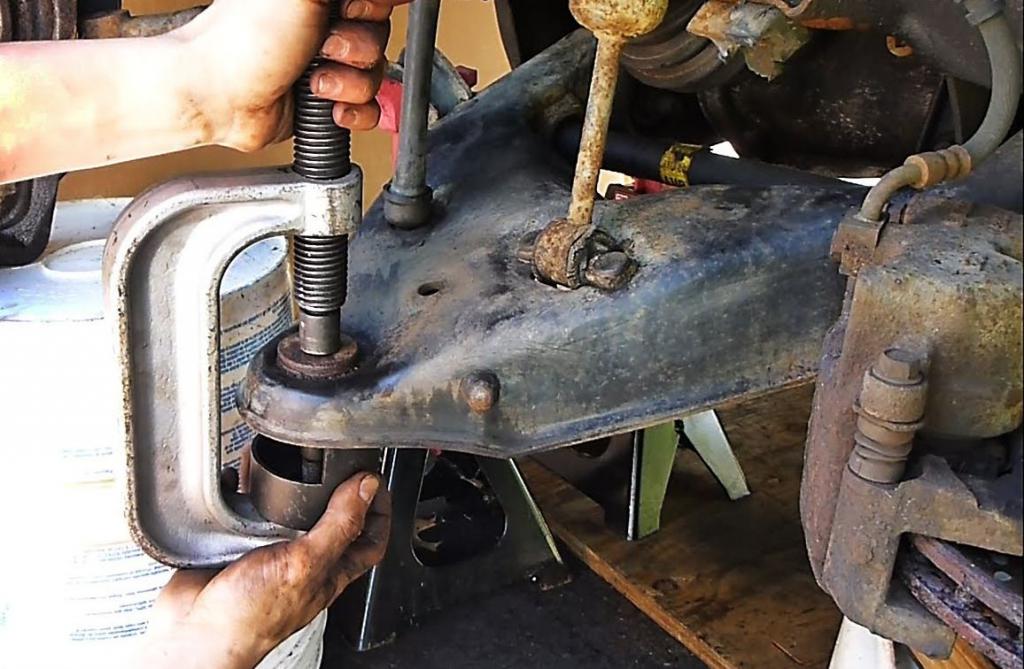
Он устанавливается одной стороной между пыльником и отверстием, в которое входит шаровой палец, а другой стороной упирается в сам палец. Затем, при заворачивании болта съемника, создается усилие, выталкивающее палец из посадочного отверстия поворотного кулака.
Что делать, если поломка произошла в дороге?
Бывают случаи, когда шаровой палец нужно поменять в дороге, а съемника нет. Как быть в этом случае? Вместо съемника нужно использовать монтировку и тяжелый молоток. После отворачивания фиксирующей гайки нужно вставить монтировку между поворотным кулаком и нижним рычагом. Усилие нужно прикладывать в направлении выталкивания шаровой опоры. Одновременно с этим нужно постукивать молотком по той части поворотного кулака, в которой фиксируется шаровая опора.
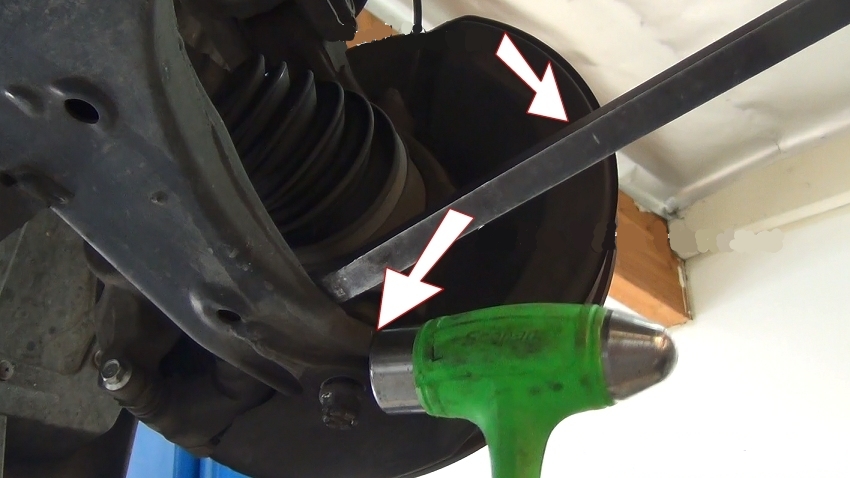
Этот метод часто использовался при замене шаровых пальцев ВАЗ-2101 — ВАЗ-2107, которые нередко ломались в дороге.
Обратная сборка
Если замена шарового пальца происходит при помощи трех болтов, которыми он фиксируется в рычаге, то обратная сборка не составляет труда. Выполняются все те же действия, только в обратной последовательности. Также деталь несложно поменять, если она зафиксирована при помощи стопорного кольца. В этом случае пружинистое кольцо разжимается, извлекается старая деталь и устанавливается новая.
В случае если шаровая опора запрессована в посадочное место, лучше заменить весь рычаг. Причина заключается в следующем. Даже если удастся запрессовать новую опору в рычаг, посадочное отверстие будет иметь больший размер, чем при первоначальной установке. Поэтому надежность фиксации будет меньшей. Насколько фиксация будет слабее, никто не знает. Поэтому лучше не рисковать и поставить новый рычаг с опорой в сборе.
СПОСОБ ИЗГОТОВЛЕНИЯ ШАРОВОГО ПАЛЬЦА
Изобретение относится к области холодной объемной штамповки стержневых изделий с головками типа шаровых пальцев.
Известен способ холодной штамповки шарового пальца [Пат. 2212973, РФ, МПК7 В21К 1/46. Способ изготовления шаровых пальцев / Д.М. Закиров, Р.Ш. Валиев, И.Б. Нуркаев], который включает отрезку заготовки, первую и вторую предварительные высадки головки, окончательное редуцирование стержня и окончательную высадку шаровой головки. Одновременно с предварительным редуцированием стержня и конуса на первом переходе высадки производят редуцирование подголовной цилиндрической части.
Однако известный способ обладает следующими недостатками: увеличение расхода материала при производстве шарового пальца и низкая стойкость инструмента.
Из известных технических решений наиболее близким по совокупности существенных признаков к заявляемому объекту является способ изготовления полого шарового пальца [Пат. SU 764820 А, РФ, МГЖ7 В21К 1/76. Способ изготовления шаровых пальцев / В.А.Головин, Г.С. Ракошиц, А.Н. Кошкин, О.Ф. Трофимов, С.А. Кириллов, Л.М. Гринштейн, В.Г. Шибаков]. В вышеуказанном способе используют цилиндрическую заготовку с диаметром, соответствующим диаметру сферической головки готового пальца, формирование цилиндрической хвостовой части и полого цилиндрического участка осуществляют комбинированным выдавливанием, предварительно формуя при этом переходную коническую часть, а затем производят ее окончательную формовку путем частичного обжима полого цилиндрического участка.
Этот способ обладает недостатками:
1. Большие удельные силы деформирования при комбинированном выдавливании, заканчивающимся обратным выдавливанием.
2. Относительно низкая стойкость инструмента, что в условиях автоматизированного производства требует дополнительных затрат на изготовление инструмента и переналадку многопозиционных автоматов.
Задачей изобретения является разработка способа изготовления шарового пальца, обеспечивающего увеличение рабочего ресурса инструмента, улучшение показателей качества готовых деталей и постановку на полностью автоматизированное производство.
Указанный технический результат достигают тем, что в известном способе изготовления шарового пальца с полой головкой холодной объемной штамповкой шаровой палец изготавливают из сплошной цилиндрической заготовки, из которой на первой операции поперечно-прямым выдавливанием на полой части получают полуфабрикат в виде стержня, плавно переходящего в полую головку, наружный диаметр которой равен наибольшему диаметру сферической головки пальца, а на последующих операциях производят формирование редуцированием коническо-цилиндрической стержневой части с размерами, соответствующими параметрам готовой детали, и деформирование обжимом полой сферической головки.
Сущность изобретения поясняется нижеследующим описанием и прилагаемыми к нему чертежами, где:
на Фиг. 1 — цилиндрическая заготовка;
на Фиг. 2 — поперечно-прямое выдавливание полой части пальца;
на Фиг. 3 — редуцирование стержневой части;
Заявляемый способ заключается в следующем. Шаровой палец изготавливают холодной объемной штамповкой из сплошной цилиндрической заготовки круглой формы (Фиг. 1). На первом переходе осуществляют операцию поперечно-прямого выдавливания на полой части пальца (Фиг. 2) для формирования обжимом полой сферической головки, наружный диаметр которой равен наибольшему диаметру сферической головки шарового пальца. На последующей операции производят редуцирование стержневой части заготовки, при которой формируют конус с размерами (Фиг. 3), соответствующими параметрам готовой детали. Далее производится операция обжима сферической головки шарового пальца (Фиг. 4).
Изготовление по предлагаемому способу полого шарового пальца позволяет:
1) воспроизвести его в неограниченном количестве;
2) увеличить рабочий ресурс полого шарового пальца за счет плавного следования волокнистой структуры конфигурации детали;
3) полностью автоматизировать производство полого шарового пальца;4) повысить стойкость инструмента за счет операции поперечно-прямого выдавливания, требующей меньших усилий.
Способ изготовления шарового пальца с полой головкой холодной объемной штамповкой, отличающийся тем, что из сплошной цилиндрической заготовки на первой операции получают полуфабрикат в виде стержня, плавно переходящего в полую часть, наружный диаметр которой равен наибольшему диаметру полой сферической головки шарового пальца, путем поперечно-прямого выдавливания на сплошной цилиндрической заготовке упомянутой полой части, а на последующих операциях производят формирование коническо-цилиндрической стержневой части шарового пальца с размерами, соответствующими размерам готового шарового пальца, редуцированием стержневой части полуфабриката и деформирование обжимом полой части полуфабриката с получением полой сферической головки шарового пальца.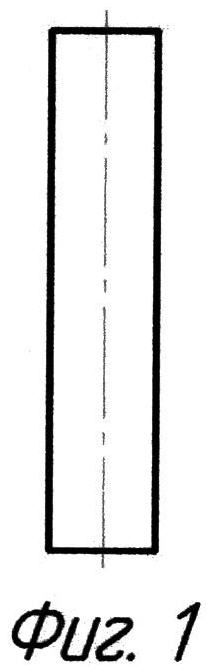

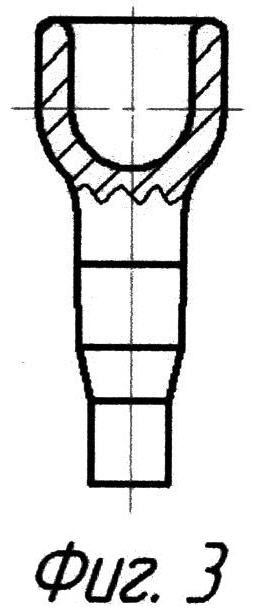
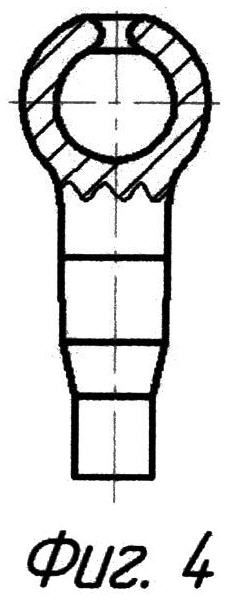
Съемник пальцев рулевых тяг, снятие пальцев шаровых шарниров
Пальцы шаровых шарниров закрепляются в рычагах поворотных кулаков, в рулевой сошке и маятниковом рычаге при помощи конических соединений, затягиваемых гайками. Эти соединения (конусность 3:25, угол 6°52′) самотормозящиеся. Степень самоторможения конического соединения зависит в первую очередь от угла конусов и усилия их затягивания.
Съемник пальцев рулевых тяг, выпрессовка пальцев шаровых шарниров рулевого управления автомобилей ВАЗ и ГАЗ.
Если когда-то на автомобилях ВАЗ (гайка М14х1,5) рекомендовали момент затяжки 5,1-6,3 кгсм, то позже он был снижен до 4,3-5,4 кгсм. У переднеприводных автомобилей ВАЗ гайка (М12х1,25) шарового пальца рулевой тяги затягивается моментом 2,76-3,41 кгсм. Затягивать гайки шаровых пальцев без динамометрического ключа нельзя.
Как выпрессовать пальцы шаровых шарниров рулевого управления.
Иногда, например, при снятии средней и боковых рулевых тяг автомобилей ВАЗ обходятся вообще без приспособлений. Отвернув гайки пальцев, наносят удар острым концом молотка по сошке (маятниковому рычагу) чуть выше шарнира средней тяги. Часто хватало двух ударов, и палец выпадал. Для рассматриваемого способа необходима эстакада или смотровая канава.
При неумелом проведении операции маятниковый рычаг может оказаться деформированным. В этом случае спица рулевого колеса может уйти от горизонтального положения при движении по прямой. Да и бить молотком по столь ответственным деталям рулевого привода вряд ли полезно для них.
Выпрессовка пальцев шаровых шарниров крайних рулевых тяг автомобилей ВАЗ из рычагов поворотных кулаков съемником А.47052 не представляет особого труда. Он надежный, доступ к шарниру свободный. Съемник А.47035, рекомендуемый для выпрессовки пальцев из сошки и маятникового рычага, более сложный и менее надежный. Подвижная система приспособления А.47035 (с рычагом, коромыслом, серьгами) вообще-то и не нужна, что подтверждается конструкцией универсального винтового съемника.
Универсальный винтовой съемник пальцев рулевых тяг.
Принцип его действия основан на том, что при выпрессовке необходимо только стронуть палец в его коническом гнезде. В связи с большей жесткостью съемника и большим диаметром винта у рассматриваемого съемника для компактности плечо рычага уменьшено до 1,6 (60:37=1,6), у съемника А.47035 оно равно 1,7 (74:43=1,7).
Захват вставляем, отжав резиновый чехол, под гнездо пальца шарнира. На палец и захват устанавливаем рычаг и вворачивая винт, выпрессовываем палец шарнира. Выпрессовка пальцев значительно облегчается, если смочить их проникающей жидкостью (керосин, WD-40). На перетянутые пальцы целесообразно наложить на несколько часов «компресс» из ветоши, смоченной этими жидкостями.
Замена шарниров рулевых тяг автомобилей ГАЗель и Соболь.
У автомобилей ГАЗель и Соболь две рулевых тяги. Продольная соединяет сошку с рычагом поворотного кулака левого колеса, а поперечная — рычаг поворотного кулака с рычагом рулевой трапеции у правого колеса. Поперечная тяга имеет левый и правый наконечники для регулировки схождения колес.
Все четыре шарнира рулевого управления одинаковые. У продольной тяги они запрессованы непосредственно в концы тяг, у поперечной — в наконечники. Резьбовые концы шаровых пальцев продольной тяги направлены в одну сторону, а у поперечной оси шарниров располагаются под углом 90 градусов.
Выпрессовка шарниров рулевых тяг автомобилей ГАЗель и Соболь.
Запрессовка шарниров рулевых тяг автомобилей ГАЗель и Соболь.
Выбивают шарниры ударом молотка по пальцу шарнира, оперев тягу или наконечники на жесткую опору. Но это не всегда удается, часто палец выбивает донышко шарнира, а корпус шарнира остается в тяге или в наконечнике. Удобнее проводить выпрессовку шарниров с применением оправки и опоры на прессе или воспользовавшись молотком. Более ответственная операция — запрессовка новых шарниров. Здесь желательно использование пресса, а применение оправки и опоры при этом необходимо.
По материалам книги «Приспособления для ремонта автомобилей».
Росс Твег.
Похожие статьи:
- Схемы системы управления инжекторного двигателя ВАЗ-21214 на Лада 4х4, схемы жгута проводов, контроллер ЭСУД, датчики, блоки реле и предохранителей ЭСУД.
- Блоки предохранителей и реле на Шевроле Нива ВАЗ-2123, номиналы предохранителей, защищаемые цепи, схема соединений монтажного блока предохранителей и реле.
- Схемы электрооборудования Chevrolet Niva ВАЗ-2123, разъемы и соединительные колодки, жгуты проводов, схема системы управления двигателем.
- Пикап Great Wall Pao, экстерьер и интерьер, особенности конструкции, комплектация, характеристики, обзор.
- Land Rover Discovery Sport 2019 года, экстерьер и интерьер, особенности конструкции, комплектация, характеристики, обзор.
- SsangYong Korando четвертого поколения, экстерьер и интерьер, особенности конструкции, комплектация, характеристики, обзор.
Сборочный чертеж(шаровая опора) | Начертательная геометрия и Инженерная графика
Днепропетровский национальный университет им. Олеся Гончара
Кафедра двигателестроение
Сборочный чертеж «Шаровая опора»
Днепропетровск 2017
ТРЕБОВАНИЯ К ВЫПОЛНЕНИЮ ЧЕРТЕЖЕЙ
1. Создать слои:
— осевая линия
тип линии – штрих-пунктир (пример ACAD_ISO04W100)
вес линии – 0,2 мм
цвет линии – на выбор (только чтобы четко просматривалась линия)
— основная линия
тип линии – сплошная (CONTINUOUS)
цвет линии – на выбор (только чтобы четко просматривалась линия)
— размер/текст
тип линии – сплошная (CONTINUOUS)
вес линии – 0,2 мм
цвет линии – на выбор (только чтобы четко просматривалась линия)
— штриховка
тип линии – сплошная (CONTINUOUS)
вес линии – 0,2 мм
цвет линии – на выбор (только чтобы четко просматривалась линия)
— вспомогательная геометрия
тип линии – сплошная (CONTINUOUS)
вес линии – по умолчанию
цвет линии – на выбор (только чтобы четко просматривалась линия)
2. Настроить размерный и текстовый слой согласно визуализации чертежа (размер шрифта желательно не меньше 5 мм)
3. Весь чертеж выполнять примитивами с атрибутами «по слою»
4. Простановка размеров:
На сборочном чертеже – габаритные размеры
На деталировочных чертежах – все необходимые размеры (использовать «базовые» размеры). Размеры должны быть понятны для изготовителя деталей по вашему чертежу.
6. Количество деталей должно быть не менее 5.
Состав: Шаровая опора:1.Гайка, 2.Контргайка, 3.Шаровая пята, 4.Втулка рамы двигателя
Софт: AutoCAD 15
Шаровые опоры: нейлон против масленок
Постепенно вытеснив шкворневую систему, шаровые опоры стали сегодня безальтернативным элементом конструкции подвески любого автомобиля. Попробуем разобраться в специфике этой простой и одновременно сложной детали.
Немного теории
Назначение шаровых опор — обеспечение подвижности управляемых колес автомобиля в горизонтальной плоскости при полном сохранении их вертикального положения. Проще говоря — это «сустав», позволяющий колесам поворачиваться при рулении. Принципиальная конструкция детали достаточно проста и состоит из двух основных элементов: металлического «пальца» с шарообразным оконечником и корпуса с соответствующей сферической полостью.
Устанавливаются шаровые опоры как промежуточные звенья между поворотным кулаком и рычагами подвески. В многорычажных подвесках ставят по две шаровых опоры на каждый поворотный кулак — на верхней и нижней точке сочленения, а на системах со стойкой «Макферсон» используют всего одну опору на нижней точке. Как правило, резьбовая часть пальца шаровой опоры фиксируется в поворотном кулаке, а корпус крепится к рычагу. (Реже применяется обратный вариант, такой как, например, у автомобилей ВАЗ семейства «Самара», где корпус шаровой закрепляется на кулаке, а резьбовая часть пальца шаровой — на нижнем рычаге.)
По способам крепления шаровых опор к рычагам существует четыре разновидности. Прежде всего, это самое распространенное до недавних пор крепление на болтовых соединениях. Среди владельцев подержанных машин это самый любимый и желанный вариант, позволяющий поменять шаровую отдельно. Труднее будет ремонт в том случае, если шаровая опора закреплена на рычаге заклепками. Еще труднее, когда шаровая запрессована в рычаг — тут многие производители вообще не допускают извлечения шарнира, предлагая только замену вместе с рычагом. И как апофеоз неремонтопригодности выступает конструкция, где корпус шаровой интегрирован в рычаг, составляя с ним фактически единое целое и извлечь его невозможно.
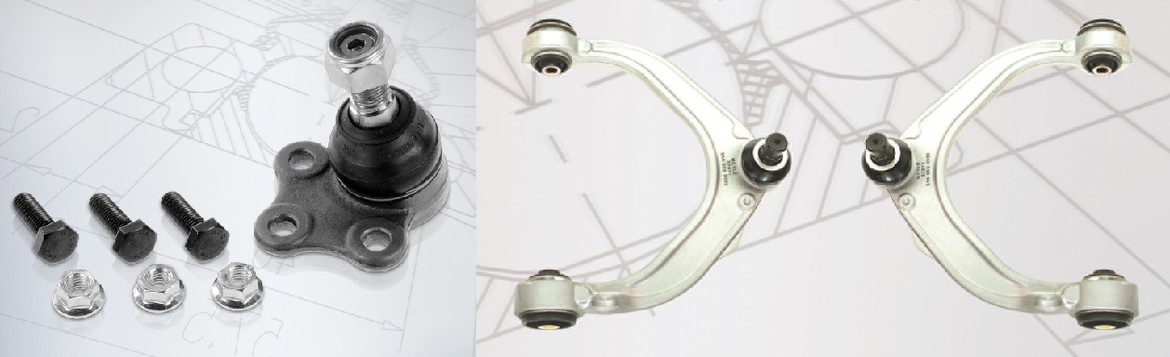
Шаровая опора с болтовым креплением (слева) и опоры интегрированные в рычаг.
Стоит заметить, что системы с несьемной шаровой опорой сейчас получают все большее распространение, особенно у японских и корейских машин. Автопроизводители считают их более технологичными, а ремонтопригодность и возможность отдельной замены уже отступает на второй план. И здесь особая ответственность ложится непосредственно на сам узел — шаровую опору.
Путем прогресса
При всей принципиальной простоте, конструкция шаровой опоры имеет свои особенности и нюансы, которые прямо влияют на ее характеристики. Не случайно, с момента своего появления в конце 40-х годов, этот узел претерпел множество изменений и доработок, став к настоящему времени высокотехнологичной деталью.
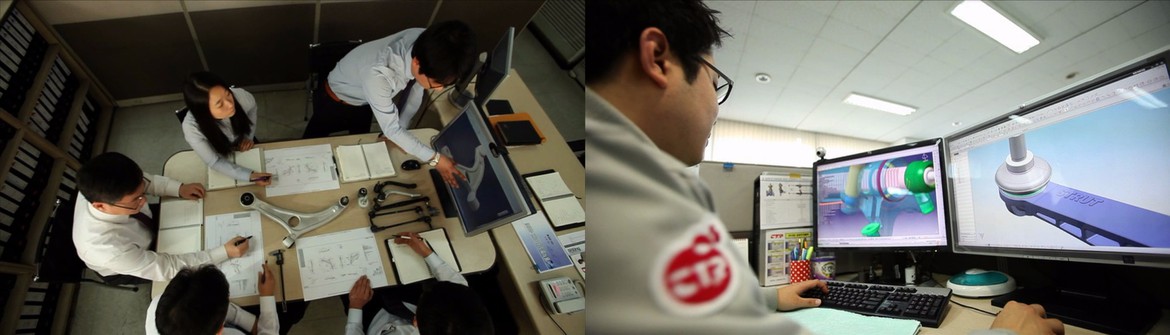
Разработка шаровых опор - сложный наукоемкий процесс.
Первые шаровые опоры представляли собой конструкцию с полусферической опорной частью. Вскоре от нее отказались, сделав оконечник пальца в виде шара (отсюда и название) — так с 50-х годов прошлого века появилась уже близкая к современной конструкция шаровой опоры. Это был (за исключением пыльника) полностью металлический узел , в котором уплотнение пальца в корпусе осуществлялось посредством пружинного подпора, а подвижность обеспечивалась за счет смазки, заправляемой через специальный клапан— т.н. «масленку». В плане требований по обслуживанию такая шаровая оказывалась близка к шкворню, также нуждаясь в периодическом смазывании и немногим выигрывая лишь в легкости поворачивания.
Технологии материалов развивались бурно, и от смазывания шаровых опор конструкторы отказались, начав с 60-х годов использовать полимерные «вкладыши» между корпусом и пальцем в сочетании с перманентной смазкой, которая единожды закладывалась при изготовлении детали на заводе на весь срок службы. А еще через двадцать лет из конструкции шаровой исчез пружинный подпор, утратив свою необходимость. Прогресс в сфере промышленного оборудования дал возможность производителям изготавливать пару корпус-палец с высокой точностью, а на смену пластикам «вкладышей» прошлых лет пришли новые материалы — родственники нейлона, способные дольше сохранять свои свойства и заданные характеристики детали.
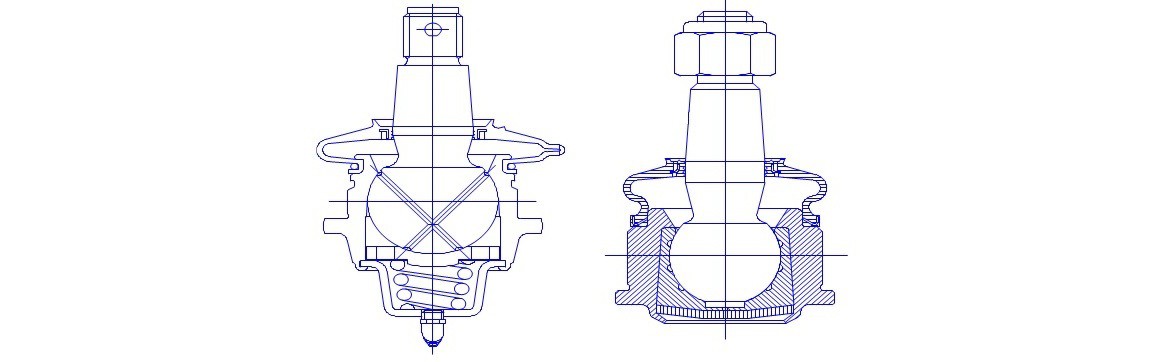
Шаровые опоры в разрезе: слева — устаревшая полностью металлическая конструкция с пружинным подпором и ниппелем для смазки, справа — современная деталь со вкладкой из инженерного пластика на основе нейлона.
Претерпели изменения и другие элементы конструкции. Так, на смену применявшимся прежде пыльникам с фиксацией проволочным кольцом пришли «интегрированные» пыльники, которые неотделимы от корпуса шарнира. Они обеспечивают гораздо лучшую защиту узла от попадания влаги и пыли, вызывающих коррозию, но в случае их повреждения замене не подлежат — только вместе с шаровой.
По старинке
Однако, несмотря на все прогрессивные технологии, старые конструкции с пружинным подпором и «масленкой» все еще в ходу — такие шаровые предлагаются на рынке запчастей для ремонта как для отечественных автомобилей, так и для иномарок. При этом одновременно с ними предлагаются и современные необслуживаемые шаровые. Но многие потребители отдают предпочтение «старым и проверенным». Почему?
Необслуживаемые опоры с пластиковыми вкладышами появились еще на советских автомобилях ВАЗ и АЗЛК, но в эпоху дефицита эту (как и остальные) запчасть было не достать. Народ ухитрялся как мог, встраивая в шаровые «масленки» и закачивая в них «солидол». Нечто подобное наблюдается и теперь — наши автомобилисты еще верят в то, что обслуживаемый узел при должном внимании будет служить дольше необслуживаемого. Причем доходит даже до «советских истоков» — в современные шаровые опоры с перманентной смазкой некоторые наши умельцы также встраивают «масленки» и закачивают туда консистентную смазку, искренне считая, что это очень полезно и продлевает срок службы детали.
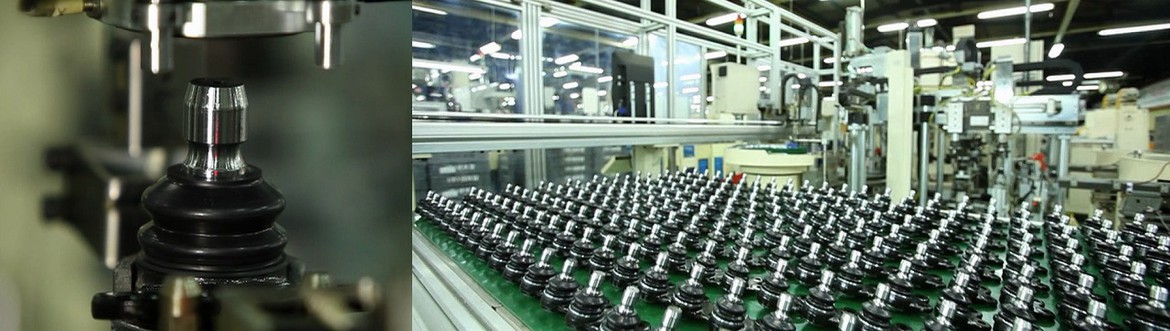
Между тем смазка, которую закладывают в шаровые на заводе, используется специальная, она совсем другая, нежели купленная в автомагазине и заправленная в гаражных условиях. Пользы от такой самодеятельности, как утверждают инженеры, не будет никакой. Об этом говорили и пытались объяснить автолюбителям еще в советские годы, но, как видно, не совсем успешно.
Немалую роль играет сложившееся у нас (и вполне оправданное) недоверие к пластикам, и убежденность в том, что металл с хорошей и регулярной смазкой будет гораздо надежнее и долговечнее. При этом никого не смущает, например, покрытие «тефлон» на кухонных сковородках, который является «родственником» воска. Также и пластмассы в привычном понимании этого слова в современных шаровых опорах нет. В деталях выпускаемых мировыми производителями используются особые полимеры, специально разработанные с учетом работы этого узла.
И снова о технике
Одними из главных физических параметров шаровой опоры являются крутящий момент и величина зазора между корпусом и пальцем. Первый определяет легкость поворачивания элементов узла относительно друг друга, и чем он меньше — тем лучше. Тем меньше сила трения элементов детали, ведущая к ее износу и выходу из строя. (Также меньшее усилие потребуется для поворота рулевого колеса, хотя при наличии гидроусилителей этот показатель нивелируется. Но ГУР не облегчает работу других элементов подвески — в первую очередь рулевых тяг и наконечников, которые получают на себя излишнюю нагрузку.)
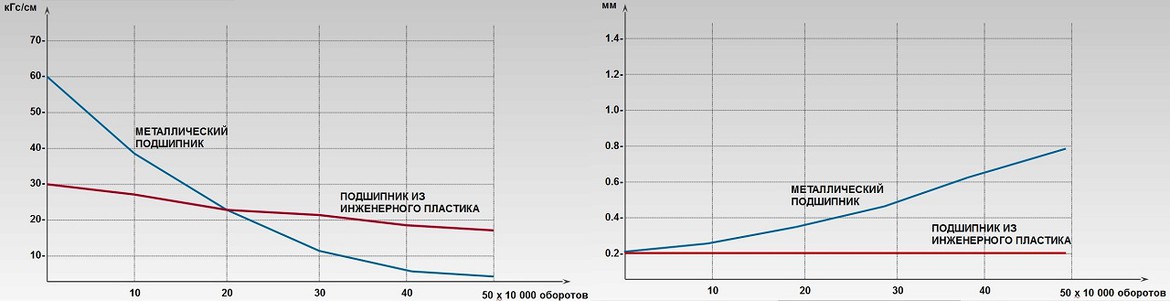
Динамика изменения крутящего момента (усилия поворачивания) и зазора (определяет ресурс) между корпусом и пальцем шаровой опоры (испытания NEO CTR). На графиках видно, как с увеличением «пробега» у цельнометаллической опоры быстро уменьшается высокий момент и растет зазор, а у детали со вставкой из инженерного пластика при изначально меньшем моменте зазор остается неизменным.
Работа сил трения ведет к увеличению зазора между пальцем и корпусом, который при достижении критической величины и делает шаровую непригодной для дальнейшего использования — деталь нужно будет менять. Именно увеличившийся зазор создает тот характерный стук в подвеске при движении по неровной дороге, сообщая о том, что нужен ремонт. Последствия езды со стучащими шаровыми могут оказаться непредсказуемы, поскольку в случае разъединения шарнира у подвески отделяется весь ступичный узел колеса с поворотным кулаком и автомобиль ложится на днище.
Как показывают испытания, проведенные компанией NEO CTR, современные шаровые опоры, изготовленные с применением инженерного пластика на основе нейлона, сохраняют установленный зазор между пальцем и корпусом в течение более чем 500 000 циклов «поворачивания». При этом в устаревших металлических шаровых с «масленкой» в тех же условиях зазор увеличивается в четыре раза, достигая критической величины.
Но это еще в идеальных условиях стендовых испытаний, где нет других нагрузок. В реальной же эксплуатации, шаровые опоры подвергаются воздействия множества других разнонаправленных сил: «ударным» нагрузкам при проезде неровностей, «разрывным» при попадании колесом на яму в повороте и их всевозможным комбинациям. Ответственные производители всегда тестируют все свои изделия на «вырывание», «изгибание» и «удар», стремясь добиться наилучших показателей.
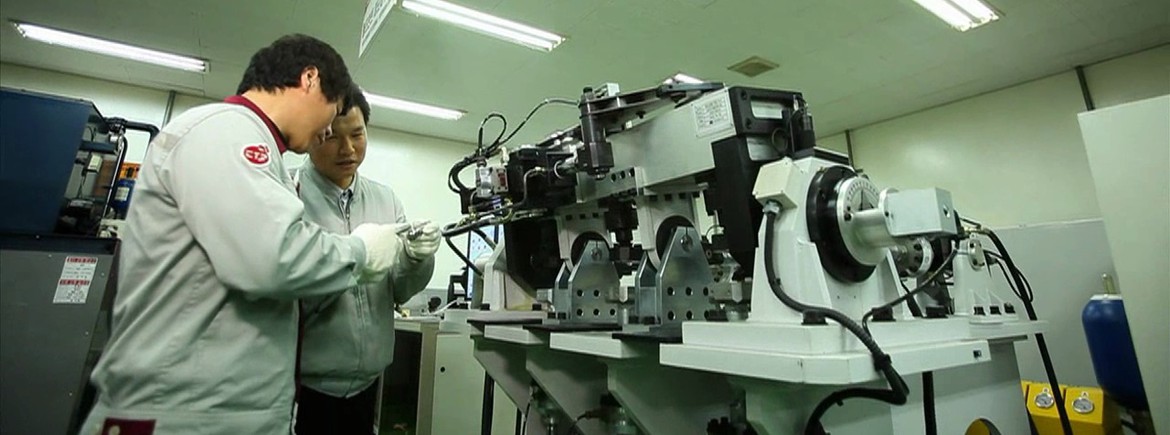
Стенд для ресурсных испытаний шаровых опор на производстве NEO CTR. Деталь проходит 500 000 циклов "поворачивания".
Свою роль в ходимости шаровых опор влияет конструкция подвески в целом, которая может быть как очень удачной в плане нагруженности этого узла, так и не вполне. Сильно сказывается манера езды самого владельца и состояние дорог, по которым он передвигается. Например, срок службы современной шаровой опоры с «нейлоновым» седлом и инженерным пластиком для одной и той же модели автомобиля может составлять как 30 000 км пробега, так и более 80 000 км.
Каков итог?
У первых автомобилей свечи зажигания были разборными: в них можно (а порой и нужно) было отделить и заменить изолятор, почистить или поменять электроды. Надо было регулярно смазывать ступичные подшипники. Но вскоре свеча стала изготавливаться как цельный элемент и о разборных конструкциях тут уже никто не помнит и не мечтает. Ступичные подшипники ходят со вложенной на заводе смазкой и не требуют ухода. Подобный путь сейчас проделывают многие элементы автомобиля, и шаровая опора здесь не стала исключением. Из разборного и нуждающегося в периодическом обслуживании узла, шаровая опора превращается в высокотехнологичный компонент — надежный, необслуживаемый и неремонтируемый.