Рабочий цикл четырехтактного дизельного двигателя
Рабочий цикл авто с дизельным двигателем отличается тем, что при такте впуска в цилиндр двигателя поступает очищенный воздух, а не горючая смесь, как в карбюраторном двигателе.
Первый такт — впуск.
Поршень перемещается от ВМТ к НМТ, через открытый впускной клапан в цилиндр поступает очищенный воздух (из-за разрежения, создаваемого поршнем). Воздух перемешивается с небольшим количеством оставшихся от предыдущего цикла отработавших газов, температура повышается и в конце такта впуска достигает 300—320 К, а давление 0.08—0.09 МПа. Коэффициент наполнения цилиндра 0,9 и выше, т. е. больше, чем у карбюраторного двигателя.
Работа четырехтактного одноцилиндрового дизельного двигателя:
а — впуск воздуха; б — сжатие; в — рабочий ход; г — выпуск отработавших газов; 1— цилиндр; 2 — топливный насос, 3 — поршень: 4 — форсунка, 5 — впускной клапан, 6 — выпускной клапан
Второй такт — сжатие.
Поршень движется от НМТ к ВМТ, впускной и выпускной клапаны закрыты. Давление и температура воздуха увеличиваются и в конце такта составляют соответственно 3—5 МПа и 800—900 К. Степень сжатия регламентируется исправностью деталей КШМ и равна 17—21.
Третий такт — рабочий ход.
В конце такта сжатия (20—30 градусов угла поворота коленчатого вала ло прихода поршня в ВМТ) с помощью насоса через форсунку в цилиндр под высоким давлением (15—20 МПа) в мелкораспыленном виде впрыскивается порция топлива. Топливо от соприкосновения с нагретым воздухом испаряется, его пары перемешиваются с нагретым воздухом и воспламеняются. При сгорании топлива, вследствие подвода большого количества теплоты, резко увеличиваются лишение и температура образовавшихся газов. В начале такта расширения давление газов составляет 7—8 МПа. а температура 2100—2300 К. Под действием давления поршень перемешается от ВМТ к НМТ, совершая полезную работу. Объем цилиндра увеличивается, давление и температура газов снижаются и при подходе поршня к НМТ составляют 0,2-0,4 МПа .
Четвертый такт — выпуск.
Поршень перемещается от НМТ к ВМТ. Через открытый выпускной клапан отработавшие газы выталкиваются через выпускной трубопровод в окружающую среду. В конце такта выпуска давление газов равно 0,11 -0,12 МПа, температура 850—1200. После этого рабочий цикл дизеля повторяется.
В двухтактных двигателях время, отводимое на рабочий цикл, используется более полно, так как процессы выпуска и впуска совмещены по времени с процессами сжатия и рабочего хода. Рабочий цикл происходит за 360 градусов (один оборот коленчатого вала).
При движении поршня от ВМТ к НМТ одновременно происходят процессы расширения и выпуска с продувкой цилиндра, а при обратном движении от НМТ к ВМ1 впуск и сжатие. Изменения параметров цикла (давление и температура) соответствуют изменениям параметров четырехтактного двигателя.
Сравнение рабочих циклов четырех- , двухтактных двигателей показывает, что при одинаковых размерах цилиндра и частоте вращения коленчатого вала мощность двухтактных двигателей выше в 1.5—1,7 раза. Он проще по конструкции и компактнее.
Работа дизельного двигателя, подробнее
Глава 1 — Двигатель | whatisvehicle
Итак, начнём. Двигатель автомобиля (Engine), что же это такое?
Автомобиль – сложный организм, сродни человеческому. У него много различных механизмов(органов), без которых он не будет работать. Но как и у человека, у автомобиля есть «сердце» и этим сердцем является автомобильный двигатель.
История автомобильного двигателя
Чуть-чуть истории. Двигатель прошёл долгую историю развития. По сути, первыми двигателями являлись парус и водяное колесо. Водяным колесом широко пользовались в странах Древнего мира(таких как Египет, Китай, Индия) для оросительных систем, а в средние века в Европе использовали как основу энергетической базы производства. Дальше появились двигатели внешнего сгорания. Широкое распространение получили паровые двигатели.
Паровой двигатель(Steam engine) — двигатель ВНЕШНЕГО сгорания, который преобразовывает энергию пара в механическую работу. Советую почитать очень интересную и непростую историю развития данного двигателя: http://www.bibliotekar.ru/encAuto/5.htm
Далее в процессе развития двигателей появились двигатели внутреннего сгорания, ДВС. Одним из них, нашедший наибольшее распространение — бензиновый двигатель.
Бензиновые двигатели (petrol engine, gasoline engine) — это класс двигателей внутреннего сгорания, в цилиндрах которых предварительно сжатая смесь топлива(бензина) и воздуха поджигается электрической искрой
Позже появились дизельные двигатели.
Дизельный двигатель — это двигатель внутреннего сгорания, работающий по принципу воспламенения распыленного дизельного топлива от соприкосновения с разогретым сжатым воздухом. Плюсом является экономичность топлива, более высокий крутящий момент. Однако, минусом является сложность систем, дороговизна изготовления и эксплуатации.
Ну и заглянем в будущее автомобилей. Итак, существуют так же электрические двигатели.
Электрический двигатель — Это установка, в которой электрическая энергия превращается в механическую работу и тепло. Это развивающееся направление в автомобилестроении. Однако, на дорогах большинство машин имеют бензиновый или дизельный двигатель, поэтому, оставим будущее и вернёмся к настоящему.
Принцип действия
Итак, автомобильный двигатель. Прежде чем рассматривать его устройство, давайте чуть-чуть разберёмся с тем, как работает автомобильный двигатель не вдаваясь в детали.
У каждого двигателя есть свой рабочий цикл.
Рабочий цикл двигателя — периодически повторяющиеся процессы в двигателе по преобразованию тепловой энергии в механическую.
У каждого двигателя есть цилиндры, в которых ходят поршни. Это главное место, где происходит самый главный процесс.
ВМТ — Верхняя Мёртвая Точка.
НМТ — Нижняя Мёртвая Точка.
Такт — это движение поршня от ВМТ к НМТ или от НМТ к ВМТ;
Двигатели могут быть двухтактные и четырёхтактные. Двухтактные двигатели на автомобиле не используются, однако предлагаю быстренько ознакомиться с принципом их работы. Для общего образования, так сказать.
Двухтактные двигатель
Перед нами двухтактный двигатель. Здесь всё предельно просто.
Первый такт — Поршень двигателя движется вверх(картинка А), открывает отверстие(1) и сжимает смесь, которая уже находится в цилиндре. После чего, свеча зажигания воспламеняет горючее(картинка В).
Второй такт — После загорания опускающийся поршень(картинка С) сначала открывает выпускное отверстие(2), а затем переходное отверстие(3). После этого через него впускается новая порция воздушно-топливной смеси.
Таким образам поршень также заменяет клапаны двигателя, и в горючее добавляется масло для смазки поршня. Многие двухтактные двигатели снабжены ребрами для воздушного охлаждения цилиндра.
Четырёхтактный двигатель
А теперь вернёмся к четырёхтактном автомобильному двигателю.
Автомобильные двигатели, как мы уже сказали, могут быть бензиновыми и дизельными. И поэтому предлагаю рассмотреть их такты вместе. Несмотря на то, что они схожи, но в них есть так же и различия.
1-й такт впуск (наполнение).
Поршень движется от ВМТ к НМТ, впускной клапан открыт. Под действием перепада давления, возникающего в результате движения поршня:
Бензиновый двигатель: бензовоздушная смесь через впускной канал наполняет цилиндр.
Дизельный двигатель: воздух через впускной канал наполняет цилиндр.
2-й такт сжатие.
Поршень движется от НМТ к ВМТ, все клапана закрыты. Давление и температура в цилиндре поднимаются.
бензиновый двигатель: в конце такта сжатия на свечу зажигания подается высокое напряжение, между электродами свечи проскакивает искра и поджигает бензовоздущную смесь
дизельный двигатель: через форсунку высокого давления подается дизельное топливо, которое воспламеняется от нагретого в процессе сжатия воздуха.
3-й такт рабочий ход. Поршень движется от ВМТ к НМТ, все клапана закрыты. В начале такта продолжается сгорание топлива, начавшееся в конце такта сжатия. Температура и давление газов повышается. Давление передается поршню и перемещает его к НМТ. Тепловая энергия сгоревшего топлива превращается в механическую работу движения поршня.
4-й такт выпуск. Поршень движется от НМТ к ВМТ, выпускной клапан открыт. Происходит выталкивание
отработавших газов из цилиндра.
Для большей наглядности взгляните на следующие рисунки:
Такты бензинового двигателя:
Такты дизельного двигателя:
Таким образом 1 рабочий цикл 4-х тактного двигателя происходит за 2 оборота коленчатого вала (720° его поворота). Отличие между бензиновым и дизельным двигателем лишь в топливе и способе его воспламенении на такте сжатия. Однако, это вносит свои изменения в применяемые агрегаты, но об этом речь пойдёт потом.
Двигатели почти всех современных автомобилей являются четырёхтактными по своему циклу работы, и энергия, полученная от сжигания топлива, почти полностью преобразовывается в полезную. Цикл Отто, так называется подобный принцип, по имени Николауса Отто, изобретателя двигателя внутреннего сгорания (1867 год).
Основные параметры
Полный объем цилиндра ( Va ) — объем, заключенный между головкой, цилиндром и поршнем при нахождении его в НМТ;
Объем камеры сжатия ( VC ) — объем, заключенный между головкой, цилиндром и поршнем при нахождении его в ВМТ;
Рабочий объем цилиндра ( Vh ) — объем, образующийся при движении поршня от ВМТ к НМТ ( Vh = Va-Vc );
Полный объем двигателя ( iVh ) сумма рабочих объемов всех цилиндров двигателя; Он же литраж двигателя.
Степень сжатия ( E ) отношение полного объема к объему камеры сжатия ( E = Va/Vc = 1 + Vh/Vc );
Степень сжатия показывает, во сколько раз сжимают горючую смесь в цилиндре. Чем больше степень сжатия, тем больше будет давление на поршень при сгорании смеси, а следовательно и больше мощность двигателя. Увеличивать степень сжатия очень выгодно — от той же порции топлива можно получить больше полезной работы.
Мощность двигателя
Мощность — это физическая величина, равная отношению работы, совершенной за определенное время, к этому времени. В системе единиц СИ мощность измеряется в Ваттах (Вт). Поднимая груз массой 1 килограмм на высоту 1 метр за 1 секунду, мы развиваем мощность 1 кг x 9,8 м/с2 x 1 м/с = 9,8 Вт.
Мощность автомобильных двигателей обычно измеряют в лошадиных силах.
Термин «лошадиная сила» был введен в конце XVIII в. английским изобретателем Дж. Уаттом. Наблюдая за работой лошадей, вытягивающих из угольных шахт при помощи блоков корзины с углем, ученый измерил общий вес извлеченной ими породы и высоту, на которую он был поднят за определенное время. Уатт рассчитал, что 1 лошадь за 1 минуту с глубины 30 м вытягивает в среднем 150 кг угля. Эта единица мощности и получила название лошадиной силы (horsepower).
После принятия в 1960 г. системы единиц СИ лошадиная сила стала вспомогательной единицей мощности, равной 736 Вт. Средняя мощность человека равна 70—90 Вт, что составляет 0,1 лошадиной силы
1 л.с. = 0,73549875 кВт
Порядок работы цилиндров двигателя
Для наибольшей равномерности нагрузки коленчатого вала многоцилиндрового двигателя необходимо, чтобы рабочие такты в цилиндрах повторялись в определенной последовательности, которая называется порядком работы цилиндров. Порядок работы цилиндров зависит от числа цилиндров двигателя и его тактности; при этом последовательно работающие цилиндры не должны стоять рядом.
Полный цикл у четырехтактного двигателя осуществляется за два оборота вала, т. е. за 720°, у двухтактного за 360°. Для того чтобы в любой момент вал двигателя имел некоторое постоянное усилие от воздействия газов на поршень, колена вала необходимо смещать относительно друг друга на угол ф. Этот угол зависит от числа цилиндров г и тактности двигателя и равен цикловой продолжительности поворота вала в градусах, отнесенной к числу цилиндров. Следовательно, для четырехтактного двигателя ф = 720°/г, для двухтактного ф = 360°/z.
Определим, например, порядок работы цилиндров, расположенных в один ряд, у четырехтактного четырехцилиндрового двигателя. В этом случае ф = 720° : 4 = = 180°. Вал имеет конфигурацию, при которой поршни 1 и 4 перемещаются в направлении, противоположном движению поршней 2 и 3. Получающееся при этом чередование процессов в цилиндрах показано в табл. 8. Если в первом цилиндре осуществляется рабочий ход, то поршень второго цилиндра движется вверх, при этом из двух возможных процессов (сжатие и выпуск) примем выпуск. Тогда поршень третьего цилиндра, также перемещающийся вверх, должен осуществлять сжатие. В четвертом цилиндре поршень движется вниз одновременно с поршнем первого цилиндра, осуществляющим рабочий ход, поэтому в четвертом цилиндре должен быть впуск. Чередование процессов в последующих тактах всех цилиндров определяется цикловой последовательностью. Из табл. 8 видно, что процессы расширения (рабочего хода) будут проходить в цилиндрах в следующем порядке: 1—3—4—2. Если во втором цилиндре в первом такте принять вместо процесса выпуска сжатие, то порядок работы цилиндров изменится и будет 1—2—4—3. Следовательно, для четырехтактного четырехцилиндрового однорядного двигателя возможны два порядка работы цилиндров.
Для более полного усвоения предлагаю визуально взглянуть на следующие рисунки:
а — чередование тактов 1-2-4-3; б — чередование тактов 1-3-4-2
И напоследок, видео ролик о работе(бензиновый и дизельный):
Итак, начальные сведения мы получили. Теперь мы можем приступать к изучению устройства двигателя внутреннего сгорания.
Понравилось это:
Нравится Загрузка…
Рабочий цикл 2-х тактного дизеля
Рис.2 Диаграмма рабочего цикла двухтактного дизеля:
А – продувочное окно; Б – выпускное окно; 1 – цилиндр; 2 – поршень; 3 – форсунка
Работа двухтактных дизелей невозможна без продувки, которая обеспечивается нагнетателем. Поэтому весь цикл проходит при давлении выше атмосферного.
1-й такт – продувка и сжатие. Поршень движется от НМТ к ВМТ. В цилиндр поступает воздух от нагнетателя. Через открытые продувочные (впускные) и выпускные окна происходит продувка цилиндра (очистка от отработавших газов) с одновременным наполнением свежим воздухом. После закрытия выпускных окон воздух сжимается и нагревается (Р=36 кг/ ; t=700°С). В конце такта (за 10 — 25° до ВМТ по углу поворота коленчатого вала) происходит впрыск и воспламенение топлива. При этом давление и температура газов в цилиндре резко возрастают (Р=90 — 100 кг/
; t=1800°С).
2-й такт – рабочий ход и выпуск. Поршень движется от ВМТ к НМТ и совершает работу. В начале такта идет догорание топлива и давление остается постоянным. Далее объем цилиндра увеличивается, давление и температура газов понижаются. В конце открываются выпускные окна и происходит свободный выпуск отработавших газов. После открытия продувочных (впускных) окон начинается продувка.
Дизель 10Д100
Рис.3 Общий вид дизеля 10Д100:
1 – турбокомпрессоры; 2, 4, 8, 9 – люки; 3 – воздухопровод; 5 – воздухоохладитель; 6 – отсек топливной аппаратуры; 7 – тяговый генератор; 10 – поддизельная рама; 11, 12 – водяные насосы; 13 – главный масляный насос; 14 – объединенный регулятор дизеля; 15 – выпускные патрубки
Основные характеристики
Круговая диаграмма
Круговая диаграмма показывает распределение фаз рабочего цикла дизеля в зависимости от угла поворота кривошипа нижнего коленчатого вала (НКВ). Отсчет градусов ведется от ВМТ.
Рис.4 Диаграмма фаз газораспределения дизеля 10Д100
Фаза | Продолжи-тельность | Угол поворота НКВ |
ВМТ | ||
Рабочий ход | 124º | |
Начало открытия выпускных окон нижним поршнем | 124º | |
Свободный выпуск газов | 16º | |
Начало открытия продувочных окон верхним поршнем | 140º | |
Продувка и заполнение цилиндра чистым воздухом | 96º | |
Закрытие выпускных окон | 236º | |
Наддув | 8º | |
Закрытие продувочных окон | 244º | |
Сжатие воздуха | 106º | |
Начало подачи топлива | 350º | |
Подача и воспламенение топлива | 10º | |
ВМТ | 360º |
Поддизельная рама
Рис.5 Поддизельная рама:
1 – забор масла; 2 – слив масла из фильтра тонкой очистки; 3 – забор масла насосом; 4 – слив масла из вспомогательных агрегатов; 5 – верхний лист для установки блока дизеля; 6 – сетки; 7 – трубка масломерной рейки; 8 – горловина для заливки масла; 9 – опоры для пружин; 10, 12 – отверстие и труба подачи воды к воздухоохладителям; 11 – платики установки рамы; 13 – поддон (маслосборник) рамы; 14 – забор масла маслопрокачивающим насосом
Служит для установки блока дизеля и тягового генератора.
К двум продольным вертикальным листам рамы сверху и снизу приварены горизонтальные листы. Нижние листы являются опорными для установки картера на настильный лист рамы тепловоза, а верхние – для установки блока дизеля. Со стороны генератора горизонтальные листы усилены накладками, а также к ним приварены опоры для пружин, которые служат амортизаторами для тягового генератора. Продольные вертикальные листы связаны между собой двумя сварными поперечными балками коробчатого сечения.
Снизу к раме приварен поддон, который служит маслосборником. В поддон вварен коллектор для подвода масла к масляному насосу. Для увеличение жесткости внутри поддона приварены поперечные перегородки, а спереди и сзади торцевые стенки. Масло в поддон заливают через горловину с фильтрующей сеткой и крышкой. Для слива масла в дне поддона имеется труба. Уровень масла измеряют рейкой, проходящей через трубку. Сверху поддона на уголках крепятся съемные сетки. Они предохраняют масло от засорения и служат пеногасителями.
Задняя часть рамы имеет форму вилки. На ней четырьмя болтами с каждой стороны укрепляют тяговый генератор.
Поддизельную раму со стороны управления через опорные лапы прикрепляют к раме тепловоза четырьмя болтами с мощными цилиндрическими пружинами. Со стороны генератора поддизельная рама прикреплена четырьмя болтами к настильному листу рамы тепловоза.
Блок цилиндров
Является основной частью дизеля – его остовом. В нем расположены все основные детали и узлы.
Блок представляет собой коробчатую конструкцию, сваренную из стальных вертикальных и горизонтальных листов. Вертикальные листы
(16 мм) разделяют его на 12 отсеков: отсек управления, 10 отсеков цилиндров и отсек вертикальной передачи. Горизонтальными листами ( 25 и 22 мм) блок делится на 5 отсеков: отсек верхнего коленчатого вала, отсек воздушного ресивера; отсек топливных насосов, отсек выпускных коллекторов и отсек нижнего коленчатого вала.
В отсеке управления расположены все механизмы управления топливными насосами и приводные шестерни кулачковых валов. Отсек закрыт крышкой.
На торце блока со стороны отсека управления в верхней части укреплен кронштейн для установки двух турбокомпрессоров. Внизу – выпускные патрубки и опорная плита для установки водяных и масляного насосов и их приводы.
На торце блока со стороны тягового генератора в верхней части установлен воздушный нагнетатель с редуктором и воздухоохладители. В нижней – корпус уплотнения коленчатого вала и валоповоротный механизм.
Отсек верхнего коленчатого вала сверху закрыт крышкой, которая крепится к блоку шпильками. В крышке имеется 10 люков для осмотра верхнего коленчатого вала, его подшипников и кулачковых валов.
Рис.6 Блок дизеля:
1 – ниши для выпускных коллекторов; 2 – отсек управления; 3 – отсек верхнего коленчатого вала; 4 – место установки воздухоохладителя; 5 – люк в отсеке вертикальной передачи; 6 – люки в отсеке топливной аппаратуры; 7 – люки в отсеке воздушного ресивера; 8 – люки в отсеке нижнего коленчатого вала; 9 – опоры нижних коренных подшипников
В отсеке воздушного ресивера с левой и правой стороны имеется по 5 люков, закрытых крышками. Через эти люки осматривают верхние поршни, кольца, втулки цилиндров, очищают продувочные окна. На двух крышках с обеих сторон установлены предохранительные клапаны на 2,5 кг/см2.
В отсеке топливных насосов имеются люки для монтажа и осмотра топливной аппаратуры.
Ниже справа и слева вдоль блока имеются ниши, в которые устанавливаются выпускные коллекторы. Через эти ниши перед монтажом выпускных коллекторов устанавливают выпускные коробки. Ниши для выпускных коллекторов закрыты плитами жесткости. В плитах вырезаны люки для постановки и снятия крышек люков выпускных коллекторов и термопар.
В отсеке нижнего коленчатого вала с обеих сторон расположены по 10 люков для осмотра нижнего коленчатого вала и его подшипников, а также для выемки нижних поршней. На всех крышках этих люков с левой стороны установлены предохранительные клапаны на 0,5 кг/см2.
Цилиндровая втулка (гильза)
Рис.7 Втулка цилиндра (гильза):
1 – выпускная коробка; 2 – адаптер; 3,4,; 5,6,8,9,10,11 – уплотнительные кольца; 7 – рубашка охлаждения; А – продувочные окна; Б – отверстие для отвода охлаждающей воды; В – отверстия для адаптеров; Г – отверстия для входа охлаждающей воды; Д – выпускные окна
Служит для направления движения поршней и образует камеру сгорания для сжигания топлива. Отлита из специального чугуна. Внутренняя поверхность подвергается хонингованию, а затем для лучшей прирабатываемости и защиты от коррозии фосфатированию.
Втулка в верхней части имеет прямоугольный фланец, которым четырьмя шпильками (по две с каждой стороны) ее прикрепляют к блоку. Между отверстиями для шпилек во фланце сделано по одному отверстию с резьбой под рымы для выпрессовки и выемки втулки.
Ниже равномерно по окружности расположены 16 продувочных (впускных) окон. Вход воздуха происходит под углом для получения завихрения.
Это улучшает очистку цилиндра от отработавших газов и смешивание топлива с воздухом.
В средней части втулки на ее наружной стороне отлиты продольные ребра, служащие для посадки рубашки охлаждения. В нижней части рубашка фиксируется стопорным кольцом. Для уплотнения между цилиндровой втулкой и рубашкой снизу и сверху ставят по два резиновых уплотнительных кольца в канавки, проточенные на посадочных поясках втулки. Для надежного уплотнения в этих местах на пояски наносят клей ГЭН-150. Во втулке и рубашке имеется два отверстия для адаптеров форсунок и одно отверстие для адаптера индикаторного крана. На наружной поверхности втулки и рубашки в верхней части проточены канавки для резиновых уплотнительных колец, предохраняющих от просачивания масла, попадающего от верхнего порщня.
В нижней части втулки имеется 10 выпускных окон по 5 с каждой стороны. Эта часть втулки входит в выпускную коробку, в которой она свободно перемещается при изменении температуры. Чтобы не допустить пропуска газов, на нижней части цилиндровой втулки проточены канавки для резиновых уплотнительных колец.
Сверху втулка охлаждается воздухом, поступающим из ресиверов. Средняя часть втулки нагревается наиболее интенсивно и поэтому охлаждается водой, которая подводится через два отверстия в нижней части рубашки, расположенные друг напротив друга, а отводится через одно отверстие в верхней части с левой стороны. Нижняя часть втулки охлаждается через стенку выпускной коробки циркулирующей там водой.
При работе дизеля внутренняя часть втулки смазывается масляным туманом, образующимся при разбрызгивании масла вращающимися частями дизеля.
Адаптеры
Рис.7 Адаптер:
1 –втулка нажимная; 2 – гайки; 3 – шпилька; 4 – фланец; 5 – корпус; 6 – кольцо резиновое; 7 – кольцо медное
Служат для установки форсунок и индикаторного крана.
Адаптер состоит из корпуса и фланца, соединенных шпильками. Полый корпус вворачивается в стенку цилиндровой втулки. Во втулке корпус уплотняется медным кольцом, а в рубашке – резиновым. Резиновое кольцо поджимается к бурту корпуса нажимной втулкой, гайкой и контргайкой.
Форсунки и индикаторные краны устанавливаются в центральную расточку корпуса адаптера и крепятся с помощью двух фланцев.
Выпускная система
Рис.8 Выпускная система:
1 – дренажное отверстие; 2 – ловушка; 3,5 – пробки; 4 – крышка смотрового люка; 6 – кран; 7 – компенсатор; 8 – кожух; 9 – выпускные патрубки; 10 – выпускные коллекторы
Служит для удаления отработавших газов. Включает выпускные коробки, выпускные коллекторы, выпускные патрубки и компенсаторы.
Выпускная коробка представляет собой отливку из чугуна прямоугольной формы, имеющую в середине цилиндрическое отверстие для цилиндровой втулки, а с боков наклонные каналы для выпуска газов.
Нижняя часть коробки имеет кольцевой установочный бурт с шестью отверстиями с резьбой для крепления к нижнему горизонтальному листу отсека выпускных коллекторов ( из отсека НКВ). Перед окончательным закреплением болтов выпускные коробки устанавливают по линейке так, чтобы их наружные боковые поверхности с левой и правой сторон находились в одной плоскости, так как плоскости коробок соединены с обеих сторон с плоскостями двух выпускных коллекторов.
Внутри стенок выпускной коробки внизу и вверху имеются полости, сообщающиеся между собой. В эти полости через нижние окна в боковых плоскостях коробок поступает вода из нижней части выпускных коллекторов. Она охлаждает стенки выпускной коробки и стенки нижней части цилиндровой втулки и выходит через верхние окна в верхнюю часть выпускных коллекторов.
Выпускные коллекторы образованы внутренними и наружными кожухами, между которыми проходит охлаждающая вода. Кожухи представляют собой прямоугольные коробки (листовая сталь 3 мм), приваренные к стальной плите (25 мм). В плите против каждого канала выпускной коробки прорезано прямоугольное отверстие, через которое газы проходят внутрь коллектора. Внутренний канал коллектора со стороны генератора закрыт торцовым листом, а со стороны отсека управления имеет прямоугольный фланец.
В плите над каждым отверстием для газов и под ним прорезаны прямоугольные отверстия, совпадающие с окнами для прохода воды в боковых стенках выпускных коробок. Наружный кожух соединен с внутренним фланцами крышек и распорками, предупреждающими деформацию.
Каждый коллектор соединен с боковыми плоскостями выпускных коробок шпильками через поронитовые прокладки, покрытые ГЭН-150. На шпильки навернуты закрытые гайки. Кроме отверстий для шпилек в плите имеется 12 отверстий с резьбой для пробок. При разборке эти пробки выворачивают и вворачивают болты, которыми отрывают пригоревший коллектор от выпускных коробок.
В наружном и внутреннем кожухах против окон плиты вырезаны люки, в которые вварены фланцы с отверстиями для болтов крышек. Крышки двойные с заложенным внутрь асбестом. В крышки люков с левой стороны по ходу тепловоза вварены гнезда термопар.
Сверху коллектора против каждого цилиндра вварены фланцы для подвода воды к рубашкам охлаждения цилиндровых втулок. В нижней части коллектора между люками девятого и десятого цилиндров приварены две бонки с отверстиями. Верхнее проходит в газовую полость. Нижнее – в водяную полость и служит для установки штуцера с вентилем (используется при спуске воды из коллектора).
Торцовые фланцы выпускных коллекторов соединены через поронитовые прокладки с фланцами выпускных патрубков. Во фланцах установлены термоболты для контроля за температурным режимом.
Выпускные патрубки имеют двойные стенки. Между стенками поступает охлажденная вода от водяного насоса. Внутренний канал патрубка служит для прохода отработавших газов. Снизу на выпускных патрубках имеется по два штуцера с пробками. Через один сливается вода, через другой – несгоревшее топливо. В верхней части приварены штуцера, к которым присоединены трубки для отвода воды или пара в коллектор горячей воды.
Компенсаторы представляют собой стальные сильфоны и служат для компенсации линейных размеров при изменении температуры. В них установлены решетки для предотвращения попадания в турбокомпрессоры осколков поршневых колец.
Коленчатые валы
Рис.9 Коленчатые валы:
а – верхний; б – нижний; 1 – шпилька; 2 – гайка; 3 – шестерня;
4,5,6 – фланцы; 7 – направляющее кольцо; С — каналы
Преобразуют возвратно-поступательное движение поршней во вращательное и являются наиболее нагруженной частью дизеля. На них действуют силы давления газов при сгорании топлива в цилиндре, силы инерции возвратно-поступательно движущихся масс и вращающих моментов.
На дизеле установлены два коленчатых вала, отлитых из высокопрочного чугуна, отличающихся друг от друга длиной и конструкцией концевых частей. На переднем конце НКВ крепится антивибратор с удлиненной ступицей, шестерня эластичного провода насосов (водяных и масляного) и вилка карданного соединения. На заднем конце расположены фланцы для крепления конической шестерни вертикальной передачи и ведущего диска дизель-генераторной муфты. На переднем конце ВКВ крепится шестерня привода кулачковых валов топливных насосов. На заднем конце расположены фланцы для крепления конической шестерни вертикальной передачи и муфты привода торсионного вала редуктора нагнетателя второй ступени. Нижний вал опережает верхний по углу поворота на 12º.
Каждый вал имеет 12 коренных и 10 шатунных шеек. Шатунные шейки смещены относительно друг друга на 36º в соответствии с порядком работы цилиндров и совместно со щеками образуют кривошипы. Для облегчения валов коренные и шатунные шейки выполнены полыми.
Смазка из системы поступает к коренным подшипникам через штуцеры в крышках ВКВ и в опорах НКВ, а затем по сверлениям в щеках кривошипов к шатунным подшипникам.
Коренные подшипники
Рис. Вкладыши коренных подшипников:
а —
Коленчатые валы имеют 12 коренных подшипников: 11 подшипников являются опорными (воспринимают радиальные нагрузки) и один опорно-упорный (воспринимает как радиальные, так и осевые нагрузки). Опорно-упорный подшипник стоит на 11-й шейке у фланца крепления конической шестерни вертикальной передачи.
Каждый подшипник состоит из двух половинок – вкладышей. Вкладыши изготавливают из бронзы и внутреннюю поверхность заливают баббитом (0,5 0,2 мм). С наружной стороны вкладышей имеется несквозное отверстие под штифт для правильной установки и фиксации от проворота. Между собой вкладыши также фиксируются штифтами. Один вкладыш опорно-упорного подшипника имеет бурты, которые охватывают опоры. Вкладыши в средней части несколько толще, поэтому с боков образуются зазоры (на масло) 0,15…0,23 мм, в котором находится масло для улучшения смазки подшипников.
Условно вкладыши разделяются на рабочие – бесканавочные (верхние у ВКВ и нижние у НКВ) и нерабочие – канавочные. Бесканавочные вкладыши НКВ и ВКВ конструктивно отличаются, что связано со способом подвода смазки. У рабочего вкладыша ВКВ с наружной стороны имеется дугообразная канавка, по краям которой просверлены два отверстия для прохода смазки внутрь подшипника.
Вкладыши маркируются со стороны управления НЧ10ВД(Г), где
НЧ – условное буквенное обозначение дизеля
10 – десятая опора
В – верхний коленчатый вал
Д – дно (нижний)
Г – гора (верхний
Вкладыши имеют восемь градаций – номинал (0) и семь ремонтных размеров. Толщина номинального вкладыша d0 = 19 мм. Каждая градация +0,25 мм.
Поршни
Образуют камеру сгорания и передают усилие от давления газов на шатуны. Нижние поршни передают коленчатому валу около 70% мощности.
Каждый поршень состоит из стакана, вставки и двух опорных плит (верхней и нижней).
Рис.10 Поршень:
1 – стакан; 2 – маслосъемные кольца с прорезями для прохода масла;3 – маслосъемное кольцо без прорезей; 4 – стопорное кольцо; 5 – нижняя опорная плита; 6,16 – комплекты прокладок; 7 – бронзовая втулка;8 – поршневой палец; 9 – вставка; 10 – ползушка; 11 – пружина; 12,17 – компрессионные кольца; 13 – верхняя опорная плита; 14 – винт; 15 – ступенчатый штифт; 18 – болт
Стакан отливается из специального чугуна. Сложная форма днища обеспечивает лучшее перемешивание топлива с воздухом. Форма днища верхнего поршня является зеркальным отражением нижнего. На внутренней поверхности днища имеются концентричные незамкнутые ребра, образующие каналы для прохода охлаждающего масла. Этими ребрами стакан опирается на вставку. Наружное кольцевое ребро соединено с цилиндрической частью стакана радиальными ребрами жесткости. На наружной поверхности стакана в верхней части выполнены четыре канавки, а в нижней части три канавки для установки уплотнительных (компрессионных) и маслосрезывающих колец.
Головка поршня имеет два конуса, что позволяет избежать задира поршней, и хромируются для повышения жаростойкости. Юбка поршня покрывается слоем полуды для лучшей прирабатываемости к зеркалу цилиндра. Юбка нижнего поршня удлинена за счет специальных козырьков.
Вставка отлита из чугуна и в сборе с плитами и регулировочными прокладками фиксируется в стакане стопорным кольцом. Верхняя плита крепится к вставке винтами и имеет запрессованный ступенчатый штифт, который фиксирует стакан, плиту и вставку в определенном положении. Под верхней плитой установлены прокладки для регулирования линейной величины камеры сжатия. Нижняя плита фиксируется штифтом и двумя болтами. Прокладки служат для регулирования зазора между плитой и стопорным кольцом.
В вертикальной расточке вставки установлена и поджата пружиной алюминиевая ползушка, которая притирается к сферической поверхности верхней головки шатуна. В двух расточках, выполненных перпендикулярно оси поршня, запрессованы бронзовые втулки, служащие опорой для поршневого пальца. Поршневой палец стальной пустотелый диаметром 82 мм свободно вращается во втулках, а его осевое смещение ограничено специальными приливами на внутренней стороне юбки.
Каждый поршень имеет четыре компрессионных и три маслосрезывающих кольца. Первое и третье компрессионные кольца на нижнем и первое на верхнем поршне имеют прямые замки, отлиты из высокопрочного чугуна и по наружной поверхности хромированы. На этой поверхности имеются канавки, заполненные дисульфидом молибдена для лучшей прирабатываемости. Второе и четвертое кольца на нижнем и три на верхнем поршне изготовлены из специального чугуна, покрыты слоем полуды, имеют косые замки, а для приработки скосы в 1º с двух сторон и запрессованный бронзовый поясок. Маслосрезывающие кольца изготавливают из специального чугуна и покрывают полудой. Два нижних кольца имеют 12 прорезей для прохода масла и косые замки. У верхнего замок ступенчатый, прорезей нет.
Шатуны
Рис.11 Шатун:
1 – стержень; 2 – корончатая гайка; 3 – болт; 4 – штифт; 5 – крышка;6,7 – вкладыши; 8 — втулка
Преобразуют возвратно-поступательное движение поршня во вращательное движение коленчатого вала и передают усилие от поршня на коленчатый вал.
Шатуны изготовлены из стали 40ХФА. Состоят из стержня двутаврового сечения и двух головок – верхней и нижней. Конструкция верхнего и нижнего шатунов одинакова, но стержень нижнего шатуна длиннее на 102,2 мм. В стержне шатуна просверлены два косых канала, которые соединены с продольным, совпадающим с кольцевой канавкой в средней части верхней головки шатуна. Диаметр продольного канала у нижнего шатуна больше. Это вызвано необходимостью подачи большего количества масла для охлаждения к нижнему поршню как к более нагруженному.
В верхнюю головку шатуна запрессована втулка, состоящая из двух втулок: внешней стальной и внутренней бронзовой, соединенных двумя горизонтальными штифтами. В обеих втулках просверлены восемь радиальных отверстий, совпадающих с кольцевой канавкой в бронзовой втулке, которая по внутренней поверхности имеет поперечные косые канавки для смазки пальца по всей длине. Сферическая поверхность верхней головки шатуна притерта совместно с ползушкой поршня.
Нижняя головка шатуна разъемная. В ней установлены два бронзовых вкладыша, залитые баббитом, — рабочий бесканавочный и нерабочий канавочный (в крышке). С обеих сторон рабочего вкладыша имеются небольшие канавки и косые каналы, совпадающие с соответствующими косыми каналами в шатуне. По краям вкладышей фрезеруются выемки для выхода масла на всю ширину подшипника. С наружной стороны нерабочего вкладыша имеется несквозное отверстие под штифт, фиксирующий вкладыш от проворота. Крышка крепится двумя болтами, которые в средней части имеют пояски, обеспечивающие точность сборки.
Вертикальная передача
Служит для передачи части мощности от верхнего коленчатого вала к нижнему, защиты при заклинивании одного из них и обеспечения опережения нижнего коленчатого вала по отношению к верхнему на 12º.
Состоит из двух больших и двух малых конических шестерен со спиральными зубьями, двух вертикальных валов, вращающихся в подшипниках верхнего и нижнего корпусов, торсионного вала, ступицы, шлицевой втулки и муфты.
Большие шестерни крепятся призонными болтами к фланцам коленчатых валов. Малые шестерни посажены на шпонках на нижний и верхний вертикальные валы. Каждый вал вращается в роликовом и двух радиально-упорных шариковых подшипниках. Наружные кольца шариковых подшипников зажимаются фланцами. Под фланцы крепления корпусов к блоку дизеля ставят стальные прокладки для регулировки бокового зазора между зубьями шестерен.
Нижний вертикальный вал выполнен пустотелым и имеет внутренние шлицы. Торсионный вал своими нижним и верхним концами соединен со шлицевыми частями нижнего вала и шлицевой втулки. Муфта болтами присоединена к ступице, посаженной на шпонке на конусную часть верхнего вала и закрепленной на нем гайкой со стопорной планкой. В ней установлена шлицевая втулка. Соединение нижнего и верхнего валов обеспечивается за счет натяга и шпонки.
Шестерни смазываются струями масла из сопел с калиброванными отверстиями, связанных трубками с нижним и верхним масляными коллекторами. Подшипники верхнего корпуса смазываются маслом, стекающим с шестерен. К подшипникам нижнего корпуса масло подводится через штуцер ввернутый во фланец.
Рис.12 Вертикальная передача:
1 – нижний корпус; 2,17,20,27 – гайки; 3 – торсионный вал; 4,10 – болты;
5,24 – радиально-упорные шариковые подшипники; 6 – проставочное кольцо; 7 – регулировочное кольцо; 8 – малая коническая шестерня; 9 – большая коническая шестерня; 11,25 – роликовые подшипники; 12 – регулировочная прокладка; 13 – распорная втулка; 14 – верхний вал; 15 – верхний корпус; 16,23 – нажимные фланцы; 18 – ступица; 19 – конический штифт; 21 – шлицевая муфта; 22 – шлицевая втулка; 26 – нижний вал
Антивибратор
Служит для устранения явления резонанса крутильных колебаний путем изменения частоты собственных колебаний нижнего коленчатого вала.
Рис.13 Антивибратор:
1 – ступица; 2,4,6,7, – пальцы; 3 – груз; 5 – болты крепления стопорных планок; 8 – втулка в отверстии груза; 9 – планка стопорная; а,б – канавки; в – каналы радиальные; г – выточка кольцевая; д — канал
Рис. Схема работы маятникового антивибратора:
1 – ступица; 2 – пальцы; 3 – груз
Так как коленчатый вал является сложной системой, то он имеет несколько частот собственных колебаний. Установлено, что опасные (критические) крутильные колебания будут возникать при следующих частотах вращения: 330, 470, 550 и 825 об/мин.
Антивибратор состоит из ступицы с тремя неподвижными дисками. Между дисками расположены 8 грузов в виде секторов (4 с одной стороны и 4 с другой) массой 10,34 кг каждый. Грузы насажены на 16 пальцев разного диаметра (4 комплекта по 4 пальца одинакового диаметра). Поэтому зазоры между пальцами и отверстиями в грузах разные (от 3,75 мм до 20,7 мм). Осевое перемещение пальцев ограничено стопорными планками. Отверстия в неподвижных дисках и в грузах защищены от износа вставными втулками.
Каждый груз свободно (с зазором) посажен на два пальца одинакового диаметра. Грузы, расположенные друг против друга по диаметру, имеют одинаковы размер пальцев. Таким образом, имеется 4 пары грузов с разной величиной перемещения в соответствии количеством критических частот вращения коленчатого вала. Каждая пара гасит критическую частоту вращения одного из порядков.
Когда вал вращается с частотой ниже или выше критической, грузы под действием центробежных сил перемещаются от центра в крайнее положения на величину зазора между пальцами и отверстиями. При работе вала на критической частоте одна пара грузов, рассчитанная для гашения этих резонансных колебаний, придет в действие. При увеличении частоты вращения грузы в силу инерции будут стремиться сохранить прежнюю частоту, а, следовательно, отставать на некоторый угол и препятствовать закручиванию вала. При уменьшении частоты вращения частота вращения грузов будет опережать частоту вращения вала и препятствовать закручиванию вала в другую сторону.
Дизель-генераторная муфта
Рис. Дизель-генераторная муфта:
1 – диск ведомый; 2 – набор пластин; 3 – диск ведущий; 4,6,7,9 – болты;
5,8 — сухари
Соединяет нижний коленчатый вал дизеля с якорем тягового генератора.
Состоит из ведомого диска, который болтами соединен с якорем тягового генератора, и ведущего диска, соединенного болтами с фланце нижнего коленчатого вала дизеля. Между дисками установлен комплект из 80 стальных пластин толщиной 0,5-0,8 мм. Пластины при помощи одних болтов через сухари прижимаются к ведомому диску, а другими болтами через сухари – к ведущему диску. Болты вставлены в отверстия дисков и пластин плотно, а сухари в диски с большим зазором. Конструкция муфты допускает работу этих валов при небольшом несовпадении осей.
Рис. Расположение меток на ведущем диске муфты привода
тягового генератора
По наружному ободу ведущего диска нарезаны косые зубья, которые входят в зацепление с червячным винтом валоповоротного механизма. Окружность ведущего диска разградуирована на 360º и на ней нанесены 12 меток. Из них 10 от 1Т до 10Т соответствуют положениям кулачков распределительного вала – по ним устанавливают топливные насосы соответствующих цилиндров. Остальные две метки ВМТ Н1 и ВМТ В1 соответствуют внутренним мертвым точкам поршней первого цилиндра дизеля.
Валоповоротный механизм
Служит для проворота коленчатых валов вручную при осмотре, регулировке и т.д.
Валоповоротный механизм укреплен внизу на торцовой стенке блока дизеля со стороны тягового генератора. На неподвижном кронштейне установлен поворотный подвижный кронштейн с пружинами, в котором в бронзовых втулках вращается вал с червяком. На поворотном кронштейне и неподвижном кронштейне выполнены две пары совпадающих отверстий.
Во время работы дизеля подвижный кронштейн повернут (вверх) и укреплен стопорным штоком так, что червяк не входит в зацепление с зубчатым венцом ведущего диска дизель-генераторной муфты.
При установке валоповоротного механизма в рабочее положение поворотом кронштейна за вал червя вводится в зацепление с зубчатым венцом дизель-генераторной муфты и в этом положении удерживается штоком. Шток вводится в совпадающие отверстия кронштейнов и прижимается фиксатором.
Для предотвращения пуска дизеля при включенном валоповоротном механизме предусмотрена блокировка с электрической системой пуска. Чтобы ввести в зацепление червяк с зубчатым венцом муфты, необходимо вывести шток из отверстия, освободив удерживающий его фиксатор. При этом прекращается нажим штока на кнопку конечного выключателя. В результате чего разрывается электрическая цепь системы пуска, и дизель не может быть запущен.
Новый двигатель оправдал себя на автомобилях Mazda – Автомобили – Коммерсантъ
Новый двигатель оправдал себя на автомобилях Mazda
Журнал «Коммерсантъ Автопилот» №9 от , стр. 12
 Новый двигатель оправдал себя на автомобилях Mazda
Двигатели бывают 2-тактные, 4-тактные, а в особый период — 3-тактные. Этот анекдот приписывают преподавателям военной кафедры одного из московских автомобильных вузов. А действительно, сколько тактов может быть в двигателе? Первый — впуск порции смеси в цилиндр, второй — сжатие смеси, третий — воспламенение сжатой смеси и рабочий ход, четвертый — выпуск отработавших газов. И так практически у всех двигателей, как бензиновых, так и дизельных. В немногих оставшихся двигателях тактов 2 («Автопилот» #3 1994 г.).
Mazda, назло планете всей выпускающая автомобили с роторным двигателем Ванкеля (Felix Wankel), год назад вновь поразила всех, внедрив в серию 5-тактный двигатель американца Ральфа Миллера (Ralpf H. Miller). Он в конце 40-х годов развил принцип Отто (Nicolaus Otto), автора 4-тактного цикла. Mazda Xedos 9 (или Eunos 800 на японском рынке, или Millenia S — на американском) высшего среднего класса — стилистическое развитие моделей 626 и Xedox 6. Кстати, аэродинамический лидер в своем классе — CD=0,29.
Как работает двигатель? При первом такте поршень движется вниз от верхней мертвой точки (ВМТ), открывается впускной клапан и в цилиндр поступает топливо-воздушная смесь. Второй такт. Поршень двигается к ВМТ. Если в 4-тактном двигателе в этот момент впускной клапан уже закрыт, то здесь он остается открытым еще на протяжении 1/5 хода поршня, но смесь продолжает поступать в цилиндры под небольшим давлением, которое обеспечивает спиральный нагнетатель Lysholm. Давление поршня дополнительно способствует равномерности заполнения цилиндра. Третий такт — сжатие — начинается со 2/5 хода. Впускной клапан закрыт. Дальше все обычно — поршень достигает ВМТ, сжатую смесь воспламеняют… Четвертый такт рабочий. Газы воздействуют на поршень на протяжении всего его хода от ВМТ к нижней мертвой точке. Пятый такт: через выпускной клапан выходят отработавшие газы, поджимаемые вновь поднимающимся поршнем. От хода поршня, как известно, зависит рабочий объем цилиндра и степень сжатия (отношение рабочего объема цилиндра к объему камеры сгорания). Чем больше степень сжатия, тем больше мощность. Но растут рабочая температура и выбросы NOx. И приходится использовать дорогое высокооктановое топливо. Словом, сложно, неэкологично, расточительно. Стоит в обычном двигателе укоротить ход поршня, как ухудшаются характеристики, поскольку газы, выделившиеся после воспламенения, действуют на поршень на меньшем расстоянии. Миллер, «растянув» цикл Отто, добился того, что ход поршня при сжатии меньше рабочего хода поршня. То есть, не проиграв в характеристике, он понизил рабочую температуру двигателя, уменьшил максимальные обороты и за счет этого увеличил ресурс. А также очистил выхлоп от NOx. И получил возможность использовать топливо с октановым числом 91.
Двигатель V6 рабочим объемом 2255 куб. см имеет алюминиевые блок и головку цилиндров, 4 клапана на цилиндр, 2 распредвала в каждой головке, электронный многоточечный впрыск, степень сжатия 8,0, мощность 210 л. с. при 5500 об./мин., крутящий момент 194 Нм при 4500 об./мин., причем высокий момент держится в более широком диапазоне оборотов, чем у обычных двигателей. Кстати, еще один важный показатель эффективности двигателя, литровая мощность — едва ли не самая высокая среди всех Mazda: 97,6 л. с. с каждого литра. Остается ждать, что нечто подобное сделают с 2-тактным двигателем и появится… 3-тактный.
Дизельный двигатель — это… Что такое Дизельный двигатель?
Ди́зельный дви́гатель — поршневой двигатель внутреннего сгорания, работающий по принципу самовоспламенения распылённого топлива от воздействия разогретого при сжатии воздуха.[1]
Спектр топлива для дизелей весьма широк, сюда включаются все фракции нефтеперегонки от керосина до мазута и ряд продуктов природного происхождения — рапсовое масло, фритюрный жир, пальмовое масло и многие другие. Дизель может с определённым успехом работать и на сырой нефти.
Компрессионные карбюраторные двигатели не относят к дизельным двигателям, так как в «дизелях» происходит сжатие чистого воздуха, а не топливо-воздушной смеси. Топливо впрыскивается в конце такта сжатия.[2][3].
История
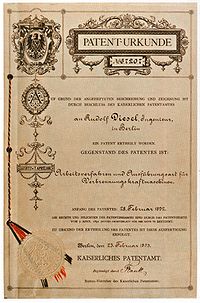
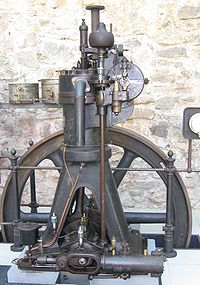
В 1824 году Сади Карно формулирует идею цикла Карно, утверждая, что в максимально экономичной тепловой машине нагревать рабочее тело до температуры горения топлива необходимо «изменением объема», то есть быстрым сжатием. В 1890 году Рудольф Дизель предложил свой способ практической реализации этого принципа. Он получил патент на свой двигатель 23 февраля 1892 года (в США в 1895 году[2]), в 1893 году выпустил брошюру. Ещё несколько вариантов конструкции были им запатентованы позднее.[3] После нескольких неудач первый практически применимый образец, названый Дизель-мотором, был построен Дизелем к началу 1897 года, и 28 января того же года он был успешно испытан. Дизель активно занялся продажей лицензий на новый двигатель. Несмотря на высокий КПД и удобство эксплуатации по сравнению с паровой машиной практическое применение такого двигателя было ограниченным: он уступал паровым машинам того времени по размерам и весу.
Первые двигатели Дизеля работали на растительных маслах или лёгких нефтепродуктах. Интересно, что первоначально в качестве идеального топлива он предлагал каменноугольную пыль. Эксперименты же показали невозможность использования угольной пыли в качестве топлива — прежде всего из-за высоких абразивных свойств как самой пыли, так и золы, получающейся при сгорании; также возникали большие проблемы с подачей пыли в цилиндры.
Инженер Экройд Стюарт (англ.)русск. ранее высказывал похожие идеи и в 1886 году построил действующий двигатель (см. полудизель). Он предложил двигатель, в котором воздух втягивался в цилиндр, сжимался, а затем нагнетался (в конце такта сжатия) в ёмкость, в которую впрыскивалось топливо. Для запуска двигателя ёмкость нагревалась лампой снаружи, и после запуска самостоятельная работа поддерживалась без подвода тепла снаружи. Экройд Стюарт не рассматривал преимущества работы от высокой степени сжатия, он просто экспериментировал с возможностями исключения из двигателя свечей зажигания, то есть он не обратил внимания на самое большое преимущество — топливную эффективность.
Независимо от Дизеля в 1898 году на Путиловском заводе в Петербурге инженером Густавом Тринклером был построен первый в мире «бескомпрессорный нефтяной двигатель высокого давления», то есть дизельный двигатель в его современном виде с форкамерой, который назвали «Тринклер-мотором». При сопоставлении Дизель-мотора и Тринклер-мотора русская конструкция, появившаяся на полтора года позднее немецкой и испытанная на год позднее, оказалась гораздо более удачной в плане практического использования. Именно Тринклер-мотор был первым двигателем с воспламенением от сжатия, работавшим на сырой нефти. Использование гидравлической системы для нагнетания и впрыска топлива позволило отказаться от отдельного воздушного компрессора и сделало возможным увеличение скорости вращения. Российская конструкция оказалась проще, надёжнее и перспективнее немецкой.[4] Однако под давлением Нобелей и других обладателей лицензий Дизеля работы над двигателем в 1902 году были прекращены.
В 1898 г. Эммануэль Нобель приобрёл лицензию на двигатель внутреннего сгорания Рудольфа Дизеля. С 1899 г. Механический завод «Людвиг Нобель» в Петербурге развернул массовое производство дизелей. В Петербурге Тринклер приспособил двигатель для работы на сырой нефти вместо керосина. В 1900 г на Всемирной выставке в Париже двигатель Дизеля получил Гран-при, чему способствовало известие, что завод Нобеля в Петербурге наладил выпуск двигателей, работавших на сырой нефти. Этот двигатель получил в Европе название «русский дизель».[5] Выдающийся русский инженер Аршаулов впервые построил и внедрил топливный насос высокого давления оригинальной конструкции — с приводом от сжимаемого в цилиндре воздуха, работавший с бескомпрессорной форсункой (В. Т. Цветков, «Двигатели внутреннего сгорания», МАШГИЗ, 1954 г.).
В настоящее время для обозначения ДВС с воспламенением от сжатия используется термин «двигатель Дизеля», «дизельный двигатель» или просто «дизель», так как теория Рудольфа Дизеля стала основой для создания современных двигателей этого типа. В дальнейшем около 20—30 лет такие двигатели широко применялись в стационарных механизмах и силовых установках морских судов, однако существовавшие тогда системы впрыска топлива с воздушными компрессорами не позволяли применять дизели в высокооборотных агрегатах. Небольшая скорость вращения, значительный вес воздушного компрессора, необходимого для работы системы впрыска топлива сделали невозможным применение первых дизелей на автотранспорте.
В 20-е годы XX века немецкий инженер Роберт Бош усовершенствовал встроенный топливный насос высокого давления, устройство, которое широко применяется и в наше время. Он же создал удачную модификацию бескомпрессорной форсунки. Востребованный в таком виде высокооборотный дизель стал пользоваться всё большей популярностью как силовой агрегат для вспомогательного и общественного транспорта, однако доводы в пользу карбюраторных двигателей (традиционный принцип работы, лёгкость и небольшая цена производства) позволяли им пользоваться большим спросом для установки на пассажирских и небольших грузовых автомобилях: с 50-х — 60-х годов XX века дизель устанавливается в больших количествах на грузовые автомобили и автофургоны, а в 70-е годы после резкого роста цен на топливо на него обращают серьёзное внимание мировые производители недорогих маленьких пассажирских автомобилей.
В дальнейшие годы происходит рост популярности дизельных двигателей для легковых и грузовых автомобилей, не только из-за экономичности и долговечности дизеля, но также из-за меньшей токсичности выбросов в атмосферу. Все ведущие европейские производители автомобилей в настоящее время имеют модели с дизельным двигателем.
Дизельные двигатели применяются также на железной дороге. Локомотивы, использующие дизельный двигатель — тепловозы — являются основным видом локомотивов на неэлектрифицированных участках, дополняя электровозы за счёт автономности. Тепловозы перевозят до 40 % грузов и пассажиров в России, они выполняют 98 % маневровой работы[источник не указан 995 дней]. Существуют также одиночные автомотрисы, дрезины и мотовозы, которые повсеместно используются на электрифицированных и неэлектрифицированных участках для обслуживания и ремонта пути и объектов инфраструктуры. Иногда автомотрисы и небольшие дизель-поезда называют рельсовыми автобусами.
Принцип работы
Четырёхтактный цикл
Работа четырёхтактного дизельного двигателя.- 1-й такт. Впуск. Соответствует 0° — 180° поворота коленвала. Через открытый ~от 345—355° впускной клапан воздух поступает в цилиндр, на 190—210° клапан закрывается. По крайней мере до 10-15° поворота коленвала одновременно открыт выхлопной клапан, время совместного открытия клапанов называется перекрытием клапанов.
- 2-й такт. Сжатие. Соответствует 180° — 360° поворота коленвала. Поршень, двигаясь к ВМТ (верхней мёртвой точке), сжимает воздух в 16(в тихоходных)-25(в быстроходных) раз.
- 3-й такт. Рабочий ход, расширение. Соответствует 360° — 540° поворота коленвала. При распылении топлива в горячий воздух происходит инициация сгорания топлива, то есть частичное его испарение, образование свободных радикалов в поверхностных слоях капель и в парáх, наконец, оно вспыхивает и сгорает по мере поступления из форсунки, продукты горения, расширяясь, двигают поршень вниз. Впрыск и, соответственно, воспламенение топлива происходит чуть раньше момента достижения поршнем мёртвой точки вследствие некоторой инертности процесса горения. Отличие от опережения зажигания в бензиновых двигателях в том, что задержка необходима только из-за наличия времени инициации, которое в каждом конкретном дизеле — величина постоянная и изменению в процессе работы не подлежит. Сгорание топлива в дизеле происходит, таким образом, длительно, столько времени, сколько длится подача порции топлива из форсунки. Вследствие этого рабочий процесс протекает при относительно постоянном давлении газов, из-за чего двигатель развивает большой крутящий момент. Из этого следуют два важнейшие вывода.
- 1. Процесс горения в дизеле длится ровно столько времени, сколько требуется для впрыска данной порции топлива, но не дольше времени рабочего хода.
- 2. Соотношение топливо/воздух в цилиндре дизеля может существенно отличаться от стехиометрического, причем очень важно обеспечить избыток воздуха, так как пламя факела занимает небольшую часть объема камеры сгорания и атмосфера в камере должна до последнего обеспечить нужное содержание кислорода. Если этого не происходит, возникает массивный выброс несгоревших углеводородов с сажей — «тепловоз „даёт“ медведя».).
- 4-й такт. Выпуск. Соответствует 540° — 720° поворота коленвала. Поршень идёт вверх, через открытый на 520—530° выхлопной клапан поршень выталкивает отработавшие газы из цилиндра.
Далее цикл повторяется.
В зависимости от конструкции камеры сгорания, существует несколько типов дизельных двигателей:
- Дизель с неразделённой камерой: камера сгорания выполнена в поршне, а топливо впрыскивается в надпоршневое пространство. Главное достоинство — минимальный расход топлива. Недостаток — повышенный шум («жесткая работа»), особенно на холостом ходу. В настоящее время ведутся интенсивные работы по устранению указанного недостатка. Например, в системе Common Rail для снижения жёсткости работы используется (зачастую многостадийный) предвпрыск.
- Дизель с разделённой камерой: топливо подаётся в дополнительную камеру. В большинстве дизелей такая камера (она называется вихревой либо предкамерой) связана с цилиндром специальным каналом так, чтобы при сжатии воздух, попадая в оную камеру, интенсивно завихрялся. Это способствует хорошему перемешиванию впрыскиваемого топлива с воздухом и более полному сгоранию топлива. Такая схема долго считалась оптимальной для легких дизелей и широко использовалась на легковых автомобилях. Однако, вследствие худшей экономичности, последние два десятилетия идёт активное вытеснение таких дизелей двигателями с нераздельной камерой и с системами подачи топлива Common Rail.
Двухтактный цикл
Принцип работы двухтактного дизельного двигателя Продувка двухтактного дизельного двигателя: внизу — продувочные окна, выпускной клапан верху открытКроме вышеописанного четырёхтактного цикла, в дизеле возможно использование двухтактного цикла.
При рабочем ходе поршень идёт вниз, открывая выпускные окна в стенке цилиндра, через них выходят выхлопные газы, одновременно или несколько позднее открываются и впускные окна, цилиндр продувается свежим воздухом из воздуходувки — осуществляется продувка, совмещающая такты впуска и выпуска. Когда поршень поднимается, все окна закрываются. С момента закрытия впускных окон начинается сжатие. Чуть не достигая ВМТ, из форсунки распыляется и загорается топливо. Происходит расширение — поршень идёт вниз и снова открывает все окна и т. д.
Продувка является врожденным слабым звеном двухтактного цикла. Время продувки, в сравнением с другими тактами, невелико и увеличить его невозможно, иначе будет падать эффективность рабочего хода за счет его укорочения. В четырёхтактном цикле на те же процессы отводится половина цикла. Полностью разделить выхлоп и свежий воздушный заряд тоже невозможно, поэтому часть воздуха теряется, выходя прямо в выхлопную трубу. Если же смену тактов обеспечивает один и тот же поршень, возникает проблема, связанная с симметрией открывания и закрывания окон. Для лучшего газообмена выгоднее иметь опережение открытия и закрытия выхлопных окон. Тогда выхлоп, начинаясь ранее, обеспечит снижение давления остаточных газов в цилиндре к началу продувки. При закрытых ранее выхлопных окнах и открытых — еще — впускных осуществляется дозарядка цилиндра воздухом, и, если воздуходувка обеспечивает избыточное давление, становится возможным осуществление наддува.
Окна могут использоваться и для выпуска отработавших газов, и для впуска свежего воздуха; такая продувка называется щелевой или оконной. Если отработавшие газы выпускаются через клапан в головке цилиндра, а окна используются только для впуска свежего воздуха, продувка называется клапанно-щелевой. Существуют двигатели, где в каждом цилиндре находятся два встречно двигающихся поршня; каждый поршень управляет своими окнами — один впускными, другой выпускными (система Фербенкс-Морзе — Юнкерса — Корейво: дизели этой системы семейства Д100 использовались на тепловозах ТЭ3, ТЭ10, танковых двигателях 4ТПД, 5ТД(Ф) (Т-64), 6ТД (Т-80УД), 6ТД-2 (Т-84), в авиации — на бомбардировщиках Junkers (Jumo 204, Jumo 205).
В двухтактном двигателе рабочие ходы происходят вдвое чаще, чем в четырёхтактном, но из-за наличия продувки двухтактный дизель мощнее такого же по объёму четырёхтактного максимум в 1,6—1,7 раз.
В настоящее время тихоходные двухтактные дизели весьма широко применяются на больших морских судах с непосредственным (безредукторным) приводом гребного винта. Ввиду удвоения количества рабочих ходов на одних и тех же оборотах двухтактный цикл оказывается выгодным при невозможности повысить частоту вращения, кроме того, двухтактный дизель технически проще реверсировать; такие тихоходные дизели имеют мощность до 100 000 л.с.
В связи с тем, что организовать продувку вихревой камеры (или предкамеры) при двухтактном цикле сложно, двухтактные дизели строят только с неразделёнными камерами сгорания.
Варианты конструкции
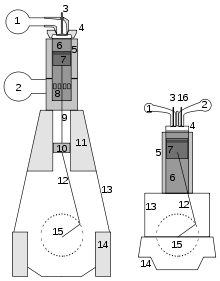
Для средних и тяжелых двухтактных дизельных двигателей характерно применение составных поршней, в которых используется стальная головка и дюралевая юбка. Основной целью данного усложнения конструкции является снижение общей массы поршня при сохранении максимально возможной жаростойкости донышка. Очень часто используются конструкции с масляным жидкостным охлаждением.
В отдельную группу выделяются четырехтактные двигатели, содержащие в конструкции крейцкопф. В крейцкопфных двигателях шатун присоединяется к крейцкопфу — ползуну, соединенному с поршнем штоком (скалкой). Крейцкопф работает по своей направляющей — крейцу, без воздействия повышенных температур, полностью ликвидируя воздействие боковых сил на поршень. Данная конструкция характерна для крупных длинноходных судовых двигателей, часто — двойного действия, ход поршня в них может достигать 3 метров; тронковые поршни таких размеров были бы перетяжеленными, тронки с такой площадью трения существенно снизили бы механический КПД дизеля.
Реверсивные двигатели
Большинство ДВС рассчитаны на вращение только в одну сторону; если требуется получить на выходе вращение в разные стороны, то используют передачу заднего хода в коробке перемены передач или отдельный реверс-редуктор. Электрическая передача также позволяет менять направление вращения на выходе.
Однако на судах с жёстким соединением двигателя с гребным винтом фиксированного шага приходится применять реверсивные двигатели, чтобы иметь возможность двигаться задним ходом. Для этого нужно изменять фазы открытия клапанов и впрыска топлива. Обычно распределительные валы снабжаются двойным количеством кулачков; при остановленном двигателе специальное устройство приподнимает толкатели клапанов, что даёт возможность передвинуть распредвалы в новое положение. Встречаются также конструкции с реверсивным приводом распределительного вала — здесь при изменении направления вращения коленчатого вала сохраняется направление вращения распределительного вала. Двухтактные двигатели с контурной продувкой, когда газораспределение осуществляется поршнем, не нуждаются в специальных реверсивных устройствах (однако в них всё же требуется корректировка момента впрыска топлива).
Реверсивные двигатели также применялись на ранних тепловозах с жёстким соединением вала двигателя с колёсами.
Преимущества и недостатки
![]() | Проверить информацию. Необходимо проверить точность фактов и достоверность сведений, изложенных в этой статье. |
![]() | Возможно, эта статья содержит оригинальное исследование. Добавьте ссылки на источники, в противном случае она может быть выставлена на удаление. |
Современные дизельные двигатели обычно имеют коэффициент полезного действия до 40-45 %, некоторые малооборотные крупные дизели — свыше 50 % (например, MAN S80ME-C7 тратит только 155 гр на кВт*ч, достигая эффективности 54,4 %).[6] Дизельный двигатель из-за особенностей рабочего процесса не предъявляет жестких требований к испаряемости топлива, что позволяет использовать в нём низкосортные тяжелые масла.
Дизельный двигатель не может развивать высокие обороты — топливо не успевает догореть в цилиндрах, для возгорания требуется время инициации. Высокая механическая напряженость дизеля вынуждает использовать более массивные и более дорогие детали, что утяжеляет двигатель. Это снижает удельную мощность двигателя, что послужило причиной малого распространения дизелей в авиации (только некоторые бомбардировщики Junkers, а также советский тяжёлый бомбардировщик Пе-8 и Ер-2, оснащавшиеся авиационными дизелями АЧ-30 и АЧ-40 конструкции А. Д. Чаромского и Т. М. Мелькумова). На максимальных эксплуатационных режимах топливо в дизеле не догорает, приводя к выбросу облаков сажи.
Сгорание впрыскиваемого в цилиндр дизеля топлива происходит по мере впрыска. Потому дизель выдаёт высокий вращающий момент при низких оборотах, что делает автомобиль с дизельным двигателем более «отзывчивым» в движении, чем такой же автомобиль с бензиновым двигателем. По этой причине и ввиду более высокой экономичности в настоящее время большинство грузовых автомобилей оборудуются дизельными двигателями[источник не указан 196 дней]. Например, в России в 2007 году почти все грузовики и автобусы были оснащены дизельными двигателями (окончательный переход этого сегмента автотранспорта с бензиновых двигателей на дизели планировалось завершить к 2009 году)[7]. Это является преимуществом также и в двигателях морских судов, так как высокий крутящий момент при низких оборотах делает более лёгким эффективное использование мощности двигателя, а более высокий теоретический КПД (см. Цикл Карно) даёт более высокую топливную эффективность.
По сравнению с бензиновыми двигателями, в выхлопных газах дизельного двигателя, как правило, меньше окиси углерода (СО), но теперь, в связи с применением каталитических конвертеров на бензиновых двигателях, это преимущество не так заметно. Основные токсичные газы, которые присутствуют в выхлопе в заметных количествах — это углеводороды (НС или СН) , оксиды (окислы) азота (NOх) и сажа (или её производные) в форме чёрного дыма. Больше всего загрязняют атмосферу в России дизели грузовиков и автобусов, которые часто являются старыми и неотрегулированными.
Другим важным аспектом, касающимся безопасности, является то, что дизельное топливо нелетучее (то есть легко не испаряется) и, таким образом, вероятность возгорания у дизельных двигателей намного меньше, тем более, что в них не используется система зажигания. Вместе с высокой топливной экономичностью это стало причиной широкого применения дизелей на танках, поскольку в повседневной небоевой эксплуатации уменьшался риск возникновения пожара в моторном отделении из-за утечек топлива. Меньшая пожароопасность дизельного двигателя в боевых условиях является мифом, поскольку при пробитии брони снаряд или его осколки имеют температуру, сильно превышающую температуру вспышки паров дизельного топлива и так же способны достаточно легко поджечь вытекшее горючее. Детонация смеси паров дизельного топлива с воздухом в пробитом топливном баке по своим последствиям сравнима со взрывом боекомплекта[источник не указан 400 дней], в частности, у танков Т-34 она приводила к разрыву сварных швов и выбиванию верхней лобовой детали бронекорпуса[источник не указан 400 дней]. С другой стороны, дизельный двигатель в танкостроении уступает карбюраторному в плане удельной мощности, а потому в ряде случаев (высокая мощность при малом объёме моторного отделения) более выигрышным может быть использование именно карбюраторного силового агрегата (хотя это характерно для слишком уж лёгких боевых единиц).
Конечно, существуют и недостатки, среди которых — характерный стук дизельного двигателя при его работе. Однако, они замечаются в основном владельцами автомобилей с дизельными двигателями, а для стороннего человека практически незаметны.
Явными недостатками дизельных двигателей являются необходимость использования стартёра большой мощности, помутнение и застывание (запарафинивание) летнего дизельного топлива при низких температурах, сложность и более высокая цена в ремонте топливной аппаратуры, так как насосы высокого давления являются прецизиоными устройствами. Также дизель-моторы крайне чувствительны к загрязнению топлива механическими частицами и водой. Ремонт дизель-моторов, как правило, значительно дороже ремонта бензиновых моторов аналогичного класса. Литровая мощность дизельных моторов также, как правило, уступает аналогичным показателям бензиновых моторов, хотя дизель-моторы обладают более ровным и высоким крутящим моментом в своём рабочем объёме. Экологические показатели дизельных двигателей значительно уступали до последнего времени двигателям бензиновым. На классических дизелях с механически управляемым впрыском возможна установка только окислительных нейтрализаторов отработавших газов, работающих при температуре отработавших газов свыше 300 °C, которые окисляют только CO и CH до безвредных для человека углекислого газа (CO2) и воды. Также раньше данные нейтрализаторы выходили из строя вследствие отравления их соединениями серы (количество соединений серы в отработавших газах напрямую зависит от количества серы в дизельном топливе) и отложением на поверхности катализатора частиц сажи. Ситуация начала меняться лишь в последние годы в связи с внедрением дизелей так называемой системы Common rail. В данном типе дизелей впрыск топлива осуществляется электронно-управляемыми форсунками. Подачу управляющего электрического импульса осуществляет электронный блок управления, получающий сигналы от набора датчиков. Датчики же отслеживают различные параметры двигателя, влияющие на длительность и момент подачи топливного импульса. Так что, по сложности современный — и экологически такой же чистый, как и бензиновый — дизель-мотор ничем не уступает своему бензиновому собрату, а по ряду параметров (сложности) и значительно его превосходит. Так, например, если давление топлива в форсунках обычного дизеля с механическим впрыском составляет от 100 до 400 бар (приблизительно эквивалентно «атмосфер»), то в новейших системах «Common-rail» оно находится в диапазоне от 1000 до 2500 бар, что влечёт за собой немалые проблемы. Также каталитическая система современных транспортных дизелей значительно сложнее бензиновых моторов, так как катализатор должен «уметь» работать в условиях нестабильного состава выхлопных газов, а в части случаев требуется введение так называемого «сажевого фильтра» (DPF — фильтр твёрдых частиц). «Сажевый фильтр» представляет собой подобную обычному каталитическому нейтрализатору структуру, устанавливаемую между выхлопным коллектором дизеля и катализатором в потоке выхлопных газов. В сажевом фильтре развивается высокая температура, при которой частички сажи способны окислиться остаточным кислородом, содержащимся в выхлопных газах. Однако часть сажи не всегда окисляется, и остается в «сажевом фильтре», поэтому программа блока управления периодически переводит двигатель в режим «очистки сажевого фильтра» путём так называемой «постинжекции», то есть впрыска дополнительного количества топлива в цилиндры в конце фазы сгорания с целью поднять температуру газов, и, соответственно, очистить фильтр путём сжигания накопившейся сажи. Стандартом де-факто в конструкциях транспортных дизель-моторов стало наличие турбонагнетателя, а в последние годы — и «интеркулера» — устройства, охлаждающего воздух после сжатия турбонагнетателем — чтобы после охлаждения получить большую массу воздуха (кислорода) в камере сгорания при прежней пропускной способности коллекторов, а Нагнетатель позволил поднять удельные мощностные характеристики массовых дизель-моторов, так как позволяет пропустить за рабочий цикл большее количество воздуха через цилиндры.
В своей основе конструкция дизельного двигателя подобна конструкции бензинового двигателя. Однако, аналогичные детали у дизеля тяжелее и более устойчивы к высоким давлениям сжатия, имеющим место у дизеля, в частности, хон на поверхности зеркала цилиндра более грубый, но твёрдость стенок блока цилиндров выше. Головки поршней, однако, специально разработаны под особенности сгорания в дизельных двигателях и почти всегда рассчитаны на повышенную степень сжатия. Кроме того, головки поршней в дизельном двигателе находятся выше (для автомобильного дизеля) верхней плоскости блока цилиндров. В некоторых случаях — в устаревших дизелях — головки поршней содержат в себе камеру сгорания («прямой впрыск»).
Сферы применения
Дизельные двигатели применяются для привода стационарных силовых установок, на рельсовых (тепловозы, дизелевозы, дизель-поезда, автодрезины) и безрельсовых (автомобили, автобусы, грузовики) транспортных средствах, самоходных машинах и механизмах (тракторы, асфальтовые катки, скреперы и т. д.), а также в судостроении в качестве главных и вспомогательных двигателей.
Мифы о дизельных двигателях
Цех судовых дизелей завода «Даймлер-Бенц» в Штутгарте Дизельный двигатель с турбонаддувом- Дизельный двигатель слишком медленный.
Современные дизельные двигатели с системой турбонаддува гораздо эффективнее своих предшественников, а иногда и превосходят своих бензиновых атмосферных (без турбонаддува) собратьев с таким же объёмом. Об этом говорит дизельный прототип Audi R10, выигравший 24-х часовую гонку в Ле-Мане, и новые двигатели BMW, которые не уступают по мощности атмосферным (без турбонаддува) бензиновым и при этом обладают огромным крутящим моментом.
- Дизельный двигатель слишком громко работает.
Громкая работа двигателя свидетельствует о неправильной эксплуатации и возможных неисправностях. На самом деле некоторые старые дизели с непосредственным впрыском действительно отличаются весьма жёсткой работой. С появлением аккумуляторных топливных систем высокого давления («Common-rail») у дизельных двигателей удалось значительно снизить шум, прежде всего за счёт разделения одного импульса впрыска на несколько (типично — от 2-х до 5-ти импульсов).
- Дизельный двигатель гораздо экономичнее.
Основная экономичность обусловлена более высоким КПД дизельного двигателя. В среднем современный дизель расходует топлива до 30 % меньше[8]. Срок службы дизельного двигателя больше бензинового и может достигать 400—600 тысяч километров. Запчасти для дизельных двигателей несколько дороже, стоимость ремонта так же выше, особенно топливной аппаратуры. По вышеперечисленным причинам, затраты на эксплуатацию дизельного двигателя несколько меньше, чем у бензинового. Экономия по сравнению с бензиновыми моторами возрастает пропорционально мощности, чем определяется популярность использования дизельных двигателей в коммерческом транспорте и большегрузной технике.
- Дизельный двигатель нельзя переоборудовать под использование в качестве топлива более дешёвого газа.
С первых моментов построения дизелей строилось и строится огромное количество их, рассчитанных для работы на газе разного состава. Способов перевода дизелей на газ, в основном, два. Первый способ заключается в том, что в цилиндры подаётся обеднённая газо-воздушная смесь, сжимается и поджигается небольшой запальной струёй дизельного топлива. Двигатель, работающий таким способом, называется газодизельным. Второй способ заключается в конвертации дизеля со снижением степени сжатия, установкой системы зажигания и, фактически, с построением вместо дизеля газового двигателя на его основе.
Рекордсмены
Самый большой/мощный дизельный двигатель
Судовой, 14 цилиндровый — Wärtsilä-Sulzer RTA96-C, созданный финской компанией Wärtsilä в 2002 году, для установки на крупные морские контейнеровозы и танкеры, является самым большим дизелем в мире[9].
Конфигурация — 14 цилиндров в ряд
Рабочий объём — 25 480 литров
Диаметр цилиндра — 960 мм
Ход поршня — 2500 мм
Среднее эффективное давление — 1,96 МПа (19,2 кгс/см²)
Мощность — 108 920 л.с. при 102 об/мин. (отдача с литра 4,3 л.с.)
Крутящий момент — 7 571 221 Н·м
Расход топлива — 13 724 литров в час
Сухая масса — 2300 тонн
Габариты — длина 27 метров, высота 13 метров
Самый большой дизельный двигатель для грузового автомобиля[источник не указан 1275 дней]
MTU 20V400 предназначен, для установки на карьерный самосвал БелАЗ-7561.
Мощность — 3807 л.с. при 1800 об/мин. (Удельный расход топлива при номинальной мощности 198 г/кВт*ч)
Крутящий момент — 15728 Н·м
Самый большой/мощный серийный дизельный двигатель для серийного легкового автомобиля[источник не указан 1275 дней]
Audi 6.0 V12 TDI с 2008 года устанавливается на автомобиль Audi Q7.
Конфигурация — 12 цилиндров V-образно, угол развала 60 градусов.
Рабочий объём — 5934 см³
Диаметр цилиндра — 83 мм
Ход поршня — 91,4 мм
Степень сжатия — 16
Мощность — 500 л.с. при 3750 об/мин. (отдача с литра — 84,3 л.с.)
Крутящий момент — 1000 Нм в диапазоне 1750-3250 об/мин.